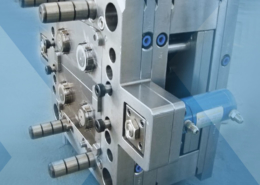
Cellulose Powder–Filled PP Biocomposite Under Development - plastic molding deve
Author:gly Date: 2024-09-30
Ultimately, Braunform claims 45% overall production savings with RotaricE² technology by eliminating the need for two injection molds and machines, as well as an assembly line.
The development supports legislation that sets single-use plastic targets and recycled content goals for brand owners, which stateside is most notably forthcoming CA SB 54.
Rick Lingle is Senior Technical Editor, Packaging Digest and PlasticsToday. He’s been a packaging media journalist since 1985 specializing in food, beverage and plastic markets. He has a chemistry degree from Clarke College and has worked in food industry R&D for Standard Brands/Nabisco and the R.T. French Co. Reach him at [email protected] or 630-481-1426.
The encapsulating concept was introduced at NPE2015 for a single-cavity model, but the 2024 difference is that there is a higher output “double-cavity processing with precise control of the layer,” explains Andy Stirn, general manager advanced systems. “And that is now applicable for chemically recycled content along with mechanically recycled content.”
The RotaricE² concept integrates several production steps — including assembly — in a small space. The technology will be demonstrated by Arburg (Hall 13, Booth A13-1-B13) on an Allrounder More machine, which will produce a Luer pharmaceutical cap measuring 10 mm in diameter and 11 mm in length.
The breakthrough is gaining traction. Stirn informs us that tests and trials are already lined up in North and South America with more to follow.
Milacron and partners perfect the injection molding of a precise layer of recycled content — mechanical or advanced processes — to sustainably boost the eco-footprint of 5-gal plastic pails.
Notably, the multi-component Braunform side-gate injection mold will combine capping and unscrewing functions. The 4+4 cavity mold serves as a basis for a compact series mold in a modular design with up to 64+64 cavities. Six functions are combined in the ejector side — core-back, two sliders per cavity, lifting of the lid, translational capping of the closures, unscrewing, and final ejection. Modules are individually centered and easily accessible, and the overall design is cleanroom compatible thanks to electric drives, corrosion-resistant steel, low-fat lubrication, and rolling element centering systems. Diffusion-welded inserts facilitate die insert cooling on the nozzle side.
Sybridge’s Matt Little and Milacron’s Andy Stirn pause at NPE2024 with the innovative pail and the injection molding system in the background. RICK LINGLE
The inner and outer layers are made of high-density polyethylene. The advanced recycling material demonstrated on May 6 was provided by LyondellBasell. Shell Polymers provides the virgin HDPE.
The RotaricE² injection mold system reportedly achieves 45% overall production savings by integrating several production steps.
Kistler developed the two indirect pressure sensors used in each injection mold cavity to detect defective parts, which are sorted out by the handling system.
SyBridge’s Matt Little, business development manager, life sciences and consumer, sees plastic handles replacing metal to simplify and maximize plastic pail recyclability.
German injection mold supplier Braunform will showcase its RotaricE² technology, which achieves time and cost savings by emphasizing process control over quality control, at K 2022 on Oct. 19 to 26 in Düsseldorf, Germany.
The plastic industry seeks sustainability opportunities throughout the breadth of the market from automotive to medical to packaging. It’s in the latter market where the depth of that commitment was exemplified in the plastic pail category at NPE2024 where Milacron exhibited an M-Series Model 1070 injection molding system capable of adding a core layer of recycled content.
By integrating servo-electric rotary drives in the mold and redirecting rotary movement into translational movement, Braunform achieves compact radial arrangement of injection mold cavities with slides or masking devices around a sprue or, preferably, a side-gate system, the company said.
Participating in the demonstration this year were a collaboration of NPE partner companies Beck Automation, KW Plastics, LyondellBasell, MCC Verstraete, Mold Masters, Shell Polymers, and SyBridge Technologies.
The at-show encapsulated post-consumer recycle (PCR) layer was 46%, according to Stirn, “but we go up to 50% with complete control of where the recycle layer is located, whether inner, middle, or outer layer.”
Geoff Giordano is a tech journalist with more than 30 years’ experience in all facets of publishing. He has reported extensively on the gamut of plastics manufacturing technologies and issues, including 3D printing materials and methods; injection, blow, micro and rotomolding; additives, colorants and nanomodifiers; blown and cast films; packaging; thermoforming; tooling; ancillary equipment; and the circular economy. Contact him at [email protected].
Sustainably speaking, other pails pale in comparison. But that’s not the ultimate solution because there’s more pail sustainability ahead.
A Smart Control system by hot-runner specialist Ewikon ensures real-time data mining on the hot side. The hot-runner system is especially important for the Luer cap, as the shot weight of the TPE-based second component is only 0.05 g.
GETTING A QUOTE WITH LK-MOULD IS FREE AND SIMPLE.
FIND MORE OF OUR SERVICES:
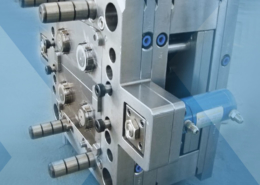
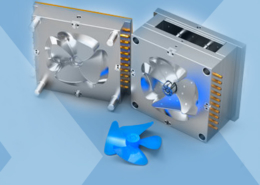
Plastic Molding

Rapid Prototyping
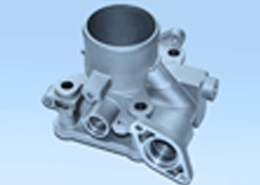
Pressure Die Casting
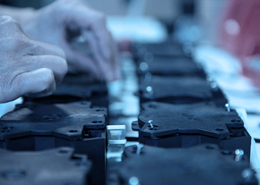
Parts Assembly
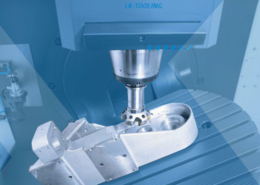