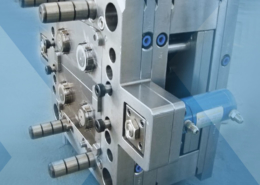
BRC banks on frugality, family values for continued success - rubber plastic mol
Author:gly Date: 2024-09-30
Some in the medical industry are using silicone rubber molds made with a 3D-printed master pattern for low-to-mid production runs of cast polyurethane device housings.
Avenue Mould Solutions (Sligo, Ireland) brings to GW Plastics expertise in building ultra-high-cavitation tooling for the medical device, diagnostics and pharmaceutical markets.
It’s also cheaper and faster to make a master silicone tool that takes days and costs thousands of dollars vs. creating a metal mold that takes weeks to make and costs tens of thousands of dollars for injection molding.
Devices can also incorporate fillers such as fiberglass, carbon fiber, and Kevlar to add rigidity, strength or, in the case of Kevlar, impact resistance. The fillers are laid into the mold by hand, then polyurethane is cast into it and subsequently permeates the weave of the filler fiber.
Once the mold is made, the polyurethane’s liquid components are poured in at a specific ratio. The polyurethane is cured with heat, which gives the thermoset a chance to harden and develop ultimate mechanical properties. External features can include snap fits, interlocking joints, threaded fasteners, and living hinges.
GW Plastics (Bethel, VT) announced today the purchase of Avenue Mould Solutions, a precision mold building, machining and injection molding company based in Sligo, Ireland. Noting growing demand for its services from medical device OEMs, GW Plastics said that the acquisition of Avenue Mould Solutions will bring into the fold “unparalleled global precision moldmaking and advanced manufacturing capability to support customers on three continents.”
In addition, 3D printing enables masters with complex geometries and internal features for housings for such items as testing, diagnostic and therapeutic devices; instrument panels; medical and dental capital equipment; and lifestyle items such as treadmills and exercise bicycles.
3D printing speeds up the cast urethane process, according to Chuck Alexander, director of product management, Stratasys Direct (Valencia, CA), the manufacturing division of Stratasys Ltd. “Creating a master with 3D printing allows you to get to a completed mold and the casting process quicker,” he said.
Avenue Mould Solutions Managing Director Felim McNeela stressed that Avenue will continue to serve its existing customers and offer mold-building for customers who wish to do their own injection molding. “GW Plastics does not wish to change Avenue’s successful history of supplying tooling to our injection molding and contract manufacturing customers,” said McNeela.
Among the reasons they’re doing so are the ability to be first to market with a new product; be able to enter new markets; make small runs to test new devices; make design changes more easily; and even achieve full production for items needed in small numbers.
This acquisition will give GW Plastics precision mold-building facilities in North America, Asia and Europe, in addition to injection molding and contract manufacturing. Avenue Mould Solutions has particular expertise in building ultra-high-cavitation tooling for the medical device, diagnostics and pharmaceutical markets.
For markets where innovation is the norm and product life is short, silicone tooling to cast polyurethane also allows manufacturers to improve their designs at a faster pace without having to amortize the cost of hard tooling. “Any design change becomes easier to incorporate as you go along,” Alexander said.
“You can use that soft material since it doesn’t have to hold up to the pressures of injection,” Alexander said. “If you’re adding pressure, even if it’s low pressure, you need a hard tool to do that. And that’s where the cost goes up.”
Generally, a silicone mold makes sense for production runs of 500 units per year or less, according to Alexander. Typically, when medical manufacturers introduce new devices, the volumes are generally low—tens or hundreds of units annually. Injection molding tooling can be cost-prohibitive in markets with that low of an annual sales volume. For some applications where production runs remain small, a soft silicone tool may be all that’s ever needed.
The acquisition follows expansions of GW Plastics’ facilities in San Antonio, TX; Tucson, AZ; and Dongguan, China, as well as its thermoplastics and silicones manufacturing and mold-building facilities in Royalton, VT, all within the last two years.
“We’ve had customers sell hundreds of units a year and they never go to a hard tool,” Alexander said. “They stay with cast urethanes.”
Other available material features important in the medical industry are compatibility with medical imaging, electrostatic dissipation and electromagnetic shielding to block electronic signals either from or to a device. Copper or silver coatings can be applied in a layer 0.005” (0.127mm) thick using standard spray paint equipment after the casting process is done.
“Avenue Mould Solutions brings to GW Plastics an experienced and highly skilled advanced manufacturing workforce, an award-winning mold-building company and a growing medical device contract manufacturing business that has been successfully serving Ireland and other markets for 30 years,” said Brenan Riehl, GW Plastics President and CEO, in a prepared statement. “We are pleased that Avenue has decided to join GW Plastics and help us continue to expand our capabilities to better meet our customers’ needs on a global basis.”
GETTING A QUOTE WITH LK-MOULD IS FREE AND SIMPLE.
FIND MORE OF OUR SERVICES:
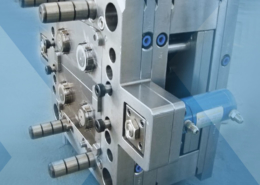
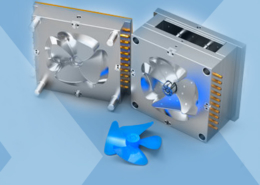
Plastic Molding

Rapid Prototyping
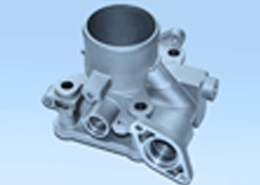
Pressure Die Casting
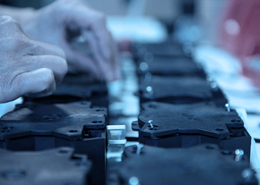
Parts Assembly
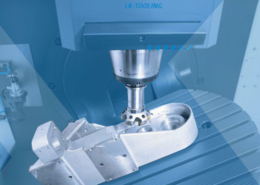