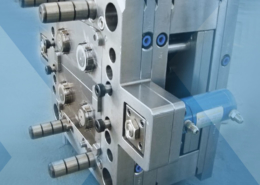
CamdenBoss brings injection moulding in-house, supported by Arburg - custom plas
Author:gly Date: 2024-09-30
“Others have tried unsuccessfully to eliminate the criticality of weld lines in structural parts,” said Lucchetta in a prepared statement. Dynamic packing during the initial phase of the “holding” process allows for improved matrix interdiffusion at the interface and reorientation of the fibers in the direction of flow. However, according to Smart Mold, this typically requires two independent injection molding units. By contrast, GAPP allows for the dynamic packing of weld lines using a single injection unit and miniaturized gas injectors. Moreover, the small size of the gas injectors makes the technology compatible with existing molds, according to the company. “I am convinced that the strength of GAPP technology lies in the ability to implement it in existing molds with noninvasive and inexpensive modifications,” stressed Lucchetta.
The technology can play a key role in advancing the use of recycled plastic in glass-fiber-reinforced compounds, he added.
Different types of materials, including COC and COP, and their applications in producing high-quality and reliable components.
Experimental tests cited by Lucchetta reportedly showed that GAPP can increase weld line strength by 240% in polypropylene reinforced with 35% short-glass fibers, almost reaching the nominal strength of the compound.
Recognize common pain points faced by manufacturers and discuss potential strategies to overcome these challenges, such as reducing production costs, shortening lead times, and ensuring product quality.
Editor in chief of PlasticsToday since 2015, Norbert Sparrow has more than 30 years of editorial experience in business-to-business media. He studied journalism at the Centre Universitaire d'Etudes du Journalisme in Strasbourg, France, where he earned a master's degree.
Weld lines, also called knit lines, are a common problem encountered by injection molders. Beyond aesthetic issues, weld lines can also lead to functional failure. During a press conference at K 2022 in Düsseldorf, Germany, compounder Sirmax Group introduced Gas-Assisted Push-Pull (GAPP) technology, which, it claims, can prevent weld lines in injection molded plastic parts.
GAPP technology can solve weld line strength issues in all parts made of fiber-reinforced thermoplastics that require high mechanical performance, said Smart Mold. Applications include supports, brackets, cooling fans, pulleys, and other structural parts.
Get a detailed look at the various components of pre-filled syringes, including barrels, plungers, and caps, and learn the essential factors to consider during the manufacturing process, such as material selection, mold design, and regulatory compliance.
Are you a medical injection molding professional involved in pre-filled syringe production or seeking to expand your expertise in this rapidly growing market? This webinar will enable you navigate the challenges and opportunities of manufacturing pre-filled syringe components.
Gas-Assisted Push-Pull technology enables dynamic packing of weld lines using a single injection unit and miniaturized injectors.
Weld lines typically appear in a part when an obstruction of some kind separates the melt flow and prevents it from "knitting" together. Weld lines are among the most critical structural defects in parts made by the injection molding of fiber-reinforced thermoplastics, explained Sirmax in a press release. In a weld line, reinforcement fibers adopt an orthogonal orientation with respect to the filling direction, which results in a significant reduction in the strength and rigidity of the molded part. During the presentation at the K, Lucchetta explained how GAPP promotes the interpenetration of weld line flow fronts by changing the shape of the interface, promoting inter-diffusion between flow fronts, and realigning reinforcing fibers.
Hiren Khatri is an industry veteran with over 20 years in the injection molding industry. In these years, Hiren has held several keys roles at Husky, including Service Engineer, Hot runner and Controller Sales, Specialty Closures & Medical Project Sales, Rigid Packaging Beverage Project Sales. Before his current assignment, Hiren was leading Medical and Specialty Closure for Husky and Schoettli’s breakthrough Systems technology. Based at Schoettli India’s Branch in Mumbai as Key Account Manager of Medical System, Hiren is actively involved in all the major SAARC region Medical System projects of the company. Hiren is relentlessly promoting a unique integrated system approach to medical equipment injection molding, which removes artificial boundaries and variability that could exist when assembling components from different suppliers. This integrated system approach enables reducing risk and improving overall manufacturing performance, making Husky and Schoettli the ideal supplier for meeting today’s medical injection molding manufacturing market needs and expectations.
Professor Giovanni Lucchetta of the University of Padua, founder of Smart Mold, a university spin off that developed and patented GAPP, explained the technology at the Sirmax stand. Italy-based Sirmax has a 50% stake in Smart Mold.
GETTING A QUOTE WITH LK-MOULD IS FREE AND SIMPLE.
FIND MORE OF OUR SERVICES:
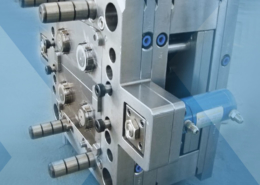
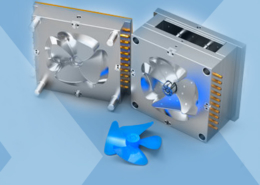
Plastic Molding

Rapid Prototyping
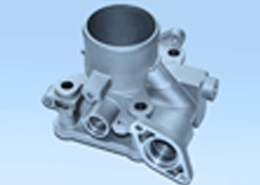
Pressure Die Casting
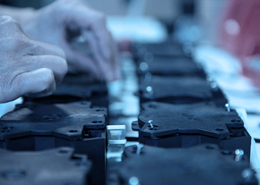
Parts Assembly
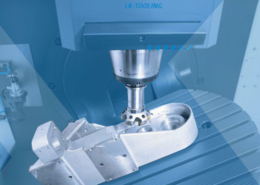