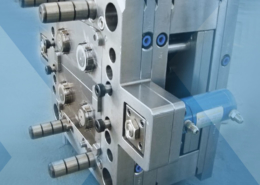
Design Aid Shows Resins and Materials Interacting - short run injection molding
Author:gly Date: 2024-09-30
The Water Jet Machining (WJM) process is an advanced, non-conventional machining process wherein a water jet is fired at the workpiece. The jet erodes the material of the workpiece and causes it to become shaped, i.e. jetting is a machining process that utilizes a water jet to remove material from a workpiece.
It is necessary to use high pressure tubes to flow water under high pressure. Tubes typically range in size from 6 mm to 14 mm in diameter. The cutting head can also be moved with great flexibility.
When high-velocity jets of water strike a workpiece, they cause erosion of the workpiece material, which results in machining.
"As a manufacturer of plastics such as polycarbonate, we naturally have a responsibility in dealing with these important materials, including at the end of their product life. Our advantage is [that] we know how our products are designed and, therefore, can conduct targeted research into recycling solutions," said Dr. Thorsten Dreier, Covestro's chief technology officer. "The chemical recycling of polycarbonate is another example with which our colleagues in development show that closed cycles are possible in the future. We need to use end-of-life plastics as a resource and reuse them as alternative raw materials to close the loop."
The pump will take water from the reservoir and transfer it to the intensifier. The pump creates pressure in the water from 1500 to 4000 bars. A 50 to 100 HP electric motor is used.
The recycled product can be mass-balanced and reused as a raw material for the production of polycarbonate without further processing. "Such high-quality recycled raw materials are needed for applications that require the highest quality level. These include, for example, applications in the automotive sector with special requirements in terms of safety, optical transparency, or aesthetics, and products in our everyday lives such as consumer electronics," said Lily Wang, head of the Engineering Plastics business entity.
Water is collected in the catcher or drain after the workpiece is cut. From here, the water may proceed for further purification or be recirculate.
In order to increase the machining capability of water jets, abrasive particles are mixed with the jet of water. With mixed abrasives, hard materials such as aluminum, steel, granite, and cast irons can be machined.
Covestro has developed a robust process for recycling polycarbonate monomers at laboratory scale, with pilot-scale technical implementation starting.
Mechanical recycling of polycarbonate is already an important component of Covestro's recycling strategy. The mechanical recycling process is used whenever waste streams are sufficiently pure and the recycled polycarbonate meets the requirements profile of the future application.
I tend to agree, based on my experience with every single piece of consumer electronic or electrical equipment I´ve purchased over the last 20 years...
Simple water jet machines are almost like their abrasive counterparts in terms of construction and operation. In order to better understand the abrasive jet machine, let’s examine its construction and operation.
The water jet intensifier creates a high-pressure liquid jet is by increasing water jet pressure. This intensifier is connected to the accumulator. Water is taken in at low pressure and expelled at high pressure through an accumulator. The mechanism works by hydraulic reciprocation.
Water emerging from the nozzle has a pressure of 60,000 pounds per square inch or 4137 bar. This means that the pressure is over 4000 times greater than the normal atmospheric pressure (1 bar). Hard materials cannot be machined with simple water jet machining. It is only suitable for softer materials such as rubber, ABS, leather, wood, and plastics.
WJM is similar to Ultrasonic machining and Abrasive jet machining in that the workpiece is machined mechanically. For precise and automated control, this machining process is paired with a CNC machine.
In just over a year´s time, Microsoft will stop supporting Windows 10. I foresee that a lot of businesses (that tend to run slightly older hardware)...
The nozzle produces highly kinetic jets of water from high pressure. Since the nozzle’s area decreases at its end, this creates more kinetic energy. Finally, the water jet is directed at the workpiece.
The control valve controls both the amount and the pressure of water being passed. It directs the water to the flow regulator. Kinetic energy is then transferred from pressure energy to the flow regulator.
A flow regulator regulates the flow of water that reaches the control valve. By adjusting the flow regulator, water will be sent to the nozzle, where it will be transformed into high-velocity water.
Water is temporarily stored in the accumulator. Several control valves are connected to the accumulator. By keeping the flow of high-pressure water continuous, it eliminates pressure fluctuations.
Materials supplier Covestro has developed an innovative chemical recycling process to convert polycarbonate back to its monomers so that they can be fed into the production process as alternative raw materials. Technical implementation of chemical recycling is now beginning on a pilot scale at the company’s site in Leverkusen, Germany. The process will be further optimized toward eventual deployment at a commercial scale.
Chemical recycling complements mechanical recycling in that larger waste streams that are unsuitable for the mechanical process can be treated to enable the production of plastics that meet the highest quality requirements. Covestro is actively developing chemical recycling.
The newly developed process, which was driven by an international team, is a specific chemolysis process adapted to polycarbonate. "Pre-sorted waste streams containing a product content of more than 50% polycarbonate can be recycled this way. This has been successfully demonstrated with various polycarbonate-containing plastic waste streams," explained Markus Dugal, head of process technology at Covestro. "With the help of chemolysis, the cycle can be closed to a direct precursor of polycarbonate. This makes the recycling process very sustainable."
Covestro is also driving forward further processes for innovative recycling of polycarbonate in its research laboratories. These include chemolytic alternatives, recycling with enzymes that break down the plastic, and smart pyrolysis. Promising alternatives can also be tested with the pilot plant.
With more than 78 manufacturing processes, including metal casting, metal fabrication, precision CNC machining, plastic fabrication, metal finishing and more, etc., in addition to our 200+ sub-contractor partners, OmnidexCN is able to support every project or component production regardless of the development stage or mass production.
GETTING A QUOTE WITH LK-MOULD IS FREE AND SIMPLE.
FIND MORE OF OUR SERVICES:
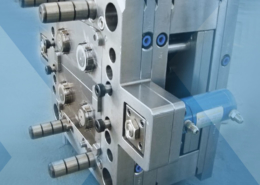
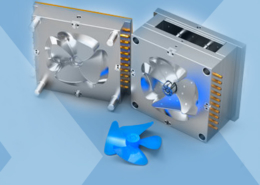
Plastic Molding

Rapid Prototyping
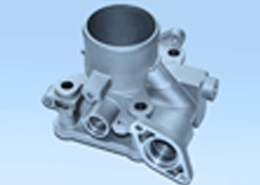
Pressure Die Casting
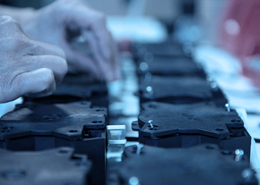
Parts Assembly
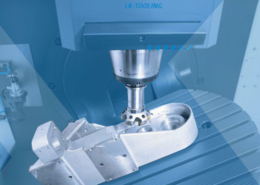