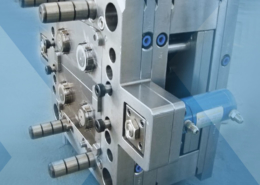
Century Mold buys Integrity Tool's injection molding division - plastic molding
Author:gly Date: 2024-09-30
Working to improve the situation, Fromm and his colleagues teamed up with the Kunststoff-Zentrum in Leipzig to develop a new kind of tempering technique that, depending on the product, is up to 90 percent more energy efficient than other techniques used to date. The trick is to avoid having to heat up the entire tool; these can weigh half a ton or even more depending on the plastic part being produced. All that is heated now is the surface of the tool that actually comes into contact with the plastic melt.
To achieve this, the researchers set about integrating incredibly fine thermocouples, made from nickel or nickel-chrome alloy and each just a few hundred nanometers thick. Thermo- couples can be produced using thin-film technology and incorporated into the insulation layer. Due to their extremely low mass, thermocouples react incredibly fast to temperature changes and make it possible to directly measure the temperature of the tool wall. Through a series of laboratory experiments, the researchers were able to demonstrate that thin-film heating can be used to achieve the desired tool wall temperature very quickly indeed. The researchers are now looking for industry partners to help prepare the process for use in series manufacture.
Electrical insulation is provided by a ceramic layer that shields the conductive heating layer from the steel tool underneath. The layer that actually gets heated is made of a specially designed conductive hard material. In this case, the challenge of sputtering lies not only in producing a perfect insulating layer so as to avoid any short circuits, but also in integrating a sensor into the thin-film heating layer. A sensor placed here can measure the temperature of the tool wall and be used to regulate the manufacturing process.
Please enter your email address and create a password to access the full content, Or log in to your account to continue.
This is possible thanks to thin-film heating. Researchers coat the wall of the forming tool using a vacuum-based coating technique known as sputtering. Imagine a game of pool in which the balls are base-material atoms – in this case from the thin film. Hitting them with energy-rich ions sends them ricocheting around the vacuum chamber. The sputtered material is deposited onto the surface of the forming tool in layers only a few micrometers thick (1 micrometer equals one thousandth of a millimeter). To put this into perspective, a human hair is approximately 80 micrometers thick. Not only can this extremely thin coating be used to heat the forming tool surface to the desired temperature, but it is also capable of withstanding the thermodynamic stresses that occur during injection molding.
Your email address is used only to let the recipient know who sent the email. Neither your address nor the recipient's address will be used for any other purpose. The information you enter will appear in your e-mail message and is not retained by Phys.org in any form.
In this interview with A.J. Pruitt, Technology Manager at Accumold, we delve into the company's groundbreaking advancements in micro molding technology, specifically focusing on thin-walled cannulas. These innovative cannulas are transforming wearable diabetes devices by offering enhanced precision, comfort, and reliability for users. Accumold's successful shift from traditional extrusion methods to advanced micro molding techniques addresses longstanding challenges in cannula production, such as high fallout rates and costly secondary processes.
In this conversation, Pruitt sheds light on how these developments not only refine the functionality of diabetes management devices but also pave the way for broader industry impact. Discover how Accumold's approach is setting new standards in medical device manufacturing and what it means for the future of wearable health technology.
Get weekly and/or daily updates delivered to your inbox. You can unsubscribe at any time and we'll never share your details to third parties.
To manufacture plastic parts with high-end surfaces, the entire forming tool is heated to around 110 degrees Celsius using a technique known as variothermic tempering. Thermo- plastic materials such as polycarbonate are processed at similar temperatures. In order to get the finished plastic part out without damaging it, the mold must be cooled by around 20 to 30 degrees Celsius. This has to be done for every production cycle before the whole process can begin again, which "eats up a considerable amount of energy," explains Alexander Fromm from the Fraunhofer Institute for Mechanics of Materials IWM in Freiburg.
We keep our content available to everyone. Consider supporting Science X's mission by getting a premium account.
In future, thin-film heating will allow plastic parts to be produced with greatly improved surface quality. Researchers have also found a way to make the whole process more energy efficient.
Use this form if you have come across a typo, inaccuracy or would like to send an edit request for the content on this page. For general inquiries, please use our contact form. For general feedback, use the public comments section below (please adhere to guidelines).
If you have ever tried to make waffles then you are bound to be familiar with the following problem: You only get good waffles if the iron is heated to the correct temperature. The same principle applies to the manufacture of plastics parts, such as displays, facings, covers and instrument panels, using injection molding techniques. A liquid plastic melt is injected into a steel forming tool which is heated just like a waffle iron. The point is to produce a perfect cast of the tool's surface, which may be smooth like a mirror or feature a functional structure. Using injection molding to realize the desired structural and functional surface qualities of plastic parts is intended as a one-step process without the need for any extensive finishing work. The process also has to be economic and energy efficient.
GETTING A QUOTE WITH LK-MOULD IS FREE AND SIMPLE.
FIND MORE OF OUR SERVICES:
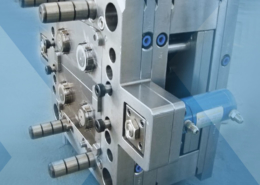
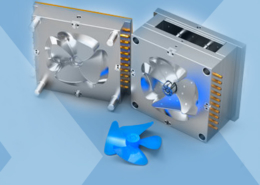
Plastic Molding

Rapid Prototyping
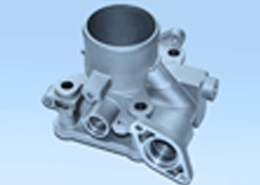
Pressure Die Casting
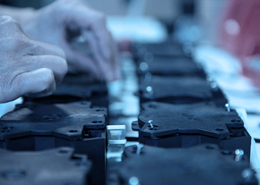
Parts Assembly
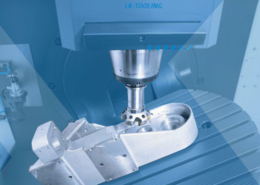