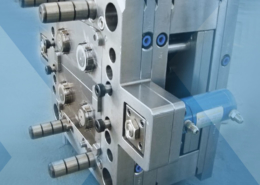
Ceramic Injection Molding Market Share Report, 2023 – 2032 - aerospace injection
Author:gly Date: 2024-09-30
To provide customers with additional information on making the switch from paint to molded-in-color parts, PolyOne has created an eBook titled, “Trend Report: Efficient Manufacturing And Molded-In Color.”
The robot receives its energy supply directly from the DC intermediate circuit of the EcoPower and also returns any surplus energy derived from axis deceleration to that circuit. On this machine, a crinkle box made of PP will be manufactured using a single-cavity mould supplied by the Austrian company Haidlmair. The power supply for the machine will come from ultra-modern ecological salt battery technology on sodium-nickel basis supplied by innovenergy. The battery has a total capacity of over 45 kWh, more than sufficient for continuous operation of the machine during an entire 8-hour trade fair day. To compensate the injection moulding machine’s short-term load peaks, additional electrochemical capacitors known as super-caps are used to complement the sodium-nickel storage units.
With its presentation of an EcoPower 180/750+ B8X DC machine, WITTMANN BATTENFELD France will demonstrate to its visitors the WITTMANN Group’s expertise in the field of utilising renewable energies. This machine, operating with a solar power storage unit, is also equipped with a WX142 robot in DC version.
Furthermore, WITTMANN BATTENFELD France will exhibit a selection from the WITTMANN Group’s range of materials handling technology. In addition to central conveyors and stand-alone conveyors, such as the Feedmax S3 net, the exhibits will also include the new Feedmax Clean with dedusting function, which has been specially developed in response to the more and more stringent demands of the circular economy and the resulting increase in plastic granulates containing dust. The program will be rounded off with an XMB filter station and a Codemax RFID-controlled coupling station, which in combination with the M8 network control system ensures correct material feeding.
“Many car parts are painted, not just metal and thermoplastic exterior parts, but also thermoplastic parts in a vehicle’s interior,” notes Gary Fielding, vice president and general manager, Color and Additives EMEA at PolyOne. “We have successfully helped carmakers transition from paint to MIC for many exterior applications such as skid plates and trims. This recent project is a significant step forward in reducing the cost to manufacture highly visible interior applications.”
The key to molding good parts is for OEMs to decide, very early on, that a part will be colored with molded-in color masterbatch; that decision will then support the development of a mold and part suitable for masterbatch.
In addition to the robots and auxiliaries connected to the machines on display, a number of stand-alone solutions will also be shown at the FIP.
Paint adds a great surface finish to automobile parts, but painting always adds cost, time, and additional logistics requirements according to PolyOne. By using Smartbatch FX metallic masterbatches, the molder was able to produce parts ready for assembly with no secondary processing required. Suitable for standard injection molding machinery, Smartbatch FX reduces the cost per part by 30 percent or more compared to painted parts. Lowered energy requirements versus painting and the reduction of VOCs also make this masterbatch a more environmentally sustainable solution.
The SmartPower B8X to be presented comes equipped with all-electric injection units, thus combining the advantages of the servo-hydraulic SmartPower’s flexible, generous mould space with the all-electric EcoPower’s excellent performance and high precision.
Stephen has been with PlasticsToday and its preceding publications Modern Plastics and Injection Molding since 1992, throughout this time based in the Asia Pacific region, including stints in Japan, Australia, and his current location Singapore. His current beat focuses on automotive. Stephen is an avid folding bicycle rider, often taking his bike on overseas business trips, and is a proud dachshund owner.
The industry’s challenges, in light of COVID-19 and an uncertain economy, could open the door much wider to greater use of metallic-effect masterbatches, as these significantly lower cost per part. The challenge with masterbatch remains molding parts that do not have visual defects such as flow or weld lines.
“Typically, you do not want a bunch of holes or sharp curves in a part if you intend to use metallic-effect masterbatch. Too often, a mold is made for molding of parts that will be painted, and then — when it is time for a facelift — the OEM decides it wants to save some money and shift from paint to masterbatch. However, without investing in a new mold, the existing mold design often makes it very difficult for masterbatch to be successfully used.
Transitioning from paint to the use of MIC with Smartbatch FX helps manufacturers in the automotive, appliance, consumer goods and other industries create attractive, durable parts at reduced cost. PolyOne’s metallic-effect masterbatches can be incorporated into pre-colored compounds or dosed at a molding machine.
PolyOne recently collaborated with a leading global automotive OEM and its injection molder to eliminate paint from a new vehicle’s interior. To support the transition to molded-in-color (MIC) parts, PolyOne provided metallic-effect Smartbatch FX masterbatch colorants for two PC/ABS side panels on the center console of a compact SUV now entering commercial production. The parts (two; one on each side of the center console) are C-shaped, 35-cm long, and at their widest point 11-cm wide.
PolyOne recently collaborated with a leading global automotive OEM and its injection molder to eliminate paint from a new vehicle’s interior.
A further highlight of the presentation will be a selection from the range of granulators manufactured locally at WITTMANN BATTENFELD France. The exhibits will include G-Max 9 and G-Max 23 grinders as well as the screenless granulator models S-Max 2 and the new S-Max Dual 6. The S-Max Dual 6 is the ideal granulator for central grinding of reject parts, but it can also be used for in-line recycling of sprue from injection moulding machines. For use beside the press, the footprint of the S-Max Dual 6 has been reduced by about 25% compared to its predecessor model.
At the FIP Solution Plastique 2024 in Lyon to be held from June 4 to 7, WITTMANN BATTENFELD will present ultra-modern injection moulding technology, automation and auxiliaries to trade visitors.
Multi-component technology expertise will be shown as well, by the production of a bottle opener made of PC and TPE on a SmartPower B8X Combimould, using a mould supplied by FKT Formenbau und Kunststofftechnik, Germany. The SmartPower B8X 120/350H/130S is presented as an insider solution with a W918 robot from WITTMANN and a conveyor belt integrated in the production cell. The robot takes the prepared metal parts from a magazine and places them into the mould, where they are insert-moulded with polycarbonate. A rotary unit subsequently turns the resulting base bodies into position and passes them on to the second station, where they are over-moulded with TPE to provide them with a better grip. The finished parts are then deposited on the insider cell’s conveyor belt.
The range of dryers on display at the FIP will include a Drymax primus und a Drymax plus dry air dryer, as well as a Card primus compressed air dryer. The dry air dryers from the Drymax series are each equipped with two desiccant cartridges and therefore deliver a continuous flow of process air with consistent dry air quality for perfect drying of plastic granulate. The Drymax plus offers high operating comfort with a generously dimensioned touch display panel. Card compressed air dryers are small and effective and ideally suited for simple drying applications directly next to the machine’s feed zone.
Energy measurements using the IMAGOxt software will be carried out on all injection moulding machines shown at the WITTMANN BATTENFELD booth. IMAGOxt, a program developed by WITTMANN Digital, will be used to display the energy consumptions of all injection moulding machines exhibited at the fair, and the auxiliaries connected to them. The program also calculates the CO2 consumption. All values calculated can be recorded in quality reports and thus remain available for long-term analyses. IMAGOxt is available as a web application, as an optional extension of the WITTMANN TEMI+ MES system, or as a stand-alone program.
From its range of robots, WITTMANN BATTENFELD France will exhibit at the FIP a WX138T with AC servo axis and a Primus 128 model with the new R9 robot control unit. With its control cabinet flange-mounted to the horizontal axis and its internal power chain, the WX138T is particularly suited for compact production cells. It is driven by toothed belts to reduce its operating noise to a minimum. The Primus 128 for pick-&-place applications offers a robust axle design thanks to its vertical Y axis supported by a steel profile. A lubrication system for the vertical axis included as standard ensures a continuous supply of lubricant and consequently quiet operation of the drive system with minimal wear.
Moreover, WITTMANN BATTENFELD France will also demonstrate its expertise in micro injection moulding by showing a MicroPower 15/10 specially designed for this type of application live in action. With this machine a micro retaining ring for medical miniature tubes will be produced from PC with an 8-cavity mould supplied by Wittner, Austria. This product has a part weight of only 2 mg. The machine comes with a rotary unit, an integrated WITTMANN W8VS2 robot and a camera for complete parts inspection. Following removal and camera inspection, the parts are transferred to transport containers, separated according to individual cavities.
From the segment of temperature control technology, one temperature controller from the Tempro basic series will be presented at the FIP, plus a single-circuit and a dual-circuit appliance from the Tempro plus D series. The features of auxiliaries from the Tempro plus D series are their comfortable touch control units and optional extras such as utilisation-controlled pump regulation with EcoDrive. In addition, WITTMANN BATTENFELD France will show a selection from the WITTMANN portfolio of flow controllers. A WFC 120 flow regulator will also be on display. The WFC is an appliance to control both flow quantity and temperature. It comes with a maintenance-free flow measurement unit.
And though the argument against masterbatch always is about these visual defects, little is said about scrap from paint lines, which can reportedly be more than 20%. Painting is not only more costly, and energy-intensive; it also generates very high levels of non-recyclable scrap.
Transitioning from paint to masterbatch for metallic-effect parts is not new, but it is nowhere near as widespread as one would expect according to some auto industry observers. Inertia — We’ve always done it that way — and legacy investment in paint lines, supports the continued use of paint.
Finally, WITTMANN BATTENFELD France will provide tangible evidence of the WITTMAN Group’s expertise in dosing technology by showing a volumetric Dosimax MC Balance blender and a Gravimax primus 14 blender with real-time weighing.
GETTING A QUOTE WITH LK-MOULD IS FREE AND SIMPLE.
FIND MORE OF OUR SERVICES:
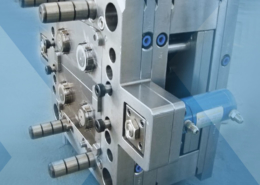
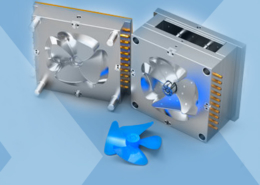
Plastic Molding

Rapid Prototyping
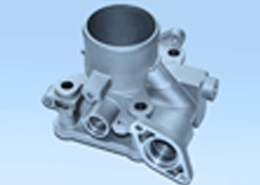
Pressure Die Casting
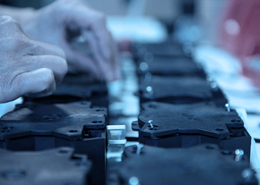
Parts Assembly
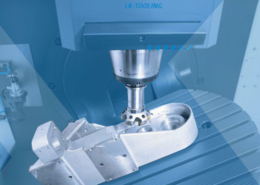