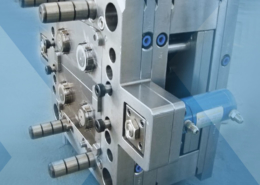
Blow-Molded Plastics Show 4% Growth Yearly - custom plastic molding company
Author:gly Date: 2024-09-30
Copyright - Unless otherwise stated all contents of this web site are © 2024 - William Reed Ltd - All Rights Reserved - Full details for the use of materials on this site can be found in the Terms & Conditions
The new grades underwent stick-slip tests at several premium automotive OEMs according to the VDA230-206 standard using testing machines from Ziegler Instruments, with very positive test results: a 10-point scale is used where 10 is the highest risk level. The new Elix grades managed toscore 1 – the lowest risk level. Tests were conducted with different forces (10 N, 40 N) and speeds (1 mm/s and 4 mm/s) at several temperatures.
They cited an example comparing 30 million bottles using two-step HDPE ISBM technology to EBM production, which showed cost savings of at least 15%, due to lightweighting and lower operating costs because of higher outputs, less maintenance and reduced energy consumption.
According to Fabian Herter, Industry Manager Automotive at Elix Polymers, with these new grades, significant cost savings are possible: “Until now, in many instances, fabrics or grease had to be added afterwards to reduce squeak and rattle. However, this involves additional costs and manual labor – and therefore is not ideal. Now, thanks to these new Elix grades, we are able to offer a more competitive solution when compared to other resins that are currently available.”
The firm said thinner packaging could still be a bigger barrier and pointed towards their Supertough range, which enables up to 25% thinner but stronger films.
Mr. Herter added: “This new development is the result of our close partnership with leading OEMs. Together, we identified the need to address this issue and we were able to develop tailor-made solutions. This approach is fully in line with our strategy to focus on specialty added-value materials.”
Typical critical automotive interior parts affected include door handles, seating parts, cup holders, and air vents. The newly developed grades may also be suited for other segments such as E&E, white goods, or consumer goods.
Supertough 22ST05 offers the potential to downgauge by up to 25% opening greater development perspectives for wide width films.
Total ran workshop presentations at K Show in Dusseldorf on different subjects, including “Food safe rigid packaging: ultra-low migration solutions” and “Bimodal technology for industrial packaging.”
Philippe Thiriaux, rigid packaging manager at Total, said: “This revolutionary technology, a breakthrough in the packaging industry, should provide our customers with a wider range of applications and features for the consumer and food packaging market.”
From a financial standpoint the two-step HDPE ISBM technology can be an attractive alternative to the traditional EBM process in typical industry cases, said the group.
Stephen has been with PlasticsToday and its preceding publications Modern Plastics and Injection Molding since 1992, throughout this time based in the Asia Pacific region, including stints in Japan, Australia, and his current location Singapore. His current beat focuses on automotive. Stephen is an avid folding bicycle rider, often taking his bike on overseas business trips, and is a proud dachshund owner.
Elix Polymers (Tarragona, Spain) has developed a range of specialty grades of acrylonitrile-styrene-butadiene (ABS) and polycarbonate (PC)/ABS to reduce the squeak that is generated when plastic parts come into contact with other plastic parts, leather, PVC foil, or other products. These undesirable noises can negatively affect the driver’s comfort and the car’s quality impression.
The new grades use Elix Polymers base polymers: standard ABS, high-heat ABS, ABS/PC or PC/ABS – and because their key properties remain the same, this does not affect existing OEM approvals of Elix grades. Furthermore, as the shrinkage of the materials stays the same, current molds can be used without further need for modifications.
The group claims it reduces material and conversion costs and provides an alternative to extrusion blow molded (EBM) HDPE and ISBM PET.
Husky (injection molding machinery), Sidel (stretch blow molding machinery and packaging design) and Total (polymer development) used the HDPE SB 1359 resin for ISBM processing and evaluated the cost of ownership of two-step HDPE ISBM, including material costs, capital investment and fixed and variable costs.
GETTING A QUOTE WITH LK-MOULD IS FREE AND SIMPLE.
FIND MORE OF OUR SERVICES:
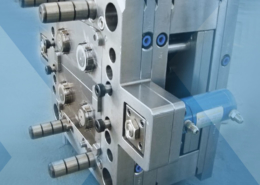
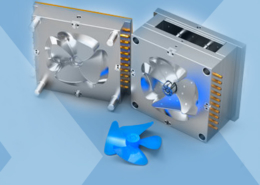
Plastic Molding

Rapid Prototyping
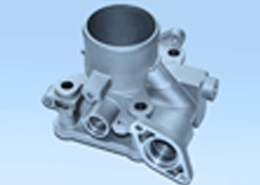
Pressure Die Casting
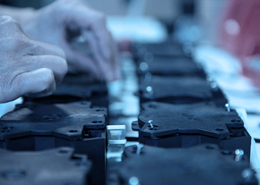
Parts Assembly
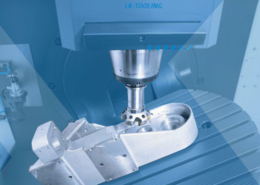