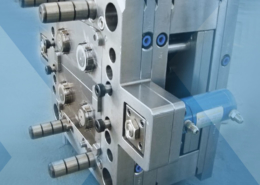
DIY Injection Mold Design For The Home Shop - making plastic molds at home
Author:gly Date: 2024-09-30
German injection mold supplier Braunform will showcase its RotaricE² technology, which achieves time and cost savings by emphasizing process control over quality control, at K 2022 on Oct. 19 to 26 in Düsseldorf, Germany.
Thiru. DR. T.R.B. Rajaa commented on the inauguration, “It was my pleasure to inaugurate Kriya Medical Technologies’ highly innovative ICHOR Medical Molding System at their manufacturing facility today at the SIPCOT Medical Devices Park in Oragadam near Chennai. Such one-of-a-kind facilities align perfectly with our Chief Minister of Tamil Nadu Thiru. MK Stalin’s vision of boosting advanced manufacturing capabilities in the state.”
Ultimately, Braunform claims 45% overall production savings with RotaricE² technology by eliminating the need for two injection molds and machines, as well as an assembly line.
The ICHOR System is a fully integrated, high-speed manufacturing setup for Evacuated Blood Collection Tubes. With a production capacity of 700,000 tubes per day, the system is set to enhance local production capabilities. This development aims to elevate India’s status as a high-tech manufacturing hub, with aspirations to export these products to major markets including the United States, Canada, and Japan.
By integrating servo-electric rotary drives in the mold and redirecting rotary movement into translational movement, Braunform achieves compact radial arrangement of injection mold cavities with slides or masking devices around a sprue or, preferably, a side-gate system, the company said.
Notably, the multi-component Braunform side-gate injection mold will combine capping and unscrewing functions. The 4+4 cavity mold serves as a basis for a compact series mold in a modular design with up to 64+64 cavities. Six functions are combined in the ejector side — core-back, two sliders per cavity, lifting of the lid, translational capping of the closures, unscrewing, and final ejection. Modules are individually centered and easily accessible, and the overall design is cleanroom compatible thanks to electric drives, corrosion-resistant steel, low-fat lubrication, and rolling element centering systems. Diffusion-welded inserts facilitate die insert cooling on the nozzle side.
The ICHOR system operates continuously with full automation and remote monitoring capabilities extending to Canada, Japan, and Luxembourg. The system was developed through a global partnership, with Kriya Medical Technologies overseeing product design and quality standards, while Husky managed the automation and equipment design.
A Smart Control system by hot-runner specialist Ewikon ensures real-time data mining on the hot side. The hot-runner system is especially important for the Luer cap, as the shot weight of the TPE-based second component is only 0.05 g.
Geoff Giordano is a tech journalist with more than 30 years’ experience in all facets of publishing. He has reported extensively on the gamut of plastics manufacturing technologies and issues, including 3D printing materials and methods; injection, blow, micro and rotomolding; additives, colorants and nanomodifiers; blown and cast films; packaging; thermoforming; tooling; ancillary equipment; and the circular economy. Contact him at [email protected].
Kriya Medical Technologies, headquartered in Chennai, has launched the ICHOR Medical Molding System, a fully automated manufacturing system designed to produce 250 million blood collection tubes each year. The unveiling of this advanced machinery took place on Wednesday, September 18, 2024, at Kriya Medical’s manufacturing facility located in the Oragadam Industrial Corridor, Chennai. The event was inaugurated by Thiru. DR. T.R.B. Rajaa, Minister for Industries, Investment Promotions and Commerce, Government of Tamil Nadu.
The RotaricE² injection mold system reportedly achieves 45% overall production savings by integrating several production steps.
Anu Moturi, CEO and Founder of Kriya Medical Technologies, highlighted the significance of the ICHOR system in the company’s mission. “Our mission at Kriya is to make quality healthcare accessible to all. The ICHOR system is a crucial part of this mission, allowing us to significantly scale up the production of essential diagnostic and therapeutic tools that can improve the lives of billions worldwide. We believe that every life is valuable, and through the ICHOR system and our other offerings, we are dedicated to being a trusted partner in delivering accessible, high-quality healthcare.”
Express Healthcare, first published as Express Healthcare Management in January 2000, has grown to become the No.1 Business News Magazine for the healthcare industry. The editorial contents include: news, views, analysis and interviews, under main segments: Market, Strategy, Knowledge, Life, Radiology, Hospital Infra, IT@Healthcare. Besides this, we bring out a quarterly publication, called In Imaging for the radiology and imaging segment.
The RotaricE² concept integrates several production steps — including assembly — in a small space. The technology will be demonstrated by Arburg (Hall 13, Booth A13-1-B13) on an Allrounder More machine, which will produce a Luer pharmaceutical cap measuring 10 mm in diameter and 11 mm in length.
Kistler developed the two indirect pressure sensors used in each injection mold cavity to detect defective parts, which are sorted out by the handling system.
GETTING A QUOTE WITH LK-MOULD IS FREE AND SIMPLE.
FIND MORE OF OUR SERVICES:
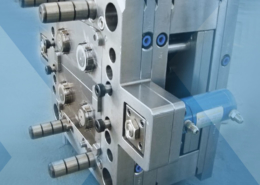
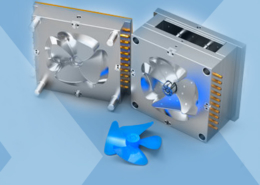
Plastic Molding

Rapid Prototyping
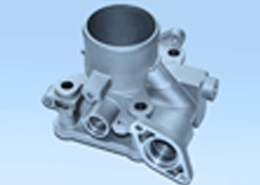
Pressure Die Casting
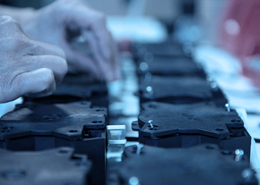
Parts Assembly
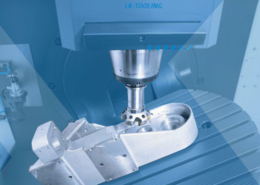