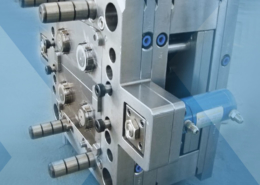
Blend Amorphous PHA with PLA to Improve injection Molded Part Properties - biode
Author:gly Date: 2024-09-30
The previous solution was a single flighted 3-zone screw with a bolt-on long glass-fiber (LGF) mixing head. With the demand for injection molding machines for processing long glass fiber-reinforced plastic in rod granule form on the rise, Engel decided to manufacture the screw and mixing head from a single piece and to further optimise the screw geometry. The newly developed LFS offers maximum plasticizing consistency when processing rod granules and reduces fiber breakage. In order to ensure superior distribution of the fiber bundles in the product, the screw geometry was also optimised. Highly effective flight-welding gives the screw the required wear- and corrosion-resistance.
Engel's response to the increasing requirements of the automotive industry in particular, and the increasing use of fibre-reinforced materials, takes the form of two new screws – the PFS (Physical Foaming Screw) and the LFS (Long Glass Fibre Screw).
In addition to Barkley Plastics, its membership includes Alucast, Brandauer, Grove Design, James Lister & Sons, Kimbermills International, PP Control & Automation and Muller Holdings.
“My Dad has been with the business since the late 70s and MD for the past 14 years, so we all felt the time was right for him to move upstairs and let a new management team build on the excellent platform he has built.”
Steve Smith, Operations Director, went on to add: “The focus is undoubtedly on strengthening our automotive partnerships, whilst at the same time using our two-shot moulding, injection moulding and toolmaking expertise to win complementary work in new markets.
The former logistics and business development manager will be joined at the helm by Operations Director Steve Smith and the duo are already setting their sights on maximising an £120,000 investment in automation and increasing its involvement in medical, construction and white goods.
The screw, non-return valve and barrel massively influence the melt quality and repeatability of the injection molding process as well as the lifespan and cost-effectiveness of the injection molding machine. As a provider of tailor-made, integrated system solutions, Engel also adapts the plasticizing unit to the specific requirements of the respective application.
This will reinforce the firm’s traditional expertise in automotive, where it continues to produce tools and injection moulded parts for customers including Aston Martin, BMW Mini, JLR, Nissan and Toyota.
The latest investment, which has been supported by WMG and the Made Smarter Programme, has seen the firm purchase six-axis collaborative robots that can work alongside an operator.
“Investment is a big thing for us at the moment. We must explore ways we can be more productive and efficient to help us offset rising energy prices and ensure we deliver competitive products to our global customer base.”
The requirements placed on plasticizing units are continuing to grow. “This is driven, among other things, by the on-going substitution of traditional technical materials, which generates considerable increases in the performance of polymer materials,” reports Günther Klammer, head of the Plasticising Systems division at Engel. “We ensure that even new materials can be processed even faster and to even higher quality standards despite what are in part increasing stresses on mechanical components.” The keys to this are, on the one hand, continuous investment in new machining technologies and, on the other, splitting the screw portfolio in order to offer the best possible solution for every material execution.
Employing more than 1700 people across 12 different factories, MAN can offer every engineering discipline imaginable, including aluminium casting, automation and control systems, forging, plastic injection moulding, precision machining, high-volume pressing, tube manipulation and welded assemblies.
A not well-known fact may be that Engel is the world’s largest screw manufacturer in the injection molding industry. At K 2019 Düsseldorf, Germany, the company will be presenting its extensive plasticizing portfolio.
Barkley Plastics, which is a founding member of the Manufacturing Assembly Network, has one of the largest toolmaking facilities in the UK, producing high precision tools capable of delivering 50 million mouldings for distribution domestically and throughout Europe and the rest of the world.
Employing 100 people at its Highgate factory, it can support its expanding client base with initial design and product development, right through to manufacture and assembly, with over 40 modern moulding presses – ranging from 5 to 650 tonne – able to produce the most intricate of components.
A leading plastic injection moulding and toolmaking specialist has appointed a new senior management team to help it target diversification and international opportunities.
He continued: “There’s a lot of challenges to contend with, but also a lot of opportunities as we look to take our toolmaking capabilities and injection moulding expertise into new markets, not to mention building on the success of our own interlocking floor product ‘PlasFloor’ by bringing a new home and garden range to market.
He concluded: “I think that highlights our engineering knowledge and the vast range of manufacturing capability we can offer. That’s something we’ve got to leverage going forward.”
“We’ve already had some significant success with this approach, with fire safety products exported to Eastern Europe and a new tooling project to help develop EV/Battery technology for agricultural and off-road vehicles. There’s even a project we’re doing to supply products for underwater boat lighting.”
The PFS was developed specifically for structural foam molding. In conjunction with a new material design, the new screw geometry ensures even better homogenisation of the gas-loaded melt and increases both productivity and the screw service life wherever fibre-reinforced polymers are used. A victory injection molding machine equipped with the new PFS will produce highly decorated, three-dimensionally complex parts at Engel's stand during K 2019. The application combines MuCell structural foam molding from Trexel with the roll-to-roll in-mold decoration (IMD) process.
“2022 is a massive year for the business as we look to bounce back from the pandemic and the supply chain issues affecting the automotive sector,” explained Matt.
The LFS for processing long glass fiber-reinforced materials reliably maintains the fiber length and ensures uniform distribution of the fibres in the melt. Picture: Engel
Stephen has been with PlasticsToday and its preceding publications Modern Plastics and Injection Molding since 1992, throughout this time based in the Asia Pacific region, including stints in Japan, Australia, and his current location Singapore. His current beat focuses on automotive. Stephen is an avid folding bicycle rider, often taking his bike on overseas business trips, and is a proud dachshund owner.
Long glass-fiber reinforced polypropylene and polyamide are commonly used for lightweight automotive construction – above all when high impact strength, excellent impact behaviour and low weight are required. The processing challenge in injection molding is to keep the fiber as long as possible and ensure uniform distribution of the fibers in the melt.
Barkley Plastics is a member of the Manufacturing Assembly Network (MAN), a group of seven sub-contract manufacturers and a specialist engineering design agency.
Matt Harwood has become Managing Director of Barkley Plastics, taking over from his father Mark who has become Chairman of the Birmingham-based business.
GETTING A QUOTE WITH LK-MOULD IS FREE AND SIMPLE.
FIND MORE OF OUR SERVICES:
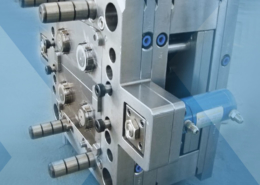
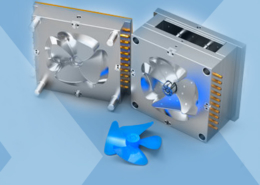
Plastic Molding

Rapid Prototyping
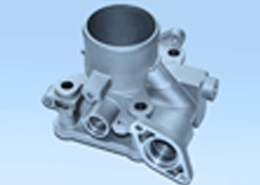
Pressure Die Casting
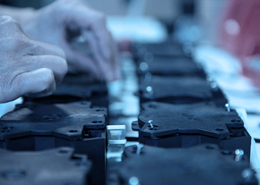
Parts Assembly
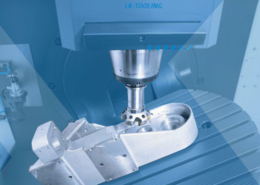