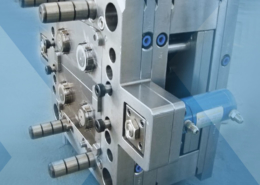
China Plastic Injection Molding Supplier Custom Plastic Molded Parts - injection
Author:gly Date: 2024-09-30
Sabic fully supports its new PP compound portfolio with extensive expertise in foamed part design, development, and processing, as well as predictive engineering. For instance, the company can provide guidance on the selection of the appropriate chemical blowing agent for each grade. Sabic’s technical team will collaborate with customers to achieve desired aesthetics at the lowest possible part weight.
The choice between the short-shot and core-back techniques, with their different tooling requirements, also helps to determine whether FIM with Sabic PP compounds is cost neutral or delivers cost savings. Additional cost savings are possible through cycle time reductions from flow improvements inherent in FIM.
Precision Southeast Inc., which also has a facility in Indiana, specializes in custom injection molding along with several engineering services, including metal-to-plastic conversions, rapid prototyping and tooling. The company’s press sizes range from 20 to 600 tons. Precision offers overmolding and in-mold assembly and a range of value-add services, such as assembly, ultrasonic welding, leak testing and decorating that includes pad printing and hot stamping.
The transaction facilitates the merger of two Gladstone Investment Corp. portfolio companies to establish a custom injection molding company with facilities in New Hampshire, South Carolina and Indiana that offer a comprehensive range of plastic injection molding capabilities. The credit agreement was used to pay off existing debt and to consolidate the debt capital in the resulting consolidated entity.
To drive future developments in polymer foams, Sabic operates a Foam Innovation Center in the Netherlands. This center, which is equipped with foam process capabilities as well as analytical equipment, enables the company to develop new foam solutions and technology innovations and collaborate with customers.
Finished inner tailgate trim part made with Sabic PPc F9005 grade through foam injection molding. The molded part features fixations, ribs, honeycomb, doghouse, domes, holes, textures, and excellent aesthetics. Sabic’s PP compound has high flow, can decrease sink marks, and reduces weight by up to 30%.
Another consideration is the foaming process, which can use chemical or physical agents. The new Sabic PP compounds are good candidates for use with chemical blowing agents, which are typically preferred for visible foamed parts. These agents are introduced to the molding machine in the form of a masterbatch, along with the plastic pellets, and activated during the melt phase to release gases for foaming.
Until she retired in September 2021, Clare Goldsberry reported on the plastics industry for more than 30 years. In addition to the 10,000+ articles she has written, by her own estimation, she is the author of several books, including The Business of Injection Molding: How to succeed as a custom molder and Purchasing Injection Molds: A buyers guide. Goldsberry is a member of the Plastics Pioneers Association. She reflected on her long career in "Time to Say Good-Bye."
“The automotive industry continues to look for new weight-out strategies that can advance energy efficiency and sustainability goals,” said Sabic’s Abdullah Al-Otaibi, General Manager, ETP & Market Solutions. “Although foam injection molding produces desirable lightweight parts, manufacturers have been forced to sacrifice aesthetics . . . until now. We applied our extensive expertise in foaming technology to develop these new compounds to help resolve the issue of surface quality and open new application opportunities for foamed parts.”
Previously, the FIM process was essentially limited to non-visible parts, restricting its usefulness in automotive applications. Foaming can underperform in surface aesthetics — silver streaking, swirl lines and dimples are common defects. Sabic PP compounds for foamed interior parts deliver low-gloss textured (grained) surfaces with uniformly high quality and eliminate streaking and swirling. Talc filler in these grades acts as a nucleator that promotes the generation of finer bubbles, which contribute to a consistent surface appearance. For enhanced aesthetics, these grades are currently available in selected automotive interior colors. Custom coloring is also available.
Sabic has introduced a specialized portfolio of Sabic PP compounds for foam injection molding (FIM). New mineral-reinforced Sabic PPc F9005, PPc F9007, and PPc F9015 grades can help deliver attractive aesthetics for visible automotive interior parts with complex geometries, such as door panels and trim, seat and trunk cladding, A/B/C/D pillar covers, and center consoles.
Core-back molding, which requires part redesign and new tooling, can lower weight by as much as 30%. Both Sabic PPc 9005 and PPc 9015 grades are formulated for core-back molding and deliver medium stiffness and impact.
The merger establishes a custom injection molding company with facilities in New Hampshire, South Carolina and Indiana that offer a comprehensive range of plastic injection molding capabilities.
Unlike standard FIM materials, which typically exhibit surface defects, the new advanced PP compounds feature uniformly high surface quality similar to solid injection molded parts. Compared with solid components, foamed parts made with Sabic PP compounds offer significant weight savings that can help cut emissions. According to a cradle-to-grave life-cycle assessment study (pending third-party review), the advanced materials can help OEMs lower carbon dioxide (CO2) emissions by as much as 15%.
GI Plastek (Wolfeboro, NH) has merged with Precision Southeast Inc. (Myrtle Beach, SC) to create PSI Molded Plastics Inc. Citizens Bank’s Commercial Banking unit is providing $23 million in credit to help fund the merger.
GI Plastek is a manufacturer of custom injection molded products using structural foam, gas assist and straight injection molding. It also offers value-added assembly and secondary finishing operations, including painting, inserting and decorating. The company’s press sizes run from 220 to 1,574 tons. In 2016, GI Plastek added two new large tonnage machines with an 1,100- and 500-ton clamping force and installed a new multi-booth mechanized paint line for a total investment of $2 million, according to the company’s website.
Short-shot molding, which uses the same tooling as an injection molded part, can reduce weight by up to 10%. Sabic PPc 9007 is formulated for short-shot FIM and low-impact applications.
In August 2009, Wincove Capital acquired GI Plastek. Six years later, Gladstone Investment Corp. acquired Wincove-GIP Acquisition Inc. (d.b.a. GI Plastek) from Wincove Capital.
GETTING A QUOTE WITH LK-MOULD IS FREE AND SIMPLE.
FIND MORE OF OUR SERVICES:
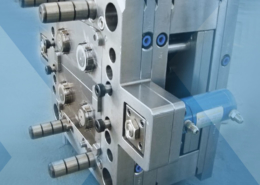
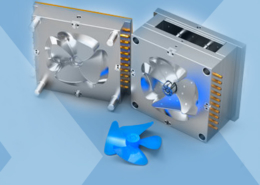
Plastic Molding

Rapid Prototyping
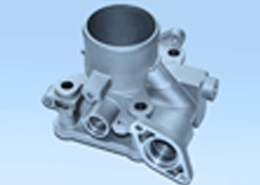
Pressure Die Casting
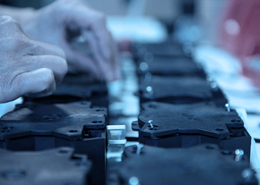
Parts Assembly
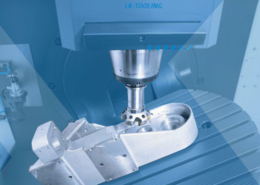