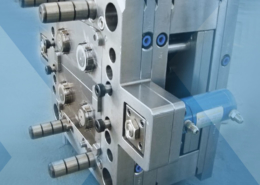
Composite processing technologies integrate press, injection molding - molding o
Author:gly Date: 2024-09-30
Pooling its engineering competences and technological resources, BASF’s Performance Materials division in collaboration with Sumitomo (SHI) Demag and H + S Automatisierung have created a manufacturing cell to produce a range of test specimens for the product development and research activities of thermoplastic polymers and compounds.
Sumitomo (SHI) Demag’s IntElect 1000 kN injection molding machine is at the core of a fully digitized manufacturing cell producing test specimens for product development and research involving thermoplastic polymers and compounds.
Then, the change of the mold inserts is synchronized to the cell control via output and input signals with transmission of the new mold data record via the robot interface. After the change of the mold insert, the temperature control units are heated up again. Automatic operation resumes and a new mold data record is initiated as soon as the target temperature is reached.
Taking center stage in the cell is Sumitomo (SHI) Demag’s ultra-precise IntElect 1000 kN injection molding machine. Selected for its compact design, energy efficiency, and repeatability, the IntElect’s enhanced welfare and safety features were also welcomed by the team of 30 research operatives at the facility. Progressive solutions to automate mold changes and low noise emissions combined with fully-digitized robotic processing solutions also received high marks.
Historically, Wilson was highly reliant on skilled injection molding specialists to create the molds along with engineers responsible for creating design inputs—both constrained resources that was limiting the team’s ability to innovate. “I have all these pain points along the way at the design and build phase,” notes Glen Mason, director of advanced manufacturing at Wilson. “What the freeform injection molding technology allows me to do is go from art to printed mold with no touch to make parts. That has completely transformed our workflow. In a constrained resource situation, we have dozens, potentially hundreds, of ideas that never see the light of day.”
Many of the specimens processed at BASF’s technical centre are high-temperature thermoplastics, fiber reinforced and often flame retardant. Consequently, melt temperatures can reach up to 400°C with mold temperatures hitting 180°C.
Angelika Homes comments: “Unlike our former MES systems, this one logs every single aspect of a trial and the results, giving us insight for every single shot. This data is extremely valuable as it represents the entire processing sequence and enables us to draw deeper conclusions about how materials perform under certain conditions and how a customer might later process it.”
In order to hit it out of the park, Wilson Sporting Goods needed a workflow that allowed the sporting goods manufacturer to take concept bats from “art to part” in the shortest amount of time without dependence on highly-trained injection molding experts. Wilson’s goal was to zero in on an alternative to its traditional metal tooling and prototyping methods, allowing it to quickly crank out functional and testable prototypes and get product to market quicker.
The Nexa3D/Addifab digital workflow gets Wilson to fully molded parts in hours, allowing the bat design team to make better decisions about future products. For instance, mold build time has gone from two weeks to one week, and the overall idea-to-part time has been cut from 12 weeks to seven weeks (a 40% decrease) while also removed two “touch points” in the process that previously required expert input, Mason says. AM-produced tooling also eliminates much of the design complexity associated with traditional subtractive molding when producing complex geometries. “A lattice is a great example of an incredibly complex (or impossible) shape that would require massive design and build efforts when the 3D printed version is extremely easy,” Mason says.
BASF’s MES informs the cell when the current produced sample setting is about to end, lining up the next mold application. Immediately after the injection process stops, cooling of the mold insert is directed by the integrated temperature control unit interface.
Automation Systems Senior Engineer at Sumitomo (SHI) Demag, Markus Hausmann explains: “In order to lower the temperature to 80°C and depressurize the insert to guarantee that the SDR robot can remove the mold insert safely, our machine control has to talk and interact seamlessly with BASF’s MES.
Using AM to quickly prototype bat parts is just one part of the equation. Mason says it’s just as important to prototype the process to determine whether the combined design and material produces a winning bat at scale. “A prototype part only informs me about fit and function and if it’s not in the correct material, I can’t even do performance testing,” Mason explains, adding the end product from the AM-only process is just a novelty. “That’s really where our 3D printing journey was prior to Addifab and Nexa3D. “We were making things to look at, but they were almost useless.”
The solution came in the form of a new digital workflow combining 3D printing and freeform injection molding delivered through a partnership with Nexa3D and Addifab (Nexa3D acquired Addifab in April). Nexa3D’s large print build envelope and ultrafast LSPc process lets multiple parts be printed simultaneously and quickly, allowing the R&D team to explore multiple design iterations in a single print batch. The addition of the Addifab solution brings fast-turn, plastic injection molding into the mix to produce the proposed bat part prototypes—a process change that has been instrumental to shortening the product development lifecycle.
For BASF, solving the punch challenge was one of the greatest engineering accomplishments. Due to its extensive application profile, BASF tests a wide range of materials from soft and tough to stiff and brittle polymers. There are also many different sample geometries, including thicknesses varying from 0.8 to 4 mm. All BASF test specimens are manufactured in accordance with the ISO 294 standard. This specifies the precision of the sprue system and specific requirements each sample geometry must fulfil. “Removal by punch is a pre-requisite, as it does not change the material properties and eliminates dust particles,” explains Hausmann.
The multifunctional gripper ensures all sample geometries are placed with exacting precision onto the punch plate. This is complex in itself because BASF works with many materials that have high fiber glass content, which can cause warpage. Describing how the servo driven parallel punch gripper overcomes the challenge of placing parts securely onto the punch plate, Hausmann notes: “If the test specimens are not held sufficiently well in place, the punchings could be crooked or not conform to specified quality standards.”
The Nexa3D and Addifab system helps the Wilson R&D team eliminate steps when designing new tooling for baseball bats. Image Courtesy of Wilson Sporting Goods
Integrating BASF’s existing mold insert concept and special features into the injection unit, the installation also includes a thermal temperature control unit and a new digital Manufacturing Execution System (MES) to map each test sequence. Reinhard Jakobi, Head of Performance Materials Processing at BASF, describes the project as an achievement of advanced engineering combining mature technology with state-of-the-art automation and molding precision.
At the pilot center, the BASF research team typically configures 20 test settings daily on this machine. That means the control program of the cell has to be adapted to different materials, sample geometries, temperatures, and processing parameters. Every single setting that runs is recorded and documented digitally.
Creating tomorrow’s polymer innovations starts with understanding the chemical and mechanical performance and processing conditions of materials. At BASF’s Injection Molding & Extrusion Pilot Plant in Ludwigshafen, Germany, the newest all-electric, fully-automated injection molding cell from Sumitomo (SHI) Demag is delivering pioneering and repeatable results for more than 4,000 tests a year.
At any time, up to 12 interchangeable inserts can be loaded to the side magazine and then swapped automatically into the injection molding machine. By integrating an HB-Therm temperature control system with Sumitomo (SHI) Demag’s machine control, automated mold insert changes can be completed safely and efficiently, even when running the process at high mold temperatures.
As parts and tooling get even more complex, Mason expects Wilson to expand its use of similar digital workflows. “I don’t see a future that is less complex than the present,” he says. “Using a workflow that allows us to quickly test and develop parts and processes with an ever-increasing complexity enabled by low-cost, elegant AM technology will only become more valuable as time goes on.”
For operative safety and efficiency, a linear SDR 5-35S robot serves two purposes. A new feature is full automation of the selection and placement of 12 interchangeable mold inserts from a magazine located within the cell. After the part is molded, the same robot fitted with a multifunctional gripper gently extracts the test specimen from the mold and passes it to the small six-axis, articulated-arm Yaskawa GP8 robot for precise cutting of the specimens from the gate using a servo spindle drive punching machine.
GETTING A QUOTE WITH LK-MOULD IS FREE AND SIMPLE.
FIND MORE OF OUR SERVICES:
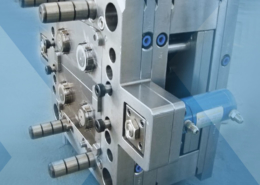
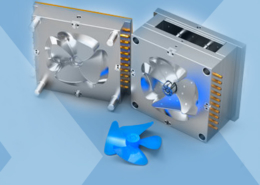
Plastic Molding

Rapid Prototyping
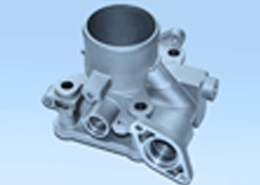
Pressure Die Casting
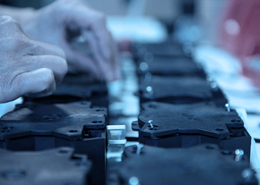
Parts Assembly
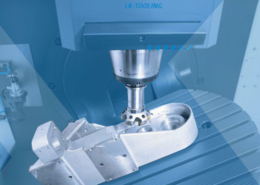