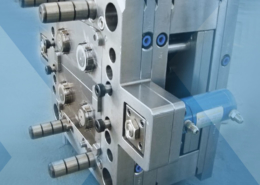
Controlled-Viscosity Molding Gains Commercial Traction - plastic molding 1 inch
Author:gly Date: 2024-09-30
The Abbe’s numbers calculated from Eq. (2) for pristine PS, PS-S and PS-SD at 486, 589, and 656 nm wavelength using RI in Fig. 8 are calculated from Table S1. The obtained high Abbe’s number for the PS-S and PS-SD molds are in the range ~ 30 ± 1, indicate the high level dispersion of sulfur and SD copolymer in PS matrix, this also supports the increased RI in the composites.
Core Technology Molding turned to Mold-Masters E-Multi auxiliary injection unit to help it win a job and dramatically change its process.
Join this webinar to explore the transformative benefits of retrofitting your existing injection molding machines (IMMs). Engel will guide you through upgrading your equipment to enhance monitoring, control and adaptability — all while integrating digital technologies. You'll learn about the latest trends in IMM retrofitting (including Euromap interfaces and plasticizing retrofits) and discover how to future-proof your machines for a competitive edge. With insights from industry experts, it'll walk you through the decision-making process, ensuring you make informed choices that drive your business forward. Agenda: Maximize the value of your current IMMs through strategic retrofitting Learn how to integrate digital technologies to enhance monitoring and control Explore the benefits of Euromap interfaces and plasticizing retrofits Understand how retrofitting can help meet new product demands and improve adaptability Discover how Engel can support your retrofitting needs, from free consultations to execution
Direct utilization of elemental sulfur in producing HRI polymers are limited due to the low solubility and compatibility of sulfur in most organic solvents and chemicals26. Recently, Theato et al., reported the use of elemental sulfur in the preparation of polythioamide by Willgerodt–Kindler reaction with High Refractive Index of n = 1.87 at λ = 589.3 nm27. In another study Zhang et al., prepared polystyrene-sulfur composites with high Abbe’s number (27.3–30.4) and refractive index of n = 1.6220, in this method elemental sulfur was partially reacted with styrene and mixed with polystyrene in solution to improve the compatibility and dispersibility of the sulfur; which resulted in improving RI of the polymer28.
Milacron has three material partners for the project, with Shell supplying virgin HDPE for the skin and the core uses postconsumer resin (PCR) from KW Plastics and LyondellBasell that has been reclaimed, reprocessed and repelletized, with the PCR core to alternate each day between the two suppliers. To support this level of production, Milacron’s booth includes a 20-by-30-foot “Resin Room” with two 30-ton air-cooled chillers and a complete material handling system, including surge bins and vacuum pumps. Stirn notes that the company coinjected a pail at NPE2015, but it was from only a single-cavity mold running at 45-48% PCR core level.
Lü, C., Cui, Z., Wang, Y., Yang, B. & Shen, J. Studies on syntheses and properties of episulfide-type optical resins with High Refractive Index. J. Appl. Polym. Sci. 89, 2426–2430. https://doi.org/10.1002/app.12459 (2003).
The main advantage of these composites is their ability to scale up and processability into variety of different objects by melt and solution processing technique. Molded objects and films prepared by injection molding and hot-press methods are displayed in Fig. S3 are transparent and uniformly colored like extrudate indicate the stability and unchanged morphology of the composites. Thus, the nanocomposites are feasible to process into desire shape and size without altering the transparency. The composites also exhibits high solubility in most of organic solvent similar to polystyrene and form a clear and stable solution (see image Fig. S4); hence, enable to prepare ultra-thin films on glass slides by solution casting or spin coating method. Thus, the one step preparation and easy processability of polystyrene-sulfur composites have greater advantage over inorganic polymer composites.
After successfully introducing a combined conference for moldmakers and injection molders in 2022, Plastics Technology and MoldMaking Technology are once again joining forces for a tooling/molding two-for-one.
This work is funded by the Abu Dhabi National Oil Company (ADNOC) Research & Development and also by Khalifa University of Science and Technology (KU).
In this work, we demostrate the preparation of low cost High Refractive Index polystyrene-sulfur nanocomposites in one step by combining inverse vulcanization and melt extrusion method. Poly(sulfur-1,3-diisopropenylbenzene) (PS-SD) copolymer nanoparticles (5 to 10 wt%) were generated in the polystyrene matrix via in situ inverse vulcanization reaction during extrusion process. Formation of SD copolymer was confirmed by FTIR and Raman spectroscopy. SEM and TEM further confirms the presence of homogeneously dispersed SD nanoparticles in the size range of 5 nm. Thermal and mechanical properties of these nanocomposites are comparable with the pristine polystyrene. The transparent nanocomposites exhibits High Refractive Index n = 1.673 at 402.9 nm and Abbe’y number ~ 30 at 10 wt% of sulfur loading. The nanocomposites can be easily processed into mold, films and thin films by melt processing as well as solution casting techniques. Moreover, this one step preparation method is scalable and can be extend to the other polymers.
Li, C. et al. Synthesis and characterization of organo-soluble thioether-bridged polyphenylquinoxalines with ultra-high refractive indices and low birefringences. Polymer 51, 3851–3858. https://doi.org/10.1016/j.polymer.2010.06.035 (2010).
Gao, C., Yang, B. & Shen, J. Study on syntheses and properties of 2,2′-mercaptoethylsulfide dimethacrylate transparent homo- and copolymer resins having High Refractive Index. J. Appl. Polym. Sci. 75, 1474–1479. https://doi.org/10.1002/(sici)1097-4628(20000321)75:12%3c1474::aid-app5%3e3.0.co;2-1 (2000).
Nam, K.-H., Lee, A., Lee, S.-K., Hur, K. & Han, H. Infrared transmitting polyimides based on chalcogenide element-blocks with tunable high-refractive indices and broad optical windows. J. Mater. Chem. C 7, 10574–10580. https://doi.org/10.1039/C9TC03574E (2019).
In the middle of Milacron’s booth, the company has a nonoperating 90-foot extrusion line. The SG75 single-screw extruder is paired with a new pipe head that Milacron is making in-house for the first time. The display also features pullers and saws, plus a new extruder control. At the end of the line, a small cobot picks up finished pipe, stacking and arraying the product.
Discover how artifical intelligence is revolutionizing plastics processing. Hear from industry experts on the future impact of AI on your operations and envision a fully interconnected plant.
(A) In situ inverse vulcanization of sulfur and DIB in polystyrene matrix, (B) digital image of the processed circular disc of PS-S and PS-SD composites (C) FTIR and (D) Raman spectra of PS, PS-S and PS-SD composites with different sulfur loading, respectively.
Griebel, J. J. et al. Dynamic covalent polymers via inverse vulcanization of elemental sulfur for healable infrared optical materials. ACS Macro Lett. 4, 862–866. https://doi.org/10.1021/acsmacrolett.5b00502 (2015).
While prices moved up for three of the five commodity resins, there was potential for a flat trajectory for the rest of the third quarter.
Xia, Y. et al. Synthesis of transparent aqueous ZrO2 nanodispersion with a controllable crystalline phase without modification for a high-refractive-index nanocomposite film. Langmuir 34, 6806–6813. https://doi.org/10.1021/acs.langmuir.8b00160 (2018).
Griebel, J. J. et al. New infrared transmitting material via inverse vulcanization of elemental sulfur to prepare High Refractive Index polymers. Adv. Mater. 26, 3014–3018. https://doi.org/10.1002/adma.201305607 (2014).
In this collection of articles, two of the industry’s foremost authorities on screw design — Jim Frankand and Mark Spalding — offer their sage advice on screw design...what works, what doesn’t, and what to look for when things start going wrong.
Lü, C. & Yang, B. High refractive index organic–inorganic nanocomposites: Design, synthesis and application. J. Mater. Chem. 19, 2884–2901. https://doi.org/10.1039/B816254A (2009).
Ultradent's entry of its Umbrella cheek retractor took home the awards for Technical Sophistication and Achievement in Economics and Efficiency at PTXPO.
Multiple speakers at Molding 2023 will address the ways simulation can impact material substitution decisions, process profitability and simplification of mold design.
Despite price increase nominations going into second quarter, it appeared there was potential for generally flat pricing with the exception of a major downward correction for PP.
Abbe’s number (νD), a key parameter to measure refractive index dispersion, is also an important for optical materials used in the visible region. νD can be calculated from bellow Eq. (2)
Start by picking a target melt temperature, and double-check data sheets for the resin supplier’s recommendations. Now for the rest...
Initially, pure polystyrene melted at 230 °C in an extruder, to this known amount of sulfur; DIB were added in stepwise and allowed to mix for 30 min. Under extrusion condition sulfur undergo ring opening polymerization to form a viscous polysulfur which later reacts with DIB to yield cross-linked SD copolymers. These viscous melts effectively mix with PS melts and diffuse into the matrix due to the applied shear resulting in a homogeneously dispersed transparent composites (see Fig. 1A). Colorless polystyrene changed to orange red color confirming the successful cross-linking reaction (see Fig. 1B bottom row). Similar color change was also observed when pure sulfur directly reacted with DIB (see Fig. S1). These cross-links provide structural stability to the polysulfur chains whereas DIB improves the compatibility with PS matrix. For comparison, composites were also prepared without the cross-linkers resulting in transparent yellow colored polystyrene-sulfur (PS-S) composites (see Fig. 1B top row). Optically transparent materials were obtained with up to 10 wt% of sulfur loading, excess addition resulted in agglomeration of particles and reduced transparency (see Fig. S2). Therefore, the composites with 5 and 10 wt% of sulfur loading were only prepared and used for further study.
Okutsu, R., Suzuki, Y., Ando, S. & Ueda, M. Poly(thioether sulfone) with High Refractive Index and high Abbe’s number. Macromolecules 41, 6165–6168. https://doi.org/10.1021/ma800797p (2008).
Effect of the fillers on the structural behavior of polystyrene was analyzed by XRD. Figure 2 shows the XRD patterns comparison between PS with PS-S and PS-SD composites at different sulfur loading. PS shows a broad XRD peak at 2θ = 20° confirming its amorphous nature, similarly PS-S and PS-SD composites are also displayed amorphous peak in the same range, however; the peak intensities are reduced according to the sulfur content. It is also interesting to note that the sharp crystalline sulfur peaks (see insight image) are completely absent even in 10 wt% loaded composites samples, indicating the change in sulfur morphology after the extrusion. This can be explained as follows; during melt mixing process, both PS and polysulfur turns to viscous melts and hence the polysulfur chains can easily diffuse into the PS matrix under applied shear to form a homogeneous polymer blends. When these polymers are extruded they are allowed to cool naturally to the room temperature, during cooling process diffused polysulfur chains solidifies much faster than PS due to the difference in solidification rate. Thus, the mobility of polysulfur chains are arrested inside the PS matrix and results in random dispersion. Consequently, when these polysulfur chains revert back to the monomeric octasulfur form, their crystalline structure is destroyed which leads to the non-crystalline amorphous sulfur. In case of PS-SD the polysulfur chains reacts with the DIB to form highly cross-linked copolymers which further restricts the chain mobility and increases the amorphous nature. Thus, the sulfur crystalline peaks are completely absent in the composites. Furthermore, faster solidification of sulfur also interfere with the crystalline arrangement of PS chains and reduces the lamellar thickness, hence, increasing in sulfur loading resulted in decreased peak intensity. Similar behaviors was also observed in our previous work when sulfur is blended with high density polyethylene40.
In summary, this work demonstrate the simple, scalable method to achieve high RI material by direct utilization of elemental sulfur via in situ inverse vulcanization and melt extrusion technique. The prepared PS-S and PS-SD composites are transparent and showed high transparency depending on the film thickness. Further, TEM images confirmed the homogeneous dispersion of both sulfur and SD nanoparticles in the PS matrix without any visible aggregates. Absence of sulfur crystalline peaks in DSC thermogram supported the conversion of crystalline sulfur into uniformly dispersed amorphous form in the PS matrix. DMTA study indicate the slight reduce in the Tg with the increasing filler loading due to the plastization effect of sulfur under heat treatment. Mechanical properties of the composites are comparable to the pristin PS, hence can be used in wide application without sacrificing the strength. RI of PS n = 1.601 at 402.9 nm was increased to n = 1.656 and 1.673 by the incorporation of 10 wt% of sulfur and SD copolymer nanoparticles respectively in the composites. Higher RI of PS-SD then PS-S composites are due to the uniform dispersion and improved dipolar arise from the cross-linked structure of sulfur and DIB. The main advantage of the method is that the RI can be controlled by the addition of sulfur and DIB during extrusion process and the obtained materials can be easily processed in to different shapes by adopting both melt and solution processing techniques, moreover the proposed method can also be extended to the other melt processable polymers.
Another all-electric 275-ton Fanuc Roboshot is molding medical vials from a 48-cavity tool using a Mold-Masters hot runner system. Post-molding, a platen-mounted robot removes the 48 vials and places them on conveyor above the clamp, with the parts separated into “lanes.” Stirn says this setup helps “containerize” production for traceability while minimizing floor space impact.
Liu, B.-T. & Li, P.-S. Preparation and characterization of High-Refractive-Index polymer/inorganic hybrid films containing TiO2 nanoparticles prepared by 4-aminobenzoic acid. Surf. Coat. Technol. 231, 301–306. https://doi.org/10.1016/j.surfcoat.2012.03.011 (2013).
In Fig. 3, DSC thermogram of pure sulfur shows three endothermic transitions at 106, 124, and at 184 °C, which are assigned for the solid–solid transition of sulfur from orthorhombic to monoclinic form, melting of monoclinic sulfur and for the polymerization of sulfur, respectively. However, these melt transition peaks are completely absent in both PS-S and PS-SD composites suggests that the crystalline sulfur changed to the amorphous form41. These results further supports the formation of amorphous sulfur and the absence of crystalline peaks in XRD.
NPE2024: Coinjection of postconsumer resin, in-mold decoration, LSR micromolding and bioplastics processing are just some of the machine displays at Milacron's booth.
Polystyrene pellets, 5 mm was obtained from sigma-Aldrich chemicals (USA), Powdered Sulfur (> 99% purity) supplied by Merck chemical (Germany), and 1,3-diisopropenylbenzene (DIB, 97%) supplied by (TCI America) were used without further purification.
Liu, H.-T., Zeng, X.-F., Zhao, H. & Chen, J.-F. Highly transparent and multifunctional polymer nanohybrid film with superhigh ZnO content synthesized by a bulk polymerization method. Ind. Eng. Chem. Res. 51, 6753–6759. https://doi.org/10.1021/ie300425v (2012).
Mixed in among thought leaders from leading suppliers to injection molders and mold makers at the 2023 Molding and MoldMaking conferences will be molders and toolmakers themselves.
Antonello, A. et al. Hybrid organic–inorganic ZnS-loaded nanocomposite films for stable optical coatings. Thin Solid Films 518, 6781–6786. https://doi.org/10.1016/j.tsf.2010.06.013 (2010).
August 29-30 in Minneapolis all things injection molding and moldmaking will be happening at the Hyatt Regency — check out who’s speaking on what topics today.
The mechanical properties of the PS and their composites were studied by DMTA and UTM. Figure 5a–c shows the loss tangent (tan δ), storage modulus (G′) and loss modulus (G″) versus temperature graphs of PS, PS-S-5, PS-S-10, PS-SD-5 and PS-SD-10, respectively. Single glass transition temperature (Tg) was observed in tanδ curve for PS, PS-S and PS-SD hybrid samples, shown in Fig. 5a–c and reported in Table 1. All the tanδ curves show uniformity with homogeneous nature of the hybrid materials. The tan δ curves of the PS, PS-S-5, PS-S-10, PS-SD-5 and PS-SD-10 hybrid materials show the glass transition temperature and tanδ max at 109.7 °C, 1.51; 95.4 °C, 2.01; 93.9 °C, 2.16; 99.3 °C, 1.84; and 102.2 °C, 1.76 , respectively. PS has a Tg of 109.7 °C, which was shifted to 95.4 °C and 93.9 °C after incorporation of sulfur (5% and 10%) into polymer matrix, suggest a unhindered segmental motion of PS chains. This could be due to the phase change of elemental sulfur, which act as a plasticizer in the hybrid materials. A comparison of glass transition temperature between PS-S and P-SD hybrid materials show that hybrid materials prepared from sulfur copolymer cross-linker (SD) were harder than the sulfur (S) based hybrid materials. This could be due to the strong cross-linking between the sulfur chains and formation of interpenetrating (IPN) network in PS matrix, which increased the cross-linked density in PS-SD-5 and PS-SD-10 hybrid materials. The observed Tg and storage modulus values for the series PS-SD-5 and PS-SD-10 show that, the Tg and crosslinking density increase with increasing SD content in the hybrid materials. Figure 5b,c shows the G′ and G′′ plots of PS, PS-S-5, PS-S-10, PS-SD-5 and PS-SD-10 hybrid materials. The storage modulus measures the stiffness and crosslinking density of the hybrid materials and loss modulus measures the glass transition temperature, reported in Table 1. Decrease in storage modulus was observed for the PS-S-5 and PS-S-10 hybrid materials compare to pure PS polymer and increase in storage modulus was observed for PS-SD-5 and PS-SD-10 compare to PS-S-5 and PS-S-10 hybrid materials at 40 °C and Tg + 5 °C region. However, storage modulus and crosslinking density both were decreased after incorporating sulfur and sulfur copolymer cross linker. The crosslink density (νe) of PS, PS-S-5, PS-S-10, PS-SD-5 and PS-SD-10 hybrid materials was calculated by using Eq. (1).
Taking advantage of these S–S bonds, herein, we report on the preparation of scalable polystyrene sulfur composites by one step melt extrusion technique with improved RI. In this method, cross-linked sulfur copolymer nanoparticles were generated inside the polystyrene matrix by in situ reaction of sulfur and DIB during extrusion process. The amount of sulfur in the composite was optimized to obtain transparent materials with High Refractive Index (RI) as well as Abbe’s number. In situ cross-linking reaction was confirmed by FTIR and Raman spectroscopy. The thermal properties were studied by DSC and TGA. Surface morphology and optical properties were estimated by SEM, TEM and UV–Vis spectroscopy respectively. Mechanical and thermomechanical properties of the composites were also studied and compared with pure polystyrene. The main advantage of the prepared composites is that these composites can be easily scalable and processable into films, molds and thin films by melt processing as well as solution casting method without sacrificing the mechanical properties.
Plastics Technology covers technical and business Information for Plastics Processors in Injection Molding, Extrusion, Blow Molding, Plastic Additives, Compounding, Plastic Materials, and Resin Pricing. About Us
While prices moved up for three of the five commodity resins, there was potential for a flat trajectory for the rest of the third quarter.
Shankarayya Wadi, V. K. et al. NMR and EPR structural analysis and stability study of inverse vulcanized sulfur copolymers. ACS Omega 3, 3330–3339. https://doi.org/10.1021/acsomega.8b00031 (2018).
Sustainability continues to dominate new additives technology, but upping performance is also evident. Most of the new additives have been targeted to commodity resins and particularly polyolefins.
When, how, what and why to automate — leading robotics suppliers and forward-thinking moldmakers will share their insights on automating manufacturing at collocated event.
technotrans says climate protection, energy efficiency and customization will be key discussion topics at PTXPO as it displays its protemp flow 6 ultrasonic eco and the teco cs 90t 9.1 TCUs.
Lü, C., Cui, Z., Li, Z., Yang, B. & Shen, J. High Refractive Index thin films of ZnS/polythiourethane nanocomposites. J. Mater. Chem. 13, 526–530. https://doi.org/10.1039/B208850A (2003).
Thermal stability of the PS-S and PS-SD nanocomposites was examined through thermogravimetric analyses (TGA). In Fig. S8, pure sulfur shows one step decomposition initiated around 200 °C and completely decomposes around 300 °C. However, nanocomposites showed two-step degradation, first step degradation started at around 205 °C was estimated to the decomposition of sulfur and is comparable to the amount of initial sulfur feed and the second decomposition step was by the polystyrene matrix. The amount of sulfur loading is comparable with the initial degradation of sulfur suggest complete incorporation of sulfur during extrusion processing.
Milacron has filled the corners of its 26,600-square-foot NPE2024 booth with technology representative of its various fellow operating companies and preferred partner brands, including DME, FANUC Roboshot, Mold-Masters and its own injection molding machine line with the debut of its M Series. Milacron’s Andy Stirn says most prominent will be a 1,070-ton M-Series injection molding machine running a SyBridge Technologies 2-cavity tool for 5-gallon pails featuring in-mold label (IML) decoration and up to 50% recycled content via coinjection and a Mold-Masters valve-gated hot runner.
Optical transparency of the PS composites was investigated using UV–Vis-near-IR transmition spectroscopy over a broad optical window (200–3,000 nm) to determine the effect of sulfur and samples thickness on optical properties. Samples with thickness around 15 μm and 2 mm were prepared by drop casting and injection molding method respectively. The thin films of PS, PS-S-5 and PS-S-10 appeared transparent, whereas, PS-SD-5 and PS-S-10 are slightly yellow in color. However, the molded samples of PS-S composites appear faint yellow and the inverse vulcanized PS-SD samples exhibits deep orange color (see insight image in Fig. 7a,b respectively). The thin films PS-S-5 and PS-SD-5 with 5 wt% sulfur loading are 85% transparent near IR region similar to pure polystyrene, however, increasing sulfur content to 10 wt% reduced the transparency to around 70%. Whereas, the optical transparency for thicker molded samples (2 mm disc) diminished to 60% in comparison to thin films (see Fig. 7a,b). This could be due to the increase in sample thickness as well as the absorbance of C-H vibrations from polystyrene and DIB co-monomer in the near-IR 1,500–3,000 nm range. Expended zone of the UV–Vis spectra between 200–800 nm for both thin films and molded samples are presented in Fig. 7c,d respectively. The spectra clearly indicate that the optical transparency of the PS-SD-10 thin films is higher than the PS-S-10. It has been observed that the larger nanoparticles aggregates in a polymer matrix steeply increase the intensity of scattered light, which would induce a dramatic decrease in the transparency44. Sulfur shows partial solubility in toluene, thus, the thin films prepared in toluene at lower sulfur concentration (5 wt%) showed higher transparency, however, when the loading increased the undissolved sulfur particles partially aggregates which resulted in reduced transparency. Whereas, in case of PS-SD samples the SD copolymers are completely soluble in toluene and hence form homogeneous solution of SD particles, thus displays higher transparency. In molded samples all samples displayed similar transparency around 60%. It is worth to note that the 15 µm‐thin films exhibit cutoff wavelengths (λcutoff) of 270–310 nm and the molded samples exhibited low transparency below 600 nm in the visible spectrum, as readily evidenced by the yellow to orange color of the composites material. However, the retention of high transparency in the visible (above 600 nm) was observed.
Polystyrene-sulfur (PS-S) and polystyrene-S/DIB (PS-SD) nanocomposites were prepared by one step melt extrusion method using twin-screw Haake Minilab II extruder. The extruder temperature for all preparation was maintained at 230 °C with an average screw rotation of 100 rpm and the mixing time of 30 min. The extruder was kept inside fume wood and the extrusion were carried out under N2 atmosphere in presence of a H2S gas detector for all experiments as percussion. The PS-SD nanocomposites were prepared by the in situ inverse vulcanization of S-DIB in polystyrene matrix under extrusion conditions by keeping cross-linker (DIB) amount at 30 weight percent with respect to the sulfur content. A representative example for the preparation of PS-SD-5 containing 5 weight % sulfur is as follows. Polystyrene (4.75 g) is melted inside the extruder at 230 °C, to this 0.25 g sulfur (5% with respect to PS) and 0.075 g DIB (30 wt% with respect to sulfur) was added and allowed to mix for 30 min. The composite was then extruded and allowed to cool down to room temperature naturally. The samples were termed as PS-SD-X composites (X = sulfur content, 5 or 10 wt%). A similar conditions was applied to prepare PS-S composites except by adding DIB cross-linker. The composites were denoted as PS-S-Y (Y = sulfur content, 5 or 10 wt%). Pure polystyrene was also extruded which serves as reference. The extruded materials were then chopped into small pieces and molded in to desired shapes by injection molding. Injection molding was carried out by using Thermo Scientific Haake minijet pro injection molder at cylinder temperature 190 °C and mold temperature 115 °C and the injection pressure kept at 500 bar. All the molded samples have uniform thickness of 2 mm. Thin film were prepared by using hot-press just above the melt temperature of the polystyrene.
Park, S., Lee, D., Cho, H., Lim, J. & Char, K. Inverse vulcanization polymers with enhanced thermal properties via divinylbenzene homopolymerization-assisted cross-linking. ACS Macro Lett. 8, 1670–1675. https://doi.org/10.1021/acsmacrolett.9b00827 (2019).
Lorentz, H. A. Ueber die Beziehung zwischen der Fortpflanzungsgeschwindigkeit des Lichtes und der Körperdichte. Ann. Phys. 245, 641–665. https://doi.org/10.1002/andp.18802450406 (1880).
Wadi, V.S., Jena, K.K., Halique, K. et al. Scalable High Refractive Index polystyrene-sulfur nanocomposites via in situ inverse vulcanization. Sci Rep 10, 14924 (2020). https://doi.org/10.1038/s41598-020-71227-z
Higashihara, T. & Ueda, M. Recent progress in High Refractive Index polymers. Macromolecules 48, 1915–1929. https://doi.org/10.1021/ma502569r (2015).
The G′ values of PS-SD-5 and PS-SD-10 hybrid materials at temperatures 40 °C suggest the presence of good cross-linking and hardness. The glass transition temperature of the hybrid materials from tan δ curves and loss modulus (G′) curves shows very similar data, this could be due to the homogeneous arrangement of the molecular structure in the hybrid materials.
Similarly, in current study the cross-linked sulfur nanoparticles with S–S bonds were generated inside the polystyrene matrix during extrusion process, these polymer composites can be easily molded in to different shape by molding or hot-press method. To measure RI, the composites were molded in to 2 mm thick circular molds and the variation in RI with respect to the wavelength are measured and are presented in Fig. 8. Pristine PS shows RI n = 1.601 at 402.9 nm, whereas, addition of elemental sulfur in the matrix increased the RI n = 1.656, and RI increased with increase in the sulfur loading confirms the role of S–S bonds in improving RI. Cross-linking these sulfur with DIB further improved the RI to 1.652 to 1.673 according to the SD copolymers loading (5 and 10 wt%) respectively. The higher RI of PS-SD compared to the PS-S are due to the higher dipolar arising from the cross-linked structure and the presence of aromatic DIB in PS matrix.
SEM images of (a) sulfur, (b) PS, (c) PS-S-10, (d) PS-SD-10 and their corresponding elemental imaging on the right side. TEM image of (e) PS, (f) PS-S-5, (g) PS-SD-10 and (h) PS-S-10. (i) Enlarged TEM image of PS-SD-10, insight graph show the EDX of the sample.
Jena, K. K. & Alhassan, S. M. Melt processed elemental sulfur reinforced polyethylene composites. J. Appl. Polym. Sci. https://doi.org/10.1002/app.43060 (2016).
Incorporation of elemental sulfur into polymers during synthesis is highly challenging due to its low solubility and compatibility with majority of organic chemicals. Further, polysulfur produced from heat treatment are highly brittle and unstable at room temperature; which also make it undesirable for use during polymer processing. Thus, in this method polysulfur chains are stabilized by reacting elemental sulfur with DIB cross-linker inside the polystyrene matrix during extrusion via in situ inverse vulcanization. A schematic representation for the preparation of transparent polystyrene-sulfur composites is shown in Fig. 1A.
Lee, S. et al. Refractive index engineering of transparent ZrO2–polydimethylsiloxane nanocomposites. J. Mater. Chem. 18, 1751–1755. https://doi.org/10.1039/B715338D (2008).
Lü, C. et al. Preparation and characterization of ZnS–polymer nanocomposite films with High Refractive Index. J. Mater. Chem. 13, 2189–2195. https://doi.org/10.1039/B304154A (2003).
The Mold-Masters hot runner controls are fully integrated into the Milacron’s injection molding machine control, with plans to utilize different resins and mixes of materials, including in different colors, to showcase how the coinjection technology can hide or reveal the core in a very controlled manner.
Next to the DME area, Milacron is promoting its various aftermarket capabilities, including control technologies for retrofitting, information on its Industry 4.0 M Powered real-time monitoring and analysis program, as well as a general aftermarket display. “Aftermarket is a big part of our business and value proposition,” Stirn says.
A 55-ton all-electric Fanuc Roboshot with DIY Robots automation is set up for an LSR application in partnership with a cold-deck runnerless tool from M.R. Mold & Engineering and metering from Nexus to create very small umbrella-type diaphragms from a four-cavity tool. How small are the parts? Small enough that Milacron hasn’t been able to weigh them individually, but combined they weigh just 0.9g. Milacron turned to DME and its machining expertise to fabricate an 8-mm plunger system for the application to dose in material with precision. The positional accuracy of the plunger is due in no small part to the machine. “No machine controls motion like a Roboshot,” Stirn says.
Resin drying is a crucial, but often-misunderstood area. This collection includes details on why and what you need to dry, how to specify a dryer, and best practices.
In this three-part collection, veteran molder and moldmaker Jim Fattori brings to bear his 40+ years of on-the-job experience and provides molders his “from the trenches” perspective on on the why, where and how of venting injection molds. Take the trial-and-error out of the molding venting process.
By submitting a comment you agree to abide by our Terms and Community Guidelines. If you find something abusive or that does not comply with our terms or guidelines please flag it as inappropriate.
Lee, J. M. et al. Synthesis of poly(phenylene polysulfide) networks from elemental sulfur and p-diiodobenzene for stretchable, healable, and reprocessable infrared optical applications. ACS Macro Lett. 8, 912–916. https://doi.org/10.1021/acsmacrolett.9b00306 (2019).
Kleine, T. S. et al. 100th anniversary of macromolecular science viewpoint: High Refractive Index polymers from elemental sulfur for infrared thermal imaging and optics. ACS Macro Lett. 9, 245–259. https://doi.org/10.1021/acsmacrolett.9b00948 (2020).
V.S.W. and S.M.A. initiated the idea and executed the work. V.S.W., K.K.J. and K.H. prepared and characterized composites. B.R. and L.C. conducted RI experiment. V.S.W., V.T. and S.M.A. analyzed and drew conclusions. All authors have given approval to the final version of the manuscript.
The Plastics Industry Association (PLASTICS) has released final figures for NPE2024: The Plastics Show (May 6-10; Orlando) that officially make it the largest ever NPE in several key metrics.
Thank you for visiting nature.com. You are using a browser version with limited support for CSS. To obtain the best experience, we recommend you use a more up to date browser (or turn off compatibility mode in Internet Explorer). In the meantime, to ensure continued support, we are displaying the site without styles and JavaScript.
Recently, Pyun et al. prepared sulfur rich copolymers via inverse vulcanization technique, in this method linear sulfur chains were stabilized between organic molecules by forming highly cross-linked structure. The presence of these S–S bonds and the cross-linked structure imparted HRI n > 1.7 to the copolymers, moreover, S–S bonds are largely inactive in IR region and hence enabled to take high quality images in the near (1.5 μm) and mid‐IR (3–5 μm) regions29,30. Further enhancement in RI was achieved by adding inorganic selenium in the copolymer, the addition of selenium into the inverse vulcanized sulfur copolymers significantly improved the RI (n > 2) and showed excellent IR transparence31. More recently, Kleine, et al., developed chalcogenide hybrid inorganic/organic polymers with enhanced long-wave infrared (LWIR) spectrum (7–14 µm), this low organic content terpolymers showed superior IR transparence and demonstrated the ability to take highly resolved thermal images in near or complete dark environment32,33. Similar chemistry of introducing S–S bond in the copolymer to improve the refractive index was later adopted by many researchers are prepared various HRI copolymers34,35,36,37,38.
Lim, J. et al. A one-pot synthesis of polysulfane-bearing block copolymer nanoparticles with tunable size and Refractive Index. Chem. Commun. 52, 2485–2488. https://doi.org/10.1039/C5CC08490C (2016).
In recent years, optical materials with High Refractive Index (RI) have received much attention because of their wide variety of application in areas such as ophthalmic lenses, filters, optical adhesives, high reflective and antireflection coatings as well as advanced optoelectronic fabrications1. Inorganic materials usually possesses a high RI (n = 2.0–5.0)2, however, their lower flexibility and higher densities (> 2.5 g cm3) limits their applications3. On the other hand polymeric materials overcome these issues and attracted many researchers due to the advantages of low weight, excellent impact resistance, easy processability and low cost compared with inorganic materials4. Unfortunately, RI for majority of polymers lay below n = 1.3–1.65. According to the Lorentz–Lorenz equation, refractive index of the polymers can be enhanced considerably by introducing a substituent with high molar refraction, low molar volume, high aromatic contents, or high density6,7. Thus, several methods were employed to achieve High Refractive Index (HRI) by introducing range of functional moieties such as aromatic rings, heteroaromatic rings, heavy atom halogen (Cl, Br, and I) and sulfur in the polymer; however, these methods involves extensive monomer and polymer synthesis procedure8. In another approach inorganic or metal nanoparticles like (ZrO2)9,10, (TiO2)11,12,13, ZnO14 etc., were added into a polymer matrix to produce polymer composites with HRI. It has been well established that sulfur atoms are effective in increasing refractive indices because of their high atomic refraction, hence the sulfur containing nanoparticles like FeS15, ZnS16,17 and PbS18 were also used as nano-fillers to increase the RI. However, dispersion of inorganic nanoparticles in the polymer matrix is highly challenging, moreover increasing concentration increases their agglomeration tendency which could significantly effect the transparency of the material and could limits their applications. Thus, polymer that contain sulfur in back bone including epoxy19, polyurethane20, polymethacrylate21,22, poly(thiocarbonate)s23,24, poly(thioether sulfone)24 and polyimide (PI)25 have been explored extensively for their HRI properties.
Chung, W. J. et al. The use of elemental sulfur as an alternative feedstock for polymeric materials. Nat. Chem. 5, 518. https://doi.org/10.1038/nchem.1624 (2013).
Exhibitors and presenters at the plastics show emphasized 3D printing as a complement and aid to more traditional production processes.
Introduced by Zeiger and Spark Industries at the PTXPO, the nozzle is designed for maximum heat transfer and uniformity with a continuous taper for self cleaning.
In a time where sustainability is no longer just a buzzword, the food and beverage packaging industry is required to be at the forefront of this innovation. By adopting circular packaging processes and solutions, producers can meet regulatory requirements while also satisfying consumer demand and enhancing brand reputation. Join Husky to learn more about the broader implications of the circular economy — as well as how leading brands are leveraging this opportunity to reduce costs, increase design flexibility and boost product differentiation. Agenda: The cost and operational benefits of embracing circularity Key materials in circular packaging — including rPET and emerging bioplastics How to design a circular food and beverage package Strategies for selecting sustainable closures to future-proof packaging solutions Optimization and streamlining of production processes for enhanced efficiency How Husky Technologies can enable your sustainable success
Take a deep dive into all of the various aspects of part quoting to ensure you’ve got all the bases—as in costs—covered before preparing your customer’s quote for services.
Learn about sustainable scrap reprocessing—this resource offers a deep dive into everything from granulator types and options, to service tips, videos and technical articles.
Join KraussMaffei for an insightful webinar designed for industry professionals, engineers and anyone interested in the manufacturing processes of PVC pipes. This session will provide a comprehensive understanding of the technology behind the production of high-quality PVC pipes: from raw material preparation to final product testing. Agenda: Introduction to PVC extrusion: overview of the basic principles of PVC pipe extrusion — including the process of melting and shaping PVC resin into pipe forms Equipment and machinery: detailed explanation of the key equipment involved — such as extruders, dies and cooling systems — and their roles in the extrusion process Process parameters: insight into the critical process parameters like temperature, pressure and cooling rates that influence the quality and consistency of the final PVC pipes Energy efficiency: examination of ways to save material and energy use when extruding PVC pipe products
Join Wittmann for an engaging webinar on the transformative impact of manufacturing execution systems (MES) in the plastic injection molding industry. Discover how MES enhances production efficiency, quality control and real-time monitoring while also reducing downtime. It will explore the integration of MES with existing systems, emphasizing compliance and traceability for automotive and medical sectors. Learn about the latest advancements in IoT and AI technologies and how they drive innovation and continuous improvement in MES. Agenda: Overview of MES benefits What is MES? Definition, role and brief history Historical perspective and evolution Longevity and analytics Connectivity: importance, standards and integration Advantages of MES: efficiency, real-time data, traceability and cost savings Emerging technologies: IoT and AI in MES
While the melting process does not provide perfect mixing, this study shows that mixing is indeed initiated during melting.
Plastics Technology’s Tech Days is back! Every Tuesday in October, a series of five online presentations will be given by industry supplier around the following topics: Injection Molding — New Technologies, Efficiencies Film Extrusion — New Technologies, Efficiencies Upstream/Downstream Operations Injection Molding — Sustainability Extrusion — Compounding Coming out of NPE2024, PT identified a variety of topics, technologies and trends that are driving and shaping the evolution of plastic products manufacturing — from recycling/recyclability and energy optimization to AI-based process control and automation implementation. PT Tech Days is designed to provide a robust, curated, accessible platform through which plastics professionals can explore these trends, have direct access to subject-matter experts and develop strategies for applying solutions in their operations.
In situ cross-linking reaction of SD copolymers was verified by carrying out Fourier-transform infrared spectroscopy (FT-IR) analysis (Fig. 1C). In the FT-IR spectrum of PS-SD samples the appearance of new stretching bands at 1,012 and 645 cm−1 corresponding to C–S bonding indicating successful chemical reaction between sulfur and DIB39. Intensities of these peaks are relatively weak due to the higher peak intensities of polystyrene in the same IR region. Moreover, absence of characteristic C=CH2 peak located at 900 cm−1 clearly indicates the complete consumption of DIB during cross-linking reaction. Interestingly, polystyrene peaks in the spectra’s are unchanged suggests the structural stability and non-reactivity of PS against sulfur under extrusion condition (see Fig. S6). This was also supported by solid state 1H-NMR spectra (see Fig. S7). The nature of carbon–sulfur bonding within the polymeric matrix of PS-SD was further elucidated by Raman spectroscopy analysis (see Fig. 1D). PS-SD showed S–S bonding peaks at 152, 220, and 474 cm−1 along with the ν (C–S) peak at 182 cm−1, which indicates successful chemical reaction of sulfur and DIB.
Althues, H., Henle, J. & Kaskel, S. Functional inorganic nanofillers for transparent polymers. Chem. Soc. Rev. 36, 1454–1465. https://doi.org/10.1039/B608177K (2007).
Matsuda, T., Funae, Y., Yoshida, M., Yamamoto, T. & Takaya, T. Optical material of High Refractive Index resin composed of sulfur-containing aliphatic and alicyclic methacrylates. J. Appl. Polym. Sci. 76, 45–49. https://doi.org/10.1002/(sici)1097-4628(20000404)76:1%3c45::aid-app6%3e3.0.co;2-m (2000).
The DME section of the booth has a 170-ton Q series servo-hydraulic machine with automation as well as a high amount of DME products inside the tool, including collapsible cores and some serialization devices for part identification. Running a BioLogiQ bioresin, the machine is molding a phone holder. Stirn says the Q series promotes energy efficiency and automation integration. The machine has a small, heated sprue built-in, and a DME controller and hot runner, for the single-cavity tool.
In a partnership with Kurz, Milacron is introducing its new M series two-platen servo-hydraulic machines. In a touch display application geared toward the automotive or appliance markets, Kurz-supplied decorative and functional foil is fed through the open tool for back molding. The 500-ton cell has three integrated robots, including one that enters the mold with an infrared heater used to heat the foil. Another robot removes the molded part from the press and places it on a fixture for trimming. The finished part is then moved to another fixture where it’s backlit to show the different patterns and buttons that are revealed as it is interacted with by consumers.
While the major correction in PP prices was finally underway, generally stable pricing was anticipated for the other four commodity resins.
Dan, S., Gu, H., Tan, J., Zhang, B. & Zhang, Q. Transparent epoxy/TiO2 optical hybrid films with tunable refractive index prepared via a simple and efficient way. Prog. Org. Coat. 120, 252–259. https://doi.org/10.1016/j.porgcoat.2018.02.017 (2018).
Effect of elemental sulfur and SD copolymer nanoparticles on tensile strength, elastic modulus and elongation at break of the PS-S and PS-SD hybrid materials were investigated. The stress vs strain curve and data are reported in Fig. 5d and Table 2. The UTS, Young’s Modulus and the elongation at break determined from Fig. 5d were presented in Fig. 6 show that UTS and Modulus decrease with increasing the elemental sulfur content. The ultimate tensile strength (UTS) of the PS-S and PS-SD hybrid materials slightly decreased for sulfur and SD loaded samples, i.e., 66.46, 62.03, 58.19, 50.27 and 54.31 MPa for PS, PS-S-5, PS-S-10, PS-SD-5 and PS-SD-10 hybrid samples respectively. However, with increasing SD concentration to 10 wt% resulted in increased UTS to 54.31 and modulus to 2283 MPa. This could be due to the formation of interpenetrating network (IPN) in the hybrid material. Interesting results were observed in elongation at break (%), where all the data close to same with slightly increase in elongation after addition of sulfur in PS polymer matrix. However, the mechanical properties of these PS-sulfur composites are much more superior to the inverse vulcanized copolymers (see Table 2)42. Inverse vulcanized materials are highly brittle to handle, whereas, in this case the PS-S and PS-SD composites exhibited mechanical strength similar to neat PS. The high mechanical strength and one step preparation method can be advantage to prepare in bulk by scale up process and can also be explored in wider application areas.
Melt extrusion of the polymer was carried out using twin-screw Haake Minilab II extruder with screw diameter 5/14 mm conical and screw length 109.5 mm. Infrared spectra of the PS, PS-S and PS-SD composites were recorded by Attenuated Totally Reflectance Fourier Transformed Infrared spectroscopy technique (FTIR-ATR), using a Bruker Vertex 70. Diffraction (XRD) patterns were collected using analytical X’Pert PRO Powder Diffractometer (Cu-Ka radiation 1.5406 Å, 40 kV, 40 mA) in the range of 5°–80° 2θ scale, with a step size of 0.02°. The thermal degradation behavior was studied in TGA Netzsch Sta. 409 PC/PG (Germany). The samples (10–15 mg) were scanned from 25 to 600 °C at a heating rate of 10 °C/min in nitrogen environment. Differential Scanning Calorimetry (DSC) analysis of the composite samples (5–10 mg) was done using DSC Netzsch (Germany) at a heating rate of 10 °C/min in the temperature range between − 0 and 200 °C in a nitrogen environment. The dynamic mechanical behavior of the samples was studied using dynamic mechanical analyzer (TA Instruments, DMAQ800). The experiments were carried out a fixed frequency of 1 Hz and at a heating rate of 2 °C/min. The tests were conducted in a temperature range of 25 to 150 °C using rectangular samples of dimensions with (25 mm × 12 mm × 0.5 mm). (TEM) images were obtained using FEI Tecnai G20 operated at 200 kV accelerating voltage to observe the nanoscale structures of the sulfur in the composite. Samples were ultra-microtomed at room temperature conditions to prepare less than 100 nm thick samples. Refractive index of the samples were determined by using nulling imaging ellipsometer (Nanofilm_ep3se + NIR upgrade, Accurion). The incident elliptically polarized light was reflected off the sample onto a detector through an objective and a polarizer. The ellipsometric null condition was fulfilled when the incident light ellipticity, was selected so that the reflected light was completely linearly polarized and an analyzer (A) before the detector was in such position that the absolute minimum of light flux was detected. The shape of the incident light was controlled by positions of a polarizer (P) and a lambda quarter-wave plate (C). The positions of P, C, A at the nulling condition are related to the optical properties of the sample. Reduction of the measured data with computerized optical modeling leads to a deduction of complex refractive index. Initially, an angular dependence at selected wavelengths were measured for each sample. The obtain data was used to determine complex index or refraction for each selected wavelength, using supplied modeling software (EP4-model, Accurion). In modeling software, surface roughness and inclusion of voids during pouring were take into account.
Additive technology creates air pockets in film during orientation, cutting down on the amount of resin needed while boosting opacity, mechanical properties and recyclability.
Mold maintenance is critical, and with this collection of content we’ve bundled some of the very best advice we’ve published on repairing, maintaining, evaluating and even hanging molds on injection molding machines.
Boyd, D. A. et al. Optical properties of a sulfur-rich organically modified chalcogenide polymer synthesized via inverse vulcanization and containing an organometallic comonomer. ACS Macro Lett. 8, 113–116. https://doi.org/10.1021/acsmacrolett.8b00923 (2019).
Wei, Q. et al. Hyperbranched polymers with high transparency and Inherent High Refractive Index for application in organic light-emitting diodes. Adv. Funct. Mater. 26, 2545–2553. https://doi.org/10.1002/adfm.201504914 (2016).
In this collection, which is part one of a series representing some of John’s finest work, we present you with five articles that we think you will refer to time and again as you look to solve problems, cut cycle times and improve the quality of the parts you mold.
This month’s resin pricing report includes PT’s quarterly check-in on select engineering resins, including nylon 6 and 66.
Mike Sepe has authored more than 25 ANTEC papers and more than 250 articles illustrating the importance of this interdisciplanary approach. In this collection, we present some of his best work during the years he has been contributing for Plastics Technology Magazine.
Formnext Chicago is an industrial additive manufacturing expo taking place April 8-10, 2025 at McCormick Place in Chicago, Illinois. Formnext Chicago is the second in a series of Formnext events in the U.S. being produced by Mesago Messe Frankfurt, AMT – The Association For Manufacturing Technology, and Gardner Business Media (our publisher).
Stirn says the pail is a great application to utilize coinjection for sandwiching recycled content between layers of virgin resins, but there are others. While 5-gallon pails would normally run in cycle times of 18-25 seconds, Milacron is targeting 18- to 20- second cycles for the show display. “For coinjection, that is phenomenal,” Stirn says. “For a standard monolayer setup that’s competitive, to go that fast with coinjection of two pails is special.”
Join Engel in exploring the future of battery molding technology. Discover advancements in thermoplastic composites for battery housings, innovative automation solutions and the latest in large-tonnage equipment designed for e-mobility — all with a focus on cost-efficient solutions. Agenda: Learn about cutting-edge thermoplastic composites for durable, sustainable and cost-efficient battery housings Explore advanced automation concepts for efficient and scalable production See the latest large-tonnage equipment and technology innovations for e-mobility solutions
As reported in our Keeping Up section last month, Milacron LLC invited Plastics Technology to its Batavia, Ohio, headquarters for an exclusive preview of its new Elektron line of all-electric injection presses ahead of their official debut at Milacron’s open house Apr. 24-25.
Fukuzaki, N., Higashihara, T., Ando, S. & Ueda, M. Synthesis and characterization of highly refractive polyimides derived from thiophene-containing aromatic diamines and aromatic dianhydrides. Macromolecules 43, 1836–1843. https://doi.org/10.1021/ma902013y (2010).
Open Access This article is licensed under a Creative Commons Attribution 4.0 International License, which permits use, sharing, adaptation, distribution and reproduction in any medium or format, as long as you give appropriate credit to the original author(s) and the source, provide a link to the Creative Commons license, and indicate if changes were made. The images or other third party material in this article are included in the article’s Creative Commons license, unless indicated otherwise in a credit line to the material. If material is not included in the article’s Creative Commons license and your intended use is not permitted by statutory regulation or exceeds the permitted use, you will need to obtain permission directly from the copyright holder. To view a copy of this license, visit http://creativecommons.org/licenses/by/4.0/.
Featuring twin injection units and a high-base machine design, the cell showcases the potential to free drop the buckets onto a conveyor running below the press, which is still common for many pail molders. Here, backside automation provides label insertion, with key stats on the label, as well as part removal and full inspection.
where: nD, nF, and nC are the refractive indices of the material at the wavelengths of the sodium D (589.3 nm), hydrogen F (486.1 nm), and hydrogen C (656.3 nm) lines, respectively.
Liu, J.-G. & Ueda, M. High refractive index polymers: Fundamental research and practical applications. J. Mater. Chem. 19, 8907–8919. https://doi.org/10.1039/B909690F (2009).
Sulfur containing polymer displayed HIR due to the high atomic refraction property of sulfur atom. Thus, the amount of sulfur and their degree of molecular packing in the polymers play an important role in controlling RI properties1. Hence, in recent studies, highly cross-linked sulfur rich copolymers prepared via inverse vulcanization using elemental sulfur displayed High Refractive Index (n > 1.7)29. In these sulfur rich copolymers the S–S bonds are largely IR inactive due to low organic content make them to use in IR imaging in near and mid-infrared region also and thus imparted high n to the sulfur copolymers and demonstrated the ability to use in IR imaging. The properties of these sulfur copolymers can be easily tunable by varying the cross-linkers amount.
Second quarter started with price hikes in PE and the four volume engineering resins, but relatively stable pricing was largely expected by the quarter’s end.
Khawaja, S. Z., Vijay Kumar, S., Jena, K. K. & Alhassan, S. M. Flexible sulfur film from inverse vulcanization technique. Mater. Lett. 203, 58–61. https://doi.org/10.1016/j.matlet.2017.05.133 (2017).
Caseri, W. Nanocomposites of polymers and metals or semiconductors: Historical background and optical properties. Macromol. Rapid Commun. 21, 705–722. https://doi.org/10.1002/1521-3927(20000701)21:11%3c705::aid-marc705%3e3.0.co;2-3 (2000).
This Knowledge Center provides an overview of the considerations needed to understand the purchase, operation, and maintenance of a process cooling system.
Tsai, C.-M. et al. High refractive index transparent nanocomposites prepared by in situ polymerization. J. Mater. Chem. C 2, 2251–2258. https://doi.org/10.1039/C3TC32374A (2014).
Lü, C., Guan, C., Liu, Y., Cheng, Y. & Yang, B. PbS/polymer nanocomposite optical materials with High Refractive Index. Chem. Mater. 17, 2448–2454. https://doi.org/10.1021/cm050113n (2005).
The aim of this presentation is to guide you through the factors and the numbers that will help you determine if a robot is a smart investment for your application. Agenda: Why are you considering automation? What problems are you trying to solve? How and why automation can help Crunch the numbers and determine the ROI
He, L., Zhao, H. & Theato, P. No heat, no light—The future of sulfur polymers prepared at room temperature is bright. Angew. Chem. Int. Ed. 57, 13012–13014. https://doi.org/10.1002/anie.201807005 (2018).
where R is the universal gas constant, and T the temperature in K. G′ values in the rubbery region at T > Tg were taken to calculate υe by using Eq. (1).
Thousands of people visit our Supplier Guide every day to source equipment and materials. Get in front of them with a free company profile.
Jiang, L. et al. Direct introduction of elemental sulfur into polystyrene: A new method of preparing polymeric materials with both High Refractive Index and Abbe number. Polymer 180, 121715. https://doi.org/10.1016/j.polymer.2019.121715 (2019).
Say “manufacturing automation” and thoughts immediately go to the shop floor and specialized production equipment, robotics and material handling systems. But there is another realm of possible automation — the front office.
Anderson, L. E. et al. Chalcogenide hybrid inorganic/organic polymers: Ultrahigh Refractive Index polymers for infrared imaging. ACS Macro Lett. 6, 500–504. https://doi.org/10.1021/acsmacrolett.7b00225 (2017).
Kleine, T. S. et al. High Refractive Index copolymers with improved thermomechanical properties via the inverse vulcanization of sulfur and 1,3,5-triisopropenylbenzene. ACS Macro Lett. 5, 1152–1156. https://doi.org/10.1021/acsmacrolett.6b00602 (2016).
SEM and TEM images were used to study the surface morphology in the PS composites. Figure 4a shows the SEM image of elemental sulfur particles in random size, whereas neat PS in Fig. 4b display the uniform smooth surface, similar smooth surface was also observed in PS-S and PS-SD composites (se Fig. 4c,d) indicate high level of dispersion and compatibility of sulfur with PS matrix. EDX and elemental mapping of the composites confirms the presence of sulfur, however the particles are not observed in the SEM image due to their smaller size. Uniform distribution of sulfur and carbon elemental images further supports the formation of homogeneous composites. Sulfur dispersion and their particle size was studied by TEM using thin films prepared by ultramicrotome (films thickness around 100 nm). In Fig. 4e, PS shows plane surface, whereas, the samples PS-S-5 and PS-SD-10 displayed the uniformly dispersed dark particles on the smooth surface without any agglomeration (see Fig. 4f,g), these particles are completely absent in the pure polystyrene. Enlarged image of PS-S-10 and PS-SD-10 in Fig. 4h,i respectively, suggest the dark particles are around 5 nm in size and are arises due to the higher electron density of sulfur. EDX analyses further confirms the presence of sulfur in the dark spots. High transparence of the composites can be related to the nano size and non-agglomerated sulfur and SD particles.
(a–c) Representative DMA curves, including tan δ, storage modulus (E′), and loss modulus (E″) of PS and its composites respectively. The experiments were carried out at a frequency of 1 Hz and a heating rate of 5 °C/min. (d) Tensile stress vs tensile strain curves of pure PS and their sulfur composites.
Determining the source of streaking or contamination in your molded parts is a critical step in perfecting your purging procedures ultimately saving you time and money.
Kim, H. et al. Synthesis and characterization of phosphorus- and sulfur-containing aromatic polyimides for High Refractive Index. Polymer 136, 143–148. https://doi.org/10.1016/j.polymer.2017.12.052 (2018).
Wadi, V. S., Jena, K. K., Halique, K. & Alhassan, S. M. Linear sulfur–nylon composites: Structure, morphology, and antibacterial activity. ACS Appl. Polym. Mater. 2, 198–208. https://doi.org/10.1021/acsapm.9b00754 (2020).
Kleine, T. S. et al. Infrared fingerprint engineering: A molecular-design approach to long-wave infrared transparency with polymeric materials. Angew. Chem. Int. Ed. 58, 17656–17660. https://doi.org/10.1002/anie.201910856 (2019).
Processors with sustainability goals or mandates have a number of ways to reach their goals. Biopolymers are among them.
Across all process types, sustainability was a big theme at NPE2024. But there was plenty to see in automation and artificial intelligence as well.
Kyprianidou-Leodidou, T. et al. High Refractive Index materials of iron sulfides and poly(ethylene oxide). J. Mater. Res. 12, 2198–2206. https://doi.org/10.1557/JMR.1997.0294 (2011).
Across the show, sustainability ruled in new materials technology, from polyolefins and engineering resins to biobased materials.
In this collection of content, we provide expert advice on welding from some of the leading authorities in the field, with tips on such matters as controls, as well as insights on how to solve common problems in welding.
Gifted with extraordinary technical know how and an authoritative yet plain English writing style, in this collection of articles Fattori offers his insights on a variety of molding-related topics that are bound to make your days on the production floor go a little bit better.
Successfully starting or restarting an injection molding machine is less about ticking boxes on a rote checklist and more about individually assessing each processing scenario and its unique variables.
GETTING A QUOTE WITH LK-MOULD IS FREE AND SIMPLE.
FIND MORE OF OUR SERVICES:
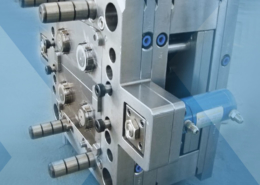
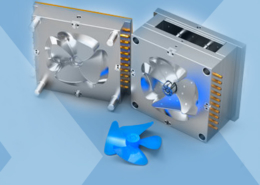
Plastic Molding

Rapid Prototyping
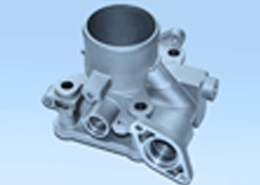
Pressure Die Casting
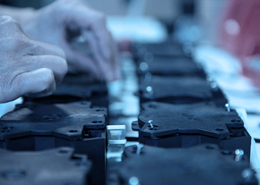
Parts Assembly
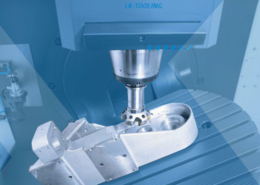