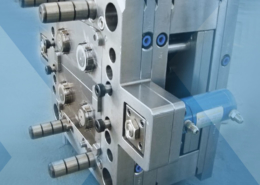
Combining plastics and composites for Class A parts without tools - frp injectio
Author:gly Date: 2024-09-30
Based on material type, the market is divided into Liquid-crystal polymer (LCP), Polyether ether ketone (PEEK), Polycarbonate (PC), Polyethylene (PE), Polyoxymethylene (POM), Others. Polycarbonate held the dominant market share of USD 0.3 billion in 2022. Polycarbonate is known for its optical clarity and high light transmission properties, making it ideal for applications where transparency is essential, such as optical components, lenses, and displays. The exceptional impact resistance of polycarbonate is a significant driver for its use in industries such as consumer electronics, automotive, and medical devices, where durable and shatter-resistant components are needed.
The demand for micro injection molded plastic components varied across industries during the pandemic. While there was increased demand for medical devices and protective equipment, other industries, such as automotive and consumer electronics, experienced reduced demand. Many manufacturers of micro injection molded plastic components had to reduce or halt production temporarily due to health and safety concerns for their workers. This led to a decrease in the supply of micro-molded products.
Vinny Sastri, who wrote the book — literally — on “Plastics in Medical Devices,” speaks to the ins and outs of process validation for the medtech supply chain.
BASF SE and Isometric Micro Molding, Inc.are dominant players in the micro injection molded plastic business due to their vast product portfolio. BASFs ecosystem integration, along with consistent innovation, have attracted millions of customers. Their brand recognition and exclusive content deals solidify their leadership in the highly competitive market.
The medical and healthcare sector is a significant driver of the micro injection molded plastic industry. The demand for micro-molded components for medical devices, diagnostics, and drug delivery systems is rising due to advancements in healthcare technology and an aging population. Advancements in polymer technology have led to the development of high-performance materials suitable for micro injection molding. These materials offer enhanced mechanical properties, biocompatibility, and resistance to extreme conditions, expanding the range of applications.
Part of a panel at the conference discussing the characterization and validation of medical devices, Sastri stressed to PlasticsToday the importance of the update to 21 CFR Part 820, which, as defined by FDA, covers the “design, manufacture, packaging, labeling, storage, installation, and servicing of all finished devices intended for human use.” The update, notes Sastri, “will be aligned with and reference most sections of ISO 13485:2016. It will replace the current regulation as it stands. Companies need to make sure that they meet the requirements for the validation of processes per ISO 13485:2016. Any identified gaps must be addressed.”
Joining him on the panel at the conference are Ali Ashter, CEO, Ashter Enterprise LLC, and a delegation from Cambridge Polymer Group including company president Stephen Spiegelberg; Becky Bader, associate director of chromatography; Jamiee Robertson, research scientist; and Michael Young, senior research chemist.
Process validation, in the broadest sense, demonstrates that the control of manufacturing processes consistently produces devices that are safe and effective, Sastri explains. While the “company that owns the registration to the medical device — the OEM — has the responsibility to comply with medical device regulations and standards, it will need to control suppliers whose products and raw materials have a significant effect on patient and user safety.” Depending on the risk of the supplied part or raw material — when used with implants, for example — the OEM may require a Tier 1 supplier to apply appropriate controls over its suppliers, Sastri adds. “Over the last 25 years, scores of deaths and injuries resulted from the lack of control over suppliers,” says Sastri, who is the author of Plastics in Medical Devices: Properties, Requirements and Applications, published by Elsevier (London).
FDA’s 21 CFR Part 820 — Quality System Regulation (QSR) has not been updated since it was first released in 1996 . . . until now. Are you ready?
FDA proposed aligning its regulations with ISO 13485: 2016, the international quality management system standard, in February 2022. Some time this year, the agency will update and release its QSR requirements, and the medical device manufacturing supply chain will need to be prepared. Vinny Sastri, president of Winovia, a consultancy helping the medical device industry comply with quality system regulations, will speak to this and broader issues involving process validation for medical device plastics and products at the forthcoming MiniTec conference track presented by the Society of Plastics Engineers (SPE). The track is part of the Informa Markets Engineering (IME) West event, which includes the co-located Medical Design & Manufacturing (MD&M) and Plastec West trade shows and associated conferences, coming to the Anaheim Convention Center in Anaheim, CA, on Feb. 6 to 8, 2024.
Setting up the tooling and molds for micro-injection molding can be expensive, especially for small production runs. This initial cost can be a barrier for small and medium-sized enterprises (SMEs) and startups. The choice of the right material is crucial for micro-injection molding. Finding materials that meet the stringent requirements for micro-sized components can be challenging.
The medical and healthcare industry relies on micro-injection molding for the production of precise and sterile components such as syringe barrels, catheters, and other medical devices. The demand for such products continues to rise with the aging global population and advancements in medical technology. The automotive industry uses micro-injection molding for producing small and intricate parts, including connectors, sensors, and interior components. As vehicles become more sophisticated with advanced electronics and sensors, the demand for micro-molded plastic parts increases.
Based on application, the market is categorized into medical and healthcare, automotive, electronics, telecommunications, aerospace and defense, others. Medical and healthcare accounted for over 45% market share in 2022 and is projected to grow through 2032. The trend towards smaller, minimally invasive medical devices and drug delivery systems creates a strong demand for micro injection molded components. The medical sector demands materials that are biocompatible and safe for use in implantable devices and diagnostic equipment.
While suppliers to the medtech industry have been known to grouse about “overly burdensome” regulations, there is a business argument to be made for diligent compliance. “Suppliers to the medtech industry who demonstrate control of their products and processes can leverage this competency to continue to make inroads and increase their customer base, leading to increased sales,” says Sastri. The proof, incidentally, is on the MD&M West show floor, where top-tier suppliers put their quality systems credentials front and center in their booth. It clearly represents a competitive advantage.
Looking for more? Our expert team of researchers can create market analysis reports for any of your needs.
Home > Chemicals & Materials > Polymers > Industrial Polymers > Micro Injection Molded Plastic Market
North America dominated the global micro injection molded plastic market in 2022. Within North America, the U.S. generated a revenue of over USD 0.2 billion in 2022 The aging population in North America drives the demand for medical devices, diagnostics, and drug delivery systems, which often rely on micro injection molded components. North America is a major center for technology and electronics innovation, leading to increased demand for micro injection molded plastic components in applications like smartphones, wearable technology, and other electronic devices.
A leading industry expert in FDA and ISO quality management systems and a certified Six Sigma black belt, Sastri has a strong track record in leading, managing, establishing, and implementing quality initiatives into client organizations around the world.
Global Market Insights Inc. 4 North Main Street, Selbyville, Delaware 19975 USA Toll Free: +1-888-689-0688 USA: +1-302-846-7766 Europe: +44-742-759-8484 APAC: +65-3129-7718 Email: sales@gminsights.com
Micro Injection Molded Plastic Market was valued at USD 1.2 billion in 2023 and is anticipated to register a CAGR of over 11% between 2024 and 2032. As electronic devices become smaller and more compact, there is a growing need for micro-molded plastic components to fit within tight spaces. This includes components for smartphones, wearable devices, medical devices, and more.
I asked Sastri for three key takeaways he hopes to leave conference attendees with at the session scheduled for Feb. 6 at 1:30 p.m. “An understanding of the basic regulatory requirement and principles of process validation,” topped the list. Moreover, attendees will see that understanding applied to a practical example and will walk away with the ability to “identify how to demonstrate compliance to process validation within an organization or company,” Sastri adds.
Editor in chief of PlasticsToday since 2015, Norbert Sparrow has more than 30 years of editorial experience in business-to-business media. He studied journalism at the Centre Universitaire d'Etudes du Journalisme in Strasbourg, France, where he earned a master's degree.
The trend of miniaturization in various industries, including electronics, medical devices, and automotive, is driving the demand for micro injection molded plastic components. As products become smaller and more complex, the need for precise, small plastic parts continues to grow.
GETTING A QUOTE WITH LK-MOULD IS FREE AND SIMPLE.
FIND MORE OF OUR SERVICES:
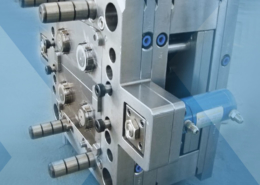
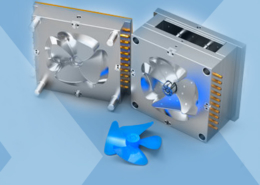
Plastic Molding

Rapid Prototyping
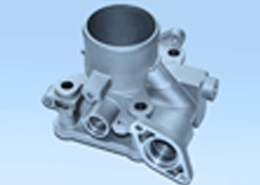
Pressure Die Casting
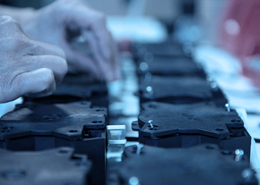
Parts Assembly
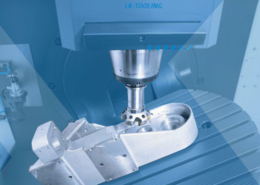