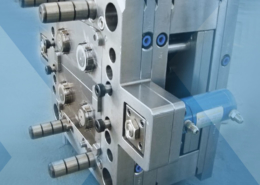
Buy China Wholesale Injection Plastic Parts For Phone Camera Lens Barrel &
Author:gly Date: 2024-09-30
Stephen has been with PlasticsToday and its preceding publications Modern Plastics and Injection Molding since 1992, throughout this time based in the Asia Pacific region, including stints in Japan, Australia, and his current location Singapore. His current beat focuses on automotive. Stephen is an avid folding bicycle rider, often taking his bike on overseas business trips, and is a proud dachshund owner.
Advantage of Low Labour Cost and Mass Production Along with Material Flexibility and Low Production Waste to Drive the Global Injection Moulding Machines Market
Utilizing injection molding machinery permits the actual mass production of injection-molded plastic components. The injection molding machine is the most effective and energy-efficient way of mass-producing plastic products. The rise of the global injection molding machines market is propelled by the multiple qualities of injection molding machines, such as their durability, user-friendliness, higher manufacturing rates and rapid production, and high quality. Rapidly increasing industrial investment and robust demand for injection-molded polymers in the automotive and healthcare industries are driving the expansion of the global injection molding machine market. In addition, industry leaders' manufacturing of energy-efficient, fully automated injection molding equipment stimulates the expansion of the injection molding market. Market participants provide injection molding machines in numerous sizes and designs to meet customers' needs.
Furthermore, its high flow rate (MVR is 14 cm³/10 min. under 5 kg force at 260°C) helps to reduce cycle times, thereby increasing productivity. A further advantage is its very high impact strength (58 kJ/m² at 23°C, 41 kJ/m² at -30°C, according to ISO 180-1A). In addition, significant cost savings are reportedly possible thanks to its improved paintability versus PC/ABS, which leads to a reduced scrap rate.
Increasing production rates and rapid injection molding output are predicted to boost global injection molding machines market growth. In addition, injection molding allows for producing plastic components with various finishes, including light texture, medium texture, pad printed, smooth, and screen printed. Consequently, it is projected that cheap labor costs and mass manufacturing associated with injection molding machines will promote market growth.
Elix Ultra HH4115HI ABS/PC, which was introduced late last year, has several advantages over PC/ABS alloys. These advantages include a 5% lower density (1.07 g/cm³ vs. 1.13 g/cm³), as well as low emissions and odor (VDA 278 VOC = 8 / FOG = 3 ppm, VDA 270 = 3.0).
March 12, 2024 10:35 ET | Source: Straits Research Private Limited - Reed Intelligence Straits Research Private Limited - Reed Intelligence
Elix Ultra HH4115HI has been tested and approved at several automotive OEMs. Among them, Audi noted its low emissions and odor and considers the material to be very interesting for lower instrument panel parts, center console parts, and door panel parts according to its TL 52231 specification. BMW has approved it under its GS 93016 specification, and some initial serial projects are now running. GM has approved Ultra HH4115HI under GMW 15572-T4, and Daimler has approved it under DBL 5404 AA83.
Elix Polymers foresees a wide range of applications for this innovative material, including door panel parts, instrument panel parts, center console trim, seat parts, luggage compartment trim, and both interior and exterior pillar covers. As with other grades from Elix Polymers, materials pre-colored to OEM specifications are possible, in addition to tailor-made solutions with special additive packages for very demanding part and environmental requirements.
Whether you are looking at business sectors in the next town or crosswise over continents, we understand the significance of being acquainted with the client’s purchase. We overcome our clients’ issues by recognizing and deciphering the target group and generating leads with utmost precision. We seek to collaborate with our clients to deliver a broad spectrum of results through a blend of market and business research approaches.
According to Straits Research, “The global injection molding machines market size had a market share of USD 10,724 million in 2021, expected to advance to USD 16,964 million with a CAGR of 5.9% during the forecast period.” Injection molding is an automated process in which an automatic tool operates efficiently on an injection molding machine. Machines and robots perform the majority of injection molding. These persons are solely accountable for overseeing and managing the process. This automation reduces the labor costs of the process. This drop in labor expenditure is predicted to reduce the cost of manufacturing plastic components. In addition, injection molding can make many identical components every hour.
Asia-Pacific's injection molding machines market share will grow at a CAGR of 6.3% during the forecast period. Due to the region's expanding demand for injection-molded plastics, it is projected that China, India, and Indonesia will contribute to expanding the Asia-Pacific injection molding machine market. This is due to the expansion of the packaging industry. In addition, significant companies such as NISSEI Plastic Industrial Co. Ltd. and Japan Steel Works Ltd. are employing various strategies, such as cooperation, acquisition, and others, to accelerate the expansion of the market.
A leading supplier of interior and exterior automotive parts has selected a new ABS/polycarbonate blend from Elix Polymers for the production of exterior pillar covers to be used in an upcoming, premium class car from a well-known German manufacturer.
Europe will hold the second largest market share and is expected to grow at a CAGR of 4.9% during the forecast period. Due to their high quality and energy efficiency, there has been a surge in the usage of all-electric injection molding machines in Europe. In addition, major market participants are spending considerable effort to deliver injection molding machines that fulfill the requirements of their clients by supplying customized and machine-type-based machines. Europe's economic expansion has led to a larger consumer market, indirectly benefiting the injection-molded plastics industry. In addition, the growth of the packaging, automotive, and electrical appliance industries is expected to increase the need for injection-molded plastics, boosting the market for injection molding equipment in Europe.
New York, United States, March 12, 2024 (GLOBE NEWSWIRE) -- Injection molding is a mechanism that allows for the mass production of components. It operates by injecting molten materials into a mold. It is typically employed in mass production to manufacture thousands of similar things. Components produced by injection molding include metals, glassware, elastomers, and confections. Although thermoplastic and thermosetting polymers are the most common, other polymers exist. The real benefit of injection molding is its mass manufacturing capability. After initial costs are accounted for, the unit cost of injection-molded items is extraordinarily cheap. The ingredients, such as synthetic resins (plastics), are heated and melted before they are put into the mold and cooled to form the desired shape. This process is referred to as injection molding because it resembles the injection of fluids using a syringe. Materials are melted and poured into the mold, where they solidify before being removed and completed.
Puncture impact behavior tests carried out according to ISO 6603-2 confirm the very good performance of Elix Ultra HH4115HI at different temperatures for crash-relevant parts, such as the exterior pillar covers produced by Maier, and also for interior trim and parts that may be subject to knee or head impacts. The appearance and structure of fractures caused in tests has been evaluated very positively by several premium car manufacturers.
The central pillar cover is a technically highly demanding component that forms part of a complex assembly with other components. Elix Ultra HH 4115 HI was chosen in particular for its high strength and temperature resistance, and for its low density. The technical departments of Maier and Elix Polymers worked intensively together to find the best possible solution and optimize the injection conditions of the parts (one on each side of the car).
Maier S. Coop., based in Vizcaya, Spain, is using Elix Ultra HH4115HI in a two-component part that combines an acrylonitrile-butadiene-styrene/polycarbonate (ABS/PC) alloy with a polymethylmethacrylate (PMMA) resin.
Straits Research is a market intelligence company providing global business information reports and services. Our exclusive blend of quantitative forecasting and trends analysis provides forward-looking insight for thousands of decision-makers. Straits Research Pvt. Ltd. provides actionable market research data, especially designed and presented for decision making and ROI.
A vital characteristic of the injection-molding process is its capacity to use many types of plastic to make plastic things simultaneously. Manufacturers may use thermoplastics, thermosetting, or a combination of elastomers in injection molding to get the needed properties. This technique allows for producing more complicated objects with various forms and motifs. In addition, once the mold is prepared, the manufacturer can adjust the component's material and color. This factor is projected to drive the global market for injection molding machines. In addition, injection molding helps to reduce manufacturing waste. The majority of polymers produced by injection molding are recyclable.
GETTING A QUOTE WITH LK-MOULD IS FREE AND SIMPLE.
FIND MORE OF OUR SERVICES:
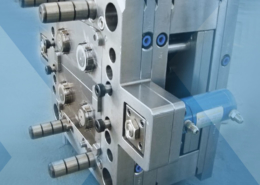
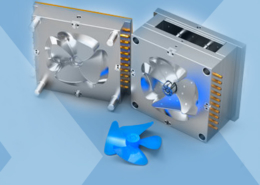
Plastic Molding

Rapid Prototyping
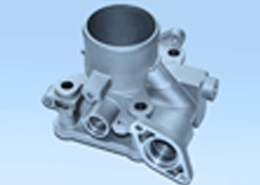
Pressure Die Casting
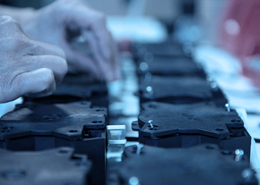
Parts Assembly
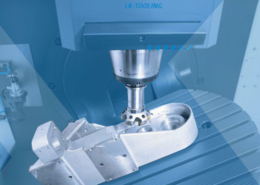