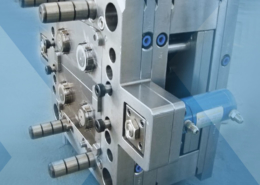
Checkerspot releases algae-based plastics prototype kit for designers - casting
Author:gly Date: 2024-09-30
LSR molding of complex part geometries and difficult materials like fluorosilicone has become a core competency at NPI/Medical. Here are two of the plant’s four 55-ton LSR presses.
Plastics Technology’s Tech Days is back! Every Tuesday in October, a series of five online presentations will be given by industry supplier around the following topics: Injection Molding — New Technologies, Efficiencies Film Extrusion — New Technologies, Efficiencies Upstream/Downstream Operations Injection Molding — Sustainability Extrusion — Compounding Coming out of NPE2024, PT identified a variety of topics, technologies and trends that are driving and shaping the evolution of plastic products manufacturing — from recycling/recyclability and energy optimization to AI-based process control and automation implementation. PT Tech Days is designed to provide a robust, curated, accessible platform through which plastics professionals can explore these trends, have direct access to subject-matter experts and develop strategies for applying solutions in their operations.
Formnext Chicago is an industrial additive manufacturing expo taking place April 8-10, 2025 at McCormick Place in Chicago, Illinois. Formnext Chicago is the second in a series of Formnext events in the U.S. being produced by Mesago Messe Frankfurt, AMT – The Association For Manufacturing Technology, and Gardner Business Media (our publisher).
Second quarter started with price hikes in PE and the four volume engineering resins, but relatively stable pricing was largely expected by the quarter’s end.
Kelly notes that there are good reasons for a QTM client to stick with NPI/Medical for full production. “If you change vendors after the development stage, you lose everything that was learned to date about how to process the part. You’re starting out afresh.”
Core Technology Molding turned to Mold-Masters E-Multi auxiliary injection unit to help it win a job and dramatically change its process.
Introduced by Zeiger and Spark Industries at the PTXPO, the nozzle is designed for maximum heat transfer and uniformity with a continuous taper for self cleaning.
In this collection of content, we provide expert advice on welding from some of the leading authorities in the field, with tips on such matters as controls, as well as insights on how to solve common problems in welding.
The largest press is a 300-ton Milacron Vista Hydraulic machine. Most of the other larger presses—85 and 110 tons—are all-electric models, including nine Roboshot 110-tonners from Milacron/Fanuc . The rest are mainly Arburg’s and one Nissei press.
Kelly continues, “We support startups. A lot of big companies won’t do that. Our bigger competitors don’t want to deal with low volumes. We even offer medical validation on low-volume development work—say, 1500 parts a year. A lot of companies won’t even consider that.”
In particular, NPI/Medical concentrates on surgical and diagnostic devices, as well as life-sciences products—DNA sequencers, filters, etc. “We’re not a commodity medical molder—no 64-cavity syringes here,” says Kelly. “We use up to eight cavities in production, and our machines go up to 300 tons.” Prototyping at NPI/Medical is generally in single-cavity tools, except for family molds.
Learn about sustainable scrap reprocessing—this resource offers a deep dive into everything from granulator types and options, to service tips, videos and technical articles.
The Plastics Industry Association (PLASTICS) has released final figures for NPE2024: The Plastics Show (May 6-10; Orlando) that officially make it the largest ever NPE in several key metrics.
Take a deep dive into all of the various aspects of part quoting to ensure you’ve got all the bases—as in costs—covered before preparing your customer’s quote for services.
Across the show, sustainability ruled in new materials technology, from polyolefins and engineering resins to biobased materials.
The development of process optimisation systems, integrating material and knowledge with simulation tools is probably the most exciting development on the horizon, claims Sargisson. Such systems will enable processors to observe advanced settings and capture deeper processing insights.
This Knowledge Center provides an overview of the considerations needed to understand the purchase, operation, and maintenance of a process cooling system.
Exhibitors and presenters at the plastics show emphasized 3D printing as a complement and aid to more traditional production processes.
Join KraussMaffei for an insightful webinar designed for industry professionals, engineers and anyone interested in the manufacturing processes of PVC pipes. This session will provide a comprehensive understanding of the technology behind the production of high-quality PVC pipes: from raw material preparation to final product testing. Agenda: Introduction to PVC extrusion: overview of the basic principles of PVC pipe extrusion — including the process of melting and shaping PVC resin into pipe forms Equipment and machinery: detailed explanation of the key equipment involved — such as extruders, dies and cooling systems — and their roles in the extrusion process Process parameters: insight into the critical process parameters like temperature, pressure and cooling rates that influence the quality and consistency of the final PVC pipes Energy efficiency: examination of ways to save material and energy use when extruding PVC pipe products
Successfully starting or restarting an injection molding machine is less about ticking boxes on a rote checklist and more about individually assessing each processing scenario and its unique variables.
Across all process types, sustainability was a big theme at NPE2024. But there was plenty to see in automation and artificial intelligence as well.
Springs made of Sabic’s glass-filled Ultem PEI are one Quick-Turn Manufacturing (QTM) success story. Used in medical, drug-delivery, and food-processing equipment (among other applications), the LeeP springs from Lee Spring Co., Brooklyn, N.Y., boast high strength and heat and chemical resistance. The tooling required six actions, each pulling from a different angle—no ordinary prototype mold—and yet complete tool design and build took around five weeks from approved CAD model to molded parts. Product was delivered to market eight weeks after the first concept discussions.
Mixed in among thought leaders from leading suppliers to injection molders and mold makers at the 2023 Molding and MoldMaking conferences will be molders and toolmakers themselves.
Production monitoring, scheduling, and lot control (essential for medical jobs) are managed by a central ERP system from IQMS, which has been in place for eight years. Kelly is looking for systems that give him more data on his operations. For future machine purchases, he’s interested in controls that capture more process data that he can access from his office desktop. He also likes the fact that one of his newer machines, a 110-ton Wittmann Battenfeld EcoPower hybrid press, has capability for remote diagnostics via the Internet.
When, how, what and why to automate — leading robotics suppliers and forward-thinking moldmakers will share their insights on automating manufacturing at collocated event.
Certified to ISO 13485:2003 and ISO 9001:2008 quality standards, NPI/Medical does work for both small startups and large medical OEMs. Kelly notes that a wave of consolidation among medical OEMs is putting additional demands on molders serving them.
Discover how artifical intelligence is revolutionizing plastics processing. Hear from industry experts on the future impact of AI on your operations and envision a fully interconnected plant.
After successfully introducing a combined conference for moldmakers and injection molders in 2022, Plastics Technology and MoldMaking Technology are once again joining forces for a tooling/molding two-for-one.
In a time where sustainability is no longer just a buzzword, the food and beverage packaging industry is required to be at the forefront of this innovation. By adopting circular packaging processes and solutions, producers can meet regulatory requirements while also satisfying consumer demand and enhancing brand reputation. Join Husky to learn more about the broader implications of the circular economy — as well as how leading brands are leveraging this opportunity to reduce costs, increase design flexibility and boost product differentiation. Agenda: The cost and operational benefits of embracing circularity Key materials in circular packaging — including rPET and emerging bioplastics How to design a circular food and beverage package Strategies for selecting sustainable closures to future-proof packaging solutions Optimization and streamlining of production processes for enhanced efficiency How Husky Technologies can enable your sustainable success
The plant employs 95 and houses 46 injection machines from 28 to 300 tons. The firm’s revenues are split 70-30 between production molding and QTM development work. Kelly projects double-digit growth for the next five years and has budgeted for two more presses this year. Says Ball, “This existing plant can support growth to $35 million in annual business.”
Seven JSW presses from 40 to 85 tons are dedicated to QTM business, though NPI/Medical will use its larger production equipment when necessary. Clean-room molding options are available for all but the lowest DynaClass level.
Core business today is development and production of medical parts, even in volumes of a few hundred parts a year. Shown here: a row of all-electric machines.
While prices moved up for three of the five commodity resins, there was potential for a flat trajectory for the rest of the third quarter.
“But we also do development work for customers we know we won’t do production for, such as those that have in-house molding capability or already have a production molder signed up. In some cases, we do QTM development for high-volume, precision industrial applications that aren’t suitable for production here. Like batteries, for instance. I don’t want my production machines tied up with anything but medical business.”
What the two businesses have in common is a focus on speed, service, and technical sophistication. For speed, NPI/Medical relies on a substantial in-house tooling department, which can produce single-cavity, tight-tolerance steel prototype molds in two to four weeks. At NPI/Medical, the word “prototype” could give the wrong impression—these tools mold production-quality parts within a prototype time frame.
Also observed during the pandemic, larger scale adoption of home healthcare and smart diagnostic devices, continues to accelerate at pace.
“When one OEM buys another, every vendor has to defend its position in the supply chain. And you must have the flexibility to adopt the new protocols of the acquiring company.”
As for technical sophistication, Kelly says, “If a customer needs a PC/ABS cover, they don’t even think of us. We’re the company that can do the tough stuff. Our niche is tight tolerances and engineering materials—PEEK, PPS, Ultem polyetherimide (PEI), Radel polyphenylsulfone, liquid-crystal polymer (LCP). It’s one of the reasons people come to us.”
Gifted with extraordinary technical know how and an authoritative yet plain English writing style, in this collection of articles Fattori offers his insights on a variety of molding-related topics that are bound to make your days on the production floor go a little bit better.
The aim of this presentation is to guide you through the factors and the numbers that will help you determine if a robot is a smart investment for your application. Agenda: Why are you considering automation? What problems are you trying to solve? How and why automation can help Crunch the numbers and determine the ROI
The toolroom builds eight to 10 QTM molds a month, satisfying 85-90% of the firm’s development needs. However, NPI/Medical outsources all its production tooling to local moldmakers.
To support these efforts, the company’s R&D team continues to develop an IoT dashboard to facilitate data analysis and visualisation, transfer and storage of know-how, as well as maintenance planning and prediction. Within this assistance system, additional autonomous and interconnected functions are being conceived to provide valuable insight into the machine performance and different production variables.
In this three-part collection, veteran molder and moldmaker Jim Fattori brings to bear his 40+ years of on-the-job experience and provides molders his “from the trenches” perspective on on the why, where and how of venting injection molds. Take the trial-and-error out of the molding venting process.
While prices moved up for three of the five commodity resins, there was potential for a flat trajectory for the rest of the third quarter.
A well-equipped toolroom with six CNC machining centers and five EDM systems helps NPI/Medical produce 8 to 10 QTM molds a month.
Kelly explains another synergy between QTM and production molding. “QTM supports us through our customers’ long development cycle before we get the production order. It takes only a few weeks to build a prototype tool, but the time frame from concept to prototype to testing, design changes, validation, and then production can be 24 to 36 months.”
Processors with sustainability goals or mandates have a number of ways to reach their goals. Biopolymers are among them.
Plastics processors are finding applications for 3D printing around the plant and across the supply chain. Here are 8 examples to look for at NPE2024.
Another key capability is the firm’s metrology lab, equipped with four optical and touch-probe coordinate measuring machines. Samples of all parts come through the lab to be qualified. The lab also inspects tooling components and fixtures.
Low- to mid-volume molding is integral to the firm’s QTM business, which it defines as “1 to 500,000 parts.” The essence of this business segment is helping clients get new product ideas off the ground fast. “When a medical or other OEM has an idea, we want them to come to us. We can help them get there. When they are in design and development chaos, that’s where we step in. They can count on us.”
Development of new medical parts from single-cavity prototype to production molding is the specialty of aptly named NPI/Medical. The first initials stand for “New Product Introduction.”
Resin drying is a crucial, but often-misunderstood area. This collection includes details on why and what you need to dry, how to specify a dryer, and best practices.
QTM can be considered the development arm of the firm’s New Product Introduction (NPI) business, also referred to as Prototype to Production (P2P). “We have customers that do continuous new-product introductions. We want to get in early to help them realize their concepts,” says Kelly. “And we want them to stay with us for long-run production.
High profile acquisitions of diagnostics companies, IPO listings, strategic partnerships, and the rise of virtual care platforms provide further assurance that the diagnostics market is on the cusp of another huge growth curve. This all indicates that there are clearly exciting opportunities ahead for moulders operating in the high tech medical device and diagnostics product development and production space.
Baystar's Borstar technology is helping customers deliver better, more reliable production methods to greenhouse agriculture.
Two examples of Quick-Turn development parts: Top: an ABS part used in heart surgery. Bottom: a polycarbonate part for separating blood components.
President David Kelly (right) and senior technical advisor Tim Erwin are long-time colleagues who have helped NPI/Medical create a new identity since its spinoff from Spectrum Plastics Group in late 2013.
August 29-30 in Minneapolis all things injection molding and moldmaking will be happening at the Hyatt Regency — check out who’s speaking on what topics today.
NPI/Medical has three certified clean rooms—one permanent Class 8 (Class 100,000) clean room equipped with six injection machines of 40 and 110 tons, and two Class 7 (Class 10,000) clean rooms for assembly, testing, and packaging. One of those is a permanent structure of 1150 ft², the other a “soft-wall” enclosure of 600 ft² for prototype and short-run work. In addition, the firm can put a hood over an individual press or cell to create a localized clean area.
In this collection of articles, two of the industry’s foremost authorities on screw design — Jim Frankand and Mark Spalding — offer their sage advice on screw design...what works, what doesn’t, and what to look for when things start going wrong.
Despite price increase nominations going into second quarter, it appeared there was potential for generally flat pricing with the exception of a major downward correction for PP.
In this collection, which is part one of a series representing some of John’s finest work, we present you with five articles that we think you will refer to time and again as you look to solve problems, cut cycle times and improve the quality of the parts you mold.
NPI/Medical offers QTM clients its DynaClass Tooling System, consisting of four levels of tooling from DynaClass 1 for “form, fit & function” prototypes (up to 5000 parts), deliverable in one to three weeks; to DynaClass 2 molds for tight-tolerance, advanced prototypes (up to 50,000 parts), suitable for validation, which take two to four weeks; and DynaClass 3 and 4 low-volume and pre-production bridge tooling for up to 100,000 and 500,000 parts, respectively, with lead times from three to eight weeks. (These tooling classes correspond to SPI Classes 105 to 102.) Standard tolerances for all DynaClass tools and parts are ±0.005 in.
Say “manufacturing automation” and thoughts immediately go to the shop floor and specialized production equipment, robotics and material handling systems. But there is another realm of possible automation — the front office.
With regard to machinery, there is a strong move towards “copy & paste” systems and processes in both Europe and North America. The global medical team at Sumitomo (SHI) Demag, led by business development director Anatol Sattel, are also noting more requests for remote system access to historical machine data. This is predominantly to assist with troubleshooting and monitoring validated process settings.
This month’s resin pricing report includes PT’s quarterly check-in on select engineering resins, including nylon 6 and 66.
In 2023, the global medical injection moulding market size was estimated at $22.54 billion. It is expected to grow at a compound annual growth rate (CAGR) of 5.8% from 2024 to 2030. Much of this growth is being driven by advances in self diagnostics, the home healthcare sector, improved healthcare infrastructures in emerging economies, and an ageing population, which WHO predicts will double by 2050.
After field testing, validation and refinement with customer feedback, Husky announced the introduction of a cold-deck system for direct gate molding of LSR.
The plant has four 55-ton Arburg presses for LSR (convertible for thermoplastics), one of them dedicated to low-volume and prototype work. “We do LSR in low and high volumes,” says Kelly. “It’s a core competency of ours. I’m not talking about O-rings or baby nipples. We do complex geometries and overmolding onto metal or thermoplastics.”
Secondary operations performed by NPI/Medical include ultrasonic welding and pad printing. One hand-held surgical stapler requires 10 “hits” from a pad printer to place labels all around the handle.
Back in the 1970s, Spectrum’s core business was electronics, specializing in reel-to-reel molding of connectors, microsensors, open-cavity packages, and LED lenses onto stainless steel and plated copper strips (a technique developed by Spectrum).
For medical moulders already producing vital monitoring devices, including oxygen, weight, glucose and ECG devices, as well as infusion pumps and cannulas etc. and already meeting the exacting healthcare standards, the transition to homecare device production should be relatively seamless.
NPE2024: A slimmed-down version of Engel’s all-electric, e-mac injection molding machine is among eight displays, which also include LSR micromolding, quick mold changes and a cube mold.
Erwin notes that NPI/Medical’s experience in LSR includes ability to process special materials. A case in point is a liquid fluorosilicone used in DNA sequencers because of its hot-oil resistance. “We’re the only molder of this particular material today,” says Erwin. “It has a viscosity of over 1 million centistokes, versus 600,000 typical for LSR, and it’s not shear-thinning like normal LSR. It’s no picnic.” Even molding standard LSR, Erwin says, is “80% art, 20% science, while thermoplastic molding today is more like 90% science.”
Mike Sepe has authored more than 25 ANTEC papers and more than 250 articles illustrating the importance of this interdisciplanary approach. In this collection, we present some of his best work during the years he has been contributing for Plastics Technology Magazine.
Multiple speakers at Molding 2023 will address the ways simulation can impact material substitution decisions, process profitability and simplification of mold design.
The company’s ultimate vision is an intelligent machine that can independently make predictions about part quality, machine wear and failures and deliver optimisations online. Enabling greater process consistency and allowing for real-time machine maintenance to be adjusted accordingly.
Thermoplastic and LSR moulding continues to be used extensively to manufacture a huge variety of everyday medical applications. The range is broad and can include implantable components, test tubes, petri dishes, PCR tubes, pipette tips and other labware, as well as medical monitoring devices, drug delivery components and surgical equipment.
MedTech is a multi-billion-dollar manufacturing sector. Unsurprisingly, industry analysts are always keen to pinpoint the newest transformational medical and life science technologies that are expected to shape future treatment pathways.
Mold maintenance is critical, and with this collection of content we’ve bundled some of the very best advice we’ve published on repairing, maintaining, evaluating and even hanging molds on injection molding machines.
QTM AND P2P NPI/Medical prides itself on its appetite for short runs. “If you need hundreds of parts, we’ll do it,” says Kelly. “We have medical orders for as few as 400 parts a year. We have a huge job coming up to mold 15 different parts and assemble them for just 250 finished assemblies a year!”
Join Engel in exploring the future of battery molding technology. Discover advancements in thermoplastic composites for battery housings, innovative automation solutions and the latest in large-tonnage equipment designed for e-mobility — all with a focus on cost-efficient solutions. Agenda: Learn about cutting-edge thermoplastic composites for durable, sustainable and cost-efficient battery housings Explore advanced automation concepts for efficient and scalable production See the latest large-tonnage equipment and technology innovations for e-mobility solutions
A case in point is the plant’s “kitting room,” designed by Erwin, where five models of DNA sequencers are packaged in ready-to-use kits. “We mold six parts and purchase three more, plus the packaging and label,” explains Ball. “We ship around 6000 a year per model. We audit the sub-vendors and provide controlled lot traceability, thanks to our IQMS ERP system. For each order, we send four kits to the customer for approval and hold the rest of the order until we receive the go-ahead. That can take less than two weeks or up to six weeks for a new job.”
Kelly, who has spent 30 years in plastics, the last 15 of them at NPI/Medical and its predecessor company, points out that the firm wasn’t always so specialized—at least not on medical products. The NPI/Medical name dates only from September 2013, when it was spun off from Minneapolis-based Spectrum Plastics Group. According to Kelly, “Changing the name was a very good thing for us, because Spectrum had been associated with a very different kind of business.”
Service encompasses NPI/Medical’s eagerness to support low-volume production, often for startup companies, and its wide range of capabilities to support varied customer demands. As president David Kelly puts it, “When a customer asks whether we have a certain capability, we want to say yes.”
Thousands of people visit our Supplier Guide every day to source equipment and materials. Get in front of them with a free company profile.
NPI/Medical has ample experience in special molding techniques, like insert molding and multimaterial overmolding. In both cases, it uses mostly hand loading of the tools, due to the prevalence of short to medium runs.
The medical market, particularly diagnostics, was strongly influenced by the Coronavirus pandemic. As anticipated, there has been a natural levelling-off for pandemic-related consumables.
Ultradent's entry of its Umbrella cheek retractor took home the awards for Technical Sophistication and Achievement in Economics and Efficiency at PTXPO.
MANY TALENTS UNDER ONE ROOF The plant’s operations are divided into four “cells” in separate rooms. Narrow corridors between the cells allow equipment to be moved in and out without disturbing production.
Assembly and packaging are other core competencies at NPI/Medical. “When we mold several parts for a product, it’s hard to compete with us for the assembly portion of the job,” says Erwin.
Despite this industry consolidation, NPI/Medical has not lost any business, and has even picked up some from “molders that are more commoditized than us,” Kelly says, “or ones that do other things besides medical, like automotive. It helps to specialize.”
The plant’s newest capability is laser etching, which is very fast—one current job etches a set of three parts in 4 sec—and imparts permanent marks that can’t wear off. NPI/Medical uses the laser technique on specially formulated grades of PC, ABS, and nylon.
Regional medical director of the Sumitomo (SHI) Demag team Andrew Sargisson shares his industry insight and global predictions for the medical market, touching upon how these latest trends are influencing investments in medical injection moulding facilities worldwide.
NPE2024: Sumitomo SHI Demag’s show focus is on the application of all-electric injection molding machine technology for a variety of markets and components.
To accommodate his customers’ obsession with quality, Kelly took the unusual step of moving the process engineers and technicians into the quality department. “That means our quality team is accountable for the process as well as the parts. It means the project manager can go to one person—the quality manager—to address any problems.”
With significant access to start-up finding, telehealth is the boom-market to watch. It is current exhibiting a CAGR of 19.7% between now and 2030. Online video and audio consultations with physicians and medical consultants are increasingly being used to deliver quality healthcare while simultaneously reducing heavy work and cost burdens. The telehealth segment is split between services and products. Items such as wearable patient monitoring and telecommunication devices accounts for around one third of the market.
In 2024, Sumitomo (SHI) Demag will host its inaugural productivity roadshow. With four stopovers planned for July in the UK and Ireland, including Limerick, customers will be invited to explore all the latest trends, productivity and profit-enhancing technologies.
The name says it all: New Product Introduction (NPI), with a focus on Medical. Or maybe not quite all: NPI/Medical is really two businesses—production molding for medical markets and Quick-Turn Manufacturing (QTM), or low-volume molding from prototype to pre-production “bridge” stage.
To support these advances and in order to meet the explicit quality management and validation ISO 13485 standards for medical devices, Sumitomo (SHI) Demag introduced new machine user parameters, digital quality control and KPI analytics into its IntElect S medical production package. One of these advanced Med-Spec demo cells is now located in Limerick, Ireland. This will enable customers to perform validations, run tool trials and use the facility to provide valuable process optimisation training to technicians.
Kelly credits much of NPI/Medical’s expertise in LSR to Tim Erwin, senior technical advisor, who joined the firm about 10 years ago from Pitney-Bowes, where he had worked for 27 years and Kelly for 15. “Tim is one of the industry’s top technical guys in LSR,” states Kelly. “He designed a cold-deck mold frame for LSR to accept interchangeable core and cavity sets. We can build a single core and cavity in four to five weeks for no more than $8000 to $10,000.”
A Novatec central drying system was recently reconfigured after the separation from Spectrum Plastics. Transitioning out of most of the reel-to-reel business and putting more emphasis on QTM development brought a need to dry more materials in smaller amounts. Mounted on a mezzanine, the system has 36 drying hoppers divided among three hopper banks, each fed by a wheel-type desiccant dryer. Numbered flexible tubes from each hopper can be connected to any of 43 numbered tubes leading to molding workcells.
Join Wittmann for an engaging webinar on the transformative impact of manufacturing execution systems (MES) in the plastic injection molding industry. Discover how MES enhances production efficiency, quality control and real-time monitoring while also reducing downtime. It will explore the integration of MES with existing systems, emphasizing compliance and traceability for automotive and medical sectors. Learn about the latest advancements in IoT and AI technologies and how they drive innovation and continuous improvement in MES. Agenda: Overview of MES benefits What is MES? Definition, role and brief history Historical perspective and evolution Longevity and analytics Connectivity: importance, standards and integration Advantages of MES: efficiency, real-time data, traceability and cost savings Emerging technologies: IoT and AI in MES
While the melting process does not provide perfect mixing, this study shows that mixing is indeed initiated during melting.
Sustainability continues to dominate new additives technology, but upping performance is also evident. Most of the new additives have been targeted to commodity resins and particularly polyolefins.
With advocacy, communication and sustainability as three main pillars, Seaholm leads a trade association to NPE that ‘is more active today than we have ever been.’
REFOCUSED ON MEDICAL NPI/Medical has occupied a 66,000 ft² plant in Ansonia, Conn., since 1999. The building, sitting on a 13-acre site, could easily be expanded to 85,000 ft², according to project manager William Ball.
Hot runner supplier Mastip used K 2022 to introduce the customized and valve-gated Aquilo liquid silicone rubber (LSR) cold deck.
Plastics Technology covers technical and business Information for Plastics Processors in Injection Molding, Extrusion, Blow Molding, Plastic Additives, Compounding, Plastic Materials, and Resin Pricing. About Us
This clean room is one of three at NPI/Medical, two for assembly (like this one) and one for molding, which has six presses of 40 to 110 tons. Inside one clean room (below), workers weld, test, and package medical parts.
Essential to NPI/Medical’s Quick-Turn capabilities is its toolroom, staffed by eight toolmakers and two apprentices. The equipment range comprises six Bridgeport milling machines, seven grinders, six CNC machining centers (including one that can operate lights-out with a six-axis robot to make up to 32 EDM electrodes) and five EDM systems. The latter can carry up to 82 electrodes, and one is a wire EDM machine, not often seen in small shops. Also relatively uncommon is a $30,000 microwelder—a “very big timesaver,” according to Ball.
Join this webinar to explore the transformative benefits of retrofitting your existing injection molding machines (IMMs). Engel will guide you through upgrading your equipment to enhance monitoring, control and adaptability — all while integrating digital technologies. You'll learn about the latest trends in IMM retrofitting (including Euromap interfaces and plasticizing retrofits) and discover how to future-proof your machines for a competitive edge. With insights from industry experts, it'll walk you through the decision-making process, ensuring you make informed choices that drive your business forward. Agenda: Maximize the value of your current IMMs through strategic retrofitting Learn how to integrate digital technologies to enhance monitoring and control Explore the benefits of Euromap interfaces and plasticizing retrofits Understand how retrofitting can help meet new product demands and improve adaptability Discover how Engel can support your retrofitting needs, from free consultations to execution
While the major correction in PP prices was finally underway, generally stable pricing was anticipated for the other four commodity resins.
Additive technology creates air pockets in film during orientation, cutting down on the amount of resin needed while boosting opacity, mechanical properties and recyclability.
More recently, there is a stronger leaning in the medical market towards larger strategic and more complex projects, such as drug delivery devices and pen style injectors. This is predominantly due to the global growth in diabetes care, where demand for advanced glucose monitoring and insulin delivery devices is propelling innovation. Testament to demand, credible industry reports forecast that the diabetes device market will surpass $68.2 billion by 2032, almost triple its 2022 value.
technotrans says climate protection, energy efficiency and customization will be key discussion topics at PTXPO as it displays its protemp flow 6 ultrasonic eco and the teco cs 90t 9.1 TCUs.
GETTING A QUOTE WITH LK-MOULD IS FREE AND SIMPLE.
FIND MORE OF OUR SERVICES:
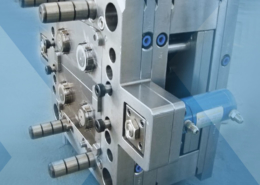
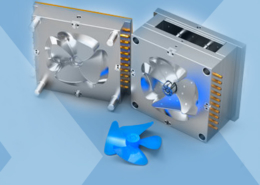
Plastic Molding

Rapid Prototyping
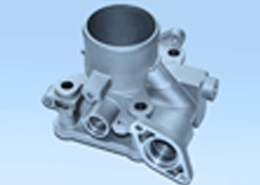
Pressure Die Casting
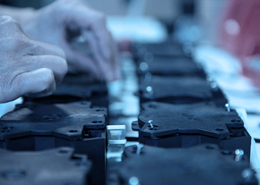
Parts Assembly
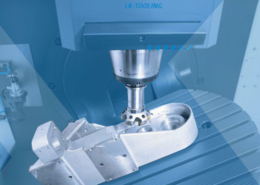