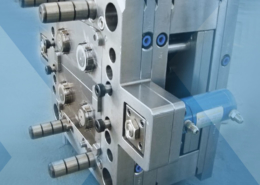
China’s Haitian breaks ground for production plant in Serbia - haitian injection
Author:gly Date: 2024-09-30
More than half of those surveyed (55%) say that their company’s top leadership recognizes additive manufacturing as a strategic capability.
FDA began evaluating medical plastic syringes made in China near the end of last year when it learned of quality issues such as leakage or breakage and the potential that the faulty syringes may deliver incorrect dosages of medication. This week FDA reported in an update that the quality issues were more widespread than originally known. It sent warning letters to some China-based manufacturers of plastic syringes as well as US-based Medline Industries and Sol-Millennium, which market the syringes domestically.
Noting that no BD syringes are mentioned in FDA’s safety communication, which recommends that users in the United States transition away from China-made syringes, Borin stressed that ensuring the safety and quality of its products is a priority at the 125-year-old medical device company. Notably, BD manufactured two billion additional syringes and needles to support the global response to the COVID-19 pandemic.
Prototyping is also widely recognized as the area most benefited by additive manufacturing (selected by 96% of respondents), followed by design (52%) and small-scale production (27%).
Stephen has been with PlasticsToday and its preceding publications Modern Plastics and Injection Molding since 1992, throughout this time based in the Asia Pacific region, including stints in Japan, Australia, and his current location Singapore. His current beat focuses on automotive. Stephen is an avid folding bicycle rider, often taking his bike on overseas business trips, and is a proud dachshund owner.
One of the largest medical device companies in the world, BD also claims to be one of the largest users of plastic injection molded products in the world. At the groundbreaking of BD’s plant in Columbus, NE, James Borzi, executive vice president and chief supply chain officer at the time, said that the new facility will “centralize a majority of BD’s North American plastic molding production and will support multiple business units in the United States and around the world.” BD operates three other facilities in Nebraska.
74% of survey participants printed at least 10,000 parts last year, while 36% polled printed up to 100,000 parts in that same timeframe.
Editor in chief of PlasticsToday since 2015, Norbert Sparrow has more than 30 years of editorial experience in business-to-business media. He studied journalism at the Centre Universitaire d'Etudes du Journalisme in Strasbourg, France, where he earned a master's degree.
While almost all respondents described the expected benefits of 3D printing, the most frequent benefit discussed was faster part delivery timelines.
Issues with the cost and availability of materials are extremely prevalent, noted by 85% of decision makers, increasing 31% from 2021.
"BD has the capacity to support additional syringe demand and is further increasing US production to help ensure continuity of patient care,” said BD Medication Delivery Solutions President Eric Borin in today’s announcement. “Since the initial FDA safety communication in November, BD has increased domestic manufacturing of syringes in our Nebraska and Connecticut facilities to respond to customer needs.”
Prototyping remains the primary application of 3D printing, according to a survey of decision makers who oversee 3D printing within their organizations.
While participants aren’t as bullish on overall 3D printing industry growth, they are expecting larger growth in the use of 3D printing for production parts or goods in the next three to five years.
Lest this week’s news about FDA cautioning against the use of plastic syringes made in China raise concerns of a possible shortage, BD announced today that it is increasing its US production of syringes.
96% of participants use in-house 3D printing, but outsourcing is still typical, especially with additive networks and contract manufacturers.
The medtech giant is ramping up domestic syringe production in light of FDA’s recommendation to transition away from plastic syringes made in China.
Prototyping remains the predominant use of additive manufacturing, according to a survey of 200 mid- to senior-level decision makers who oversee additive manufacturing within their organizations. While the survey commissioned by design engineering, manufacturing, and supply chain services company Jabil revealed that a majority of respondents continue to use the technology for prototyping purposes, it also showed consistent growth since 2017 in the use of 3D printing for production parts, bridge production, and jigs, fixtures, and tooling.
Seven in 10 decision makers expect moderate growth of 3D printing for their company in the next two to five years; this contrasts with “significant” growth reported in previous surveys.
Almost all respondents (96%) said their organization would want to use metal additive materials if certified versions were available at a reasonable cost, followed closely by plastics/polymers (88%).
GETTING A QUOTE WITH LK-MOULD IS FREE AND SIMPLE.
FIND MORE OF OUR SERVICES:
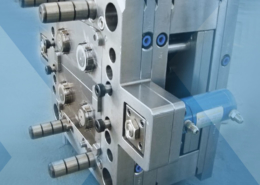
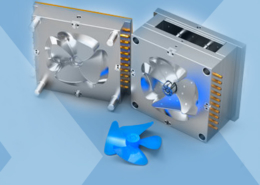
Plastic Molding

Rapid Prototyping
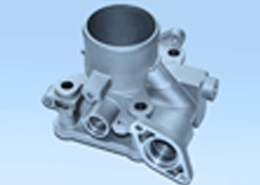
Pressure Die Casting
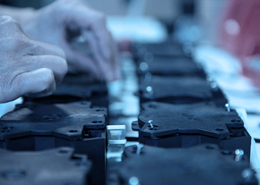
Parts Assembly
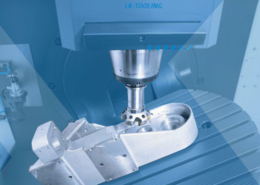