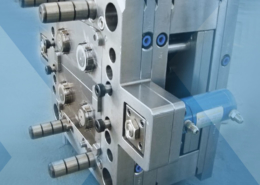
Blow-Molded Plastics Show 4% Growth Yearly - custom plastic injection molding se
Author:gly Date: 2024-09-30
We are extremely excited to share with visitors all of the latest company developments and our application-specific medical expertise, including our in-house automation offerings, our expansion in Ireland and how this supports the medical/life sciences community, plus how processors can increase productivity and machine availability.
Home diagnostic and wellbeing solutions driven by the aging population and telehealth and outpatient care will inevitably direct future treatment pathways.
As a true global medical team, it’s essential that we continue to foster greater collaboration. This sharing of project successes leads to global partnerships that are so pivotal to a responsive market aligned to future medical needs. Being support by trusted partners is proven to yield the strongest and fastest results.
The trial cell offers a dedicated area for comprehensive testing, allowing for analysis of key characteristics such as fill patterns, thermal imaging, gate freeze studies, cycle time efficiencies, and their direct influence on final product quality. By introducing this dedicated trial resource, Omega Plastics can support customers by providing insights and expert validation of tooling solutions.
There is a strong move towards “copy & paste” systems and processes in both Europe and North America. We are also seeing requests for remote system access to historical machine data for troubleshooting and monitoring validated process settings.
Over the past five years, the group has added seven additional injection moulding machines, significantly expanding its injection moulding machine capacity from 23 to 30 machines, ranging from 40T to 1,300T. Further significant investments have been made in warehousing, and material handling systems to support the additional moulding capacity.
In addition to the press expansion, Omega Plastics based in Gateshead, has established a dedicated tool trial cell to support its UK toolroom and in-house tool manufacture, operating independently of planned production activities. This specialised validation facility enables Omega Plastics to test and validate new tools without any impact on ongoing production processes.
The trial cell is equipped with two injection moulding machines, including a 40-tonne machine and a 100-tonne machine. This dedicated resource ensures optimal flexibility and precision during tooling validation processes, enhancing the overall customer experience.
Omega Plastics Group, an integrated plastic injection moulding group has announced the addition of new injection moulding press capacity at both Signal Plastics and Omega Plastics.
It should be noted that over committing to a cleanroom classification could leave medical manufacturers exposed to unwarranted compliance requirements that, once approved, they must continue to adhere to. Sometimes effective ventilation is all that’s required. Yet, for sterile medicinal products, the requirements - defined by Annex 1 of the EU and PIC/S GMPs – are now even more stringent.
Medical manufacturers that create their own GMP documentations benefit from having a consistent tool to track the qualification of all associated equipment, including mould tools and automation solutions. This makes it much easier to manage defined steps for design, installation, operational and production Qualifications and Validations.
The choice of moulding machinery selected for cleanrooms is generally customer-specific. Where medical components need to be manufactured and packed in a self-contained cleanroom environment to meet ISO Class 7 or 8 standards and comply with any GMP Annex 1 and FDA regulations, a fully configured all-electric injection moulding machine is typically the best option.
LSR is increasingly used due to its safety, durability, temperature and chemical resistance and biocompatibility. The material is often used in baby-care products, as well as the medical industry for syringes, catheters and hearing aids. It is even feasible to combine LSR and thermoplastic moulding in one cleanroom moulding cell, allowing medical moulders to switch between the two.
There are also a number of velocity and injection power features that can be overlooked. However, when used correctly and repeatably by moulding operatives, it results in faster cycle times and more stable start-ups. Training and field site support can be really valuable to moulders seeking higher productivity.
Qualification forms part of the overarching validation masterplan (VMP). However, it’s just one of the verticals that feeds into the wider Validation process. There are no Qualification or Validation shortcuts. And with no standardised GMP documentation formats to follow, there are always subtle style differences. Yet, it’s good practice to keep this documentation as tight as possible, ensuring the content is unambiguous. Detailed but of a manageable size, without deviating from the original design qualification.
High-precision direct drive technology ensures more precision and repeatability. The result - higher quality medical components. Our Medical Package direct drives are known for being clean, cool, fast and quiet. These drive systems are tailored to the applications, which lowers energy consumption and also results in less heat having to be dissipated from air-conditioned environments. All of these features help to reduce operating costs.
Across the wide press range, Omega Plastics Group can produce components with shot weights ranging from less than 1g to 4kg. The group has capability to mould complex technical hand loads and overmoulds through to fully automated robot demoulding with integrated conveyor systems.
Our medical team can provide support and guidance right up until the Site Acceptance Test (SAT). Once configured with the mould tooling, automation and other periphery equipment, the customer assumes overall responsibility for the production cell. At that point really everything should have been checked with regard to the material influences and how the moulding machine performs.
To support these efforts, Sumitomo (SHI) Demag is continuing to develop an IoT dashboard to facilitate this data analysis and visualisation, transfer and storage of know-how, as well as maintenance planning and prediction. Within this assistance system, additional autonomous and interconnected functions are being conceived to provide valuable insight into the machine performance and different production variables.
The tolerance requirements for the medical sector over the last decade has got increasingly stricter. Processing stability, dimensional accuracy and repeatability are critical. Medical devices often comprise multiple components. If just one element is out of tolerance, the device might not meet the performance expectations. Comprehensive quality control and traceability of parts production are essential for minimising risks.
Strict user parameters ensures that explicit ISO 13485 medical component quality assurance and validation standards are consistently adhered to. The key areas that might impact a stable process include changes in pressure, temperature, flow rate and cooling rates. If these are altered in any way without approval it can trigger a costly re-validation exercise.
Medical/Life Science micro-moulding is another key sector. Often using a smaller tonnage machine, the limit of what can be moulded can be as light as 0.0003g, with walls as thin as 0.01mm and dimensional tolerances to ±0.005mm
That said, laboratory equipment and diagnostics equipment remains clearly important. For these types of applications, manufacturers generally utilise larger machines within the IntElect series. The company is also closely monitoring the corona preventative agent market, including oral tablets and nasal administration pumping sprays.
One thing all of these applications have in common is their need for total accuracy and zero defects during the moulding process.
As observed during the pandemic, the shift towards virtual appointments, larger scale adoption of home healthcare programmes and smart diagnostic devices is no longer seen as being untenable. For medical moulders already producing vital monitoring devices, e.g. oxygen, weight, glucose and ECG devices, as well as infusion pumps and cannulas etc. and already meeting the exacting healthcare standards, the transition to homecare device production should be relatively seamless.
Customers that cannot determine their needs can always draw upon our pool of medical experts to populate a document with the design detail. This consultancy support gives a level of transparency to all parties, helping to circumvent renegotiations later down the project line. Having a defined structure also enhances the overall production quality.
Typical items being micro moulded using this technique can comprise a wide range of surgical, endoscopic, point of care testing, diabetes management, drug delivery and DNA research and sequencing devices. Additionally, the expanding market includes catheter components, hearing aids, dental prosthetics, microfluidics, vials, caps, specimen cups, vacuum blood and serum collection tubes, syringes, and IV parts.
Signal Plastics, based in Washington, has recently acquired a state-of-the-art Yizumi 700-tonne injection moulding press. This strategic acquisition aims to bolster production capabilities and meet the increasing demand from an existing customer as part of their production ramp-up. Equipped with a Sepro robot for demoulding and a conveyor belt to enhance productivity, the new 700-tonne press will significantly contribute to meeting customer requirements efficiently and effectively.
It depends on the application. Typically they will be medical grade plastics, which are biocompatible and suitable for products such as MRI casings, prosthetics etc. Some applications will need a higher melting point, others sterility, tensile strength or anti-corrosive properties.
The development of process optimisation systems, integrating material and knowledge with simulation tools is probably the most exciting development on the horizon. This will enable processors to observe advanced settings and capture deeper processing insights. Our ultimate vision is an intelligent machine that can independently make predictions about part quality, machine wear and failures and deliver optimisations online. Enabling greater process consistency, enhanced product quality and for real-time machine maintenance to be adjusted accordingly.
To comply with the FDA, GMP Annex 1 and CFR Part 211 requirements, the equipment used in the manufacture, processing, packing or holding of a drug product needs to be of an appropriate design, adequate size and suitably located.
These recent investments in additional injection moulding capacity and dedicated tooling resources are part of Omega Plastics Group's ongoing commitment to continuous improvement and customer satisfaction.
We can help customers by qualifying the equipment sold against the defined parameters specified. To make the entire Validation process easier for customers we can provide high quality consultancy at the outset of any project, drawing in all stakeholders when scoping out the machine design and user requirements specifications (URS). This helps to avoid over-specifying equipment or providing machinery that will never meet the processing tolerance requirements.
Process optimisation, enhanced productivity and TCO can have the biggest impact on profitability. Again, these are greatly enhanced by the high-performance drives. Confirmed by comprehensive lifetime tests performed on both the machines and components. Spindles tested under the toughest production conditions showed no signs of visible wear, even after millions of cycles.
High profile acquisitions of diagnostics companies, IPO listings, advances in liquid blood testing technology provide further assurance that the diagnostics market is on the cusp of another huge growth curve. This all indicates that there are clearly exciting opportunities ahead for moulders operating in the high tech medical device and diagnostics product development and production space.
Additionally, our company’s energy recovery system offers increased capacity. This not only improves efficiency, but also increases the longevity of the electrical components. Improving the temperature control of the spindles, motors and inverters all contribute to the safe machine operation, even in the most demanding applications.
During that time investments have also been made in the toolroom, including the acquisition of a Puma GT 2100 CNC Lathe, a new surface grinder, an Agie Carmilles EDM drill and a Fanuc ROBOCUT wire EDM, as well as in metrology software and capabilities. These investments allows Omega Plastics to aim to consistently meet customer demands and provide cutting-edge tooling solutions.
Additionally, the accompanying documentation can get really complex. Predominantly due to liability risks. With all medical packages, Sumitomo (SHI) Demag issues the Qualification documentation on installation. These files are signed and sent from the location where the machine order was fulfilled.
The medical market, particularly diagnostics, was strongly influenced by the Coronavirus pandemic. As expected, there has been a natural slow down in the consumable business related to the pandemic. Currently, there is a stronger leaning towards larger strategic and more complex projects, such as drug delivery devices and pen style injectors. This is due to the global growth in diabetes care.
Peter Sayer, group commercial director at Omega Plastics Group, said: "At Omega Plastics Group, our mission is to provide high-quality plastic injection mould tooling, components, assembly, and technical solutions on time and with exceptional customer service. These recent expansions and investments in our capabilities and resources demonstrate our commitment to our customers, ensuring we continue to exceed their expectations and deliver innovative solutions."
GETTING A QUOTE WITH LK-MOULD IS FREE AND SIMPLE.
FIND MORE OF OUR SERVICES:
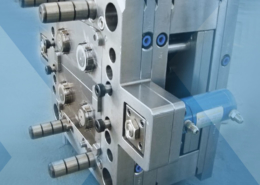
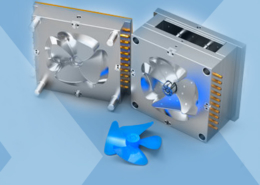
Plastic Molding

Rapid Prototyping
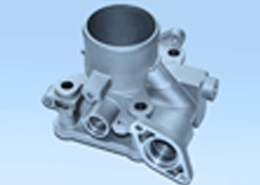
Pressure Die Casting
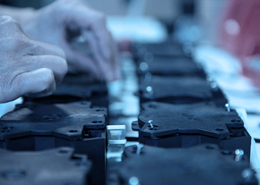
Parts Assembly
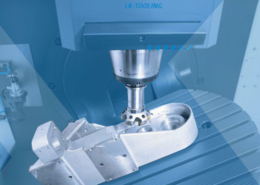