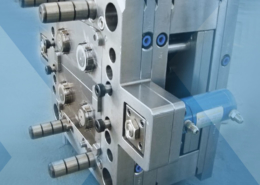
Brick battle: LEGO looking to replace ABS material for sustainable
Author:gly Date: 2024-09-30
Across the show, sustainability ruled in new materials technology, from polyolefins and engineering resins to biobased materials.
Multiple speakers at Molding 2023 will address the ways simulation can impact material substitution decisions, process profitability and simplification of mold design.
Formnext Chicago is an industrial additive manufacturing expo taking place April 8-10, 2025 at McCormick Place in Chicago, Illinois. Formnext Chicago is the second in a series of Formnext events in the U.S. being produced by Mesago Messe Frankfurt, AMT – The Association For Manufacturing Technology, and Gardner Business Media (our publisher).
While prices moved up for three of the five commodity resins, there was potential for a flat trajectory for the rest of the third quarter.
Two decades ago, a $30 million custom molding company was considered a top business. Today, as a result of mergers, acquisitions, and growth that has outpaced the national average, a company that size is considered small. So although an individual can set up a small injection molding operation for less than $1 million, unless the company has a special capability to offer or establishes a sound financial relationship with one or two customers, chances for success are slight.
Second quarter started with price hikes in PE and the four volume engineering resins, but relatively stable pricing was largely expected by the quarter’s end.
The Molding Machine: Cost Justification More than just a purchase, an injection molding machine is an investment. As with any investment, you want to know what your return will be. What value will the machine contribute to your overall operation? Where will your break-even point be? Will the machine pay for itself in a year? Two years?
In this collection of articles, two of the industry’s foremost authorities on screw design — Jim Frankand and Mark Spalding — offer their sage advice on screw design...what works, what doesn’t, and what to look for when things start going wrong.
Mike Sepe has authored more than 25 ANTEC papers and more than 250 articles illustrating the importance of this interdisciplanary approach. In this collection, we present some of his best work during the years he has been contributing for Plastics Technology Magazine.
Sustainability continues to dominate new additives technology, but upping performance is also evident. Most of the new additives have been targeted to commodity resins and particularly polyolefins.
Selecting the Best Equipment Presses with up to 100 tons of clamping force, which mold small parts, constitute the second largest group of presses used by molders in the United States. The majority of molders operate with presses in the 100-ton to 350-ton range. Presses in the 350-ton to 750-ton range represent the third largest group. Most injection molders enter the business with small to midsized molding presses.
Warehousing: A Hidden Requirement You will need space for storage of molds not in use, bags and gaylords of material, the finished-goods inventory customers most likely will request be held, and other equipment. Typically, molders use an average of 10 percent of their total floor space for warehousing. This will vary depending on the size of your molded parts, how many different materials must be kept on hand, and the size of the molds to be stored.
Join Wittmann for an engaging webinar on the transformative impact of manufacturing execution systems (MES) in the plastic injection molding industry. Discover how MES enhances production efficiency, quality control and real-time monitoring while also reducing downtime. It will explore the integration of MES with existing systems, emphasizing compliance and traceability for automotive and medical sectors. Learn about the latest advancements in IoT and AI technologies and how they drive innovation and continuous improvement in MES. Agenda: Overview of MES benefits What is MES? Definition, role and brief history Historical perspective and evolution Longevity and analytics Connectivity: importance, standards and integration Advantages of MES: efficiency, real-time data, traceability and cost savings Emerging technologies: IoT and AI in MES
Gifted with extraordinary technical know how and an authoritative yet plain English writing style, in this collection of articles Fattori offers his insights on a variety of molding-related topics that are bound to make your days on the production floor go a little bit better.
Exhibitors and presenters at the plastics show emphasized 3D printing as a complement and aid to more traditional production processes.
Customizable, the shot-size range for the IRM will be the same as current, standard injection molding machines, with the L/D ratio for the screw ranging anywhere from 24 to 36 and the screw’s diameter determined by the overall rate requirements for the system. The injection speed and pressure possible from the plunger are determined by the process’s pack-and-hold requirements.
Introduced by Zeiger and Spark Industries at the PTXPO, the nozzle is designed for maximum heat transfer and uniformity with a continuous taper for self cleaning.
While prices moved up for three of the five commodity resins, there was potential for a flat trajectory for the rest of the third quarter.
The IRM, in contrast, has a small diameter, hydraulically controlled plunger that can accurately control pack and hold, thereby enabling molders to create parts with the desired shot weight. As an example of the potential waste caused by overpacking, Dray offers up a trial completed by a cap molder applying the new system. Using a 65-mm screw and valve of R. Dray’s design, the customer saved an average of 0.04 g of material per bottle cap. When you consider that this company molds 14 billion bottle caps annually, those resin savings equate to 1,234,589 lbs of raw material saved per year. Assuming a resin price of 60 cents/lb, potential annual savings come out to $740,753 per year.
In addition, entering custom injection molding with two or three presses and minimal capabilities means entering a highly competitive market already crowded at the low end with several thousand molders. Because many of these molders, with sales less than $1 million annually, offer little in the way of secondary services, they compete on the basis of price. This results in thin margins and a low survival rate.
Join Engel in exploring the future of battery molding technology. Discover advancements in thermoplastic composites for battery housings, innovative automation solutions and the latest in large-tonnage equipment designed for e-mobility — all with a focus on cost-efficient solutions. Agenda: Learn about cutting-edge thermoplastic composites for durable, sustainable and cost-efficient battery housings Explore advanced automation concepts for efficient and scalable production See the latest large-tonnage equipment and technology innovations for e-mobility solutions
Dray is currently seeking U.S. and global patents on a system he’s dubbed the injection regrind machine (IRM), which borrows from a concept long deployed in extrusion. Namely, the use of a “shot pot” or secondary screw and barrel designed to melt up to 100% regrind material in a two-stage process. Instead of a standard reciprocating screw within a barrel preparing and injection melt, the IRM features the shot pot with a plunger.
Resin drying is a crucial, but often-misunderstood area. This collection includes details on why and what you need to dry, how to specify a dryer, and best practices.
Today, more than ever, granulation is an important step in the total production process. Our expert explains a few of the many common traps to avoid when thinking about granulators
Core Technology Molding turned to Mold-Masters E-Multi auxiliary injection unit to help it win a job and dramatically change its process.
Hundreds of tons of demonstration products will be created this week. Commercial Plastics Recycling is striving to recycle ALL of it.
Injection molding auxiliary equipmentThe central material drying/handling system, including five insulated drying hoppers, dehumidifying dryer, pumps, filters, and conveying system would cost about $115,000. Beyond that, at right are typical prices for other auxiliary equipment.
Two barrels could be better than one when it comes to running regrind material, according to screw design expert Robert Dray of the eponymous R. Dray Mfg. Inc., Dallas, Texas.
In addition to being able to run lots consisting of 100% regrind, with no theoretical limitation on shot size, Dray says the IRM would also enable injection molders to process finished parts at a lower price and higher quality, including the possibility of blending in off-spec material. Dray also estimates that by cutting out the compounding step and eliminating pelletizing, approximately 30 cents/lb savings can be achieved. Not currently partnering with any machinery OEMs, R. Dray is currently licensing the technology and customizing orders based on what the molder has on hand, including building extruders to spec to add to the press and turn it into a shot-pot IRM machine.
“We’ve been doing it in extrusion for 20 years,” Dray explains. “It’s really not new in extrusion, but it is new in injection molding.” Dray says that for the past 25 years, extruders have used his company’s patented screw designs for extruding 100% flake regrind into mostly sheet.
While many molding companies have rushed to implement the latest and greatest with regard to quality standards, others balk at the idea of so much money spent without the assurance that a particular level of quality is actually needed. In some ways, too, these so-called levels have made the playing field more uneven and are knocking smaller molding shops out of competition.
If you were starting a new facility, it would be unlikely you'd pay this list price for any of this equipment. If you are molding a highly sophisticated product mix, these prices might be low. They also don't represent the prices of the most basic imported molding machine, either. But these prices at least offer a glimpse at what a good starting point might be.
Join this webinar to explore the transformative benefits of retrofitting your existing injection molding machines (IMMs). Engel will guide you through upgrading your equipment to enhance monitoring, control and adaptability — all while integrating digital technologies. You'll learn about the latest trends in IMM retrofitting (including Euromap interfaces and plasticizing retrofits) and discover how to future-proof your machines for a competitive edge. With insights from industry experts, it'll walk you through the decision-making process, ensuring you make informed choices that drive your business forward. Agenda: Maximize the value of your current IMMs through strategic retrofitting Learn how to integrate digital technologies to enhance monitoring and control Explore the benefits of Euromap interfaces and plasticizing retrofits Understand how retrofitting can help meet new product demands and improve adaptability Discover how Engel can support your retrofitting needs, from free consultations to execution
Thousands of people visit our Supplier Guide every day to source equipment and materials. Get in front of them with a free company profile.
While the major correction in PP prices was finally underway, generally stable pricing was anticipated for the other four commodity resins.
Generally, space for secondary operations is designed in one of two ways—either as a separate area or room designated for such activities, or beside the press. The choice depends on the types of secondary operations to be performed and the space available. Some molders prefer to do secondary operations alongside the press after each cycle in order to minimize handling and maximize operator time. This can also increase efficiency in that parts don't have to be boxed, moved, unpacked for the secondary operation, and then repacked. Less handling is also easier on the parts and results in lower scrap rates—another important consideration. This requires that all operations be considered together and set up in cells, usually dedicated to a single product or assembly, sometimes with multiple parts.
For example, disposable medical components such as injection syringes are manufactured and used in the millions daily. However, the return from each one of these devices is in the tenths of a cent. Quality and manufacturing requirements are extremely stringent, and the parts generally are made from clear or clear-tinted material, which compounds the difficulty of molding. In order to make a profit, molders who choose this type of high-volume medical work must find ways to keep manufacturing costs at a minimum and efficiency high.
In recent years central material handling systems have grown in popularity. Such systems locate resin, dryers, hoppers, and blenders in one place, often in a basement below the presses, or on a mezzanine above the presses. Vacuum pumps and small pneumatic loaders at each machine move resin from the centrally located hoppers to the press via a network of tubing. Such a setup keeps bulky gaylords and dryers out of the way, allows machines to be spaced closer together on the floor, and makes material handling simpler as all resin can be managed from one location. A central system is more expensive to buy and install, but is usually more efficient in the long run.
IMM made some big assumptions and got ballpark figures from a few manufacturers who were willing to share their cost data. The tables below list some basic prices for injection molding machines and auxiliary equipment. For the purposes of this list, we assumed this 15-press facility would orient the machines in two side-by-side rows on 15-ft centers. We also decided that material handling would be central, designed to accommodate five different resins, each used in equal amounts, each with an average drying time of 3 hours. Hypothetical average cycle time would be 60 seconds at maximum shot capacity for all machines, which would consume 562 lb/hr of resin. Material would be pulled from gaylords, dried centrally, and delivered to each machine via machine-mounted vacuum receivers.
As an employer, you will also quickly discover what many molders know already: In 2001, finding and keeping reliable production employees is very difficult. The competitive job market is a significant challenge for many molders. One way to combat this problem is to rely more on robotics and automation to perform the tasks that might otherwise be done manually. Robots can be used to pull parts from the mold, remove sprues, and do some assembly work. Most robot systems mount on top of the press and by themselves may not affect plant layout. But you may elect to use conveyors or other parts handling equipment press-side in conjunction with robots. Make sure to allow enough space to accommodate such equipment.
The IRM patent enables the small plunger to control pack and hold, which can compensate for material shrinkage in the mold. “That is why our small diameter plunger still provides the required pressure,” Dray says. In the IRM’s design, a smaller plunger, which is controlled hydraulically to manage pack and hold, rests inside a larger plunger.
As far as molders and quality are concerned, size doesn't necessarily mean that a company is better. A large company or plant can be run poorly and have low productivity with below-average profits or ROI. A small plant can be well run and have high productivity and good profits. It's generally known, however, that all molders, whether they have $100 million or $1 million in production or sales, fight the same battles—only the scale is different. The bigger the company, the bigger the problems.
Machinery manufacturers say that molders use a variety of criteria when looking at a cost-justification evaluation. Some base their decision purely on the lowest price, without taking into consideration the "cost" of the machine. Price is what you pay for the machine now. Cost is what you will pay for the machine long-term, including such things as energy use and maintenance.
Finally, it's usually not enough to just mold parts anymore, package them in a box, and send them to the customer, traditionally called "shoot and ship." Many manufacturers go to molders now looking for design and engineering services, tooling assistance, and postmold decoration and assembly expertise. Captive molders, as well, are more likely to have several secondary functions integrated with the molding of the basic parts.
Speaking more on process pressure, Dray says that in most cases the IRM has the same levels as standard injection molding. Where it differs, however, is it will not lead to overpacking of parts, which wastes material. Dray says overpacking is often the result of the large screws currently standard on OEM machines, which he says cannot properly control the pack-and-hold phase of the injection molding process.
Ultradent's entry of its Umbrella cheek retractor took home the awards for Technical Sophistication and Achievement in Economics and Efficiency at PTXPO.
Plastics Technology’s Tech Days is back! Every Tuesday in October, a series of five online presentations will be given by industry supplier around the following topics: Injection Molding — New Technologies, Efficiencies Film Extrusion — New Technologies, Efficiencies Upstream/Downstream Operations Injection Molding — Sustainability Extrusion — Compounding Coming out of NPE2024, PT identified a variety of topics, technologies and trends that are driving and shaping the evolution of plastic products manufacturing — from recycling/recyclability and energy optimization to AI-based process control and automation implementation. PT Tech Days is designed to provide a robust, curated, accessible platform through which plastics professionals can explore these trends, have direct access to subject-matter experts and develop strategies for applying solutions in their operations.
You must also determine what services you will offer, and what equipment will be needed to supply such capabilities. For example, even if you decide not to have a moldmaking facility in-house, you will need a certain amount of equipment for mold maintenance and repair. Will you do any type of secondary operations? If so, what type of equipment will that require? See the box above for a list of equipment in a 15-machine shop. Equipment costs are shown below.
In this three-part collection, veteran molder and moldmaker Jim Fattori brings to bear his 40+ years of on-the-job experience and provides molders his “from the trenches” perspective on on the why, where and how of venting injection molds. Take the trial-and-error out of the molding venting process.
How a facility is set up and attendant decisions depend on the type of markets you are serving, the type of parts you need to mold, and what your customers (internal or external) dictate you have. Right at the start, also consider future expansion, either of the plant itself or of production floor space. While a 10,000-sq-ft facility might seem enormous when it's empty, it can become crowded when 10 presses and auxiliary equipment are installed. A rule of thumb is to lease or purchase a building twice the size you figure you'll need to start.
Discover how artifical intelligence is revolutionizing plastics processing. Hear from industry experts on the future impact of AI on your operations and envision a fully interconnected plant.
In this collection, which is part one of a series representing some of John’s finest work, we present you with five articles that we think you will refer to time and again as you look to solve problems, cut cycle times and improve the quality of the parts you mold.
Say “manufacturing automation” and thoughts immediately go to the shop floor and specialized production equipment, robotics and material handling systems. But there is another realm of possible automation — the front office.
Some molders prefer lower-volume parts molded for high-dollar products, which tend to offer better profit margins. For example, the box that houses the instrumentation monitoring an IV drip must meet tough cosmetic standards, and it's only produced in quantities of 100,000 a year. Others prefer to mold component parts such as gears that remain out of sight, which means that although fit and function still are critical, cosmetic requirements are less stringent.
If material handling will be done manually, that is, by using forklifts to convey gaylords, or 1000-lb containers of resin, to presses, then adequate space must be allowed to accommodate the forklifts. If pneumatic conveying systems are to be used, then you might consider an enclosed material-storage aisle between the rows of presses, which keeps bags and gaylords of material out of sight yet handy to the presses.
The aim of this presentation is to guide you through the factors and the numbers that will help you determine if a robot is a smart investment for your application. Agenda: Why are you considering automation? What problems are you trying to solve? How and why automation can help Crunch the numbers and determine the ROI
The following is an edited excerpt from The Business of Injection Molding, by Clare Goldsberry. The book is the first title in the IMM Book Club Injection Molding Management Series, published by IMM. While much of the focus in the book is on a custom injection molding operation, many of the points about plant layout, machinery and equipment required, and staffing apply to captive molding operations as well.
Mold maintenance is critical, and with this collection of content we’ve bundled some of the very best advice we’ve published on repairing, maintaining, evaluating and even hanging molds on injection molding machines.
Mixed in among thought leaders from leading suppliers to injection molders and mold makers at the 2023 Molding and MoldMaking conferences will be molders and toolmakers themselves.
Find a Niche and a Focus Most custom molders in business today have found a niche. Through experience, the molder became good at molding a particular type of part or at molding a particular kind of material, or became astute in working in a specific segment of the marketplace. In other words, he acquired an expertise and stuck with it. A captive molder inherits a market or a range of products, but must develop the same expertise and focus that a custom molder does.
The Plastics Industry Association (PLASTICS) has released final figures for NPE2024: The Plastics Show (May 6-10; Orlando) that officially make it the largest ever NPE in several key metrics.
In this collection of content, we provide expert advice on welding from some of the leading authorities in the field, with tips on such matters as controls, as well as insights on how to solve common problems in welding.
Processors with sustainability goals or mandates have a number of ways to reach their goals. Biopolymers are among them.
Another factor to consider when investing in a molding press is the type of mold(s) it will be running. Will they be large, multicavity, hot runner molds that require larger-tonnage equipment, or single-cavity, conventional molds that require smaller-tonnage machines? Controls and the speed of system response must be also considered. Do you need a press that provides versatility, or are you investing in a press that will just run one job continuously?
Across all process types, sustainability was a big theme at NPE2024. But there was plenty to see in automation and artificial intelligence as well.
This Knowledge Center provides an overview of the considerations needed to understand the purchase, operation, and maintenance of a process cooling system.
The larger the press, the more it costs, so the size of the majority of parts that will be molded is an important consideration. In a custom operation try to give yourself some flexibility on either end of the spectrum to also mold somewhat smaller or larger parts. This is an area where your business plan and marketing strategy, which determine the direction of your business, will also help you decide on the size and amount of equipment you'll need.
Join KraussMaffei for an insightful webinar designed for industry professionals, engineers and anyone interested in the manufacturing processes of PVC pipes. This session will provide a comprehensive understanding of the technology behind the production of high-quality PVC pipes: from raw material preparation to final product testing. Agenda: Introduction to PVC extrusion: overview of the basic principles of PVC pipe extrusion — including the process of melting and shaping PVC resin into pipe forms Equipment and machinery: detailed explanation of the key equipment involved — such as extruders, dies and cooling systems — and their roles in the extrusion process Process parameters: insight into the critical process parameters like temperature, pressure and cooling rates that influence the quality and consistency of the final PVC pipes Energy efficiency: examination of ways to save material and energy use when extruding PVC pipe products
Plant Layout Assuming you have the capital to support a startup, or have a budget from corporate headquarters, you start physical construction with the plant. Whether you build or buy, the layout of your plant is a crucial consideration if you're going to have an efficient, profitable operation. Allow approximately 1000 sq ft of space for each molding press; this accounts for offices, molding/production, secondary operations, quality control, storage of materials, and a mold maintenance and repair area.
When the demand for world-class molding facilities is added to state-of-the-art manufacturing capabilities, the bar for entry into the custom injection molding business rises considerably. Instead of being able to enter the molding business on a shoestring, as many did 30 years ago, a large financial investment is now required. This generally requires the cooperation of a bank, an equipment leasing or lending institution, and financial backing from private investors to pull together the funds needed to succeed. Likewise, the barriers to entry for a captive operation to provide a good return on investment are high. It's not enough to buy molding machines and auxiliaries and leave them in place without improvements for the long haul. Captive operations also must not only make an initial investment, but also be prepared to stay technologically attuned.
You should also consider whether or not cleanroom molding will be needed; if material handling will be done manually or via automatic pneumatic conveying systems (or a combination); where storage areas for materials will be; and whether the layout for manufacturing will promote production efficiency and minimize part handling in molding, assembly, and any other secondary operations.
Some molders elect to use storage silos for resin; these molders usually specialize in one or two closely related markets and mold large parts from one or two materials or millions of parts from the same material. Resin from a silo can be pneumatically pumped to a machine, so little or no shelf space is required for its storage. Other molders, because of the nature of their businesses, opt to store raw materials on the shelf, a procedure that has been known to lead to overcrowding.
Despite price increase nominations going into second quarter, it appeared there was potential for generally flat pricing with the exception of a major downward correction for PP.
Quality Issues—What They're All About Finally, consider how your new plant will develop and assess product quality. During the past decade, quality issues as a part of good business operations have become a top concern for custom and captive molders. The OEM-custom molder relationship has always been one of interdependence, but until recently, custom molders had free rein when it came to matters of production.
Learn about sustainable scrap reprocessing—this resource offers a deep dive into everything from granulator types and options, to service tips, videos and technical articles.
In a time where sustainability is no longer just a buzzword, the food and beverage packaging industry is required to be at the forefront of this innovation. By adopting circular packaging processes and solutions, producers can meet regulatory requirements while also satisfying consumer demand and enhancing brand reputation. Join Husky to learn more about the broader implications of the circular economy — as well as how leading brands are leveraging this opportunity to reduce costs, increase design flexibility and boost product differentiation. Agenda: The cost and operational benefits of embracing circularity Key materials in circular packaging — including rPET and emerging bioplastics How to design a circular food and beverage package Strategies for selecting sustainable closures to future-proof packaging solutions Optimization and streamlining of production processes for enhanced efficiency How Husky Technologies can enable your sustainable success
Based on the company’s extruder screw designs, which consist of three patents in the single and double-vented configuration, the IRM Technology can be retrofitted into existing injection molding machines or built into new ones.
When, how, what and why to automate — leading robotics suppliers and forward-thinking moldmakers will share their insights on automating manufacturing at collocated event.
Several factors must be considered to determine the return on investment (ROI) for a press. One of the biggest factors driving machinery investment is the amount of energy used. Estimates put energy costs at about 5 to 7 percent of a molder's total operating budget. Considering the amount of energy a typical 15-press plant can consume, energy has become an enormous cost issue. A-c variable-speed pumps and motors offered on most newer equipment, and as a retrofit for older equipment, can save energy by using it only when called upon during the machine's cycle.
Other investment factors include the performance history for the machine under consideration, shot-to-shot repeatability, and whether the machine is geared toward high-volume, high-speed applications or low-volume, slow-cycle requirements. Ultimately, at the end of the day, what is its yield? Determining your ROI is application dependent. Some things can be quantified up front, but others can't until the mold is in the press and parts are running.
“Every shot pot has a plunger and then an extruder off to side,” Dray explains. Material is melted by the extruder and then enters the pot before being injected into the mold. The system requires adding another screw and barrel alongside the machine’s existing barrel, with single or double venting added to remove all volatiles and moisture. In the first inlet, reinforcing materials such as glass fibers can be added to improve physical properties.
While most molders accommodate the requirements of their customers, some question the necessity of all the quality bells and whistles like SPC, SQC, ISO 9000, and Six Sigma (a term coined by Motorola that refers to a quality level of three defective parts per million), given the variables of the molding process.
Plastics Technology covers technical and business Information for Plastics Processors in Injection Molding, Extrusion, Blow Molding, Plastic Additives, Compounding, Plastic Materials, and Resin Pricing. About Us
A new barrier screw has removable keys to change the dam height, allowing the screw to be tuned for highest throughput with resins as different as LLDPE and nylon, says the screw’s designer, Robert Dray, president of R.
technotrans says climate protection, energy efficiency and customization will be key discussion topics at PTXPO as it displays its protemp flow 6 ultrasonic eco and the teco cs 90t 9.1 TCUs.
August 29-30 in Minneapolis all things injection molding and moldmaking will be happening at the Hyatt Regency — check out who’s speaking on what topics today.
Additive technology creates air pockets in film during orientation, cutting down on the amount of resin needed while boosting opacity, mechanical properties and recyclability.
Take a deep dive into all of the various aspects of part quoting to ensure you’ve got all the bases—as in costs—covered before preparing your customer’s quote for services.
This month’s resin pricing report includes PT’s quarterly check-in on select engineering resins, including nylon 6 and 66.
As with most any major capital purchase, the price you pay for a particular unit depends on a lot of variables. In injection molding the variables are too numerous to list here, but generally, whatever you buy will vary by application. Much depends on what kind of material you'll mold, how much you'll use, and how large the parts are. But let's say, just for grins, that you do want to start up your own molding shop, based on the list above. And let's say you make some broad generalizations about how material will be handled, how much material you'll use, how long your cycles will be, and other considerations. About how much would the primary equipment cost for such a startup facility?
Today it's increasingly apparent that if you're starting a plant or a business, you are either given or must find a niche—a specific market or product line—and focus on molding for that market or customer. Will you mold large parts? Small parts? Do you want to be a molder of low-volume, high-dollar parts? Or high-volume, low-dollar parts? Most people would answer that they want to be a molder of high-volume, high-dollar parts. If only it worked that way.
While the melting process does not provide perfect mixing, this study shows that mixing is indeed initiated during melting.
Successfully starting or restarting an injection molding machine is less about ticking boxes on a rote checklist and more about individually assessing each processing scenario and its unique variables.
R. Dray’s injection regrind machine (IRM) uses technology deployed in extrusion to help injection molders process more regrind material. Source: R. Dray
Large OEMs—specifically, the automotive and computer industries—adopted the philosophy of manufacturing with quality as they began seeking greater market share for their products. They recognized, however, that the quality of their products could be no better than the quality of the products' component parts. For this reason, much of the responsibility for improving quality has been laid directly at the feet of custom injection molders who supply the vast number of components.
If you require some level of cleanroom molding—often required by medical and electronics parts—then you must decide how you will achieve it. The various types of cleanrooms include Class 100, Class 1000, Class 10,000 and Class 100,000. Each level has its own criteria and must meet certain requirements as established by FDA guidelines. Class 100 is the most stringent and Class 100,000 is simply a "clean environment," and therefore the easiest to achieve.
After successfully introducing a combined conference for moldmakers and injection molders in 2022, Plastics Technology and MoldMaking Technology are once again joining forces for a tooling/molding two-for-one.
GETTING A QUOTE WITH LK-MOULD IS FREE AND SIMPLE.
FIND MORE OF OUR SERVICES:
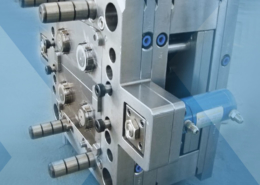
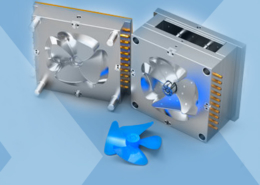
Plastic Molding

Rapid Prototyping
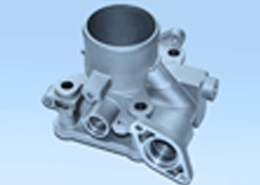
Pressure Die Casting
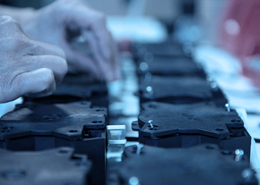
Parts Assembly
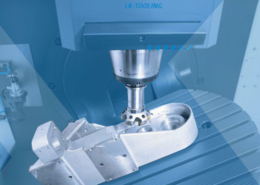