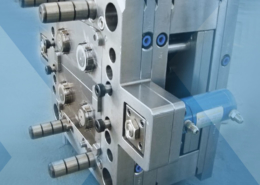
Continuous-fiber-reinforced thermoplastic composite adopted for car engine
Author:gly Date: 2024-09-30
Further advantages include improved dry cycle times and the overall stability of the mould itself. Lotan has ordered several more Shibaura Machine IMMs from TM Robotics, specifically its newest SXIII range of injection moulding machines. The SXIII is an enhanced performance model that provides significantly faster injection speeds than traditional moulding equipment. As a result, the machine offers a 35% faster cycle time than conventional hydraulic servo IMMs. Lotan also achieved a lower cost-per-mould.
Although hydraulic injection moulding machines are less expensive initially, it’s important to consider the whole life cost when buying new machines. This was demonstrated by TM Robotics’ customer Lotan, a manufacturer of plastic containers based in Leicestershire, UK. All of the injection moulding machines in Lotan’s production facility are electric, rather than hydraulic.
Here, Dervish Ibrahim, international sales manager at TM Robotics, explains why all-electric injection moulding machines are the way forward for reducing the process’s environmental impact — while also helping manufacturers achieve a lower cost-per-part.
According to the Journal of Clean Production, injection moulding may be responsible of up to 90% of the Global Warming Potential (GWP) created by the entire mould lifecycle, mainly caused by energy consumption.
Indeed, Shibaura Machine’s all-electric IMMs have been found to yield energy savings of 60% compared with European hydraulic servo IMMs. Other performance tests by Shibaura Machine measured its EC650SX-61B IMM, with a clamping force of 650 tons, against a hydraulic servo machine. It delivered a 51% energy reduction.
Further, validation testing at a Tier 1 parts supplier proved performance of the parts for rear half-shaft drive trains in electric vehicles (EVs), and this Tier 1 has asked Insit to begin commercial supply of the injection molded bellows for new EV models being launched in Europe, with start of production in 2023 and 2024.
Typically, 70% or more of a polymer’s global warming potential (GWP) is derived from its monomers. “Hytrel HTR9223LCF is manufactured utilizing monomers with significantly lower GWP,” explained Petros Dafniotis, global Hytrel T&I leader for automotive boots and bellows. A life-cycle assessment indicates that Hytrel HTR9223LCF can reduce GWP by 30% or more per part versus standard Hytrel commercial grades for constant velocity joint (CVJ) boots.
Although all-electric machines are initially more expensive with lower injection pressures, they are shown to outperform hydraulic versions in a variety of other ways. Advantages include higher rates and speeds of injection because the all-electric machining relies on toggle clamping rather than direct pressure clamping, which is better for high-speed injection moulding.
The team at Insit was very interested and asked the processing and advanced CAE experts at Celanese for support during trials of the material at a new Insit facility in Italy. The trials went so well that Insit introduced the parts to its Tier 1 customer, which also quickly recognized the value of the new material and the positive aspects of injection molded boots and bellows.
Aside from performance advantages, injection moulding machines must also be easy to use. This guarantees Lotan’s team can stay on-track to meet their key performance indicators (KPIs) by controlling the equipment and keeping it running sustainably. That’s why SXIII range of injection moulding machines are equipped with Shibaura Machine’s user-friendly controller that connects to Lotan’s programmable logic controller (PLC) for simple, repeatable operations.
“My team is very strong, but we also seek partnerships that bring us even further. The collaboration with Celanese has done exactly that, and helped my company win new business in an exciting and expanding part of the automotive industry,” Galgani commented.
But, what about the energy efficiency of all-electric versions hydraulically-powered machines? By using Shibaura Machine’s all-electric IMMs, Lotan has experienced 20 to 40% lower running costs compared with older-fashioned hydraulic machine. Traditional hydraulic injection moulding machines are also less efficient because they consume energy even while idle, whereas all-electric injecting machines only use energy while in action.
All-electric moulding machines also have the edge when it comes to maintenance. With PLC controllability, injection moulding operations can be tie-into the production facilities Internet of Things (IoT) things systems. Data on the IMM’s performance can be collected through sensors and relaid to the plant’s enterprise resource planning (ERP) or manufacturing execution systems (MES) to support preventive maintenance, traceability and quality management.
The company relies on Shibaura Machine’s all-electric injection moulding machines (IMM) supplied by TM Robotics. The machine is manufactured in-house by Shibaura Machine, formerly known as Toshiba Machine. Performance benefits of the IMM include a range of clamping force from 50 to 2,500 tons, which can be calibrated by a digital direct screw transfer (DST) control for added production flexibility.
In another instance, another EC-SX model, the 1,800 ton EC1800SX-155B, was tested against a competing all-electric IMM. Although both machines had the same energy consumption, the Shibaura Machine IMM delivered a faster cycle time, which gave overall energy efficiency savings of 30%.
By switching from press blow molding to injection molding automotive boots and bellows and using a newly developed elastomer, Insit increased productivity and reduced material usage.
Injection moulding is used to manufacture a huge variety of parts, and has several advantages. They include the ability to mould a wide variety of plastics, good repeatability, consistently high production with low waste and a low-cost-per-part — the latter is always a priority.
“The automotive industry needs to become more sustainable. We are pleased to be one of the first companies to test and certify the performance of Hytrel HTR9223LCF and look forward to press blow molding the material to help our customers reduce their environmental footprint,” added Galgani.
The Journal of Clean Production’s findings are a wake-up call to manufacturers, particularly as demand for injection moulding processes continue to grow. For example, the market for injection moulded medical devices plastics is expected to see booming growth between 2023 and 2030.
Injection moulding machines powered by a hydraulic motor can produce higher energy levels and higher injection pressures, and the initial cost of the machine is lower. But there are also disadvantages with hydraulic machines. They include the machine’s high consumption of electric energy, because its hydraulic power is connected to an electric power unit that works at maximum capacity during every phase of the moulding process.
In September 2022, Galgani and his leadership team were invited to attend a customer event at the Meyrin, Switzerland, facility of Celanese. There, Galgani and his colleagues learned about a new thermoplastic copolyester (TPC) elastomer, Hytrel HTR8745LV, that enables injection molding of diaphragm boots in multi-cavity molds. For manufacturers, injection molding offers the chance to increase productivity compared with blow molding and to save material by designing more compact bellows.
“The collaboration with Insit is a special one,” explained Fabio Bonfiglietti, the account manager who supports Insit. “Luigi Galgani has a vision for how he wants to run his company, for it to be innovative and to continue improving its sustainability. He keeps us on our toes with new developments, and he supports us when the materials are ready for testing and validation. His is a fun company to support.”
Stephen has been with PlasticsToday and its preceding publications Modern Plastics and Injection Molding since 1992, throughout this time based in the Asia Pacific region, including stints in Japan, Australia, and his current location Singapore. His current beat focuses on automotive. Stephen is an avid folding bicycle rider, often taking his bike on overseas business trips, and is a proud dachshund owner.
More than 90% of the costs of injection moulding can be attributed to energy use. This mainly applies to the electricity used to power and operate the injection moulding machine. As a result, there has been some debate in industry about the cost and sustainability advantages of hydraulic injection moulding versus all-electric machines.
Under the leadership of owner/president Luigi Galgani, automotive parts manufacturer Insit (Montà, Italy) has long been willing to experiment with new materials and processes. The results have been positive, as the company has expanded its manufacturing network beyond Italy to encompass Brazil and India, thereby supporting its global customer base. The majority of Insit’s business is generated by press blow molding of boots and bellows for the automotive industry. This is complemented by production of injection molded components, which are always processed using materials supplied by Celanese.
Maintaining a low cost-per-part throughout the manufacturing process is vital for reducing costs and delivering a higher product value — from both the manufacturer’s and the customer’s perspective. While injection moulding can support this, manufacturers are also concerned about the energy costs of injection moulding, and how this effects sustainability and the bottom line.
Material savings realized by injection molding of compact boots is one way to improve the sustainability of vehicles. Insit, however, has gone one step further as one of the first manufacturers to have tested and validated the performance of another recent Celanese innovation, Hytrel HTR9223LCF thermoplastic elastomer with a lower carbon footprint.
Injection moulding might presently be responsible of up to 90% of the processes GWP. However, the performance of all-electric IMMs like Shibaura Machine’s SXIII and EC-SX show this trend can be reversed, with positive effects on sustainability and also manufacturers’ bottom line.
GETTING A QUOTE WITH LK-MOULD IS FREE AND SIMPLE.
FIND MORE OF OUR SERVICES:
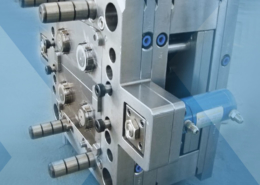
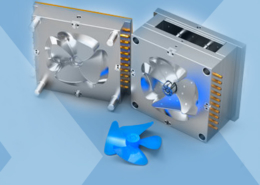
Plastic Molding

Rapid Prototyping
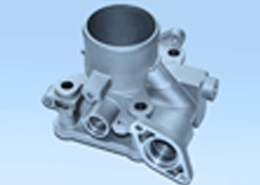
Pressure Die Casting
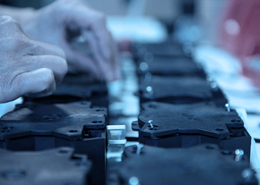
Parts Assembly
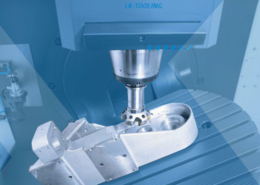