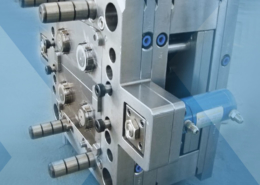
Centralized Gas Supply in Structural Foam Molding Reduces Costs - plastic foam m
Author:gly Date: 2024-09-30
Such tight control, Ignatowski explains, cannot be achieved by old-fashioned “mold and sort” quality assurance: “Quality has to be embedded in the process.” And by “the process” he means every activity from quoting through tool design and process development to molding parts and packing them in a box. Yet there’s one quality- related activity that you’ll find in almost every molding operation except this one: Prism Plastics has no quality-control department.
Tall explained that he has looked at solar a couple of times as a way to save money on his energy bills for the 12-press company. “Two previous times we looked at it, and it’s always seemed too good to be true,” said Tall. “This time we looked seriously at solar and decided that it is that good to be true. We’re a small business, so I wear a lot of hats and there are always so many things to think about other than solar power. On the third pitch, we looked more closely at what we can save and decided that financially it makes sense.”
In a time where sustainability is no longer just a buzzword, the food and beverage packaging industry is required to be at the forefront of this innovation. By adopting circular packaging processes and solutions, producers can meet regulatory requirements while also satisfying consumer demand and enhancing brand reputation. Join Husky to learn more about the broader implications of the circular economy — as well as how leading brands are leveraging this opportunity to reduce costs, increase design flexibility and boost product differentiation. Agenda: The cost and operational benefits of embracing circularity Key materials in circular packaging — including rPET and emerging bioplastics How to design a circular food and beverage package Strategies for selecting sustainable closures to future-proof packaging solutions Optimization and streamlining of production processes for enhanced efficiency How Husky Technologies can enable your sustainable success
Mold maintenance is critical, and with this collection of content we’ve bundled some of the very best advice we’ve published on repairing, maintaining, evaluating and even hanging molds on injection molding machines.
Resin drying is a crucial, but often-misunderstood area. This collection includes details on why and what you need to dry, how to specify a dryer, and best practices.
For a new molding job, flow simulation and shrinkage analysis of the mold and part are performed for Prism by Beaumont Technologies, Erie, Pa. Prism also makes use of Beaumont’s proprietary Melt Flipper technology to achieve 90% or better cavity balancing. “That allows us to run higher cavitation than our competition and maintain quality. It also helps us save material and cycle time by minimizing runner volume.” In one case, Prism took an existing eight-cavity tool design and expanded it to 16 cavities while shrinking the runner by 60% from 55.3 to 22.3 g. “That saved us 3.6¢/ part and $350,000 the first year alone—which was more than the cost of the tooling and the annual value of the program itself.”
“The return on investment with solar is phenomenal,” commented Tall. “The low cost of ownership thanks to the LFC lease, plus the SREC income and electricity savings, add up to a significant impact on our bottom line profitability, while we do something good for the planet at the same time.”
In this collection of articles, two of the industry’s foremost authorities on screw design — Jim Frankand and Mark Spalding — offer their sage advice on screw design...what works, what doesn’t, and what to look for when things start going wrong.
Mike Sepe has authored more than 25 ANTEC papers and more than 250 articles illustrating the importance of this interdisciplanary approach. In this collection, we present some of his best work during the years he has been contributing for Plastics Technology Magazine.
Because Prism’s plants do anywhere from 60 to 120 mold changes a month, its robots also have a quick-change system for end-of- arm tooling. “It’s a twist-and-click mechanism of our own design,” Ignatowski notes.
Sustainability continues to dominate new additives technology, but upping performance is also evident. Most of the new additives have been targeted to commodity resins and particularly polyolefins.
Bricker is enthused about new IQMS forecasting software that will facilitate capacity planning for the whole company to 2020. He also notes that the IQMS system gives him and other plant personnel real-time OEE statistics on each machine, which resets for each shift. OEE is Overall Equipment Effectiveness, a productivity measure that combines machine availability (uptime), performance (cycle time), and quality (defect rate). An OEE rating of 100% means the machine is making only good parts, as fast as possible, with no unplanned downtime.
Processors with sustainability goals or mandates have a number of ways to reach their goals. Biopolymers are among them.
The solar energy system will be installed by New England Clean Energy on the roof of Alpha Rho’s 36,000-square-foot facility in April. It will have 745 Canadian Solar 320-watt panels, SolarEdge inverters with optimizers under each panel and Sollega racking and mounting hardware. The system is projected to deliver electricity savings of more than $1.6 million over 25 years (factoring in inflation). In addition, Alpha Rho will benefit from a new revenue stream created by the sale of solar renewable energy certificates (SRECs), arranged by New England Clean Energy.
Equipment is fully standardized between the three plants: Toshiba Machine Co., America presses, Yushin America, Inc. robots, SRS granulators, Harvard Factory Automation, Inc. (HFA) conveyors, Dri-Air Industries, Inc. dryers, Conair loaders, Plastrac blenders, and Advantage Engineering, Inc. central chillers and mobile mold-temperature-control units. “We’ve standardized right down to the copier machines,” says Ignatowski, only half joking. “It removes one source of variability and it allows us to shift tools around in an emergency while making requalification simpler.
Join KraussMaffei for an insightful webinar designed for industry professionals, engineers and anyone interested in the manufacturing processes of PVC pipes. This session will provide a comprehensive understanding of the technology behind the production of high-quality PVC pipes: from raw material preparation to final product testing. Agenda: Introduction to PVC extrusion: overview of the basic principles of PVC pipe extrusion — including the process of melting and shaping PVC resin into pipe forms Equipment and machinery: detailed explanation of the key equipment involved — such as extruders, dies and cooling systems — and their roles in the extrusion process Process parameters: insight into the critical process parameters like temperature, pressure and cooling rates that influence the quality and consistency of the final PVC pipes Energy efficiency: examination of ways to save material and energy use when extruding PVC pipe products
This Knowledge Center provides an overview of the considerations needed to understand the purchase, operation, and maintenance of a process cooling system.
The environmental benefits of installing solar are “as appealing as the financial benefit.” Tall added, “the solar energy system will reduce the amount of carbon dioxide in the air by 412,800 pounds per year, which is equivalent to taking 39 cars off the road, or planting almost 150 acres of trees.”
That business has been growing every year since the company opened its doors, says Bricker. “We thrived during the most recent downturn, both by acquiring new programs and by taking over business from other molders. In 2010 we increased capacity at Port Huron by 13% and in Harlingen by 22%.” In fact, the company has expanded capacity eight times in its 16 years of existence.
Exhibitors and presenters at the plastics show emphasized 3D printing as a complement and aid to more traditional production processes.
There will be some maintenance costs for the solar panels. The converters that turn the sunlight into energy tend to fail like any piece of equipment, which will require replacing them from time to time, Tall explained.
Today, with four plants, Prism has 72 presses from 33 to 440 tons, 175 employees, and sales of $60 million, which Bricker expects to grow to at least $75 million in the next couple of years. All four plants are certified to the ISO/TS 16949:2009 automotive quality standard. The company’s business is about 95% automotive: safety equipment, air/fluid systems, steering/drivetrain, connectors, and sensors. The remainder encompasses medical, packaging, and aerospace.
“We needed the additional capacity,” says Prism co-founder, president, and CEO Rodney Bricker. The machines at Meadville include presses both larger and smaller than those already at Prism. “In addition, the acquisition brings in new customers—zero overlap with our existing base—and new market presence. There is no overlap in production, either.” Like Prism, Tech Molded Plastics made mostly automotive parts, but in this case connectors for wire harnesses and sensors. “And we gained new technology, our first in-house moldmaking capacity, and—not least of all—experienced people,” Bricker adds.
Prism recently installed its first six-axis articulated robot for placing metal inserts. The advantage, Ignatowski explains, is that “most molders would use a vertical press with an operator and a shuttle table for that sort of job.” Even more recently, Prism commissioned a cell with three articulated robots. The first robot removes the part from the press, laser etches a barcode, and places it in a fixture. The second robot picks it up, sonic welds it, and then hands it to another fixture. The third robot picks it up, performs vision inspection, and packages the part.
At Prism Plastics, quality is baked into every step of the process. The result: 1 billion parts per year with a defect rate less than 1 ppm.
All three plants use 100% electric presses and five-axis servo robots. All-electrics eliminate oil contamination and facilitate better process control, Ignatowski asserts. “We did a study a year ago on cold-runner molds and found that all- electric machines are sensitive enough that we don’t need in-cavity pressure sensors,” he notes. “We can control cushion, for example, to within 0.003 in. We control cycle times to within 0.1 sec.”
The aim of this presentation is to guide you through the factors and the numbers that will help you determine if a robot is a smart investment for your application. Agenda: Why are you considering automation? What problems are you trying to solve? How and why automation can help Crunch the numbers and determine the ROI
Plastics Technology covers technical and business Information for Plastics Processors in Injection Molding, Extrusion, Blow Molding, Plastic Additives, Compounding, Plastic Materials, and Resin Pricing. About Us
Additive technology creates air pockets in film during orientation, cutting down on the amount of resin needed while boosting opacity, mechanical properties and recyclability.
Tall did his homework before deciding to put in solar. “I called around and talked to people in this business park who have solar and no one had anything negative to say. Everybody ran the numbers; on paper, it’s supposed to really save me a lot of money.”
Tall figures he’ll save about $64,000 annually if the numbers work. “There’s definite savings to be had, but until you get up and running, you never really know,” he said.
“Variation is the enemy.” That’s the mantra of Prism Plastics, according to Jeff Ignatowski, director of sales and marketing. “We throw as much technology as possible into the process to eliminate variation in every step, from the quoting stage on. We won’t even quote on a project that looks like it will have too many uncontrolled variables.”
While the melting process does not provide perfect mixing, this study shows that mixing is indeed initiated during melting.
At 68,000 ft2, the Meadville plant is more than twice the size of any other Prism operation. It has mostly electric machines (Nissei America, Inc. and ARBURG, Inc.), but also some hydraulic and hybrid models. It will move gradually toward the company model of all-electric operation. Prism is investing $1 million at Meadville to add automation, warehouse capacity, and the same IQMS ERP system that ties together all the other Prism operations.
The firm also prides itself on a “lean and flat” organizational structure, aided by extensive use of automation. “We can compete globally because we don’t have excess labor cost,” Bricker asserts.
Mixed in among thought leaders from leading suppliers to injection molders and mold makers at the 2023 Molding and MoldMaking conferences will be molders and toolmakers themselves.
Take a deep dive into all of the various aspects of part quoting to ensure you’ve got all the bases—as in costs—covered before preparing your customer’s quote for services.
Join this webinar to explore the transformative benefits of retrofitting your existing injection molding machines (IMMs). Engel will guide you through upgrading your equipment to enhance monitoring, control and adaptability — all while integrating digital technologies. You'll learn about the latest trends in IMM retrofitting (including Euromap interfaces and plasticizing retrofits) and discover how to future-proof your machines for a competitive edge. With insights from industry experts, it'll walk you through the decision-making process, ensuring you make informed choices that drive your business forward. Agenda: Maximize the value of your current IMMs through strategic retrofitting Learn how to integrate digital technologies to enhance monitoring and control Explore the benefits of Euromap interfaces and plasticizing retrofits Understand how retrofitting can help meet new product demands and improve adaptability Discover how Engel can support your retrofitting needs, from free consultations to execution
Successfully starting or restarting an injection molding machine is less about ticking boxes on a rote checklist and more about individually assessing each processing scenario and its unique variables.
Across all process types, sustainability was a big theme at NPE2024. But there was plenty to see in automation and artificial intelligence as well.
technotrans says climate protection, energy efficiency and customization will be key discussion topics at PTXPO as it displays its protemp flow 6 ultrasonic eco and the teco cs 90t 9.1 TCUs.
Prism is also installing its first “collaborative” robot for packing parts at Meadville— one of the new breed that can work safely alongside humans without need for guarding. It’s a “Sawyer” model from Rethink Robotics, Cambridge, Mass. (rethinkrobotics.com).
Another essential element of Prism’s program is its ERP system from IQMS, Paso Robles, Calif. (iqms.com). Prism relies on it for production monitoring, inventory, accounting, quoting, program management, bills of materials, shipping, and preventive-maintenance scheduling. The latter function won’t let a tool run a job if it has missed a scheduled maintenance check.
Learn about sustainable scrap reprocessing—this resource offers a deep dive into everything from granulator types and options, to service tips, videos and technical articles.
August 29-30 in Minneapolis all things injection molding and moldmaking will be happening at the Hyatt Regency — check out who’s speaking on what topics today.
This tightly controlled pattern of development altered slightly in June 2016, when Prism purchased Tech Molded Plastics in Meadville, Pa. That acquisition at once doubled the company’s total revenues and more than doubled its employee head count and machine capacity. It also added in-house mold-building and prototyping.
Alpha Rho (Fitchburg, MA), an injection molder of rigid plastic boxes of various sizes and shapes, has decided to go solar. The company will produce more than 80% of its power requirements to run the company’s manufacturing, warehousing and administrative operations, according to President David Tall, who discussed this decision with PlasticsToday.
Prism’s campaign against variability starts with using Scientific Molding principles to run capability studies on each injection machine and checking its response to lot-to-lot resin variations. Average machine age is four to six years, not counting the newly acquired Meadville plant.
The Meadville toolroom has the ability to build single-cavity aluminum prototype tools and high-end production-molds used in products like connectors. Meadville produces its own molds but has little excess capacity to serve the needs of the other plants.
“Every piece of equipment of every cell talks to the ERP system,” says Bricker, with evident pride. He can monitor each machine and each plant on his iPad. (On the shop floor, color-coded lights display machine status: green—OK, yellow— setup, red—down or off-cycle.)
In this collection, which is part one of a series representing some of John’s finest work, we present you with five articles that we think you will refer to time and again as you look to solve problems, cut cycle times and improve the quality of the parts you mold.
Plastics Technology’s Tech Days is back! Every Tuesday in October, a series of five online presentations will be given by industry supplier around the following topics: Injection Molding — New Technologies, Efficiencies Film Extrusion — New Technologies, Efficiencies Upstream/Downstream Operations Injection Molding — Sustainability Extrusion — Compounding Coming out of NPE2024, PT identified a variety of topics, technologies and trends that are driving and shaping the evolution of plastic products manufacturing — from recycling/recyclability and energy optimization to AI-based process control and automation implementation. PT Tech Days is designed to provide a robust, curated, accessible platform through which plastics professionals can explore these trends, have direct access to subject-matter experts and develop strategies for applying solutions in their operations.
In this three-part collection, veteran molder and moldmaker Jim Fattori brings to bear his 40+ years of on-the-job experience and provides molders his “from the trenches” perspective on on the why, where and how of venting injection molds. Take the trial-and-error out of the molding venting process.
CT scanning also serves Prism well for reverse engineering. Ignatowski explains, “It shows where the variations from print are, so that when we build a new tool, the parts are good from the first shot.” (For more on CT scanning, see June ’15 feature) .
Prism sticks to all-electric machines, which avoids oil contamination and improves process control. A study showed the machines to be sensitive enough to run without cavity-pressure sensors.
Discover how artifical intelligence is revolutionizing plastics processing. Hear from industry experts on the future impact of AI on your operations and envision a fully interconnected plant.
Once the mold is built, Prism conducts studies of gate freeze and mold balance and prepares a rheology worksheet based on the resin’s viscosity vs. shear rate curve. (Prism uses engineering resins like nylon, PPA, PPS, PEI, PET, PBT, PC/ABS, and acetal, plus some PP.) After a qualified process is determined, setup recipes for the machine and robot are recorded in a “job book.” Prism plans to move away from this hard-copy approach to storing setup data on tablets.
Prism doesn’t fret too much about overseas competition—it has instead benefitted from “reshoring” jobs from China and Europe. “Customers who have tried offshoring have learned that the lowest overall cost for a molding job is not the same as lowest piece price,” notes Ignatowski. “It means highest customer satisfaction with quality, delivery, and overall service. We pride ourselves on 100% on-time delivery.”
Ultradent's entry of its Umbrella cheek retractor took home the awards for Technical Sophistication and Achievement in Economics and Efficiency at PTXPO.
The Plastics Industry Association (PLASTICS) has released final figures for NPE2024: The Plastics Show (May 6-10; Orlando) that officially make it the largest ever NPE in several key metrics.
Join Wittmann for an engaging webinar on the transformative impact of manufacturing execution systems (MES) in the plastic injection molding industry. Discover how MES enhances production efficiency, quality control and real-time monitoring while also reducing downtime. It will explore the integration of MES with existing systems, emphasizing compliance and traceability for automotive and medical sectors. Learn about the latest advancements in IoT and AI technologies and how they drive innovation and continuous improvement in MES. Agenda: Overview of MES benefits What is MES? Definition, role and brief history Historical perspective and evolution Longevity and analytics Connectivity: importance, standards and integration Advantages of MES: efficiency, real-time data, traceability and cost savings Emerging technologies: IoT and AI in MES
He cites the case when Prism bid on a job to produce an automotive part with super-tight tolerances that was being molded by a competitor. “We quoted only eight cavities, even though the bobbin was already being molded in 16. We said 16 cavities weren’t feasible, and we proved it by taking CT scans of competing parts from all 16 cavities. Not a one of them was in spec.”
Ignatowski explains, “Although we have no quality department, we have all the quality systems in place to supply automotive—PPAP, TS certification, etc—but instead of a vertically structured quality organization, ours is embedded horizontally across all disciplines.”
“I generate what I need for the plant and whatever I generate and don’t use goes back into the grid,” Tall said. “However there is some controversy currently in the legislature. Some want to increase the cap on the amount of unused electricity that goes back into the grid. Others, primarily the utility companies, are in opposition to raising the cap. That’s an issue. We’re on a waiting list for the net metering program, and I don’t know whether I’ll get it, but I’ll probably use most of what I generate, which will still give me a reduced electric bill through credits.”
Second quarter started with price hikes in PE and the four volume engineering resins, but relatively stable pricing was largely expected by the quarter’s end.
Until she retired in September 2021, Clare Goldsberry reported on the plastics industry for more than 30 years. In addition to the 10,000+ articles she has written, by her own estimation, she is the author of several books, including The Business of Injection Molding: How to succeed as a custom molder and Purchasing Injection Molds: A buyers guide. Goldsberry is a member of the Plastics Pioneers Association. She reflected on her long career in "Time to Say Good-Bye."
It beats other techniques for measuring critical part dimensions, and it provides unique visibility inside parts, nondestructively. One molder’s experience illustrates the benefits.
Plastics processors are finding applications for 3D printing around the plant and across the supply chain. Here are 8 examples to look for at NPE2024.
Rodney Bricker, president/CEO (l.) and Jeff Ignatowski, director of sales/marketing show off an example of how Prism’s runner optimization doubled the cavitation (from 8 to 16) in one job while cutting runner volume by 60%.
Core Technology Molding turned to Mold-Masters E-Multi auxiliary injection unit to help it win a job and dramatically change its process.
Gifted with extraordinary technical know how and an authoritative yet plain English writing style, in this collection of articles Fattori offers his insights on a variety of molding-related topics that are bound to make your days on the production floor go a little bit better.
“We aim to stay at 100%,” Bricker says. One of Prism’s most valuable tools for ensuring product quality is CT scanning, which literally provides “x-ray vision” of the internal features of parts, as well as highly accurate measurement (to 7-10μ on average) of exterior dimensions. “We’re using it more and more,” says Ignatowski. Due to the high cost of CT systems, Prism uses outside service bureaus.
Across the show, sustainability ruled in new materials technology, from polyolefins and engineering resins to biobased materials.
Thousands of people visit our Supplier Guide every day to source equipment and materials. Get in front of them with a free company profile.
Say “manufacturing automation” and thoughts immediately go to the shop floor and specialized production equipment, robotics and material handling systems. But there is another realm of possible automation — the front office.
When defects occur, Prism staff prepares a Nonconforming Report, which identifies the root cause of the problem and how to contain and correct it. “Lessons Learned” meetings are held regularly to discuss progress in reducing variability and defects.
Despite price increase nominations going into second quarter, it appeared there was potential for generally flat pricing with the exception of a major downward correction for PP.
Multiple speakers at Molding 2023 will address the ways simulation can impact material substitution decisions, process profitability and simplification of mold design.
While prices moved up for three of the five commodity resins, there was potential for a flat trajectory for the rest of the third quarter.
When, how, what and why to automate — leading robotics suppliers and forward-thinking moldmakers will share their insights on automating manufacturing at collocated event.
To finance the solar, Alpha Rho opted for a seven-year traditional lease from LFC Capital Inc., which eliminated any upfront capital investment. Instead, Alpha Rho will make 100% tax-deductible fixed monthly payments, creating a low-cost path to ownership at a substantially reduced price.
During production, process monitoring keeps a close watch on the run, with every shot subject to pass/fail qualification on the basis of 13 process variables. “The machine itself is our quality monitor,” notes Ignatowski. “We set our statistical process- control limits tighter than most people do. So nine-tenths of our in-process rejects are actually good parts.” In fact, the company claims a defect rate of less than 1 ppm.
Allegheny Performance Plastics specializes in molding parts from high-temperature resins for demanding applications as part of its mission to take on jobs ‘no one else does.’
From the day it started production in 2000, it was evident that Prism was not your average shoot-and-ship custom molder. It began operations with all-electric machines, robotic parts removal, and automated packaging. That set the pattern, from the first plant in Port Huron, Mich., to the opening of the second facility in Harlingen, Tex., in 2005 and the third—now headquarters—location in Chesterfield, Mich., in 2012. All three plants operate under “white room conditions” with automated cells, plant-wide machine monitoring, and closed-loop process control. The plants look nearly identical and each is under 30,000 ft2, which Prism considers optimal for both control and flexibility. Each “focused factory” has at most eight or 10 customers so it can focus on those customers’ needs and their particular types of parts.
After successfully introducing a combined conference for moldmakers and injection molders in 2022, Plastics Technology and MoldMaking Technology are once again joining forces for a tooling/molding two-for-one.
Join Engel in exploring the future of battery molding technology. Discover advancements in thermoplastic composites for battery housings, innovative automation solutions and the latest in large-tonnage equipment designed for e-mobility — all with a focus on cost-efficient solutions. Agenda: Learn about cutting-edge thermoplastic composites for durable, sustainable and cost-efficient battery housings Explore advanced automation concepts for efficient and scalable production See the latest large-tonnage equipment and technology innovations for e-mobility solutions
While the major correction in PP prices was finally underway, generally stable pricing was anticipated for the other four commodity resins.
Because of the rebates and SREC, Massachusetts is a solar-friendly state to be in, even though it’s one of the more costly states for energy in the country. And while it’s not exactly the “sunshine state,” Tall said there are on average enough sunny days to make solar energy worthwhile.
Each plant utilizes machine-side resin handling because central storage and conveying would present opportunities for cross-contamination, according to Ignatowski. In Chesterfield, the newest of the three plants, all utilities run under the floor. Scrap is granulated beside the press and regrind is recycled, when appropriate, in a closed loop. Prism uses SRS low-speed granulators because they produce granules that are consistently as close as possible to the original pellet size, with no longs or shorts, eliminating another source of variability. Granulators and other equipment are cleaned in a room separate from the molding area to prevent dust contamination.
Formnext Chicago is an industrial additive manufacturing expo taking place April 8-10, 2025 at McCormick Place in Chicago, Illinois. Formnext Chicago is the second in a series of Formnext events in the U.S. being produced by Mesago Messe Frankfurt, AMT – The Association For Manufacturing Technology, and Gardner Business Media (our publisher).
While prices moved up for three of the five commodity resins, there was potential for a flat trajectory for the rest of the third quarter.
In this collection of content, we provide expert advice on welding from some of the leading authorities in the field, with tips on such matters as controls, as well as insights on how to solve common problems in welding.
Consequently, Prism has most of its molds built outside—by “the best in the U.S. for very tight tolerances,” claims Ignatowski—but insists on its own standards for venting, draft angles, and so on.
Introduced by Zeiger and Spark Industries at the PTXPO, the nozzle is designed for maximum heat transfer and uniformity with a continuous taper for self cleaning.
The 51st annual SPE Automotive Innovation awards gave nods to several ‘firsts’ and added alternative vehicle systems category.
As many molders besides Prism will attest, an important factor in reducing variation is using automation wherever possible. Automation modules mounted on wheels perform operations such as degating, welding, vision quality checks, and laser etching of barcodes on parts. Prism uses robots with vision systems and vacuum sensing to confirm parts removal, cavity separation, and inline box loading or indexing carousels for box and bag filling. Box filling is controlled by weight or shot counts. A light comes on when the box is full to alert a process technician to apply tape and a label.
During its Mobility Days in Austria, Engel and KTM Technologies debuted an all-plastic molded motorcycle seat base produced via a tape-sandwich process that can run in a standard molding process.
This month’s resin pricing report includes PT’s quarterly check-in on select engineering resins, including nylon 6 and 66.
Strict control of product quality is not only an obsession at Prism Plastics, it’s a necessity. The vast majority of the 1 billion custom parts it injection molds annually are tight-tolerance, functional or critical-use components for automotive applications, many of them safety related, such as for seatbelt or airbag mechanisms. Many parts have tolerances from ±50 microns (0.05 mm) down to ±5μ or less. Example: an Ultem PEI airbag component with a ±3μ tolerance.
“Our tools are built like armored tanks so they can last a minimum of 1 million to 2 million shots.” Its first choice is to use hot runners with valve gates. It checks cavity balance by having the robot segregate the first and last parts to fill so they can be checked for conformity to quality specs. The Meadville plant has experience with laser sintering to 3D-print molds with built-in conformal cooling. “We expect to use that more and more,” Ignatowski says.
A brand-new automation cell at Prism has three articulated robots. The first robot removes the part from the press and places it in a fixture. The second robot picks it up, sonic welds it, and then hands it to another fixture. The third robot picks it up, performs vision inspection, and packages the part.
GETTING A QUOTE WITH LK-MOULD IS FREE AND SIMPLE.
FIND MORE OF OUR SERVICES:
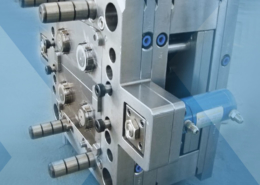
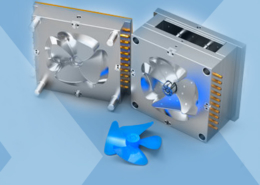
Plastic Molding

Rapid Prototyping
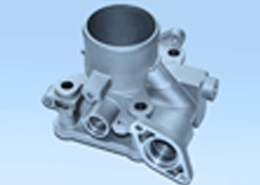
Pressure Die Casting
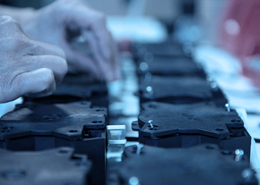
Parts Assembly
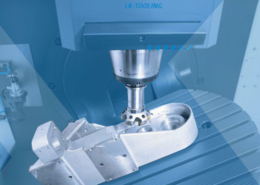