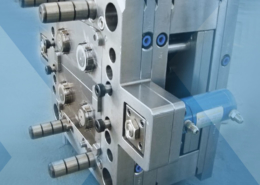
Case study: UK mould maker BM Injection on the benefits of standardisation
Author:gly Date: 2024-09-30
After developing and proving out prototypes, the first commercial use case of this technology was in 2015 with a U.S.-based company, manufacturing pultruded rods for use in industrial robotics.
CMC is expanding, with new fiber production in Europe, faster processes and higher temperature materials enabling applications for industry, hypersonics and New Space.
Lull explains that an intensive, year-and-a-half-long development process followed, designed to find the right set of parameters and tools to optimally overmold the end fittings onto thermoset composite pultruded tubes. In the end, the struts proved successful and demonstrated a 50% cost savings over traditional composite struts made from filament winding or prepreg. The struts were ultimately qualified by Airbus for commercial use, and Epsilon continues to provide these parts to the aerospace market.
CFRP pultrusion and pullwinding specialist Epsilon Composite combines thermoplastic overmolding with traditional thermoset processes, demonstrated through aircraft struts and industrial applications.
As plastic injection molding methods continue to advance and evolve, allowing for enhanced flexibility and more sophisticated customization options, molding companies must be able to stay ahead of the curve in order to offer clients the latest technologies and highest-quality end products. At The Rodon Group, we’ve always been dedicated to constant innovation and improvement, and we’re proud to announce our recent acquisition of several new plastic injection molding machines. Nissei Plastic Injection Molding Machinery Amongst the new equipment are six new hybrid molding machines from Nissei’s FNX-III series - four FNX-180 III hybrid molding machines and two FNX-360 III hybrid molding machines. Incorporating aspects of both electrically and hydraulically powered molding machines, these models are powered by Nissei’s proprietary X-Pump. Besides allowing for energy-use reductions of up to 47% compared to fully hydraulic plastic injection molding machinery, X-Pump-equipped FNX-180 III and FNX-360 III machines offer a wide range of benefits, including: Fast injection response Wide-ranging injection speed Stability in ultra-low velocity range Long-sustained, high injection holding pressure Minimal maintenance and recalibration requirements Affordability, low maintenance, and running costs High-rigidity straight-hydraulic clamping unit Superior precision With greater tonnage capabilities than those of our existing machines, the new FNX-III series plastic injection molding equipment allows Rodon to offer greater production flexibility. We’ve operated this new equipment with several new production programs and have successfully run each machine in conjunction with a Star Automation Servo Robot, which we’ll discuss in greater detail below. Star Automation Servo Robot An industry-leading automated unloader manufacturer, Star Automation specializes in unloaders specifically designed for the injection molding industry; their Servo Robots series of unloaders are among the most reliable, high-performing models available on the market. Rodon’s new Servo robots allow for efficient automatic unloading and stacking of completed, ejected molded parts. Improving our production rates while ensuring the same level of quality clients have come to expect from Rodon, these sophisticated robots feature part present sensors, part and sprue grip circuits, custom step programming, active vibration control, and defective product drop. Learn More The Rodon Group is proud to be at the forefront of the many exciting advancements and trends in plastic injection molding, and our recent equipment acquisition is just one aspect of our commitment to continuous improvement. To learn more about working with a turnkey manufacturer and saving time and money, download our newest free guide today https://info.rodongroup.com/lp-download-the-benefits-of-working-with-a-turnkey-manufacturer. Or, for more information on our products and services, check out our comprehensive product catalog today https://info.rodongroup.com/lp-the-rodon-group-catalog.
Closed mold processes have many advantages over open molding. In this knowledge center, learn the basics and vital tools needed to produce parts accurately.
An on-demand mapping tool for anisotropic materials and polymer material fracture prediction model, i-Lupe, aims to help predict impact, crash behaviors.
Prepreg co-molding compound by IDI Composites International and A&P Technology enables new geometries and levels of strength and resiliency for automotive, mobility.
Jetcam’s latest white paper explores the critical aspects of nesting in composites manufacturing, and strategies to balance material efficiency and kitting speed.
The Rodon Group is proud to announce the launch of our newly redesigned website https://www.rodongroup.com/. Based on both customer and employee feedback, we’ve streamlined and enhanced our site using the latest technology to provide the best possible user experience for our customers and fellow industry professionals. With new user-friendly, intuitive design and various new educational resources, we’ve made it easier than ever to get started on your next high-volume project. What’s New? Let’s take a look at some of the new features our new website has to offer: Responsive Mobile Site In addition to redesigning our website for desktop and laptop, we’ve also accounted for the fact that people are now using technology everywhere - in the office, at home, while traveling. Our new website is responsive and reliable on mobile phone and tablet, so you can navigate our website with ease, whether at your desk or on the production floor. Resource and Media Libraries Our new Resource Library offers free informative guides, catalogs, and helpful industry information available for download. Our eBook titles include: “An Introduction to Plastic Injection Molding” “How to Manufacture a Perfect Plastic Part” and “10 Must-Ask Questions when Choosing a Plastic Injection Molder,” all of which provide valuable industry insights and answers to frequently asked questions customers about the plastic injection molding process. We also provide a comprehensive Media Library - a complete video and photo library that outlines our capabilities and turnkey manufacturing process. In the photo section, users can browse through photos of our engineers hard at work as well as images showcasing the interior and exterior of our cutting-edge facility. Custom Molding Case Studies As a leading authority on plastic injection molding, we’re proud of our innovative problemsolving solutions, offering our high volume customers custom solutions catered to their specific application and needs. Showcasing our diverse capabilities in our new Case Study section, we’ve compiled some examples of our previous work and product offerings, such as: Residential window hardware Custom beverage cap for the food and beverage industry Point-of-purchase (POP) display components Polystyrene diagnostic kit for the medical industry Solutions and Capabilities As a full-service turnkey manufacturer, The Rodon Group works with customers from concept to completion, providing all the necessary resources to promptly and accurately complete your project. On our new website, we break down the three main stages of this turnkey process - design, toolmaking, and manufacturing - allowing potential customers to easily assess our capabilities and further understand our production and quality control processes. Learn More Providing high-volume, custom plastic injection molding solutions since 1956, The Rodon Group offers innovative manufacturing solutions for customers who have an annual volume of 1 million or more parts per year. To learn more about The Rodon Group and how we can help with your next project, visit our new website https://www.rodongroup.com/ today.
In the meantime, Epsilon and Somocap developed a new overmolding process and began producing industrial parts commercially. So, for its next R&D iteration of these struts with Airbus, Epsilon introduced overmolding of the end fittings as a solution that met the needs for both optimized cost and high reliability in the parts and process.
In 2012, the company began experimenting with alternative methods for adding end fittings or other functionality to components made via pultrusion or pullwinding. “The goal was to find a method that would result in a low-cost, high-quality product, which is kind of the Holy Grail,” explains Alexandre Lull, deputy CEO of Epsilon Composite.
CompositesWorld is the source for reliable news and information on what’s happening in fiber-reinforced composites manufacturing. About Us
This collection details the basics, challenges, and future of thermoplastic composites technology, with particular emphasis on their use for commercial aerospace primary structures.
Robbins will be Vice President, Legal Affairs and General Counsel for K’NEX Brands Hatfield, PA, – K’NEX, the only U.S. construction toy company focused on Building Worlds Kids Love®, is pleased to announce the promotion of Rachel Robbins to Vice President, Legal Affairs and General Counsel. Hired in 2013, Ms. Robbins previously served as Associate General Counsel for K’NEX Brands. Prior to joining K’NEX, Ms. Robbins was a Partner in the Commercial Litigation group of the law firm Cozen O’Connor, where she successfully represented a broad spectrum of clients in the life safety, pharmaceutical, entertainment, internet, telecommunications and sports management industries in complex commercial disputes, including antitrust, securities, trademark infringement, and product liability actions. Ms. Robbins earned her Juris Doctor from the Dickinson School of Law of Pennsylvania State University, and served as Comments Editor for the Dickinson Law Review. She earned her undergraduate degree from Binghamton University, where she majored in business management, and minored in marketing. In her new position, Ms. Robbins will provide legal counsel to company management and business teams as to commercial relationships, as well as all general corporate matters, including contracts, employment, regulatory, and intellectual property matters. About K’NEX Brands Founded in 1992, K’NEX Brands, the world’s most innovative construction toy company, was established to make and sell what has become one of the world’s leading integrated construction systems for children, and is America’s STEM building solution. Winner of over 250 international awards and recognitions, K’NEX, America’s Building Toy® company, is focused on Building Worlds Kids Love® and encourages youngsters to “imagine, build and play.” From the living room to the classroom, K’NEX has building toys specially designed for every age group and skill level. The K’NEX family of brands includes K’NEX Building Sets, K’NEX Thrill Rides, K’NEX Education™, Lincoln Logs®, Tinkertoy®, NASCAR®, Angry Birds™, Mario Kart Wii™, Mario Kart 7™, Super Mario™, PacMan™, Titanfall™, Family Guy™, Plants vs. Zombies™, and more. Since 1992, The Rodon Group®, a subsidiary of K'NEX Brands, L.P., has manufactured over 31 billion parts for the K'NEX building toy system. Join us as we help build the leaders of tomorrow. For more information, please visit www.knex.com or www.rodongroup.com. Contact: Kate Loffio K’NEX Brands 215.996.4209 kloffio@knex.com
This session is designed to demonstrate the benefits of ultra polymers for aerospace applications with real case examples of Syensqo's polymer portfolio. Agenda: Introduction to ultra polymers (PAEK, PEKK, PEEK, PAI) key features Application of ultra polymers in aerospace: concrete examples Benefits of ultra polymers: enhanced performance, durability and cost-efficiency
“[Our patients were] swabbed twice, first with the one Fox Chase had been using and then with the new test swab,” said Dr. Eric M. Horwitz, Chair of Radiation Oncology at Fox Chase. “It turned out that the one [The Rodon Group] designed actually worked even better than the one we had.” Click the headline above to read the full article. https://www.thomasnet.com/insights/plastic-injection-molder-invents-innovative-american-made-fda-registered-covid-19-testing-swab/
During this CW Tech Days event, sponsored by Composites One, experts will offer presentations to review and evaluate the composite materials, processes and applications that should and will be considered for use in the infrastructure and construction markets.
The first demonstrations of the technology involved injecting polyetheretherketone (PEEK) over the top of carbon fiber/epoxy pultruded tubes. “The PEEK is injected at a very high temperature, about 300°C, so we had to make sure that the resin matrix of the [thermoset] composite tube would be able to sustain this temperature for a brief period of time,” says Latron. Through trial and error the R&D team figured out the right combination of a fast injection overmolding process and the required glass transition temperature (Tg) thermoset matrix to produce repeatable results with no damage to the pultruded tube, despite the differences in the materials.
We developed this eBook with designers, engineers and purchasing specialists in mind. It is written to provide a basic understanding of plastic injection molding presses, processes and costs. Our goal is to make our customers more knowledgeable about what goes into making a plastic part.
How the predictive tool “CZone” is applied to simulate the axial crushing response of composites, providing valuable insights into their use for motorsport applications.
Rodon takes a solid relationship with toy giant K’NEX and applies its business model to other manufacturers—taking domestic manufacturing to the next level.
Initial demonstration in furniture shows properties two to nine times higher than plywood, OOA molding for uniquely shaped components.
Whether you’re exploring new applications or seeking to gain a foothold in emerging markets, Carbon Fiber 2024 is where you’ll discover the insights and connections needed to shape your business strategy. Register now.
An overview of ASTM Standard Guide D8509, and its coupon-level mechanical testing of design properties for analyzing composite bolted joints.
Aircraft struts and beyond. After initial successes in industrial and aerospace markets, Epsilon says it uses injection overmolding as a cost-effective, reliable alternative to adhesive bonding for many of its large-scale orders.
Collins Aerospace draws on global team, decades of experience to demonstrate large, curved AFP and welded structures for the next generation of aircraft.
However, the challenge was that Epsilon’s pultruded profiles are made with epoxy or another thermoset resin matrix, and injection overmolding introduces a thermoplastic matrix, injected under high heat and pressure, with a different coefficient of thermal expansion.
Beyond aerospace, the company has also demonstrated the technology commercially with agricultural machinery, working with a customer to replace steel spray boom arms for industrial tractors with 50-meter-wide pultruded composite booms. “The steel booms cannot be as wide, because they are heavier and not as stiff,” explains Romain Coullette, sales director of Epsilon. “Composites are stiffer, lighter and eliminate potential issues with corrosion, so there are many benefits, but productivity is the biggest advantage.” Larger booms enable fields to be sprayed in less time, increasing efficiency.
Fluid trap tip for superior collection and accurate results. An excellent choice for laboratories, hospitals, testing centers, medical schools and clinics.
Compared to other methods like bonding, use of mechanical fasteners or even filament winding over the top of the end fitting, benefits of overmolding are said to include lower cost, weight savings and improved impact tolerance. If metal is replaced by a thermoplastic, corrosion risks can also be eliminated.
Explore the cutting-edge composites industry, as experts delve into the materials, tooling, and manufacturing hurdles of meeting the demands of the promising advanced air mobility (AAM) market. Join us at CW Tech Days to unlock the future of efficient composites fabrication operations.
CompositesWorld’s Tech Days: Design, Simulation and Testing Technologies for Next-Gen Composite Structures is designed to provide a multi-perspective view of the state of the art in design, simulation, failure analysis, digital twins, virtual testing and virtual inspection.
The Thomas Verified Supplier badge indicates that Thomas has confirmed the company operates in North America, provides accurate business information on the Thomasnet.com supplier discovery platform, has undergone a complete review and validation of all products and services currently offered, and are open to quoting new opportunities.
The Rodon Group is an ISO 9001:2015 certified landfill-free, high volume, plastic injection molder. In business since 1956, the Rodon Group makes billions of parts each year in its 125,000 square foot facility. We offer a turnkey and innovative manufacturing solution including mold design, mold building, and high-volume parts manufacturing. With over 125 plastic injection molding presses, Rodon is one of the largest family-owned and operated injection molders in the United States. The Rodon Group serves a diverse group of industries including food and beverage, window and door, medical and pharmaceutical, consumer products, construction and more. The Rodon Group has earned a reputation for being one of the best in the industry, offering high-quality, low-cost solutions. With our globally competitive pricing, we offer you the opportunity for leveraging the benefits associated with using a domestic manufacturer while avoiding the risks of offshore sourcing. Specializing in close-tolerance injection molding of small plastic parts, we provide a total concept solution from design and tooling to production, fulfillment, and packaging. The combined effort of our designers and toolmakers results in molds that ensure quality, precision tolerances, and optimized cycle times. We have the capacity to mold parts with complex geometries and variations in wall thickness. Our maximum part size is 10 inches square, although our major concentration revolves around parts with smaller dimensions. We have material specialists on staff to make recommendations from more than 100 commodity, engineering, and specialty plastics, including FDA, RoHS, REACH, and NSF certified resins and HACCP-compliant materials. Our 125 fully automated presses are the heart of our operation. Ranging in size from 46 to 720 tons, they feature capacities from fractional to 107 ounces. Hydraulic, hybrid, and all-electric technologies allow us to adapt production to the individual requirements of every application. Microprocessor-controls, self-diagnostics, and full-servo robotics allow us to operate 24 hours a day, 7 days a week for maximum efficiency. Using a combination of online vision inspection systems, SPC charting, as well as in-lab test, measurement, and inspection equipment, we ensure tolerances, color, physical appearance, and mechanical characteristics match your specifications. We offer custom packaging, 3D printed prototypes, safety stocking programs, just-in-time delivery, and a number of other additional support services.
Base Materials introduces a high-performance, toughened epoxy tooling board designed for thermoforming and vacuum forming processes, direct-to-part applications and more.
Explore the technologies, materials and strategies used by composites manufacturers working in the evolving space market.
The composite tubes white paper explores some of the considerations for specifying composite tubes, such as mechanical properties, maintenance requirements and more.
Our line of universal plugs is designed to maximize manufacturing efficiency by speeding production and lowering inventory costs. Its unique annular fin design provides a positive fit for a wide range of tubing wall thicknesses with a single component. Within its 14-23 gauge range, the Universal Plug greatly reduces the number of plug I.D.'s needed in inventory. One plug per tube O.D. does the job, often with improved fit. Round, square or rectangular, Universal Plugs can make a substantial difference in efficiency and production costs.Standard plugs include a wide range of plastic plugs, flat head plugs, rectangular plugs, square plugs, forked plugs, ball plugs, specialty plugs, split stem & stem bumpers, beveled edge hole plugs and flat top hole plugs. In-house design services for specific custom plastic plugs are available. To see for yourself, contact us for samples today.
The composites industry is increasingly recognizing the imperative of sustainability in its operations. As demand for lightweight and durable materials rises across various sectors, such as automotive, aerospace, and construction, there is a growing awareness of the environmental impact associated with traditional composite manufacturing processes.
“We worked with industrial clients at first, but the first major business for us was aerospace,” says Lull. In 2018, the company began an R&D project with Airbus (Toulouse, France). This work stemmed from a previous R&D collaboration in which Epsilon had demonstrated its pultrusion technology for manufacturing high-performance tubular structural struts with bonded metallic end fittings. Epsilon successfully demonstrated the performance of the parts and reliability of the manufacturing process up to TRL 6 and Airbus’s internal standards — however, the project did not move on commercially because the structural bonding was considered too risky for critical aerospace structures. To combat these risks, Epsilon developed and patented a process specifically designed to secure the bonding according to aerospace standards, but the process was more expensive, negating the time and cost savings of choosing pultrusion for the struts to begin with.
Lull notes that a range of materials have been used, from relatively low-cost polyamide 6 (PA6) filled with glass fiber, to higher performance materials such as PEEK, polyphenylene sulfide (PPS) or polyetherimide (PEI) reinforced with glass or carbon fiber. Unreinforced resin systems can also be used if desired.
As plastic injection molding methods continue to advance and evolve, allowing for enhanced flexibility and more sophisticated customization options, molding companies must be able to stay ahead of the curve in order to offer clients the latest technologies and highest-quality end products that suit their needs in the changing market. At The Rodon Group, we’ve always been dedicated to constant innovation and improvement, and we’re proud to announce a facility expansion and acquisition of a new, large size, 720-ton hybrid plastic injection molding machine for large parts. The expansion includes an additional 125,000 square feet of space at a secondary location in Hatfield, PA. The area will allow Rodon to grow with its diverse customer base and allow for improved process flow and future advancements of our injection molding capabilities. The new 720-ton injection molding machine enhances the capacities of our existing 118 molding presses to now offer a range of fractional to 107 ounces, and clamping force of 46 to 720 tons. With a much higher tonnage capability than those of our existing machines, the new press allows us to offer greater production flexibility for large part injection molding and improves our capabilities for customers that are looking to manufacturer these types of parts. Since 1956, our core competencies have centered on small (index card size or smaller), high volume custom plastic components. With these new capabilities and expansion, we look forward to continuing to serve our existing customers as well as new customers that are looking to source globally competitive, innovative manufacturing solutions for larger plastic parts. The Rodon Group is proud to be at the forefront of the many exciting advancements and trends in plastic injection molding, and our recent equipment acquisition and expansion are just two aspects of our commitment to continuous improvement. Contact us today if we can help answer any questions.
One idea was to use composite injection overmolding as a means for joining a metal end fitting to the pultruded profile. Injection overmolding, using primarily glass or carbon fiber-reinforced thermoplastics, was chosen, Lull says, because of its potential for complementing the low cycle times and high-volume capabilities of the pultrusion or pullwinding process the company was already using.
The composites-intensive VTOL platform is next expected to undergo a series of test flights in various conditions to validate its performance, safety and reliability, leading up to eventual certification.
The composites industry plays a crucial role in developing lightweight and durable materials for a range of applications, including those critical to national defense. One key focus area is the development of advanced structural materials and manufacturing technologies that support next-generation space, missile and aircraft systems for the U.S. Department of Defense (DOD). ARC Technologies LLC (ARC), a division of Hexcel Corporation, based in Amesbury, Massachusetts, is a provider of advanced composites structures, specialty materials and other unique products that provide the U.S. Department of Defense with advanced capabilities to protect service members while in harm’s way. This team’s specialty is to understand a specific need from a program office, PEO, platform manufacturer or other offices within the DOD. With that understanding, the team can design a solution, develop a prototype for test and evaluation, perform extensive in-house testing — including electromagnetic, environmental and structural testing — and then partner with the customer through platform evaluation. The Hexcel Amesbury division has a team of engineers on staff, including mechanical, chemical, electrical and research and development specialists that can provide design, testing and manufacturing capabilities to service customer requirements from concept through production. This presentation will illustrate capabilities in advanced composites and other specialty materials structures, focusing on the Hexcel Amesbury team's niche in electromagnetic signature reduction and other unique capabilities.
This collection features detail the current state of the industry and recent success stories across aerospace, automotive and rail applications.
Ultimately, this method can either be used as a way to join a traditional metallic end fitting to the pultruded profile or tube, or the metal can be replaced altogether, and a thermoplastic composite tip can be added via overmolding.
Additionally, stitch-bonded non-crimp fabrics (NCFs) provide manufacturers and asset owners even more ways to gain a competitive advantage with products built specifically for the environments and loading conditions in which they will be utilized. Join Vectorply Corporation and Creative Composites Group (CCG) for this in-depth webinar detailing the process of engineering NCFs to build composite parts that will stand the test of time. Unlike steel, concrete and wood, composite NCFs can be optimized utilizing various fiber types, architectures and substrates to achieve the specific goals of their application efficiently. High corrosion resistance, strength and stiffness, and longevity can all be accomplished with custom-designed laminates for these heavily abused applications. Vectorply Vice President of Engineering Trevor Gundberg and Creative Composites Group Chief Sales Officer Dustin Troutman will share their industry-leading expertise on the process of laminate design and part production. Attendees can expect to learn when to use composite NCFs in their production process and the wide range of fiber-reinforced plastic (FRP) composites that Creative Composites Group produces for the industrial and infrastructure markets. Whether you want to learn more about utilizing NCFs in your production process or why CCG’s extensive product line may be the choice for your project, this webinar is the place learn the process and how to take the next steps. Agenda: Distinct advantages of non-crimp fabrics versus alternative materials How to design laminates for specific processes such as pultrusion and infusion Real-world success spotlights of NCFs in industrial applications
American Bureau of Shipping (ABS) certifies use of jointly developed CFRP repair technique on FPSO and FSO industrial systems, addressing traditional steel restoration challenges.
The patent notes, “This method is simple because it may require few steps, but it makes it possible to obtain assemblies that can withstand strong traction, compression, temperature gradients, with materials of different expansion coefficients.”
How the predictive tool “CZone” is applied to simulate the axial crushing response of composites, providing valuable insights into their use for motorsport applications.
The Marservis PROeco is a mass transportation marine vessel using Bcomp natural fiber for interior parts in place of standard materials.
Epsilon Composite (Gaillan Médoc, France) specializes in carbon fiber/epoxy pultrusion and pullwinding, enabling the manufacture of medium- to large-series, high-performance carbon fiber composite parts, faster and at a lower cost compared to many other processes.
Thermoplastics for Large Structures, experts explored the materials and processing technologies that are enabling the transition to large-part manufacturing.
In 1956, The Rodon Group was founded with just four presses, 5,000 square feet of space, and a big vision. Today, as we celebrate our 65th anniversary, we do so as one of the largest family-owned and operated plastic injection molders in the country. With 128 presses, we serve clients in a wide range of industries with innovative manufacturing solutions, and we look forward to doing so for many years to come. The Rodon Group’s History The Rodon Group was founded by Irving Glickman in 1956 while he was still working with ELGO Rubber. This small, part-time company grew steadily with Glickman's strategic investments in equipment and other additions. He was passionate about cost-effective manufacturing materials and methods, and that thoughtful planning helped get the company off the ground and growing as ELGO Rubber eventually closed. Today, The Rodon Group is one of the largest family-owned and operated plastic injection molding companies in the United States, with 250,000 square feet of manufacturing space and a robot at every press. We're ISO 9001:2015 certified with a 99.92% quality parts rating, and we guarantee our molds for the life of your project. From design to toolmaking to materials selection, we're here to take your project from start to finish. What Sets Rodon Apart Our years of plastic injection molding experience is just the beginning. Irving Glickman's knowledge and foresight laid the foundation for success, which has been driven by the key values that were established in the earliest days and continue to serve as our guiding principles: We Treat Our Employees Well: Having third-generation employees on our team is no accident. We value our team members and know they're the backbone of the company. As a result, we have high employee retention and a team that's deeply invested in our clients and the work we do. We Offer Fair Prices for Our Customers: Part of our mission is to make sure you have the cost-effective solutions you need to run your business. We take pride in customizing a solution that helps you save time and money. We Re-Invest Our Profits in Talent and Equipment: Staying at the top of the industry means staying on top of the latest innovations and ensuring we attract the best professionals to work with us. Our company grows because we're willing to invest in our people, their education, and the equipment they use every day. We Focus on Being a Solution for the Customer--Never a Problem: We're your partner for your projects. We listen to your goals and develop a plan that suits you, managing any challenges as they arise to ensure the process is seamless for you. It's our job to make your business simpler, not more challenging. Over the decades, we've worked with a variety of industries and applications, including medical, food and beverage, window and door components, and construction with SillDry, a patented window protection line co-invented by our own Joel Glickman. As a proud U.S. manufacturer, we've always promoted domestic manufacturing, and we're active members of both American Made Matters and the Made in America Movement to help educate people about the benefits of buying American-made products. The future of U.S. manufacturing is bright, and we're excited to be a part of it. Our long history and extensive experience has prepared us for the next 65 years and beyond. Our turnkey manufacturing solutions are backed by our commitment to quality and excellent customer service, and we look forward to helping you with your high-volume production project as we celebrate our 65th anniversary. Contact us to learn more or request a quote for your project.
Hatfield, PA – The Rodon Group has partnered with ICF Solutions, a division of Indian Creek Foundation on a facility-based work program. Since 1975, the Foundation’s mission is to “provide opportunities for people with intellectual and developmental disabilities; to live in and enrich the community throughout their lives.” The work program includes onsite training for various jobs that are subcontracted from local businesses, such as Rodon. Types of work include bulk mail processing, product assembly, packaging and sorting. More than 60 local businesses rely on ICF Solutions for these services. The Rodon Group has been working with ICF Solutions since 2012 and is currently utilizing their team to assemble multiple plastic parts for a variety of their customers. The trained workers average 300,000 units per month for Rodon. One or two staff members oversee the workers at each table and tables are set up by job skill, background and overall capabilities. ICF Solutions also partners with Thomas Jefferson University occupational therapists who intern to help the workers with various needs and independence goals. As of June, there were approximately 86 individuals involved in the program. According to Kevin McGrath, vice president of sales and marketing at Rodon “The collaboration with ICF has been invaluable. The assembly services they’ve provided have given us the ability to pursue additional opportunities and markets that we would not have been able to pursue otherwise. We are very thankful to have a local community resource like ICF. “ To learn more about Indian Creek Foundation and ICF Solutions, visit their website at www.indcreek.org/icf-solutions/ About The Rodon Group The Rodon Group is an ISO 9001:2008 certified landfill-free, plastic injection molder. In business since 1956, The Rodon Group makes billions of parts each year in its 125,000 square foot facility. With over 105 injection molding presses, Rodon is one of the largest family-owned and operated plastic injection molders in the United States and serves a diverse group of industries including consumer products, medical, construction, pharmaceutical and toys. Since 1992, Rodon has manufactured over 30 billion parts for the K'NEX building toy system, and is a subsidiary of K'NEX Brands, L.P.
The Rodon Group, one of the largest family-owned and operated plastic injection molders in the U.S., has added a Baxter robot to their factory floor in Hatfield, PA. See how employees work alongside Baxter, their robotic manufacturing assistant and co-worker.
The first project is underway to recover carbon fiber used in an A330-200 aircraft, which will then be regenerated for other end uses by HRC.
EU project will develop bio-based, repairable and recyclable vitrimer composites and advanced sensors for highly reliable, sustainable wind blades.
Continuous fiber-reinforced thermoplastic composite targets full circularity in aircraft interior applications, with FST, impact resistance and toughness features.
CW Tech Days are virtual events dedicated to the topics impacting the composites industry today. Access past event recordings and register for upcoming Tech Days.
An inefficient injection mold setup can result in increased machine downtime and ultimately have a negative impact on your profit margins. Click the headline above to read the full article. https://www.thomasnet.com/insights/improve-production-with-this-injection-mold-setup-checklist/
Knowing the fundamentals for reading drawings — including master ply tables, ply definition diagrams and more — lays a foundation for proper composite design evaluation.
CompositesWorld’s CW Tech Days: Infrastructure event offers a series of expert presentations on composite materials, processes and applications that should and will be considered for use in the infrastructure and construction markets.
Aerospace manufacturer joins forces with composite materials company to achieve sustainable manufacturing practices that overcome traditional composite layup tooling.
Formnext Chicago is an industrial additive manufacturing expo taking place April 8-10, 2025 at McCormick Place in Chicago, Illinois. Formnext Chicago is the second in a series of Formnext events in the U.S. being produced by Mesago Messe Frankfurt, AMT – The Association For Manufacturing Technology, and Gardner Business Media (our publisher).
Functionalizing semi-finished pultruded/pull-wound profiles. In searching for low-cost processes to add functionalization to its semi-finished composite profiles and tubes, and to reduce the use of adhesives with its products, Epsilon Composite developed and patented a thermoplastic composite injection overmolding process with its injection molding partner Somocap. Photo Credit, all images (including image in line with title): Epsilon Composite
See how we've remained a manufacturing leader since 1956. This video highlights our factory, employees and our three primary capabilities as a high-volume, custom plastic injection molder: mold design, mold building, and parts manufacturing. In business since 1956, The Rodon Group makes billions of parts each year in our 125,000-square-foot facility. With over 117 injection molding presses, we are one of the largest family-owned and operated injection molders in the United States.
Specialists in carbon fiber/epoxy pultrusion and pullwinding. These images show Epsilon’s pullwinding process before (top image) and after (bottom image) cure via a heated die the profile is pulled through.
However, bonding requires the addition of several, often manual, steps: surface preparation, application and curing of the adhesive. This makes adhesive bonding too cost- and labor-intensive for many large-series applications that require thousands of parts per year. Mechanical fasteners can also be used in some cases, but these introduce other challenges as well, such as added weight and assembly steps, and the necessity to machine holes into the pultruded part, which often reduces its mechanical properties.
This technology has become a go-to solution for Epsilon for large-series parts across end markets. “We’ve been making tens of thousands of parts with zero failure,” says Coullette. “It’s very cost-competitive. Eventually we plan to replace bonding for medium- and large-series parts in all of our end markets.”
Low-melt polyaryletherketone (LMPAEK) unidirectional tapes provide outstanding thermal and fire protection, demonstrating their effectiveness through rigorous testing. These tapes are fire, smoke and toxicity compliant with FAR25.853 and meet OSU Heat Release Rate standards. The tapes were tested under ISO 2685/AC 20-135 Change 1, meeting the fireproof criteria. Additionally, they met UL 2596 requirements for battery thermal runaway tests. These tapes are crucial for high-temperature applications showcasing their resilience and safety in both aerospace and automotive applications. Part of a broader range that includes films and compounds, Victrex LMPAEK materials are valued for their excellent processability and weldability. They offer versatile solutions for complex needs beyond traditional structural parts, such as: thermal runaway and lightning strike protection, heat sinking, and intricate bracketry. Victrex LMPAEK materials facilitate automation and high-rate production while addressing performance and sustainability challenges. With reduced environmental impact, lower weight and cost-efficiency, they meet the evolving demands of the transportation industry and support innovative design solutions. Agenda: Introduction to LMPAEK ecosystem, highlighting unidirectional tapes Thermal and fire protection performance: applications and benefits Material forms and processability Sustainability and efficiency Conclusion and future innovations
According to the U.S. patent filing in 2021, the process involves several steps: First, a hollow, tube-shaped thermoset composite profile is produced via pullwinding or pultrusion. The end of the profile is then machined to allow for the shape of the end fitting to be attached, which provides a rough surface area for the profile to attach to. Next, a tool/plug is positioned within the profile in the injection machine, and the thermoplastic is then injected, under a specified heat and pressure, around the profile and end fitting, binding them together.
Reliable news and information on where and how fiber-reinforced composites are being applied — that’s just the start of what you get from our team here at CompositesWorld.
The Rodon Group is committed to environmental sustainability. The company's green initiatives make it a leader in the plastics industry. Its manufacturing process minimizes packaging, transportation costs, waste, water consumption and energy. Consider this example: in manufacturing just one of the more than 600 unique K'NEX parts, the Rodon Group recycles enough cardboard to save 300 cubic yards of landfill space, the equivalent of three football fields!
The original demonstrator parts not only proved feasibility of the process, but exceeded performance expectations, Lull says. This led the company to patent the technology, and to begin introducing it to customers for commercial applications.
Epsilon spent the next few years figuring out the best way to implement its ideas for a hybrid thermoset composite pultruded component overmolded with a thermoplastic. For this, Epsilon worked closely with its injection molding partner Somocap (Jatxou, France). “We brought the engineering and composite knowledge, and they brought the injection molding machinery and process knowledge,” explains Ambroise Latron, head of R&D at Epsilon.
In these sessions, experts will discuss the emerging hydrogen economy and the opportunities for composites in this lucrative space.
Our Standard Caps include a wide range of plastic caps, tubing caps, ball caps, square caps, rectangular caps, bar caps, vinyl shower rod caps, heavy caps, angle iron caps, concrete form bullet caps, heavy vinyl tips, reducing silencers, wire tips, concrete form end tips and self tapping thread protectors.
Epsilon’s R&D team continues to optimize its overmolding process, to make the overall process and workflow faster and more efficient between pultrusion and injection, and to develop lower cost or modular tooling suitable for small-series applications.
Thomas uses cookies to ensure that we give you the best experience on our website. By using this site, you agree to our Privacy Statement and our Terms of Use.
Performing regular maintenance of the layup tool for successful sealing and release is required to reduce the risk of part adherence.
Kennametal will cover the influence of different composite materials characteristics on drilling performance and how to optimize the process. Agenda: Who is Kennametal? Hole making challenges in composite materials Innovations for hole making applications Upcoming events and academic partnerships
Celebrating National Composites Week 2024, CW looks at how composites are being used to provide the next generation of energy.
Prepreg co-molding compound by IDI Composites International and A&P Technology enables new geometries and levels of strength and resiliency for automotive, mobility.
Our Standard Fasteners include a wide range of fasteners, two piece plastic fasteners, finned fasteners, removable fasteners, push fasteners, tufting button set, and two piece removable rivets. Custom designed plastic fasteners are available.
Injection molding services for hardware, appliances, doors, and windows. Works with acetal, nylon, acrylonitrile butadiene styrene (ABS), high impact polystyrene (HIPS), low and high density polyethylene, polyamide, polycarbonate (PC), and polypropylene (PP) materials. Cleanroom services are provided. Caps, fasteners, plugs, swabs, sockets, spacers, bushings, and washers are also offered. Prototypes and high volume production runs are available. Designing, engineering, tooling, and inventory management are offered as secondary services. Serves construction, medical, pharmaceutical, telecommunication, transportation, food, and beverage industries.
Whether you’re exploring new applications or seeking to gain a foothold in emerging markets, Carbon Fiber 2024 is where you’ll discover the insights and connections needed to shape your business strategy. Register now.
The JEC Forum DACH is a business meetings event organised by JEC The JEC Forum DACH is organised on October 22 and 23, 2024 by JEC, in partnership with the AVK, gathering the composite materials community from the DACH Region (Germany, Austria and Switzerland).
Over the last 8 months, Archer Aviation has completed a total of 402 test flights with its composites-intensive aircraft, adding to key milestones.
Hatfield, PA – The Rodon Group participated in the Walmart sponsored U.S. Manufacturing Summit in Denver, CO. Walmart executives, industry experts, suppliers, and component manufacturers gathered for two days to discuss Walmart’s commitment to spending an additional $50 billion on investment of American-made products. Rodon exhibited at the Summit’s trade show event, where over 85 other contract manufacturers, material suppliers and service providers were on hand to meet with companies looking to manufacturer their products in the U.S. According to Michael Araten, President and CEO of K’NEX Brands and The Rodon Group, “Since 1992, our subsidiary The Rodon Group has helped K’NEX Brands make this a reality, manufacturing more than 32 billion bricks, rods and connectors at our plastic injection molding facility in Hatfield, Pennsylvania. We sell many of these toys at Walmart. So when the company (Walmart) announced its U.S. manufacturing commitment, we were thrilled – because we were aligned with a retailer that’s acting on a cause we’re passionate about.” Mr. Araten was personally invited by Walmart to speak at the Summit along with Jim Steven, CEO of Weber Grills. Walmart created a live webcast of the event which can be seen at http://news.walmart.com/events/2014-us-manufacturing-summit Walmart’s blog features an article by Mr. Araten, appropriately titled “Constructing the Future of U.S. Manufacturing”. In the post he states “While the case for manufacturing in America has been presented by many, some businesses remain skeptical that there are advantages. And we know firsthand the journey isn’t always easy. “At The Rodon Group, we not only make toys – we also make about 5 billion parts a year for industries from home construction to food and beverage. So we’ll be sharing those details with companies who are interested, and we’ll also be seeking our own partners, too.” Rodon has been on the forefront of American Manufacturing from the beginning, offering their “Cheaper than China" pricing policy and reshoring billions of manufactured parts back to the United States. According to Lowell Allen, executive vice president of manufacturing, recent expansion of their facility underscores Rodon’s commitment to re-shoring parts for other companies. “We have invested a great deal to increase our manufacturing capacity, strengthening our position as a premier U.S. plastics manufacturer.” About The Rodon Group The Rodon Group is an ISO 9001:2008 certified landfill-free, plastic injection molder. In business since 1956, The Rodon Group makes billions of parts each year in its 125,000 square foot facility. With over 105 injection molding presses, Rodon is one of the largest family-owned and operated plastic injection molders in the United States and serves a diverse group of industries including consumer products, medical, construction, pharmaceutical and toys. Since 1992, Rodon has manufactured over 32 billion parts for the K'NEX building toy system, and is a subsidiary of K'NEX Brands, L.P.
In the Automated Composites Knowledge Center, CGTech brings you vital information about all things automated composites.
Full service manufacturers incorporate a complete line of production capabilities to facilitate fast, cost-efficient manufacturing of complex products without the need for multiple contractors.
Specializing in high-volume, custom manufacturing solutions for a range of industries, The Rodon Group recently announced that their 720-ton hybrid plastic injection molding machine is now being used to manufacture a new, large-scale component for a customer in the food and beverage sector. Click the headline above to read the full article. https://thomasnet.com/insights/u-s-plastic-injection-molder-uses-720-ton-hybrid-machine-to-manufacture-new-large-scale-component
Since its start in the late 1980s, the company has manufactured semi-finished pultruded profiles for a variety of applications in aerospace, industrial and other markets. For many of the end-use parts made from Epsilon Composite’s profiles and tubes — aircraft struts, industrial parts, technical rollers and more — metal or plastic end fittings and inserts are often bonded to them to add functionality or a connection point for other parts.
There are other composite booms on the market; Epsilon’s is a truss-shaped pultruded structure, which Coullette says makes it highly optimized for high stiffness at the lowest weight possible and the least amount of material use, leading to lower overall costs.
Prepreg co-molding compound by IDI Composites International and A&P Technology enables new geometries and levels of strength and resiliency for automotive, mobility.
This sidebar to CW’s August 2024 feature article reviews this technology for more efficient composites manufacturing and why it aligns with Koridion active core molding.
Analyzing structural resonance of the aircraft under various loads becomes a critical step in obtaining flight certification.
During this webinar, the audience will be introduced to a variety of fiber composite technologies — as well as the machines and equipment — from short fibers to continuous fibers, from thermoset to thermoplastic, as well as the according process technology, including a special focus on long-fiber injection (LFI) and structural composite spray (SCS). Focus markets include automotive, aviation and AAM, transportation, and construction. This webinar will provide a detailed overview of according application examples. Agenda: Long fiber injection (LFI) Structural composite spray (SCS) Resin transfer molding (RTM), wet compression molding, etc. Pultrusion FiberForm
Increasingly, prototype and production-ready smart devices featuring thermoplastic composite cases and other components provide lightweight, optimized sustainable alternatives to metal.
Our Additional Standard Products include caster sockets for beds, snap tie cones, plastic spacers, bushings , hose washers, O rings, eyeglass clips and inserts, dowel pins and hose grips.
Recoat temperature, part orientation and bead geometry are some key design variables to consider for a successful and reliable large-format additive manufacturing (LFAM) process.
Validation of 80-100% tensile strength and comparability to injection molding via Voxelfill extrusion process was achieved through plastic and fiber-filled test series.
Recoat temperature, part orientation and bead geometry are some key design variables to consider for a successful and reliable large-format additive manufacturing (LFAM) process.
In 2018, Teijin broke ground on a facility that is reportedly the largest capacity carbon fiber line currently in existence. The line has been fully functional for nearly two years and has plenty of room for expansion.
Thunder Composite Technologies uses its automated pultrusion, RTM and other processes to produce custom-engineered composite parts for automotive and land defense vehicles.
A combination of Airtech’s 3D printing materials and Ascent’s production capabilities aim to support increased use of composite additive tooling in spaces like defense and aerospace.
Six U.S. companies have proven their recycling technologies for composites and rare earth elements, and will be supported for relevant scale demonstration and validation.
CompositesWorld's Carbon Fiber conference offers you cutting-edge information and access to industry experts in streamlining manufacturing costs, market outlooks and forecasting, and more. You will make invaluable contacts as you meet and network with the industry's most innovative and influential leaders at Carbon Fiber. __PRESENT
First application: Industrial. One of Epsilon’s core end markets, industrial applications such as arms for machinery or robotics, were the first application of its injection overmolding joining process.
Program will focus on sustainable, next-gen wing solutions, including in wing design and manufacturing and advancements in carbon fiber-reinforced composite materials.
Foundational research discusses the current carbon fiber recycling landscape in Utah, and evaluates potential strategies and policies that could enhance this sustainable practice in the region.
“It’s a big advantage for aerospace in particular,” says Lull. “This technology eliminates the risk of failure for bonding or even mechanical fasteners, and we’ve proven out the process to be able to consistently produce thousands of reliable high-quality parts with no scrap.” He adds that this solution enables parts be reliably and effectively evaluated using nondestructive inspection (NDI) methods that are not able to be used on bonded parts.
This solution can also add sustainability benefits: Chemical solvents and adhesives are removed from the process, plus the use of thermoplastic as a joining method enables the two components to be separated at the part’s end of life (EOL) with the addition of heat, increasing the potential for recyclability. “Plus, there is no scrap in the injection process. Any scraps produced can be melted down into and reused in the injection molding process,” adds Lull.
New aircraft is expected to deliver wind turbine blades from 105 meters up to expand the reach of wind energy and achieve global climate goals.
Cevotec, a tank manufacturer, Roth Composite Machinery and Cikoni, have undertaken a comprehensive project to explore and demonstrate the impact of dome reinforcements using FPP technology for composite tanks.
Flat tank enabling standard platform for BEV and FCEV uses thermoplastic and thermoset composites, overwrapped skeleton design in pursuit of 25% more H2 storage.
Arris presents mechanical testing results of an Arris-designed natural fiber thermoplastic composite in comparison to similarly produced glass and carbon fiber-based materials.
Herone, Spiral RTC, Teijin Carbon Europe and Collins Aerospace Almere recycle A350 thermoplastic composite clips/cleats waste into rods for the all-thermoplastic composite Multifunctional Fuselage Demonstrator’s crown.
CompPair and Composite Recycling introduce a roof scoop made of recycled fibers to an eco-efficient rally buggy, which channels airflow to the engine for optimal, sustainable performance.
Dive Technologies started by 3D printing prototypes of its composite autonomous underwater vehicles, but AM became the solution for customizable, toolless production.
Advanced Engineering is the UK’s largest annual gathering of engineering and manufacturing professionals. The event will help you to source new suppliers, network, build connections and learn about the latest industry developments all in one place. Get involved and exhibit alongside 400+ exhibitors offering solutions and products across all industries and sectors to help improve your productivity and inspire creativity. With over 9,000+ of your peers due to attend and ready to network with and inspire you, this is the event you can’t afford to miss!
A report on the demand for hydrogen as an energy source and the role composites might play in the transport and storage of hydrogen.
Thousands of people visit our Supplier Guide every day to source equipment and materials. Get in front of them with a free company profile.
The ITHEC 2024 will take place from the 9 to 10 October 2024 in Bremen, Germany. At the 7th International Conference, more than 300 participants from around the world will be presenting and discussing newest scientific results, meet leading international specialists, share their expertise and start business co-operations in the field of thermoplastic composite technologies. The international exhibition will feature 40+ exhibitors showcasing all steps of the supply-chain. Be it materials, machines, testing, processes, or solutions. By combining the exhibition and the conference ITHEC is further fostering the inter-connectivity between science and industry.
CW’s editors are tracking the latest trends and developments in tooling, from the basics to new developments. This collection, presented by Composites One, features four recent CW stories that detail a range of tooling technologies, processes and materials.
Stephen Heinz, vice president of R&I for Syensqo delivered an inspirational keynote at SAMPE 2024, highlighting the significant role of composite materials in emerging technologies and encouraging broader collaboration within the manufacturing community.
GETTING A QUOTE WITH LK-MOULD IS FREE AND SIMPLE.
FIND MORE OF OUR SERVICES:
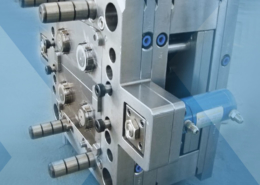
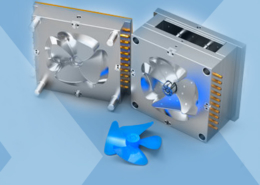
Plastic Molding

Rapid Prototyping
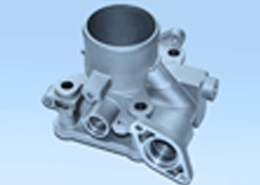
Pressure Die Casting
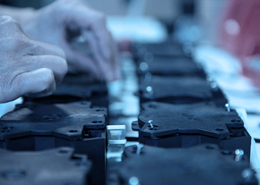
Parts Assembly
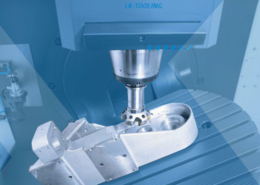