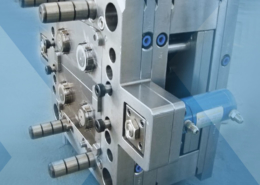
Bubbly Breakthrough: New Plastic Food Tray Loses the Weight - injection tray pla
Author:gly Date: 2024-09-30
Aside from performance advantages, injection moulding machines must also be easy to use. This guarantees Lotan’s team can stay on-track to meet their key performance indicators (KPIs) by controlling the equipment and keeping it running sustainably. That’s why SXIII range of injection moulding machines are equipped with Shibaura Machine’s user-friendly controller that connects to Lotan’s programmable logic controller (PLC) for simple, repeatable operations.
In another instance, another EC-SX model, the 1,800 ton EC1800SX-155B, was tested against a competing all-electric IMM. Although both machines had the same energy consumption, the Shibaura Machine IMM delivered a faster cycle time, which gave overall energy efficiency savings of 30%.
Get a detailed analysis on regions, market segments, customer landscape, and companies - Click for the snapshot of this report
Injection molding machines are mechanical systems used in manufacturing industries to produce plastic products in mass volume. With the increasing global population and the demand for plastic products in various sectors, the market for injection molding machines continues to grow. These machines are essential in producing components for industries such as automobiles, electronics, medicines, and packaging solutions. The versatility of injection molding machines makes them suitable for specific requirements, including labor-intensive industries like automotive hubs. The production rate of injection molding machines is a critical factor, with high-efficiency, fully automatic, and all-electric machines being highly sought after. However, wastage remains a concern, and efforts are being made to improve energy efficiency and reduce it. Plastics, a key raw material, are used extensively in various sectors, including food and beverages, vehicles per 1000 people, and industrialization. Supportive government initiatives and the rise in population have led to an increase in demand for injection molding machines. The market is also driven by urgent emergencies, such as the need for medical components and the shift towards electric vehicles. Injection molding manufacturers are continuously innovating, introducing machines with advanced features like servo pumps, monitoring systems, and hybrid machines to meet the evolving needs of various industries. The injection molding market is influenced by various factors, including the economy, finance, staff, supply networks, and urgent emergencies. The market is expected to grow further with the introduction of robotics and advancements in medical equipment and energy efficiency. The IntElect S 100/460-250 is an example of a high-performance injection molding machine that meets the specific needs of various industries. Overall, injection molding machines play a crucial role in the production of plastic components and packaging solutions for various sectors, contributing to the betterment of human health condition, community, and global trade.
The global Plastic Processing Machinery Market is experiencing robust growth, driven by increasing demand for plastic products across various industries. Key players are focusing on innovative technologies to enhance efficiency and reduce environmental impact. Similarly, the global Dies and Molds Market is expanding due to rising automotive and consumer goods manufacturing. Advanced mold technologies are improving production quality and speed. Meanwhile, the global Machine Condition Monitoring Market is growing as industries prioritize predictive maintenance to reduce downtime and maintenance costs, leveraging IoT and AI for real-time monitoring and analytics.
Injection moulding might presently be responsible of up to 90% of the processes GWP. However, the performance of all-electric IMMs like Shibaura Machine’s SXIII and EC-SX show this trend can be reversed, with positive effects on sustainability and also manufacturers’ bottom line.
The company relies on Shibaura Machine’s all-electric injection moulding machines (IMM) supplied by TM Robotics. The machine is manufactured in-house by Shibaura Machine, formerly known as Toshiba Machine. Performance benefits of the IMM include a range of clamping force from 50 to 2,500 tons, which can be calibrated by a digital direct screw transfer (DST) control for added production flexibility.
With over 500 specialized analysts, Technavio's report library consists of more than 17,000 reports and counting, covering 800 technologies, spanning across 50 countries. Their client base consists of enterprises of all sizes, including more than 100 Fortune 500 companies. This growing client base relies on Technavio's comprehensive coverage, extensive research, and actionable market insights to identify opportunities in existing and potential markets and assess their competitive positions within changing market scenarios.
NEW YORK, July 25, 2024 /PRNewswire/ -- The global injection molding machine market size is estimated to grow by USD 5.19 billion from 2024-2028, according to Technavio. The market is estimated to grow at a CAGR of 4.36% during the forecast period. Rising demand for injection molding machines from various industries is driving market growth, with a trend towards growing popularity of 3D printing. However, high initial and maintenance cost of injection molding machines poses a challenge. Key market players include ARBURG GmbH Co KG, BORCHE North America INC., Chen Hsong Holdings Ltd., Cosmos Machinery Enterprises Ltd., Electronica Plastic Machines Ltd., ENGEL Austria GmbH, FANUC Corp., Haitian International Holdings Ltd., Hillenbrand Inc., Husky Technologies, KraussMaffei Group GmbH, L.K. Technology Holdings Ltd., NISSEI PLASTIC INDUSTRIAL Co. Ltd., Shibaura Machine Co. Ltd., Sumitomo Heavy Industries Ltd., Tederic Machinery Co., Ltd., The Japan Steel Works Ltd., Toyo Machinery and Metal Co. Ltd., Ube Corp., and WITTMANN Technology GmbH.
The Injection Molding Machine market is driven by the mass production of plastic products, particularly in industries such as automobiles, electronics, medicines, and processed food & beverages. With a global population projected to reach 9 billion by 2050, the demand for plastic items is expected to increase significantly. Injection molding machines offer versatility in producing specific requirements for various industries. However, labor costs and production rate are critical factors in the market. Wastage is a concern due to the high volume of plastic production. Plastics are essential in manufacturing industries, with an average of 100 vehicles produced per 1000 people, requiring injection molding for interior and exterior parts. The economy, supply networks, and urgent emergencies also impact the market. Injection molding manufacturers must adapt to specific requirements, such as electric vehicles and electric machine components, to remain competitive. Staffing and efficient supply chains are crucial to maintaining production rates and meeting demand.
Technavio ResearchJesse MaidaMedia & Marketing ExecutiveUS: +1 844 364 1100UK: +44 203 893 3200Email: [email protected]Website: www.technavio.com/
7 Customer Landscape8 Geographic Landscape9 Drivers, Challenges, and Trends10 Company Landscape11 Company Analysis12 Appendix
Injection moulding is used to manufacture a huge variety of parts, and has several advantages. They include the ability to mould a wide variety of plastics, good repeatability, consistently high production with low waste and a low-cost-per-part — the latter is always a priority.
The Journal of Clean Production’s findings are a wake-up call to manufacturers, particularly as demand for injection moulding processes continue to grow. For example, the market for injection moulded medical devices plastics is expected to see booming growth between 2023 and 2030.
Type (Plastics, Rubber, and Others), End-user(Automotive, Consumer goods, Packaging, andOthers), and Geography (APAC, North America,Europe, South America, and Middle East and Africa)
Indeed, Shibaura Machine’s all-electric IMMs have been found to yield energy savings of 60% compared with European hydraulic servo IMMs. Other performance tests by Shibaura Machine measured its EC650SX-61B IMM, with a clamping force of 650 tons, against a hydraulic servo machine. It delivered a 51% energy reduction.
Injection moulding machines powered by a hydraulic motor can produce higher energy levels and higher injection pressures, and the initial cost of the machine is lower. But there are also disadvantages with hydraulic machines. They include the machine’s high consumption of electric energy, because its hydraulic power is connected to an electric power unit that works at maximum capacity during every phase of the moulding process.
Here, Dervish Ibrahim, international sales manager at TM Robotics, explains why all-electric injection moulding machines are the way forward for reducing the process’s environmental impact — while also helping manufacturers achieve a lower cost-per-part.
1.1 Plastics- Injection molding machines are essential equipment in the manufacturing industry for producing a diverse range of plastic parts and components. Four primary types of plastics, namely polypropylene (PP), polyethylene (PE), polystyrene (PS), and acrylonitrile-butadiene-styrene (ABS), dominate the injection molding market. Polypropylene (PP), a thermoplastic polymer, is widely utilized in automotive, packaging, and medical industries due to its high melting point, good chemical resistance, and overall toughness. Lightweight and easy to mold, PP is an ideal choice for producing caps, covers, and automotive components. Polyethylene (PE), another commonly used plastic, is popular in packaging and consumer goods industries. PE is known for its durability, flexibility, and resistance to moisture and chemicals. High-density polyethylene (HDPE) and low-density polyethylene (LDPE) are two main grades, each suitable for different applications. HDPE is used for rigid and durable products, while LDPE is used for more flexible and lightweight applications. Polystyrene (PS), a transparent thermoplastic polymer, is utilized in various consumer goods, packaging, and electronic applications. Known for its excellent dimensional stability and electrical insulation properties, PS is available in crystal and high-impact forms. Crystal PS is used where clarity and transparency are essential, such as food packaging and medical products. High-impact PS, which contains rubber or another elastomer, is used for more durable and impact-resistant applications like toys, automotive components, and electronics. ABS, a thermoplastic polymer, is a versatile material used in automotive parts, toys, electronics, and sporting goods. ABS offers a balance of mechanical, chemical, and thermal properties, making it a popular choice for its high-impact resistance, easy processability, and low cost. Additionally, it is available in various colors and finishes, making it an attractive option for consumer products. These factors contribute to the growth of the plastic segment in the global injection molding machine market during the forecast period.
Although hydraulic injection moulding machines are less expensive initially, it’s important to consider the whole life cost when buying new machines. This was demonstrated by TM Robotics’ customer Lotan, a manufacturer of plastic containers based in Leicestershire, UK. All of the injection moulding machines in Lotan’s production facility are electric, rather than hydraulic.
All-electric moulding machines also have the edge when it comes to maintenance. With PLC controllability, injection moulding operations can be tie-into the production facilities Internet of Things (IoT) things systems. Data on the IMM’s performance can be collected through sensors and relaid to the plant’s enterprise resource planning (ERP) or manufacturing execution systems (MES) to support preventive maintenance, traceability and quality management.
The Injection Molding Machine market is experiencing significant growth due to the increased demand for plastic products in various sectors. Mechanical systems in manufacturing industries are leveraging injection molding machines to produce mass volumes of plastic components for industries like automobiles, electronics, and medical. With the global population on the rise, the need for efficient and versatile production solutions is increasing. Injection molding machines are being used to produce plastic components for medicines, automotive hubs, packaging solutions, and even food & beverages. The market is driven by the economy, with finance and global trade playing crucial roles. The automotive industry, for instance, produces around 1,000 vehicles per 1,000 people, and injection molding machines are essential for manufacturing plastic components. The trend towards fully automatic, highly efficient all-electric machines is gaining popularity due to their lower labor costs and higher production rates. However, wastage remains a concern, and injection molding machine manufacturers are focusing on improving efficiency and reducing wastage. Supportive government initiatives and the rise in population are creating opportunities for injection molding machines in various sectors, including medical equipment and robotics. The market is also witnessing a trend towards specific requirements, such as the need for high clamping forces in the food & beverage industry to produce thick-walled containers. In urgent emergencies, injection molding machines can quickly produce essential plastic components, making them indispensable. The IntElect S 100/460-250 is a popular injection molding machine due to its versatility and ability to meet various industry requirements. Overall, the injection molding machine market is a vital part of the community, contributing to human health conditions, industrialization, and the global economy.
But, what about the energy efficiency of all-electric versions hydraulically-powered machines? By using Shibaura Machine’s all-electric IMMs, Lotan has experienced 20 to 40% lower running costs compared with older-fashioned hydraulic machine. Traditional hydraulic injection moulding machines are also less efficient because they consume energy even while idle, whereas all-electric injecting machines only use energy while in action.
ARBURG GmbH Co KG, BORCHE North America INC., Chen Hsong Holdings Ltd., Cosmos Machinery Enterprises Ltd., Electronica Plastic Machines Ltd., ENGEL Austria GmbH, FANUC Corp., Haitian International Holdings Ltd., Hillenbrand Inc., Husky Technologies, KraussMaffei Group GmbH, L.K. Technology Holdings Ltd., NISSEI PLASTIC INDUSTRIAL Co. Ltd., Shibaura Machine Co. Ltd., Sumitomo Heavy Industries Ltd., Tederic Machinery Co., Ltd., The Japan Steel Works Ltd., Toyo Machinery and Metal Co. Ltd., Ube Corp., and WITTMANN Technology GmbH
Get a detailed analysis on regions, market segments, customer landscape, and companies - Click for the snapshot of this report
More than 90% of the costs of injection moulding can be attributed to energy use. This mainly applies to the electricity used to power and operate the injection moulding machine. As a result, there has been some debate in industry about the cost and sustainability advantages of hydraulic injection moulding versus all-electric machines.
Technavio is a leading global technology research and advisory company. Their research and analysis focuses on emerging market trends and provides actionable insights to help businesses identify market opportunities and develop effective strategies to optimize their market positions.
Report with the AI impact on market trends - The Global Electric Vehicle Remote Diagnostics Market size is estimated to grow by USD 4.10 billion from ...
Maintaining a low cost-per-part throughout the manufacturing process is vital for reducing costs and delivering a higher product value — from both the manufacturer’s and the customer’s perspective. While injection moulding can support this, manufacturers are also concerned about the energy costs of injection moulding, and how this effects sustainability and the bottom line.
Injection molding machines have gained significant traction in the manufacturing industry due to their versatility and capability to work with various plastic and metal materials. The increasing popularity of 3D printing has led to an increased demand for these machines, as they enable the creation of complex geometries in one piece, saving time and reducing material waste. While 3D printing offers quick production of parts, injection molding machines allow for the mass production of high-quality, precise, and consistent parts. The ability to easily create prototypes using injection molding machines also facilitates the rapid design and development process. These advantages are expected to fuel the growth of the global injection molding machine market in the coming years.
Report on how AI is driving market transformation - The Global Municipal Water and Wastewater Treatment Equipment Market size is estimated to grow by ...
Although all-electric machines are initially more expensive with lower injection pressures, they are shown to outperform hydraulic versions in a variety of other ways. Advantages include higher rates and speeds of injection because the all-electric machining relies on toggle clamping rather than direct pressure clamping, which is better for high-speed injection moulding.
Further advantages include improved dry cycle times and the overall stability of the mould itself. Lotan has ordered several more Shibaura Machine IMMs from TM Robotics, specifically its newest SXIII range of injection moulding machines. The SXIII is an enhanced performance model that provides significantly faster injection speeds than traditional moulding equipment. As a result, the machine offers a 35% faster cycle time than conventional hydraulic servo IMMs. Lotan also achieved a lower cost-per-mould.
According to the Journal of Clean Production, injection moulding may be responsible of up to 90% of the Global Warming Potential (GWP) created by the entire mould lifecycle, mainly caused by energy consumption.
For more information on market segmentation with geographical analysis including forecast (2024-2028) and historic data (2018 - 2022) - Download a Sample Report
GETTING A QUOTE WITH LK-MOULD IS FREE AND SIMPLE.
FIND MORE OF OUR SERVICES:
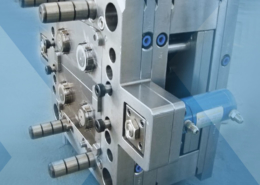
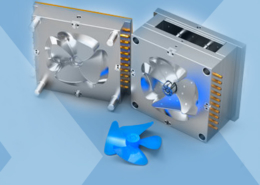
Plastic Molding

Rapid Prototyping
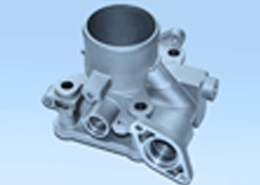
Pressure Die Casting
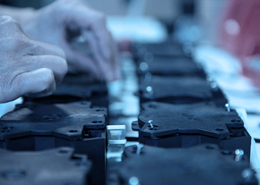
Parts Assembly
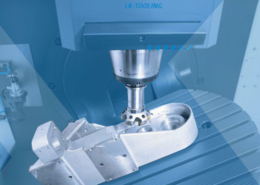