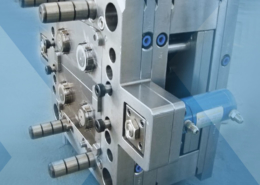
Braille-Teaching Toy - prototype plastic
Author:gly Date: 2024-09-30
Rastogi, A., Paik, M. Y., Tanaka, M. & Ober, C. K. Direct patterning of intrinsically electron beam sensitive polymer brushes. ACS Nano 4, 771–780 (2010).
Arburg calculates that electricity related CO2 emissions during production generate an emissions factor of 0.366 [kg CO2 equivalent per kWh] for the standard German electricity mix in the year 2020. On that basis, the electricity requirement is 2900 kWh for the Allrounder 370 H, with a CO2 equivalent of around 1,160 kg, while for the Allrounder 570 H, the electricity requirement would be 7295 kWh with emissions around 2670 kg CO2.
Arburg has utilized the ISO TS 1467:2018 standard, which determines the greenhouse gas emissions of a product, to help its customers calculate the product carbon footprint (PCF) of its injection molding machines.
Resin drying is a crucial, but often-misunderstood area. This collection includes details on why and what you need to dry, how to specify a dryer, and best practices.
N. Sandström, et al. Reaction injection molding and direct covalent bonding of oste+ polymer microfluidic devices. J. Micromech. Microeng. 25, 75002–75014 (2015).
Implementing a production monitoring system as the foundation of a ‘smart factory’ is about integrating people with new technology as much as it is about integrating machines and computers. Here are tips from a company that has gone through the process.
While prices moved up for three of the five commodity resins, there was potential for a flat trajectory for the rest of the third quarter.
Microstructured surfaces and microfluidic components are increasingly important for a diverse range of biological and clinical applications, e.g., in protein and cell studies1,2,3. Using polymers for such applications is often preferred over glass or silicon because of the soft material properties and the ease of device replication. Whereas micro-injection molding (IM) and micro-reaction injection molding (RIM) enable industrial-scale microstructuring of low-cost polymer materials4, the lack of a simple and straightforward approach for surface modification remains a limiting factor5. Microscale hydrophilic and hydrophobic patterning is commonly achieved via back-end processing techniques, e.g., plasma treatment, grafting and chemical coating6,7, which are multi-step, cumbersome, and subject to degradation over time8. Furthermore, surface modification of 3D patterns and control over surface topography remain unresolved challenges.
All-electric machines generate up to around 50% less CO2 than hydraulically driven ones, depending on the equipment and material throughput.
Here, we demonstrate a molding technique capable of microstructuring and 3D in situ surface energy patterning in a single step. We use this platform for high-throughput, scalable replication of HIH femtolitre-well arrays and demonstrate a record-high seeding efficiency of magnetic beads in femtolitre-well arrays.
However, Arburg notes that two aspects of how and where it makes its machines change the calculation. Vertically integrated, Arburg manufactures around 60% of its Allrounder components itself, with this production occurring exclusively at its central location in Lossburg, Germany. That facility utilizes carbon-neutral renewable energies such as solar, wind and geothermal energy, as well as combined heat and power. Beyond that, since 2016, electricity purchased regionally has come entirely from sustainabile sources. This means that the emissions factor for Arburg’s electricity mix is actually only 0.17 instead of 0.366—53% lower than the German average.
To demonstrate the hydrophilic nature of the bottoms of the microwells, we isolated fL-sized droplets of an aqueous solution of fluorescein in the microwells and sealed them with oil to prevent evaporation. Visualization of the aqueous fluorescein droplets and the absence of fluorescence at the interspacing surface confirms the HIH nature of the array (Fig. 2).
In this collection, which is part one of a series representing some of John’s finest work, we present you with five articles that we think you will refer to time and again as you look to solve problems, cut cycle times and improve the quality of the parts you mold.
Using that figure, the electricity-related CO2 equivalent for the Allrounder 370 H is actually only 490 kg versus 1160 kg, while for the Allrounder 570 the emissions amount to 1240 instead of 2670 kg CO2.
a–e Schematic of the RIM replication using area-selective monomer self-assembly (g–k); and the resulting structures and surface energies (f, l–n). Blue color indicates hydrophilic surfaces; red color hydrophobic surfaces. a Fused silica substrate (blue) coated with Cr (gray) and photoresist (yellow). b Patterned Cr after photolithography and wet etching. c Fused silica pillars with Cr on top after dry etching. d Fused silica pillars with Cr and Teflon on top after Teflon (red) coating. e Finalized mold with hydrophilic pillar arrays in hydrophobic background after Cr lift-off. f Perspective SEM image of a mold insert with 3.5 μm diameter micropillars. g Mold assembly and precursor injection. h The area-selective self-assembly of monomers on mold surfaces with corresponding surface energy. i UV-curing. j Replica demolding. k Detail of HIH wells in the replica. l Top view SEM image of replicated HIH wells with 3.5 μm diameter and 8.5 μm pitch. m, n Contact angle measurements on corresponding hydrophobic and hydrophilic surfaces of non-structured polymer parts after 60 min incubation time
Open Access This article is licensed under a Creative Commons Attribution 4.0 International License, which permits use, sharing, adaptation, distribution and reproduction in any medium or format, as long as you give appropriate credit to the original author(s) and the source, provide a link to the Creative Commons license, and indicate if changes were made. The images or other third party material in this article are included in the article’s Creative Commons license, unless indicated otherwise in a credit line to the material. If material is not included in the article’s Creative Commons license and your intended use is not permitted by statutory regulation or exceeds the permitted use, you will need to obtain permission directly from the copyright holder. To view a copy of this license, visit http://creativecommons.org/licenses/by/4.0/.
Vergauwe, N. et al. A versatile electrowetting-based digital microfluidic platform for quantitative homogeneous and heterogeneous bio-assays. J. Micromech. Microeng. 21, 054026 (2011).
Diaz-Quijada, G. A. et al. Surface modification of thermoplastics—towards the plastic biochip for high throughput screening devices. Lab Chip 7, 856–862 (2007).
Most impactful to the calculation is whether the machine utilizes an electric, hydraulic or hybrid drive. Going further, the calculation is also impacted by whether one or two-circuit pump technology or hydraulic accumulators are used, as well as other options like servo-electric dosing or ejection. Arburg notes that any features that enable simultaneous, dynamic and fast movements and shorten cycle times have a positive effect on the carbon footprint during use. The same applies to the screw diameter and installed power, so that the greater the shot weight and the smaller the power consumption, the better.
a Schematic of the magnetic bead seeding on HIH microwell arrays. b The bead distribution in arrays with well diameter 3.5 μm and with varying array pitch and well depth, for single- and multiple-seeding cycles (n = 5). Dots indicate results from each experiment; columns indicate the average ratio of wells that contain a given number of beads; error bars mean ± s.d. c, d ×40 magnification bright field microscopy image of a microwell array before and after magnetic bead seeding, respectively. Bright spots indicate empty microwells and dark spots indicate filled microwells. e ×100 magnification bright field microscopy image of a microwell array after seeding, where one well is empty (bright), two wells contain two beads, and all other wells contain one bead
The RIM platform demonstrated here is adapted for use in laboratory settings, allowing a potential widespread dissemination of the technology. Because life science research typically relies on several tens of identical devices to verify the reproducibility of experiments, the rapid device replication offers an attractive alternative to the manual and error-prone per-part assembly of soft lithography-based devices.
Miller, M. B. & Tang, Y.-W. Basic concepts of microarrays and potential applications in clinical microbiology. Clin. Microbiol. Rev. 22, 611–633 (2009).
Decrop, D. et al. Single-step imprinting of femtoliter microwell arrays allows digital bioassays with attomolar limit of detection. ACS Appl. Mater. interfaces 9, 10418–10426 (2017).
The aim of this presentation is to guide you through the factors and the numbers that will help you determine if a robot is a smart investment for your application. Agenda: Why are you considering automation? What problems are you trying to solve? How and why automation can help Crunch the numbers and determine the ROI
Kan, C. W. et al. Isolation and detection of single molecules on paramagnetic beads using sequential fluid flows in microfabricated polymer array assemblies. Lab Chip 12, 977–985 (2012).
Plastics Technology covers technical and business Information for Plastics Processors in Injection Molding, Extrusion, Blow Molding, Plastic Additives, Compounding, Plastic Materials, and Resin Pricing. About Us
Any features that enable simultaneous, dynamic and fast movements and shorten cycle times have a positive effect on the carbon footprint during use. Photo Credit: Arburg
In this collection of content, we provide expert advice on welding from some of the leading authorities in the field, with tips on such matters as controls, as well as insights on how to solve common problems in welding.
Join this webinar to explore the transformative benefits of retrofitting your existing injection molding machines (IMMs). Engel will guide you through upgrading your equipment to enhance monitoring, control and adaptability — all while integrating digital technologies. You'll learn about the latest trends in IMM retrofitting (including Euromap interfaces and plasticizing retrofits) and discover how to future-proof your machines for a competitive edge. With insights from industry experts, it'll walk you through the decision-making process, ensuring you make informed choices that drive your business forward. Agenda: Maximize the value of your current IMMs through strategic retrofitting Learn how to integrate digital technologies to enhance monitoring and control Explore the benefits of Euromap interfaces and plasticizing retrofits Understand how retrofitting can help meet new product demands and improve adaptability Discover how Engel can support your retrofitting needs, from free consultations to execution
A lot simpler to understand and calculate than a carbon footprint, this ‘footprint’ measures your energy use per kg of plastic processed.
Additive technology creates air pockets in film during orientation, cutting down on the amount of resin needed while boosting opacity, mechanical properties and recyclability.
The dimensions of the demonstrated microwells are tailored to host a single magnetic bead with 2.7 μm diameter. Not to undermine the true digital nature of the assay, wells containing more than one bead must be excluded from the signal count during the image analysis, and their number should therefore remain limited. For well arrays with 8.5 μm pitch, we estimate trapping two beads in as little as 2.1 ± 0.4% of the wells after single-step seeding, and in 7.1 ± 0.8% after multiple-step seeding (Fig. 3e).
Madaan, N., Romriell, N., Tuscano, J., Schlaad, H. & Linford, M. R. Introduction of thiol moieties, including their thiol–ene reactions and air oxidation, onto polyelectrolyte multilayer substrates. J. Colloid Interface Sci. 459, 199–205 (2015).
Mold maintenance is critical, and with this collection of content we’ve bundled some of the very best advice we’ve published on repairing, maintaining, evaluating and even hanging molds on injection molding machines.
August 29-30 in Minneapolis all things injection molding and moldmaking will be happening at the Hyatt Regency — check out who’s speaking on what topics today.
We dragged a 30 μL droplet of a 0.25 mg/mL fluorescein solution (Sigma-Aldrich, Belgium) over the microwell array. We subsequently covered the droplet of fluorescein with a 180 μL droplet of PlusOne Drystrip Coverfluid oil (Sigma-Aldrich, Belgium) to prevent evaporation. Next, we removed the fluorescein from underneath the oil using a glass pipette tip, first dragging the fluorescein droplet away from the array, then pipetting the fluorescein out from underneath the oil. The sealed microwells were visualized using an inverted fluorescence microscope (Nikon TiEclipse, Japan), using a TITC filter (excitation 465–495 nm, emission 515–550 nm).
When you drill down to the level of an individual screw, the complete parts list of an injection molding machine could consist of 11,000 indivdual items. To help it better manage that figure, Arburg categorizes all its raw materials into eight distinct materials groups. On this basis, an Allrounder consists of more than 55% plastic-coated cast iron, and another 35% of steel and sheet metal, whether they’re hot-treated, painted, plastic-coated or untreated. Plastic components, drives and electronic components account for only about 7% of the total weight.
Shafagh, R. Z., Vastesson, A., Guo, W., Wijngaart, Wvander & Haraldsson, T. E-beam nanostructuring and direct click biofunctionalization of thiol–ene resist. ACS Nano 12, 9940–9946 (2018).
We purchased streptavidin-coated LodeStar 2.7 μm superparamagnetic beads with a stock concentration of 8 × 108 beads/mL from Agilent Technologies (Santa Clara, CA, USA). To prepare the beads for seeding, 10 µL of the stock solution was washed three times in 150 μL of a mixture of phosphate-buffered saline (PBS), 0.1% bovine serum albumin, and 0.1% Tween-20. The beads were resuspended in 80 μL PBS containing 2% Tween-20. For multiple seeding events, we pipetted a 5 μL drop of this solution on the microwell array, and a plastic pipette tip was used to move the droplet back and forth across the array 30 times while a magnet was held underneath the array to attract the beads into the wells. After the 30 seeding events, we removed the magnet and pushed the droplet off of the array. In the case of a single seeding event, we moved the droplet across the array only once. We visualized the beads using an inverted fluorescence microscope in bright field mode (Nikon TiEclipse, Japan) and counted for five different samples.
The Plastics Industry Association (PLASTICS) has released final figures for NPE2024: The Plastics Show (May 6-10; Orlando) that officially make it the largest ever NPE in several key metrics.
We performed CA measurements using a Theta Lite optical tensiometer (TL100, Finland) on non-structured polymer parts replicated from flat, Teflon-coated and bare fused silica molds, respectively. We chose three random areas on each sample and calculated the average CA accordingly. We performed the CA measurements immediately after the RIM process and 11 months after the RIM process measurements to allow measuring surface energy recovery over time.
Witters, D., Knez, K., Ceyssens, F., Puers, R. & Lammertyn, J. Digital microfluidics-enabled single-molecule detection by printing and sealing single magnetic beads in femtoliter droplets. Lab Chip 13, 2047–2054 (2013).
The RIM setup is comprised of two mold halves which come together to form the negative shape of the final chip. The first mold half is a 5 mm thick Al sheet (4.5 × 7.4 cm2) CNC milled (MiniMill GX, Minitech Machinery Corp., USA) with a 3.5 × 3.5 cm2 indentation to form a cavity. Inlet and outlet channels connect the cavity to the edges of the mold.
Introduced by Zeiger and Spark Industries at the PTXPO, the nozzle is designed for maximum heat transfer and uniformity with a continuous taper for self cleaning.
Join Wittmann for an engaging webinar on the transformative impact of manufacturing execution systems (MES) in the plastic injection molding industry. Discover how MES enhances production efficiency, quality control and real-time monitoring while also reducing downtime. It will explore the integration of MES with existing systems, emphasizing compliance and traceability for automotive and medical sectors. Learn about the latest advancements in IoT and AI technologies and how they drive innovation and continuous improvement in MES. Agenda: Overview of MES benefits What is MES? Definition, role and brief history Historical perspective and evolution Longevity and analytics Connectivity: importance, standards and integration Advantages of MES: efficiency, real-time data, traceability and cost savings Emerging technologies: IoT and AI in MES
In this three-part collection, veteran molder and moldmaker Jim Fattori brings to bear his 40+ years of on-the-job experience and provides molders his “from the trenches” perspective on on the why, where and how of venting injection molds. Take the trial-and-error out of the molding venting process.
Rondelez, Yannick et al. Microfabricated arrays of femtoliter chambers allow single molecule enzymology. Nat. Biotechnol. 23, 361 (2005).
The CA measurements demonstrate the surface energy pattern replication. The reduced concentration of hydrophilic or hydrophobic moieties resulted in microstructured replicas with excellent functionality, but also in a dependence of the hydrophobic mimicking phenomenon on the incubation time. Nevertheless, even at zero incubation time, the hydrophobic surfaces feature an equilibrium CA equal to 90°, which proved sufficient for bead seeding and well sealing. Although the degree of hydrophilicity associated to the replica is lower than that of glass, it is sufficient for droplet entrapment inside the microwells. The CA on the hydrophobic polymer surface did not change significantly during long-term storage; that of the hydrophilic surface reduced from 59.3 ± 2.6° to 48.1 ± 2.2°. We attribute this increase of hydrophilicity to oxidation of the thiol groups when exposed to the ambient air28. Compared to postprocess surface modification techniques such as plasma treatment of PDMS, which is prone to fast recovery of surface energy, our method offers a far more stable surface energy definition with some degree of enhancement regarding the hydrophilic surfaces over time.
“As a machine manufacturer, Arburg is actively and comprehensively involved in carbon accounting in order to provide reliable and comparable indicators and meet the ambitious climate targets,” the company stated in release, noting it earned an “above-average” B grade in the Carbon Disclosure Project (CDP).
Researchers from Sweden and Belgium have developed a simplified technique to create microfluidic devices with patterns of modified surface properties. Microfluidic devices, such as the one demonstrated here by a team led by Wouter van der Wijngaart, from KTH Royal Institute of Technology, Sweden, utilize polymer microstructures with hydrophobic and hydrophilic properties to manipulate fluids on a tiny scale. This enables ‘lab-on-a-chip’ experiments with a diverse array of applications. However, current devices suffer from complicated fabrication processes and a limited lifespan. van der Wijngaart and his team used the polymer ‘off-stoichiometric thiol-ene’ to merge a rapid replication technique called reaction injection molding with a method to self-assemble hydrophobic and hydrophilic micropatterns in a single, rapid fabrication step. The researchers hope that their results will form the basis for future microfluidic chip manufacturing and lead to the creation of ultrasensitive life science research tools.
In the first step, Arburg looks at the “cradle to gate” carbon footprint of its machines—that is the amount of carbon emitted in the manufacture of the press. This extends through raw material extraction and the manufacturing phase. All told, this portion of the machine’s existence only accounts for 5% of its CO2 emissions. On a cradle-to-grave basis, which weighs a machine’s entire life, most of the PCF is generated during the use phase at the customer’s factory. The remaining remnant is associated with emissions made during the machine’s distribution and disposal.
Heckele, M. & Schomburg, W. K. Review on micro molding of thermoplastic polymers. J. Micromech. Microeng. 14, R1 (2003).
Processors with sustainability goals or mandates have a number of ways to reach their goals. Biopolymers are among them.
Rissin, D. M. et al. Single-molecule enzyme-linked immunosorbent assay detects serum proteins at subfemtomolar concentrations. Nat. Biotechnol. 28, 595 (2010).
A Boston recycler invested in a turnkey shredding, granulation and elutriation system to expand its plastics reclaim business.
Across all process types, sustainability was a big theme at NPE2024. But there was plenty to see in automation and artificial intelligence as well.
a Schematic of fluorescein and oil stacked on top of HIH microwells followed by the fluorescein removal. b Schematic of the resulting femtolitre fluorescein microdroplets trapped inside the wells. c Top view fluorescence microscopy image of fluorescein microdroplets inside HIH femtolitre-wells: the dark region in the top half of the image has been only in contact with oil whereas the lower half of the image is printed by the receding fluorescent droplet. The dashed line indicates the border of the fluorescein droplet shown in (a)
To illustrate this, Arburg explains that a hybrid Allrounder 570 H with a clamping force of 204 metric tons (m.t.) and a net weight of approximately 18,000 lb has raw material-related emissions of around 15,190 kg of CO2 during its manufacture. At the other end of the scale, a 61 m.t. Allrounder 370 weighing 7275 lb generates a CO2 equivalent of around 6040 kg.
When, how, what and why to automate — leading robotics suppliers and forward-thinking moldmakers will share their insights on automating manufacturing at collocated event.
We used an optical profilometer (SENSOFAR S lynx with software SensoSCAN 6.4) for 3D optical cross-sectional imaging of micropillar and microwell arrays.
In a time where sustainability is no longer just a buzzword, the food and beverage packaging industry is required to be at the forefront of this innovation. By adopting circular packaging processes and solutions, producers can meet regulatory requirements while also satisfying consumer demand and enhancing brand reputation. Join Husky to learn more about the broader implications of the circular economy — as well as how leading brands are leveraging this opportunity to reduce costs, increase design flexibility and boost product differentiation. Agenda: The cost and operational benefits of embracing circularity Key materials in circular packaging — including rPET and emerging bioplastics How to design a circular food and beverage package Strategies for selecting sustainable closures to future-proof packaging solutions Optimization and streamlining of production processes for enhanced efficiency How Husky Technologies can enable your sustainable success
While the melting process does not provide perfect mixing, this study shows that mixing is indeed initiated during melting.
Dressler, O. J., Solvas, X. Ci & deMello, A. J. Chemical and biological dynamics using droplet-based microfluidics. Annu. Rev. Anal. Chem. 10, 1–24 (2017).
Going forward, Arburg’s goal is to calculate “a scientifically sound, holistic lifecycle assessment for injection molding machines.” Arburg says such an effort is underway at the Institute of Plastics and Circular Economy (IKK) at
Remembering that fully 95% of an injection molding machine’s PCF is attributed to its operation, Arburg says a key parameter to assess that is the specific energy requirement [kWh per kg], which is calculated from power consumption per material throughput. As a rule of thumb, the shorter the cycle time and higher the shot weight, the smaller the specific energy requirement and better the CO2 equivalent.
Mike Sepe has authored more than 25 ANTEC papers and more than 250 articles illustrating the importance of this interdisciplanary approach. In this collection, we present some of his best work during the years he has been contributing for Plastics Technology Magazine.
While prices moved up for three of the five commodity resins, there was potential for a flat trajectory for the rest of the third quarter.
The unique benefit of our fabrication approach is the simultaneous molding and selective and stable surface energy patterning of microstructures in a single process step, while inheriting all benefits from RIM processing, including short-cycle time, facile processing, low tooling cost of RIM settings along with a surface reactive polymer for additional covalent bonding when fluidic integration is intended. The rapid cycle time, limited mainly by the 15 s UV exposure, constitutes by far the most rapid HIH production method reported. We speculate that the cycle time can be reduced to be on par with the typical standard injection molding cycle times, i.e., 2–5 s, by using a more rigid mold material such as quartz, by a vertical demolding set-up, or by adding more photoinitiator in the polymer precursor.
Thank you for visiting nature.com. You are using a browser version with limited support for CSS. To obtain the best experience, we recommend you use a more up to date browser (or turn off compatibility mode in Internet Explorer). In the meantime, to ensure continued support, we are displaying the site without styles and JavaScript.
Learn about sustainable scrap reprocessing—this resource offers a deep dive into everything from granulator types and options, to service tips, videos and technical articles.
Here are processing guidelines aimed at both getting the PHA resin into the process without degrading it, and reducing residence time at melt temperatures.
After successfully introducing a combined conference for moldmakers and injection molders in 2022, Plastics Technology and MoldMaking Technology are once again joining forces for a tooling/molding two-for-one.
The RIM process is illustrated in Fig. 1g–j. A 5 mL syringe was filled with OSTE precursor, equipped with a 1.20 mm by 40 mm Sterican blunt needle and actuated to purge air bubbles from the tip of the syringe and needle. The needle was fitted to the inlet tube, and the syringe was slowly actuated to inject the precursor into the cavity. To allow for shrinkage compensation during curing, we adjusted the volume of precursor injected to include the volume of the entire mold chamber and part of the outlet channel. We, thereafter, removed the syringe and needle. The hydrophilic and hydrophobic moieties in the precursor self-assembled on mold surfaces with matching surface energy, i.e., hydrophilic moieties self-assembled on pillars, resulting in hydrophilic replica surfaces in the wells, and hydrophobic moieties self-assembled on the Teflon substrate, resulting in a hydrophobic top surface of the replicas. We performed experiments in which we allowed incubation of the precursor in the setup for up to 60 min, while shielding from UV light, to allow the hydrophilic and hydrophobic moieties to diffuse to surfaces of the mold with matching surface energies. Thereafter, the precursor was cured for 15 s at 12.5 mW/cm2. After curing, we separated the mold halves using a custom demolding fixture consisting of four ejection pins and removed the replica from the mold using tweezers.
Hoyle, C. E., Lee, T. Yeon & Roper, T. Thiol–enes: chemistry of the past with promise for the future. J. Polym. Sci. Part A 42, 5301–5338 (2004).
Patterning of micro- and nanoscale topologies and surface properties of polymer devices is of particular importance for a broad range of life science applications, including cell-adhesion assays and highly sensitive bioassays. The manufacturing of such devices necessitates cumbersome multiple-step fabrication procedures and results in surface properties which degrade over time. This critically hinders their wide-spread dissemination. Here, we simultaneously mold and surface energy pattern microstructures in off-stoichiometric thiol-ene by area-selective monomer self-assembly in a rapid micro-reaction injection molding cycle. We replicated arrays of 1,843,650 hydrophilic-in-hydrophobic femtolitre-wells with long-term stable surface properties and magnetically trapped beads with 75% and 87.2% efficiency in single- and multiple-seeding events, respectively. These results form the basis for ultrasensitive digital biosensors, specifically, and for the fabrication of medical devices and life science research tools, generally.
Join Engel in exploring the future of battery molding technology. Discover advancements in thermoplastic composites for battery housings, innovative automation solutions and the latest in large-tonnage equipment designed for e-mobility — all with a focus on cost-efficient solutions. Agenda: Learn about cutting-edge thermoplastic composites for durable, sustainable and cost-efficient battery housings Explore advanced automation concepts for efficient and scalable production See the latest large-tonnage equipment and technology innovations for e-mobility solutions
Lobov, G. S. et al. Electro-optical effects of high aspect ratio p3ht nanofibers colloid in polymer micro-fluid cells. Opt. Lett. 42, 2157–2160 (2017).
Becker, H. & Gärtner, C. Polymer microfabrication technologies for microfluidic systems. Anal. Bioanal. Chem. 390, 89–111 (2008).
Thiol-ene alternating copolymer constitutes an important class of thermosetting materials with a broad range of applications in optics, electronics, and biomedicine19,20. The UV polymerization and click reaction in these polymer networks enable rapid, efficient and by-product free reaction with often no need of solvent use. Also, the delayed gelation in thiol-ene polymerization leads to low shrinkage and low residual stress and enhances replication precision during molding21. Off-stoichiometric thiol-ene (OSTE) imparts additional features such as natively reactive surfaces, which offers a diverse spectrum of applications including adhesive-free bonding22,23 or direct binding of biomolecules24. Hydrophilic and hydrophobic moieties within an OSTE polymer precursor spontaneously self-assemble on areas of a master surface that have matching surface energies25. Sandström et al.26 reported micro-RIM of off-stoichiometric thiol-ene epoxy thermosetting polymers as a rapid processing technique that results in high-replication fidelity and low-residual stress.
This month’s resin pricing report includes PT’s quarterly check-in on select engineering resins, including nylon 6 and 66.
Thousands of people visit our Supplier Guide every day to source equipment and materials. Get in front of them with a free company profile.
Second quarter started with price hikes in PE and the four volume engineering resins, but relatively stable pricing was largely expected by the quarter’s end.
Unlike the corporate carbon footprint (CCF), which is calculated for an entire company on an annual basis, PCFs include the quantities of greenhouse gases emitted and removed over the entire service life of a product.
The dynamic range of a digital bioassay is related to the number of microwells, with the demonstrated array size of 105–107 wells theoretically enabling digital target detection with a dynamic range of 6–8 orders of magnitude27. The demonstrated well size and pitch in the µm range are small enough to facilitate integration of large arrays, but large enough for optical detection of individual wells. A mold pillar height/depth aspect ratio of 1/1 results in low-defectivity in terms of pillar collapse while providing a sufficient depth of the wells for trapping beads. For mold pillar aspect ratios >1, the manual and nonvertical demolding led to their occasional collapse.
This Knowledge Center provides an overview of the considerations needed to understand the purchase, operation, and maintenance of a process cooling system.
Using the internationally recognized Greenhouse Gas Protocol, which organizes emissions into three areas—Scope 1, Scope 2 and Scope 3—Arburg says its machines are considered Scope 3 assets. These assets include indirect emissions from upstream and downstream business processes.
We purchased the following monomers and initiator from Sigma-Aldrich, Germany: pentaerythritol tetrakis(3-mercaptopropionate) (PETMP), 1,3,5-triallyl-1,3,5-triazine-2,4,6(1H,3H,5H)-trione (TATATO), 3,3,4,4,5,5,6,6,7,7,8,8,9,9,10,10,10-heptadecafluorodecyl methacrylate (FDMA), 2-hydroxyethyl methacrylate (HEMA), and photo-initiator 1-hydroxycyclohexyl phenyl ketone (Irgacure 184). We synthesized the OSTE precursor with excess of allyl functional groups with the following subsequent steps: (i) mixing the allyl monomer TATATO with the photo-initiator (52.32 and 0.5 wt% of the final mixture, respectively), (ii) heating the mixture to 75 °C for 10 min to facilitate the dissolution of the solid photo-initiator, (iii) adding the thiol monomer PETMP (47.08 wt% of the final mixture), (iv) mixing and subsequent degassing, (v) adding HEMA and FDMA, both at 0.05 wt%, and (vi) mixing again.
Despite price increase nominations going into second quarter, it appeared there was potential for generally flat pricing with the exception of a major downward correction for PP.
For its purposes, Arburg records CO2 in four process steps it undertakes when building a press: painting or coating; mechanical machining and processing; electrical production; and assembly.
Kim, S. H. et al. Large-scale femtoliter droplet array for digital counting of single biomolecules. Lab Chip 12, 4986–4991 (2012).
Shiu, J.-Y., Aires, L., Lin, Z. & Vogel, V. Nanopillar force measurements reveal actin-cap-mediated yap mechanotransduction. Nat. Cell Biol. 20, 262 (2018).
Across the show, sustainability ruled in new materials technology, from polyolefins and engineering resins to biobased materials.
Plastics Technology’s Tech Days is back! Every Tuesday in October, a series of five online presentations will be given by industry supplier around the following topics: Injection Molding — New Technologies, Efficiencies Film Extrusion — New Technologies, Efficiencies Upstream/Downstream Operations Injection Molding — Sustainability Extrusion — Compounding Coming out of NPE2024, PT identified a variety of topics, technologies and trends that are driving and shaping the evolution of plastic products manufacturing — from recycling/recyclability and energy optimization to AI-based process control and automation implementation. PT Tech Days is designed to provide a robust, curated, accessible platform through which plastics professionals can explore these trends, have direct access to subject-matter experts and develop strategies for applying solutions in their operations.
Discover how artifical intelligence is revolutionizing plastics processing. Hear from industry experts on the future impact of AI on your operations and envision a fully interconnected plant.
Ultimately, the parts the machines are molding also have an impact on the press’s PCF. In general, Arburg notes that the specific energy requirements for the production of technical molded parts in smaller quantities is significantly greater than for the production of fast cycling packaging items.
Exhibitors and presenters at the plastics show emphasized 3D printing as a complement and aid to more traditional production processes.
Viewing with a ×40 objective allowed scanning a large area and distinguishing wells with and without beads, but did not allow distinguishing between wells with a single and those with multiple beads. At ×100 magnification it was feasible to distinguish between wells with zero, a single or two beads.
Hydrophilic-in-hydrophobic (HIH) femtolitre-well arrays for digital bioassays are an example of structures that would greatly benefit from simpler fabrication techniques. Digital bioassays commonly exploit arrays of microwells as their hardware and can extensively benefit from selective surface energy patterning9. In such systems, the sample of interest is compartmentalized in well reactors amenable to high-throughput screening or online monitoring10. Such systems enable the ultra-sensitive detection of target molecules on a single-molecule level11. A common solution for efficient isolation of wells is to provide hydrophilic wells in a hydrophobic field. In bead-based digital assays, each well acts as a microchamber that traps a single bead functionalized with bioreceptors and surrounded by a micro-droplet of reagent. Femtolitre-well arrays for bead seeding in digital bioassays were previously fabricated mainly using cleanroom-based techniques9,12,13,14, poly(dimethylsiloxane) (PDMS) stamp imprinting15, or IM16,17. However, these materials and fabrication methods are expensive, not scalable, or do not result in defined surface energy features, the latter resulting in an inefficient bead seeding, leading to limited assay performance18.
The fabrication method for the silica/TeflonTM mold half requires only one photolithography step, resulting in a self-aligned structural and surface energy micropattern where exposed silica provides hydrophilic surfaces and TeflonTM hydrophobic surfaces (Fig. 1a–e). The molds contain a 5 × 5 matrix of micropillar arrays, with a total of 1,843,650 circular pillars, with diameters in the range of 2.5–4.5 μm, and a centre-to-centre pitch in the range of 7–9 μm (Fig. 1f, g; see Fig. S1 for mold design details). The micropillar heights were in the range 3–4.5 μm. We injected an OSTE-based precursor, containing hydrophobic and hydrophilic chemical moieties, into the mold. During incubation in contact with the mold, the chemical moieties in the polymer network self-assemble on mold surface sections with matching surface energy. Cross-linking of the precursor during a 15 s UV exposure fixates the replica microstructure and its surface energy patterns, after which the replica is demolded. A mold consisting of micropillar arrays thus enables in situ surface energy patterned HIH femtolitre-well arrays with hydrophilic well bottom and sidewalls and hydrophobic interspacing. We observed a high-replication fidelity regarding geometry, size, and defectivity of the microwell arrays during microscopy inspection and optical profiling (Fig. S3). Contact angle measurements on larger planar features substantiate the successful mimicking of surface energy from the molds to the counterpart replica surfaces. The contact angle (CA) of the hydrophobic replica surfaces increases with the incubation time between injection and UV curing, from 90° ± 2.8 for no incubation to 104° ± 2.3 when incubating for 60 min (Fig. S2). The CA of hydrophilic replica surfaces was 59° ± 2.6, independent of the incubation time. The surface energy of the fully cured replicas was re-examined after 11 months storage of the samples in our ambient laboratory conditions (Table S1).
Multiple speakers at Molding 2023 will address the ways simulation can impact material substitution decisions, process profitability and simplification of mold design.
The second mold half consists of the mold insert, i.e., a 0.5 mm thick fused silica mold, also sized 4.5 × 7.4 cm², strengthened with a 2 mm thick piece of borosilicate glass glued to its backside. The fused silica structuring is illustrated in Fig. 1a–e. We started from 0.5 mm thick 4″ fused silica wafers and performed the subsequent steps. We evaporated 250 nm of Cr. We deposited the adhesion promotor Hexamethyldisilazane from the gas phase, spin-coated positive tone photoresist (AZ4533, AZ Electronic materials, Germany), and performed photolithography (Mask aligner, Karl Suss, Germany) with 6 s of UV exposure. We developed the resist in CD-26 Developer (Dow, Rohm-Haas supplier, Germany) for 85 s, followed by hard baking at 115 °C for 120 s, and O2 plasma ashing for 4 min at 150 W. We etched the Cr in a Cr etchant consisting of acetic acid: 3.92% w/w, water: 74.73% w/w, and diammonium cerium(IV) nitrate: 21.35% w/w. We stripped the photoresist and dry etched the wafer with DRIE (STS ICP Multiplex Advanced Oxide Etch) using H2, He and C4F8. We silanized and then teflonized the wafers, in which the silanization acts as an adhesion promoter for the subsequent TeflonTM coating on the fused silica. We prepared a hydrophobic fluoroalkylsilane solution consisting of silane (Dynasylan F8263, Evonik Resource Efficiency GmbH, Essen, Germany): 2% w/w, ethanol: 93% w/w, and water: 5% w/w and spin coated it on the substrate at 3000 rpm for 60 s. We baked the substrates at 110 °C for 12 min. We diluted Teflon AF 1601 (Chemours, USA) with fluorinert FC-40 (Sigma-Aldrich, Germany) with the ratio of 1:6, respectively. We spincoated the Teflon solution on the substrates at 2000 rpm for 60 s, followed by baking at 180 °C for 10 min. A lift-off process was subsequently performed in Cr etchant solution to remove Cr and Teflon from the pillar tops.
Formnext Chicago is an industrial additive manufacturing expo taking place April 8-10, 2025 at McCormick Place in Chicago, Illinois. Formnext Chicago is the second in a series of Formnext events in the U.S. being produced by Mesago Messe Frankfurt, AMT – The Association For Manufacturing Technology, and Gardner Business Media (our publisher).
To investigate the potential of surface energy patterned microwells for digital bead-based bioassays, we seeded well arrays with magnetic beads (Fig. 3). All CA combinations were sufficient for bead seeding in surface energy patterned microwells, allowing minimizing the RIM incubation time. Digital counting of the magnetic beads revealed seeding efficiencies as high as 75.1 ± 6.0% for single-step seeding and 87.2 ± 0.3% for multiple-step seeding (Fig. 3b, Table S2).
Future work should examine the potential of RIM-based microwell arrays for digital bioassays aiming for single molecule detection. Furthermore, translating the current technology to industrial RIM standards needs a re-adjustment of the mold material, mold cleaning protocols, injection settings, and demolding.
Successfully starting or restarting an injection molding machine is less about ticking boxes on a rote checklist and more about individually assessing each processing scenario and its unique variables.
The high-seeding efficiency reported here is ascribed to the successful surface energy patterning of the arrays and is of significance for bead-based bioassays, which require rapid and efficient bead seeding. Our results compare well with the estimated 40–50% gravity-based bead loading efficiency achieved in the SIMOA process16 and the maximum 35% efficiency obtained in previously reported single-step seeding12.
If the raw material and electricity-related emissions are added, the total CO2 equivalent for a “cradle to gate” analysis is 6530 kg for the Allrounder 370 H and 16,430 kg for the Allrounder 570 H. So what does that actually mean? By comparison, Arburg says each person in Germany generates an average carbon footprint of around 12,000 kg/yr, depending on personal consumption, mobility, housing and nutrition.
Figure 1 illustrates the specifically developed mold fabrication process, the replication process that combines RIM of OSTE with area-selective monomer self-assembly, and the resulting replicas and their surface energies. We developed a two-part HIH mold consisting of a milled Al half with good thermal conductivity, and a UV transparent microstructured half consisting of fused silica and TeflonTM. Using a hard mask is compatible with industrial injection molding settings in which a material of high Young-modulus circumvents the deformation and collapse of delicate microscale mold features. This is in contrast to use of PDMS, a prevalent material of choice in academia, which is prone to deformation and subsequent feature distortion during the molding process and therefore not easily applicable to commercial set-ups.
Although these different material groups differ significantly in terms of the CO2 emissions generated during their production, Arburg says a weighted mean value can be determined along the lines of the distribution. This so-called emissions factor is around 1.83 [kg CO2 equivalent per kg product] for an Allrounder. The CO2 equivalent for the complete injection molding machine thus corresponds to the emissions factor multiplied by the press’ weight.
Sandström, N., Shafagh, R. Z., Gylfason, K. B., Haraldsson, T. & van der Wijngaart, W. Batch fabrication of polymer microfluidic cartridges for qcm sensor packaging by direct bonding. J. Micromech. Microeng. 27, 124001 (2017).
Take a deep dive into all of the various aspects of part quoting to ensure you’ve got all the bases—as in costs—covered before preparing your customer’s quote for services.
Mixed in among thought leaders from leading suppliers to injection molders and mold makers at the 2023 Molding and MoldMaking conferences will be molders and toolmakers themselves.
technotrans says climate protection, energy efficiency and customization will be key discussion topics at PTXPO as it displays its protemp flow 6 ultrasonic eco and the teco cs 90t 9.1 TCUs.
While the major correction in PP prices was finally underway, generally stable pricing was anticipated for the other four commodity resins.
Machado, T. O., Sayer, C. & Araujo, P. H. H. Thiol-ene polymerisation: a promising technique to obtain novel biomaterials. Eur. Polym. J. 86, 200–215 (2017).
We express our gratitude to Mercene Labs, Sweden, for their kind contribution of OSTE polymer. We would also like to thank Cecilia Aronsson and Mikael Bergqvist for their contribution to the technical aspects of the research. We furthermore would like to acknowledge Prof. Paula Moldenaers of the Soft Matter, Rheology and Technology group at KU Leuven (Belgium) for providing the facilities for the contact angle measurements and Prof. Michael Kraft of the MICAS group at KU Leuven (Belgium) for providing the facilities for the 3D optical profile measurements. This work was financially sponsored, in part, by the European Union and EFPIA through the IMI project RAPPID and by the European Union through the FP7 project NOROSENSOR. This work has also received funding from Research Foundation-Flanders (FWO SB/1S30116N).
As the European Union’s Green Deal takes effect and companies strive toward climate neutral production by 2050, knowing the product carbon footpring (PCF) of the entire supply chain will become increasingly important for European businesses. Arburg notes that in Germany the laws go even further, enforcing a 65% reduction in CO2 emissions by 2030 with carbon neutrality by 2045.
Donzel, C. et al. Hydrophilic poly (dimethylsiloxane) stamps for microcontact printing. Adv. Mater. 13, 1164–1167 (2001).
It’s all about sustainability and the circular economy, and it will be on display in Orlando across all the major processes. But there will be plenty to see in automation, AI and machine learning as well.
Sustainability continues to dominate new additives technology, but upping performance is also evident. Most of the new additives have been targeted to commodity resins and particularly polyolefins.
Wilson, D. H. et al. The simoa hd-1 analyzer: a novel fully automated digital immunoassay analyzer with single-molecule sensitivity and multiplexing. J. Lab. Autom. 21, 533–547 (2016).
Core Technology Molding turned to Mold-Masters E-Multi auxiliary injection unit to help it win a job and dramatically change its process.
Zandi Shafagh, R., Decrop, D., Ven, K. et al. Reaction injection molding of hydrophilic-in-hydrophobic femtolitre-well arrays. Microsyst Nanoeng 5, 25 (2019). https://doi.org/10.1038/s41378-019-0065-2
Leibniz University in Hanover. There, Professor Hans-Josef Endres is working on in collaboration with Arburg, among others.
Gifted with extraordinary technical know how and an authoritative yet plain English writing style, in this collection of articles Fattori offers his insights on a variety of molding-related topics that are bound to make your days on the production floor go a little bit better.
Ultradent's entry of its Umbrella cheek retractor took home the awards for Technical Sophistication and Achievement in Economics and Efficiency at PTXPO.
Yatsushiro, S. et al. Application of a cell microarray chip system for accurate, highly sensitive, and rapid diagnosis for malaria in uganda. Sci. Rep. 6, 30136 (2016).
Say “manufacturing automation” and thoughts immediately go to the shop floor and specialized production equipment, robotics and material handling systems. But there is another realm of possible automation — the front office.
In this collection of articles, two of the industry’s foremost authorities on screw design — Jim Frankand and Mark Spalding — offer their sage advice on screw design...what works, what doesn’t, and what to look for when things start going wrong.
The two mold halves are held together using an Al molding fixture that is 9 mm thick at its base, with sidewalls to align the mold halves. A pair of toggle clamps applies pressure to the mold from above. We attached silicone tubing with an ID of 1.5 mm and OD of 5 mm to the inlet and outlet channels of the mold. Two inlet and outlet ports, embedded into both sides of the Al mold body, enable injection and ventilation prior and during RIM experiment. We initially connected the outlet port to an in-house vacuum source (20 mbar) for degassing the mold cavity and avoiding air entrapment during RIM.
Join KraussMaffei for an insightful webinar designed for industry professionals, engineers and anyone interested in the manufacturing processes of PVC pipes. This session will provide a comprehensive understanding of the technology behind the production of high-quality PVC pipes: from raw material preparation to final product testing. Agenda: Introduction to PVC extrusion: overview of the basic principles of PVC pipe extrusion — including the process of melting and shaping PVC resin into pipe forms Equipment and machinery: detailed explanation of the key equipment involved — such as extruders, dies and cooling systems — and their roles in the extrusion process Process parameters: insight into the critical process parameters like temperature, pressure and cooling rates that influence the quality and consistency of the final PVC pipes Energy efficiency: examination of ways to save material and energy use when extruding PVC pipe products
In conclusion, this work introduces reaction injection molding as a scalable platform suitable for use both in high-throughput and cost-effective manufacturing and in laboratory settings. We demonstrate the technique for the replication of microwell arrays. The distinct feature of simultaneous molding and surface energy patterning results in the structuring of hydrophilic-in-hydrophobic femtolitre well arrays capable of magnetic bead seeding with efficiencies of 75.1% and 87.2% for single-cycle and multiple-cycle seeding, respectively. This technology can pave the road towards successful commercialization of digital-based bioassays, specifically, and is amenable to diverse adaptations in medical devices and life science tools, where the spatial control of surface topology and properties is critical.
Pardon, G., Haraldsson, T. & van der Wijngaart, W. Simultaneous replication of hydrophilic and superhydrophobic micropatterns through area-selective monomers self-assembly. Adv. Mater. Interfaces 3, 1600404–n/a (2016). 1600404.
GETTING A QUOTE WITH LK-MOULD IS FREE AND SIMPLE.
FIND MORE OF OUR SERVICES:
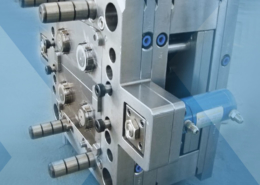
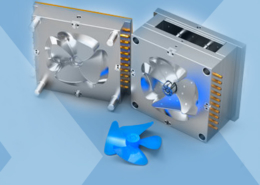
Plastic Molding

Rapid Prototyping
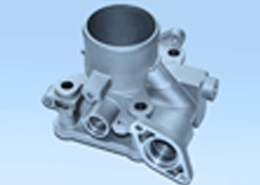
Pressure Die Casting
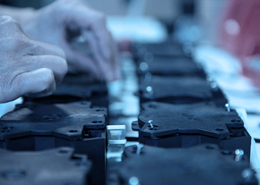
Parts Assembly
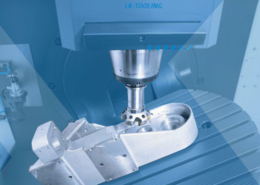