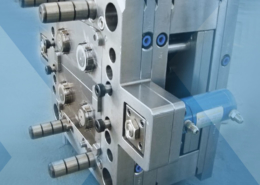
Unlocking the Potential of Molding Tooling: A Comprehensive Exploration
Author:gly Date: 2024-06-08
Introduction
Molding tooling serves as the backbone of the manufacturing industry, facilitating the production of intricate components with precision and efficiency. From injection molds to dies and fixtures, these tools play a critical role in shaping the final outcome of the manufacturing process. This article delves into the world of molding tooling, unraveling its complexities, capabilities, and significance in modern manufacturing.
Evolution of Molding Tooling
The evolution of molding tooling parallels the advancements in manufacturing technology, dating back to the industrial revolution when manual craftsmanship gave way to mechanized processes. Over the years, the advent of precision machining techniques and computer-aided design (CAD) software has revolutionized the field of molding tooling, enabling the creation of highly complex and precise molds with unprecedented accuracy. From simple two-part molds to intricate multi-cavity molds, the capabilities of molding tooling have expanded exponentially, driving innovation and progress in various industries.
Types of Molding Tooling
Molding tooling encompasses a diverse range of tools and equipment tailored to specific manufacturing processes and requirements. Injection molds, the most common type of molding tooling, are used to produce plastic components by injecting molten material into a mold cavity. Additionally, compression molds are employed in the production of composite materials, such as fiberglass and carbon fiber, by applying pressure to the material within a mold cavity. Furthermore, die casting dies and extrusion dies enable the mass production of metal components with high precision and repeatability, contributing to the efficiency and reliability of the manufacturing process.
Design and Optimization
The design and optimization of molding tooling are critical factors that determine the quality, efficiency, and cost-effectiveness of the manufacturing process. Advanced CAD software allows engineers to design molds with intricate geometries and complex features, optimizing the flow of material and minimizing defects. Moreover, simulation tools enable virtual testing of mold designs, predicting potential issues such as warpage, shrinkage, and air entrapment before the production phase, thus saving time and resources. Furthermore, the use of additive manufacturing techniques, such as 3D printing, offers new possibilities for rapid prototyping and tooling production, facilitating faster iteration and customization of molds to meet specific requirements.
Challenges and Innovations
Despite the advancements in molding tooling technology, challenges persist in terms of cost, lead time, and complexity. The high upfront cost of tooling, coupled with long lead times for design and production, can pose significant barriers to entry for manufacturers, especially small and medium-sized enterprises (SMEs). However, ongoing research and development efforts are focused on addressing these challenges through innovations such as rapid tooling techniques and modular tooling systems. Additionally, advancements in materials science, such as the development of high-performance tool steels and coatings, contribute to the durability and longevity of molds, reducing maintenance costs and downtime.
Conclusion
In conclusion, molding tooling plays a pivotal role in modern manufacturing, enabling the production of complex components with precision and efficiency. From injection molds to dies and fixtures, these tools form the foundation of the manufacturing process, driving innovation and progress across various industries. As technology continues to advance and manufacturing processes evolve, the role of molding tooling will only become more critical in shaping the future of production. By embracing innovation, collaboration, and continuous improvement, manufacturers can unlock the full potential of molding tooling to achieve greater efficiency, flexibility, and competitiveness in the global marketplace.
GETTING A QUOTE WITH LK-MOULD IS FREE AND SIMPLE.
FIND MORE OF OUR SERVICES:
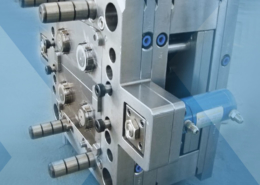
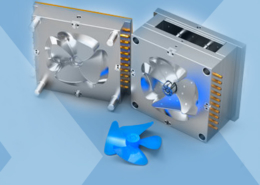
Plastic Molding

Rapid Prototyping
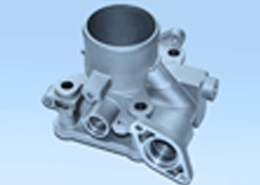
Pressure Die Casting
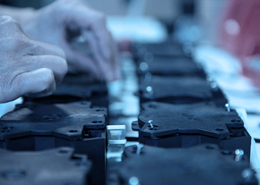
Parts Assembly
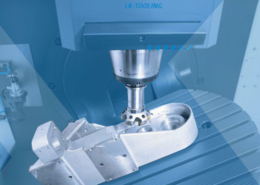