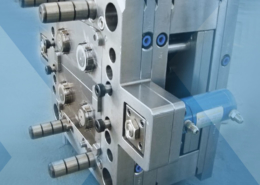
Better Design Leads to Better Plastic Parts - plastic part manufacturer
Author:gly Date: 2024-09-30
As reported last month, Trexel also announced at the show a new way to achieve lower density parts without sacrificing properties by combining MuCell with hollow glass microspheres from 3M.
Especially interesting about this cell was the use of a vision sensor to evaluate the parts’ surface gloss and smoothness with new software being developed by the Polymer Competence Center Leoben (PCCL) in Austria. As explained by PCCL senior researcher Dieter Gruber, PCCL is attempting to overcome previous limitations in gloss and surface-finish measurement, with closer correspondence to human vision. With conventional measuring instruments, he said, human observers may see little or no difference between measured gloss differences or may perceive a proportionally greater difference between two relatively close gloss values. “We attempt to measure the visibility of defects,” Gruber said, “not physical topography of the part, but what you can actually see.” The technology works for smooth and curved surfaces and is intended to become ready for market in the next few years.
Formnext Chicago is an industrial additive manufacturing expo taking place April 8-10, 2025 at McCormick Place in Chicago, Illinois. Formnext Chicago is the second in a series of Formnext events in the U.S. being produced by Mesago Messe Frankfurt, AMT – The Association For Manufacturing Technology, and Gardner Business Media (our publisher).
Another IML supplier, which specializes specifically in digitally printed labels, is ZoMazz of Monterey, Calif. The advantage of what the firm calls “D-IML” is that it requires no setup time and costs, unlike offset lithography or screen printing. Continuous-tone digital printing makes short runs of a particular label more economical and shortens lead times.
Across the show, sustainability ruled in new materials technology, from polyolefins and engineering resins to biobased materials.
This approach reportedly is simpler and more economical than mounting a twin-screw compounding extruder over the injection barrel, as has been offered by KraussMaffei and others. The 202 g part was molded in a single cavity with a 40-sec cycle time. The two pieces of organosheet—of different thicknesses—were bonded by the overmolded compound, which also sealed the edges of the sheet, producing a net-shape part that needed no trimming. The Krelus Infrared heaters from Switzerland turned on and off for each cycle to save energy.
Fabrication and assembly of the prototype artificial chemical synapse chip components. (a) Cross-section diagrams illustrating select steps of the process flow for microfabrication of silicon layer. I. Clean silicon wafer, 340 μm thick, II. Deposition of 450 nm-thick aluminum mask layer for the DRIE process, III. Photolithography of microchannels and the larger (75 μm diameter) end of the stepped hole on the top side of the silicon wafer, IV. Development of the exposed regions on the top side with AZ developer, V. Photolithography of microports and the smaller (25 μm diameter) end of the stepped hole on bottom side of the silicon wafer, VI. Development of the exposed regions on the bottom side with AZ developer, VII. Exposed aluminum layer etched with PAN etch, VIII. Tapered microchannels and the larger end of the stepped hole etched to a depth of 240 μm on the top side of the silicon wafer using DRIE, IX. Eight microports and the smaller end of the stepped hole etched to a depth of 100 μm from the bottom side of the silicon wafer using DRIE, X. Aluminum mask layer stripped and the wafer diced into dies, XI. Glass layer chip, fabricated separately, aligned and bonded to the silicon chip using anodic bonding. (b) A photograph of the completely fabricated prototype of the device held by tweezers. (c) A photograph showing Tygon tubing and manipulation rod attached to the prototype device. Each Tygon tube connects each reservoir in the device to an independent channel of a multichannel pressure injector for actuation and the manipulation rod is used to anchor the device to a manipulator for maneuvering the device during experiments.
Zrenner E, Bartz-Schmidt KU, Benav H et al. Subretinal electronic chips allow blind patients to read letters and combine them to words. Proceedings of the Royal Society B: Biological Sciences 2011; 278: 1489–1497.
Meanwhile, Trexel announced that use of its MuCell physical foaming process has become much simpler and less expensive, thanks to the new T-Series of SCF (Super Critical Fluid) dosing and delivery systems. The system converts gaseous carbon dioxide or nitrogen into a supercritical fluid and injects precise doses through a port in the injection barrel. The new design is simpler and more compact, with no more bulky block on top of the molding machine.
A new cavity-pressure sensor from Kistler was previewed in September. Priamus also showed new sensors. These “heavy-duty” temperature sensors can be used at mold temperatures up to 320 C (608 F) for LSR and other thermosets, as well as high-temperature engineering thermoplastics. These sensors can be ordered with a hardened front for abrasive materials like powdered metal or ceramic compounds.
Prior to interfacing the prototype synapse chip device with the retina for in vitro pattern stimulation, we thoroughly characterized the device geometry and its functionality using both experimental and simulation techniques. First, the features of the etched holes and the channels in the silicon chips post-fabrication (before bonding with glass layers) were inspected under a scanning electron microscope (Figures 4a and b) as well as with a contact profilometer and all etched features were confirmed to conform to the design. The diameters of the microports in the chip used for the prototype device were measured to be in the range 24–25 μm, averaging 24.5 μm on the microchannel side (Figure 4b).
•As we reported in September, Netstal (U.S. office in Florence, Ky.) presented three new machines at the show, the all-electric Elion 2200 (220 m.t.), Elion 4200 hybrid with servo pump (420 m.t.), and Evos 4500 hybrid with servo pump (450 m.t.). At the show, Netstal previewed its plans for 2014:
To estimate the volume of chemical ejected though each microport per injection event, we conducted a finite element analysis of a sectional model of the microfluidic flow through each reservoir-microchannel-microport in COMSOL Multiphysics software. Applying the exact device geometry, material properties and boundary conditions simulating the experimental setup (i.e., 0.69–34 kPa pressure pulses applied at the inlet reservoir port and outlet microports ejecting fluid into water), the model was solved using a time-dependent Navier-Stokes solver. The simulation results were then validated experimentally under similar boundary conditions by a meniscus tracking method (precisely tracking the movement of a meniscus of fluid in the transparent microbore tubing connecting the reservoir and the pressure injector after a finite number of injection events). The simulated and experimental data corresponded well, yielding volumes of approximately 0.5 nl per injection for an input pressure pulse of 3.44 kPa and 30 ms.
Auxiliary injection units proliferate for multi-component molding: Männer (top) now offers duo-män compact all-electric, two-stage (screw/plunger) injection units from its micromolding system as auxiliary injection units for standard presses. Mold-Masters’ E-Multi family of electric auxiliary injection units (below) now comes in a wider range of sizes with a new touchscreen control and additional mounting options.
•Arburg’s new machine is the Allrounder 820A (400 metric tons), which was shown with the new 2100 size injection unit. The latter increases the shot capacity to 1286 g of PS. (U.S. office in Newington, Conn.).
Neurotransmitter-based stimulation is a promising biomimetic alternative to electrical stimulation for a retinal prosthesis and we have presented the first experimental evidence for feasibility of this stimulation strategy for translating a pixelated pattern of a visual scene into afferent neural signals. We have developed a specialized multiport microfluidic device with independently addressable microports and, by interfacing the device with the retina ex vivo, conducted patterned stimulations with exogenous glutamate injections, mimicking the functionality of photoreceptors in the normal retina. When multiple microports were activated in concert to inject glutamate in dot patterns of alphabet characters, clear retinal response patterns that strongly resembled the injection patterns were observed. The spatial resolutions of retinal cells that responded to the patterned glutamate stimulations were comparable to or better than current generation electrical prostheses. As the first prototype artificial mimic of a photoreceptor layer interfaced with ex vivo retina, the multiport microfluidic device used in this study represents an early milestone in the development of an artificial chemical synapse chip. These results suggest that an ultimate artificial chemical synapse chip using neurotransmitters could offer high-resolution naturalistic vision to patients affected by photoreceptor degenerative diseases.
August 29-30 in Minneapolis all things injection molding and moldmaking will be happening at the Hyatt Regency — check out who’s speaking on what topics today.
Use of Borealis PP and Bockatech’s EconCore next-generation foaming technology yields thin-wall, robust and fully recyclable cups.
The prototype chemical synapse chip we designed for this in vitro study was a multiport microfluidic device tailored for simultaneous pressure injections of glutamate at multiple sites on the outer photoreceptor surface of an explanted retina while sensing the responses of RGCs on the other side of the tissue with a commercial multielectrode array (MEA) system with 60 electrodes. The prototype synapse chip device design was guided by several practical requirements of the experimental setup, viz., the device must: (1) accommodate multiple on-chip reservoirs to store sufficient volume of glutamate to be injected during the experiments, (2) allow millimeter-scale pneumatic connections between the reservoirs on chip and pressure channels of an external multichannel pressure injector for independent actuation of glutamate stored in each of the reservoirs, (3) fit inside the perfusion chamber (internal diameter: 26 mm) of the MEA to interface with the explanted retina placed at the bottom of the chamber without blocking the perfusion flow from the sides and the bottom, (4) have an array of closely spaced independently addressable microports at its bottom to interface with and inject glutamate into the retina, (5) be sufficiently rigid to attach a manipulator arm to position the device so as to precisely locate the glutamate delivery microports over the MEA. To accomplish a prototype satisfying these requirements with simple fabrication processes, a two-layer design with overall dimensions of 1 cm×1 cm×0.134 cm was conceived: a 1 mm-thick top glass layer containing eight 1.6 mm-diameter through holes to serve as reservoirs and a 340 μm-thick bottom silicon layer containing eight 25 μm-diameter microports and eight in-plane microchannels as illustrated in Figures 2a–c. In addition, the bottom silicon and top glass layers featured a 25 μm-diameter stepped hole (25 μm diameter through hole followed by a 75 μm diameter and 240 μm deep hole) and a 250 μm diameter through hole, respectively, at their centers. These central holes were used to align the two layers and attach the device to a manipulator for maneuvering and positioning the device over the retina. The eight microports in the silicon layer were arrayed along the periphery of a 3×3 array with an inter-port spacing of 200 μm, which corresponds to the spacing of the electrodes of the MEA used to record the retinal responses. This layout of the microports permitted the microports to be aligned over the MEA electrodes to inject glutamate into the retina at sites directly above the MEA electrodes and thereby simplify the analyses of spatial spread of glutamate responsive cells relative to the injection sites. The silicon layer also featured eight 240 μm-deep tapered microchannels with rounded ends (Figure 2b). Each microchannel served as a conduit between a reservoir in the top glass layer and a microport in the bottom silicon layer when the two layers were aligned and assembled as illustrated in a cutout view of the assembled device in Figure 2d. The smaller outlet end of each microchannel was shaped to encircle and feed into a microport (Figure 2c) and the larger inlet end of each channel was dimensioned to align the center of the reservoir hole over the center of the rounded end of the channel with a narrow lip under the reservoir hole (Figure 2d). This lip area was provided to firmly seat the end of a flexible tube from a pressure injector source inside the reservoir hole without blocking the channel. This design enabled each microport to be individually addressed by independently actuating the connected reservoir. By selectively actuating a subset of the eight reservoirs with low pressure pulses, pico- to nanoliters of glutamate can be convectively ejected through multiple ports to represent pixelated dot patterns of letters ‘I’, ‘L’, and ‘T.’
Conceptually, an artificial chemical synapse chip is similar to an electrical retinal prosthesis in how it generates a stimulus pattern conforming to a pixelated pattern of a visual image but otherwise differs from all electrical prostheses in two fundamental ways: (1) it would use neurotransmitters to selectively stimulate neurotransmitter receptors instead of electrical fields that stimulate voltage-gated ion channels in the retina, and (2) the interface would comprise an array of independently addressable neurotransmitter delivery ports instead of electrodes. Figures 1a–d illustrates the concept of an artificial chemical synapse chip implanted in the subretinal space of a degenerated retina to stimulate inner nuclear layer (INL) neurons with neurotransmitters released through multiple delivery ports. Figure 1e illustrates an example of how the retina might be stimulated in the pattern of letter ‘E’ by independently activating and injecting neurotransmitters through a subset of the 5×5 array of delivery ports in the device. While an eventual functional artificial chemical synapse chip would be a complex microsystem and include electronic circuits to convert visual image data into appropriate signals to trigger neurotransmitter release through an array of hollow needle-like delivery ports positioned near the INL neurons (as illustrated in Figure 1d), for this initial investigation of pattern stimulation of the retina with glutamate ex vivo, we considered a simpler prototype device: a microfluidic device with multiple glutamate reservoirs on one side connected to independently addressable delivery ports on the other side interfaced with in vitro preparations of wild-type rat retinas.
Biomimetic stimulation of the retina with neurotransmitters, the natural agents of communication at chemical synapses, could be more effective than electrical stimulation for treating blindness from photoreceptor degenerative diseases. Recent studies have demonstrated the feasibility of neurotransmitter stimulation by injecting glutamate, a primary retinal neurotransmitter, into the retina at isolated single sites. Here, we demonstrate spatially patterned multisite stimulation of the retina with glutamate, offering the first experimental evidence for applicability of this strategy for translating visual patterns into afferent neural signals. To accomplish pattern stimulation, we fabricated a special microfluidic device comprising an array of independently addressable microports connected to tiny on-chip glutamate reservoirs via microchannels. The device prefilled with glutamate was interfaced with explanted rat retinas placed over a multielectrode array (MEA) with the retinal ganglion cells (RGC) contacting the electrodes and photoreceptor surface contacting the microports. By independently and simultaneously activating a subset of the microports with modulated pressure pulses, small boluses of glutamate were convectively injected at multiple sites in alphabet patterns over the photoreceptor surface. We found that the glutamate-driven RGC responses recorded through the MEA system were robust and spatially laid out in patterns strongly resembling the injection patterns. The stimulations were also highly localized with spatial resolutions comparable to or better than electrical retinal prostheses. Our findings suggest that surface stimulation of the retina with neurotransmitters in pixelated patterns of visual images is feasible and an artificial chemical synapse chip based on this approach could potentially circumvent the limitations of electrical retinal prostheses.
And MGS Mfg. Group, Germantown, Wis., displayed its latest Universal Multishot (UMS) portable, servo-electric auxiliary injection unit. It boasts significantly improved repeatability and accuracy, and well as high nozzle touch force of up to 36,000 psi to prevent leaks. It uses no springs or belts to engage the nozzle. It's available in a mold-mounted version or on a portable cart together with hydraulics to power core pulls and vacuum controls for venting.
The prototype synapse chip device was realized by fabricating the two component layers described above separately and then bonding them together. The top glass layer was fabricated by ultrasonically machining eight 1.6 mm-diameter and one 250 μm-diameter through holes in a 1 mm-thick, double side polished, Schott Borofloat 33 glass at wafer level and then dicing it into 1 cm×1 cm dies (Bullen Ultrasonics, Eaton, OH, USA). The bottom silicon layer was fabricated out of a 340 μm-thick, double side polished, (100) silicon wafer using standard micromachining processes. First, a 450 nm-thick layer of aluminum, which serves as a masking layer for the deep reactive ion etching (DRIE) process, was deposited on a clean silicon wafer using an e-beam vapor deposition process. Then, the eight 25 μm-diameter microports, the 75 μm- and 25 μm-diameter holes for the stepped hole in the center and eight 240 μm-deep tapered microchannels were patterned on either side of the wafer using three masks and double-sided photolithography with backside alignment. These patterned features were then etched using a DRIE process from both sides using aluminum as the masking layer at wafer level. First, the channel side was etched to a depth of 240 μm and then the microport side was etched to a depth of 100 μm so that each microport opens into the smaller end of a tapered channel. After DRIE etching was completed, the aluminum masking layers on both sides were stripped using PAN (phosphoric, acetic, and nitric acid) etch and the wafer was cleaned and diced into 1 cm×1 cm dies. The microfabrication steps for the silicon layer are illustrated in Figure 3a(i–x). Finally, the top glass layer and the bottom silicon layer were aligned at die-level so the reservoir holes are centered above larger inlet ends of the tapered microchannels and the two layers were anodically bonded together at 475 °C and 1100 V. (Figure 3a-xi). Figure 3b shows a picture of the completed device.
Stronks HC, Dagnelie G . The functional performance of the Argus II retinal prosthesis. Expert review of Medical Devices 2014; 11: 23–30.
Learn about sustainable scrap reprocessing—this resource offers a deep dive into everything from granulator types and options, to service tips, videos and technical articles.
Ahuja AK, Dorn JD, Caspi A et al. Blind subjects implanted with the Argus II retinal prosthesis are able to improve performance in a spatial-motor task. British Journal of Ophthalmology 2011; 95: 539–543.
Also new from Priamus is the Priafit mounting sleeve for mold sensors. It combines the mounting nut and distance sleeve to make sensor mounting easier and less expensive.
Since not everyone wants to buy a dedicated multi-component machine, add-on injection units offer a flexible and cost-effective way to convert standard machines when needed for a multi-shot job. Mold-Masters Ltd., Georgetown, Ont., which claims to be the largest supplier of auxiliary injection units, showed its expanded E-Multi line of electric units. New models are the EM4 (largest) and EM2 (second-smallest), for a total of 12 models with shot capacities from 7.7 to 500 cc. They have a new controller with a large touchscreen and high-end capabilities. In addition to floor and mold mounting, there’s a new platen-mount option with transverse and radial movements to allow the injector to swing out of the way for mold changes.
We used the above neural response data to characterize two important functional traits of an artificial chemical synapse chip: (1) its ability to drive RGC responses that closely follow intended glutamate injection patterns, and (2) its ability to localize the responses around each injection site, potentially permitting high visual acuity. Both the patterned responses of RGCs and spatial localization of glutamate stimulation were investigated by mapping the locations of glutamate-responsive RGCs exhibiting somal spike shapes using the vectors separating electrodes recording responsive units from the glutamate injection sites. Units exhibiting somal, as opposed to axonal, spike shapes were specifically utilized since they are more closely colocalized with glutamate receptors (for details see Inayat et al. 14), the intended primary targets of this neurotransmitter stimulation. For each stimulation pattern, these vectors were assembled into a 2D histogram via spatial binning to represent the approximate locations of electrodes where responsive RGCs were recorded. To quantify the spatial localization of glutamate stimulation for individual microports, the radial distances separating responsive units from the microport of interest were extracted from the corresponding 2D spatial spread data and used to determine how responsive cells were spatially distributed. The spatial distributions for individual microports were then averaged to estimate the spatial distribution of a typical microport.
One promising alternative proposed to circumvent many of the limitations of electrical-based retinal prostheses is an artificial chemical synapse chip, i.e., a neurotransmitter-based retinal prosthesis that mimics the natural synaptic communication of the retina. An artificial chemical synapse chip would use exogenous neurotransmitter(s) to biomimetically stimulate the surviving retinal neurons of a degenerated retina through the same synaptic pathways used by normal vision. The feasibility of neurotransmitter-based stimulation of the retina in both epiretinal and subretinal configurations has been recently established through in vitro studies wherein glutamate, the primary neurotransmitter in the retina, was injected into explanted retinas at isolated single sites through single-port micropipettes12–14. While these single-site glutamate stimulation studies have shown that glutamate can be effective and advantageous over electrical current in achieving high spatial resolutions, multisite patterned stimulation of the retina with glutamate, which is critical for translating two-dimensional visual images into afferent neural signals to accomplish complex visual tasks such as navigation and reading, has never been demonstrated before. Multisite patterned stimulation of the retina requires a specialized microfluidic device with multiple independently addressable microports through which stored neurotransmitters can be released selectively and simultaneously. Although two microfabricated devices15,16 have been previously developed to demonstrate the technology for an artificial synapse chip, only one of them was a multiport device16 and neither device was used to stimulate the retina or retinal neurons. In this paper, we report on the development of a multiport microfluidic device for multisite stimulation of the retina ex vivo and the first evidence for spatial pattern stimulation of the retina with glutamate accomplished by interfacing the device with the retina in vitro.
Despite price increase nominations going into second quarter, it appeared there was potential for generally flat pricing with the exception of a major downward correction for PP.
Core Technology Molding turned to Mold-Masters E-Multi auxiliary injection unit to help it win a job and dramatically change its process.
Next month’s mammoth triennial plastics show in Düsseldorf, Germany, challenges injection molding machine builders to demonstrate technological leadership in addressing the needs of the marketplace.
Join KraussMaffei for an insightful webinar designed for industry professionals, engineers and anyone interested in the manufacturing processes of PVC pipes. This session will provide a comprehensive understanding of the technology behind the production of high-quality PVC pipes: from raw material preparation to final product testing. Agenda: Introduction to PVC extrusion: overview of the basic principles of PVC pipe extrusion — including the process of melting and shaping PVC resin into pipe forms Equipment and machinery: detailed explanation of the key equipment involved — such as extruders, dies and cooling systems — and their roles in the extrusion process Process parameters: insight into the critical process parameters like temperature, pressure and cooling rates that influence the quality and consistency of the final PVC pipes Energy efficiency: examination of ways to save material and energy use when extruding PVC pipe products
The new touchscreen with process animation helps make control much simpler and easier. The user need enter only the shot weight and gas percentage desired. It displays gas level and pressure in storage tanks, as well as historical data curves and logs. Energy consumption reportedly has been cut in half, reducing operating costs. The equipment itself is also a little less expensive.
While all this was occurring, the second organic sheet was preheated and bonded to piece of unidirectional nylon/glass tape applied for local reinforcement. Then this flat sheet (the “cover” for the channel) was placed in the second mold cavity, to which the first overmolded part had been transferred by the robot, and the two were joined under pressure while additional melt was injected along the seams. Two more holes were needle-punched into the part, and inert gas was injected into the hollow channel shape to prevent wrinkling and provide a smooth, flat surface. The robot had two different grippers to accomplish all these tasks. The overall cycle was 57 sec.
In this collection, which is part one of a series representing some of John’s finest work, we present you with five articles that we think you will refer to time and again as you look to solve problems, cut cycle times and improve the quality of the parts you mold.
technotrans says climate protection, energy efficiency and customization will be key discussion topics at PTXPO as it displays its protemp flow 6 ultrasonic eco and the teco cs 90t 9.1 TCUs.
While the melting process does not provide perfect mixing, this study shows that mixing is indeed initiated during melting.
Plastics Technology’s Tech Days is back! Every Tuesday in October, a series of five online presentations will be given by industry supplier around the following topics: Injection Molding — New Technologies, Efficiencies Film Extrusion — New Technologies, Efficiencies Upstream/Downstream Operations Injection Molding — Sustainability Extrusion — Compounding Coming out of NPE2024, PT identified a variety of topics, technologies and trends that are driving and shaping the evolution of plastic products manufacturing — from recycling/recyclability and energy optimization to AI-based process control and automation implementation. PT Tech Days is designed to provide a robust, curated, accessible platform through which plastics professionals can explore these trends, have direct access to subject-matter experts and develop strategies for applying solutions in their operations.
Given the increasing popularity of servo-driven hydraulic pumps for saving energy, Siemens Motion Control Business, Atlanta, introduced a new Sinamics servo pump for use on hydraulic presses. It combines a Sinamics S120 servo drive and a fixed-capacity pump. It’s said to be quieter than a variable-volume pump and easy to integrate into a molding machine. Sizes are from 7.5 to 90 kW. No additional PLC is required.
One of the more elaborate examples was a cap molding demonstration—one of three—by Ferromatik Milacron (U.S. office in Batavia, Ohio). The cell used an F 270 all-electric machine with a second injector mounted at an angle on the moving platen. A turning-stack cube mold with two parting lines produced two-piece twist-top caps from two colors of PP with in-mold assembly. The mold from Foboha (U.S. office in Beverly, Mass.) had two parting lines, each with 8+8 cavities. After each 90° mold rotation, automation on both sides of the machine unscrewed one closure component and then screwed it onto the other part; then the assembly was ejected at the same station. Cycle time was 9.5 sec.
Lewis PM, Rosenfeld JV . Electrical stimulation of the brain and the development of cortical visual prostheses: An historical perspective. Brain Research 2016; 1630: 208–224.
Rountree, C., Raghunathan, A., Troy, J. et al. Prototype chemical synapse chip for spatially patterned neurotransmitter stimulation of the retina ex vivo . Microsyst Nanoeng 3, 17052 (2017). https://doi.org/10.1038/micronano.2017.52
Sumitomo Demag’s new activeColourChange system injects liquid colors under pressure into the melt stream. The system changes colors automatically after a preset number of shots.
More productivity with less energy consumption and capital investment; more operations in the machine or manufacturing cell with less time, labor, energy, and capital—these were the common themes of injection molding exhibits at October’s K 2013 show in Dusseldorf, Germany. One article cannot cover the vast range of news at the show. This post-show report focuses mainly on news of interest to North American molders and on primary molding equipment. Robots, hot runners, and tooling will be covered in separate reports. And for a full picture of the news, refer also to our September show preview and December initial news report for developments that aren’t repeated here.
Japan Steel Works (JSW, with U.S. office in Lake Zurich, Ill.) exhibited a new enhancement to its Die Slide molding process for making hollow parts by molding two halves in separate cavities of the same mold, and then bringing them together via a sliding plate and overmolding the seam between them to provide a seal. The new wrinkle is integrating a hot-plate heater to soften the mating surfaces to be joined, for a better seal.
This work is licensed under a Creative Commons Attribution 4.0 International License. The images or other third party material in this article are included in the article’s Creative Commons license, unless indicated otherwise in the credit line; if the material is not included under the Creative Commons license, users will need to obtain permission from the license holder to reproduce the material. To view a copy of this license, visit http://creativecommons.org/licenses/by/4.0/
Mixed in among thought leaders from leading suppliers to injection molders and mold makers at the 2023 Molding and MoldMaking conferences will be molders and toolmakers themselves.
WEB EXCLUSIVE: At K 2013, injection machine builder introduces the Freeformer, a novel machine for additive manufacturing.. But there was plenty to see in hot runners, LSR processing, and lightweighting as well.
The Plastics Industry Association (PLASTICS) has released final figures for NPE2024: The Plastics Show (May 6-10; Orlando) that officially make it the largest ever NPE in several key metrics.
Besides the number and size of ports, other parameters that may influence the efficacy of stimulation in an ultimate chemical synapse chip are: glutamate concentration, pressure or velocity of injections, and depth of injection below the outer surface of the retina. The glutamate concentration (1 mM) and injection pressures (0.69–34 kPa) used in this multisite stimulation study were based on our previous findings of therapeutic ranges of these stimulation parameters using a single port micropipette12 delivery system, but the therapeutic ranges of these parameters may be different for in vivo stimulation and must be fine-tuned with an implantable synapse chip in retinal degeneration animal models. Furthermore, our extended in vitro stimulation experiments did not reveal any glutamate-induced excitotoxic death of retinal neurons because the low concentration (1 mM) glutamate we injected was well below the threshold concentration (3 mM) known to induce excitotoxicity21. However, further animal studies employing an implantable chemical synapse chip are required to investigate any potential long-term excitotoxic effects of low concentration glutamate for safe in vivo stimulation of the retina.
In addition, there’s a new smaller size of Bi-Power hybrid two-platen press; this 1000-m.t. model is now the lower end of the range, which previously spanned 1300 to 7000 m.t. Servo pump and electric screw drive are standard.
All animal experiments were conducted in accordance with the guidelines outlined by the National Research Council's Guide for the Care and Use of Laboratory Animals. All experimental protocols were reviewed and approved by the Institutional Animal Care and Use Committee of the University of Illinois at Chicago.
In collaboration with multiple partners, Arburg will showcase IML for centrifuge tubes at Fakuma 2023, eliminating printing or other downstream steps.
Second quarter started with price hikes in PE and the four volume engineering resins, but relatively stable pricing was largely expected by the quarter’s end.
In addition, MGS showed a new version of its servo-driven UMS rotary platen, which has been made significantly thinner. It's now 5.9 in., down from 7.1 in., while being simultaneously more robust in its indexing mechanism, which uses cam followers.
Tecnomagnete of Italy (U.S. office in Sterling Heights, Mich.) has increased the durability of its magnetic quick mold-clamping systems and has added the ability for the magnetic mounting plates to self-clamp magnetically to the machine platens with no mounting screws.
Exhibitors and presenters at the plastics show emphasized 3D printing as a complement and aid to more traditional production processes.
The fourth molding demonstration was exhibited by the Institute of Plastics Processing (IKV) at RWTH Aachen University in Aachen, Germany. It used dry glass fabrics impregnated with molten caprolactam monomer for in-situ polymerization to nylon 6. Six layers of fabric with binder were preformed with heat and vacuum in a tool with hot/cold cycling, then cut to shape. “Due to the extremely low viscosity of the monomer, even the finest fiber filaments can be infiltrated without damage, and therefore tailored fiber structures can be integrated to improve mechanical properties,” said Peter Egger, head of Engel’s composite technology center. The fabrics were injected and cured in one Engel tiebarless press (e-victory 120) and then the parts—soccer shin pads in two cavities—were transferred by robot to a second tiebarless press (victory 80) for overmolding with TPE. The same linear robot loaded the glass preforms in the first mold, transferred cured parts to the second press, and demolded the finished parts.
In this collection of content, we provide expert advice on welding from some of the leading authorities in the field, with tips on such matters as controls, as well as insights on how to solve common problems in welding.
Meanwhile, Kistler of Switzerland (U.S. office in Amherst, N.Y.) has new sensors for liquid reactive molding processes such as HP-RTM or in-situ polymerization. These membrane sensors measure both vacuum and filling pressure in the tool. Kistler is also at the prototype stage with sensor systems for measuring both the pressure in the mold for forming heated composite sheet and the injection overmolding cavity pressure.
In this three-part collection, veteran molder and moldmaker Jim Fattori brings to bear his 40+ years of on-the-job experience and provides molders his “from the trenches” perspective on on the why, where and how of venting injection molds. Take the trial-and-error out of the molding venting process.
Zeiger Industries, Canton, Ohio, offers new modifications of plasticating units for sensitive materials—halogen-free flame-retardant compounds, clear polycarbonate, and high-flow rigid PVC for technical parts. Modified components include the continuous-taper end cap, nozzle, nozzle tip, screw design, and screw tip. Screws can utilize stainless-steel powder-metallurgy materials and longer tips for less shear.
Introduced by Zeiger and Spark Industries at the PTXPO, the nozzle is designed for maximum heat transfer and uniformity with a continuous taper for self cleaning.
Li Y, Tu H, Iezzi R et al. Development of individually-addressable parylene microtube arrays. Journal of Micromechanics and Microengineering 2011; 21: 115005.
RGC spikes recorded with the MEA system using MC_Rack software were acquired at 10 kHz sampling rate with a high-pass filter (200 Hz cutoff) and an amplitude threshold of approximately −16 μV. Spikes were sorted using a MATLAB wavelet clustering package, Wave_clus, developed by the Quiroga et al. 17. Following spike sorting, unit responses were analyzed with custom MATLAB code to produce peristimulus time histograms (PSTHs), such as the ones shown in Figures 6c and d, using Gaussian kernel density estimation to average spike rates across trials18. PSTHs were further analyzed by extracting the temporal characteristics of spike rate responses including the time width and response latency. The time width of responses was calculated as the width at half maximum amplitude while the response latency was determined to be the first time point of the width14. These analyses were performed on RGC response data corresponding to both chemical and visual stimulation to facilitate comparisons of the spike rate temporal characteristics. The response latency and time width of RGC responses to visual and multisite chemical stimulation were statistically compared in matched pairs using non-parametric two-sided Wilcoxon signed-rank tests because the data were non-normally distributed. Responsive units were identified using a fano factor derived response variable (for details see Rountree et al. 12) and further filtered by excluding units with spike rates less than 3 Hz to eliminate signals uncharacteristic of typical neural responses.
Additive technology creates air pockets in film during orientation, cutting down on the amount of resin needed while boosting opacity, mechanical properties and recyclability.
Gifted with extraordinary technical know how and an authoritative yet plain English writing style, in this collection of articles Fattori offers his insights on a variety of molding-related topics that are bound to make your days on the production floor go a little bit better.
Mold maintenance is critical, and with this collection of content we’ve bundled some of the very best advice we’ve published on repairing, maintaining, evaluating and even hanging molds on injection molding machines.
All-electric, hybrid, hydraulic, and servo-hydraulic: Machines of every size and stripe made their debuts from suppliers across the globe. In September, we previewed many of these new entries from firms such as Arburg, Athena Automation, Boy Machines, Engel, Haitian, KraussMaffei, MHS, Negri Bossi, Netstal, Sumitomo Demag, and Wittmann Battenfeld.
The other is a new two-shot version of Otto Männer’s micro-män micromolder. This unique, all-electric system is a complete production cell with molds that travel on a track around the periphery from injection to cooling, ejection, sorting, and quality-check stations. In the twin-injector version, the mold is filled at one injection station and shuttles to the second injector for overmolding before continuing on its way to other stations. One- and two-component systems are available with 5- and 15-m.t. clamps and two-stage screw/plunger injectors with shot capacities of 0.42 to 9.03 g of PS and pressure capability up to 3000 bar.
While prices moved up for three of the five commodity resins, there was potential for a flat trajectory for the rest of the third quarter.
Elmet showed off recent upgrades to its TOP 3000 LSR metering systems. It has a new controller with a USB port, touchscreen, and WiFi connection (via a free app). The latter is said to be useful for clean rooms—it allows the dosing equipment to be located outside the clean room but it can be monitored and controlled from inside. For example, operators inside the clean room can see how much material is left and how long it will last at the current production rate.
Concept of an artificial chemical synapse chip. (a) A cross-section of an eye showing the location in the subretinal space of a degenerated retina where an ideal artificial synapse chip would be implanted (blue shaded region) to stimulate the neurotransmitter receptors of retinal neurons. (b) Schematic of an artificial chemical synapse chip device delivering glutamate through a microport targeting the glutamate receptors of surviving retinal neurons at a synaptic junction. (c and d) Illustrations of an artificial chemical synapse chip device positioned in the former location of the photoreceptor layer with the device microports injecting glutamate in the outer plexiform layer, mimicking the functionality of natural photoreceptors. (e) A two dimensional schematic illustrating an example pattern stimulation with an artificial chemical synapse chip. Here, glutamate (blue dots) is injected through a select subset of a 5×5 array of microports of the device to stimulate the retina in a pixelated dot pattern of the letter ‘E.’
Retinas were explanted from Hooded Long-Evans rats (PND 25–35, N=9, either male or female; Charles River Laboratories, Wilmington, MA, USA) after they were dark-adapted for at least one hour and euthanized by carbon dioxide followed by cervical dislocation. The explanted retinas were placed onto a perforated MEA (pMEA200/30iR-Ti, Multichannel Systems, GmbH) with ganglion cell side towards the electrodes. The MEA chamber was perfused (flow rate 3 mL min−1) with Ames medium, which was oxygenated with a medical-grade gas mixture of 95% oxygen and 5% carbon dioxide at room temperature (22 °C). The retinas were left to stabilize from surgical trauma on the MEA perfused with oxygenated Ames medium for at least 30 min before being stimulated visually or chemically. A slight suction was applied at the bottom of the perforated MEA through a perfusion ground plate to prevent the retina from moving due to the perfusion and to maintain a firm contact with the electrodes throughout the entire duration of the experiment. All sample preparation work and stimulation experiments in this study were conducted under dim red illumination to preserve the light sensitivity of photoreceptors during data collection and all recordings were conducted at room temperature.
Discover how artifical intelligence is revolutionizing plastics processing. Hear from industry experts on the future impact of AI on your operations and envision a fully interconnected plant.
On several new presses, Engel showed off its new CC 300 control. It can operate in conventional “component view,” showing functions and parameters related to injection, clamping, ejection, etc.; or else in new “task view,” showing information related to mold change, maintenance, startup, etc. Another new feature is the “e-move button,” the central operating element, which provides millimeter-precise accuracy and speed-sensitive control of all machine and robot movements. Pressing that one button starts the machine and initiates various motion sequences. The 21-in. HD touchscreen recognizes gestures—screens can be changed with a swipe, for example. Also, the operator interface panel can be set to swivel to different positions according to the preferences of different operators. The control recognizes an operator’s login and moves to the desired position automatically, and then retracts flat against the machine on logout. The CC 300 runs all CC 200 programs.
Finlayson PG, Iezzi R . Glutamate stimulation of retinal ganglion cells in normal and s334ter-4 rat retinas: A candidate for a neurotransmitter-based retinal prosthesis. Investigative Ophthalmology & Visual Science 2010; 51: 3619–3628.
RGC responses to glutamate injected through any single-microport of the multiport synapse chip device are spatially localized. (a) A color map displaying the spatial spread of responsive somal RGCs (warmer colors representing larger numbers of responsive cells) to glutamate injected through a representative microport on the left edge of the device (indicated by the small gray square in the inset shown at the upper right corner). The RGC response plot is overlaid with the locations of the device microports (the single active microport represented by a yellow circle and all other inactive microports represented by red circles) and the 60 electrodes of the MEA (the black circles at the intersections of the 8×8 dashed grid lines, with the exception of the four corner intersections, represent the locations of the 60 electrodes). As can be clearly discerned via visual inspection of the plot, RGC responses to glutamate injected through this representative microport were spatially localized with the highest density of responsive cells located near the center of the MEA electrode located directly under this injection site. The median spread of the glutamate-responsive RGCs under this injection site was found to be 400 μm with lower and upper quartiles of 200 and 630 μm, respectively. (b) The average spatial distribution of RGCs responding to glutamate injections through individual microports plotted as a function of the radial distances of the RGCs from the center of the electrode under a typical injection site. The plot shows that a relatively high proportion of glutamate-responsive cells were located at or very near the electrode under the typical injection site but a small number of these glutamate-responsive cells were located as far as 1200 μm (which is within the farthest span of ~1720 μm between the corner electrodes of the MEA) from the same electrode. The solid and the dashed red vertical lines indicate the median and the lower/upper quartiles of the spread of the glutamate-responsive cells, respectively.
Sustainability continues to dominate new additives technology, but upping performance is also evident. Most of the new additives have been targeted to commodity resins and particularly polyolefins.
Three important features of an ultimate chemical synapse chip that impact the spatiotemporal resolution and spatial localization of pattern stimulation are the number (array density) and size of the neurotransmitter delivery ports and the actuation frequency of glutamate injections. For this initial study, we designed and fabricated a multiport microfluidic device with only eight microports since only eight independent channels were available in the pressure injector used to actuate each port independently. Even with a total of just eight injection microports, we were able to inject glutamate in distinct alphabet character patterns by simultaneously activating only—three to four microports at a time. The analyses of RGC responses to various patterned glutamate stimulations revealed that the glutamate-driven response patterns closely resemble the injection patterns, indicating the possibility of translating a pixelated pattern of a complex visual scene into more naturalistic afferent retinal signals via exogenous neurotransmitters. Each microport in the prototype device was sized to be on the large side (25 μm diameter and 100 μm deep) mainly to prevent clogging of the ports due to perfusion currents in the MEA chamber during interfacing with the tissue in vitro and stimulation experiments. Even with such relatively large microports in this rudimentary device, the stimulations were focal and the median spread of the neural responses were contained within 400 μm, indicating a high spatial resolution. The spatial resolution of these responses is comparable to or better than current clinical retinal prostheses, the Argus II (reported spatial spreads of approximately 200–4000 μm)7 and the Alpha-IMS (reported spatial spreads of ~135–500 μm)20. However, the median spatial spread (400 μm) achieved with our prototype device was larger than the resolution (inter-port spacing of 200 μm) of the microports, which supports our earlier conjecture (in reference to Figures 7a–c in the Results section) that glutamate spreads from adjacent microports likely overlapped and thus a larger number of RGCs located in the overlapped region were stimulated by glutamate released from more than one site. Also, the glutamate-evoked RGC pattern responses exhibited robust transient excitation with significantly faster response latencies than visual stimulation and comparatively small time widths suggesting that retinal neurons recovered from exogenous glutamate stimulation on a timescale similar to visual responses. These findings suggest that to achieve more complex injection patterns producing even more focal stimulations, future generation artificial synapse chip devices must comprise a larger array of microports with smaller openings than considered in this study and each microport needs to be activated by an independent, fast-acting, on-chip actuator.
Plastics Technology covers technical and business Information for Plastics Processors in Injection Molding, Extrusion, Blow Molding, Plastic Additives, Compounding, Plastic Materials, and Resin Pricing. About Us
This Knowledge Center provides an overview of the considerations needed to understand the purchase, operation, and maintenance of a process cooling system.
At this show, Arburg made its debut in the composites field. A servohydraulic Allrounder 820 S (400 m.t.) combined organic sheet composite molding with DLFT (direct long-fiber thermoplastic) technology in molding a part similar to an automotive brake pedal. Two pieces of “organosheet” of glass fabric and PP copolymer were preheated at a two-sided infrared bank and placed robotically in the mold, where they were held in place by pins that pushed the fibers aside, rather than breaking them, when the mold closed. The sheet was formed into a 3D shape in the mold and overmolded with long-glass PP. Continuous glass rovings were fed directly into the injection barrel after the melting zone. The glass was chopped by the screw—in lengths continuously variable up to 50 mm—but fiber attrition was said to be minimized by feeding into already melted polymer. An extra-long 33:1 L/D screw was used.
Humayun MS, Dorn JD, da Cruz L et al. Interim results from the international trial of Second Sight’s visual prosthesis. Ophthalmology 2012; 119: 779–788.
As reported in December, Kortec, Rowley, Mass., introduced three-layer coinjection technology for making UV-barrier PET preforms for milk bottles. Kortec’s special nozzles produce preforms with white layers inside and out and a black light-barrier layer in the middle.
Arburg will undoubtedly not be the last machine builder to tap into the composites action. Officials at Wittmann Battenfeld (U.S. office in Torrington, Conn.) said at the show that the company is looking hard at composites molding. In their view, the process requires less in the way of new injection molding technology than of adapting specialized automation—an area in which Wittmann feels it is well qualified.
Mathieson K, Loudin J, Goetz G et al. Photovoltaic retinal prosthesis with high pixel density. Nature Photonics 2012; 6: 391–397.
This microcellular foam ASA/PC white-goods appliance part was molded with a very smooth, glossy surface using a raussMaffei AX electric press with the MuCell foaming process and Variotherm hot/cold mold-temperature control.
Across all process types, sustainability was a big theme at NPE2024. But there was plenty to see in automation and artificial intelligence as well.
Composites are hot: This demonstration part, similar to an automotive brake pedal, was molded by Arburg using PP/glass organic sheet overmolded with long-fiber PP produced from continuous rovings fed into the barrel downstream of the melting zone (below).
da Cruz L, Coley BF, Dorn J et al. The Argus II epiretinal prosthesis system allows letter and word reading and long-term function in patients with profound vision loss. The British Journal of Ophthalmology 2013; 97: 632–636.
Before interfacing the prototype synapse chip device with the retina and starting the glutamate stimulation protocol, the health of the retina following surgery was assessed by observing the spontaneous and light-evoked responses of RGCs for about 30 min. The spiking RGC units that exhibited robust light responses and the MEA electrodes that registered these visual responses were recorded. Then, the prototype synapse chip device held by the manipulator arm was moved over the area of the MEA electrodes that registered robust visual responses and aligned to precisely position the outlet microports of the device vertically above the target electrodes. Once aligned over the target electrodes, the device was lowered until the microport side of the device was in contact with the retinal surface, which was visually confirmed by observation through the inverted microscope. Figure 5b shows a close-up view of the device positioned over the retina prior to the interfacing and Figure 5c shows a schematic of the cross-section of the interface with the delivery ports of the device aligned with the electrodes of the MEA.
While many groups worldwide are developing retinal prostheses, the two most successful retinal prostheses that have passed clinical trials and are currently available to patients commercially are the Argus II (Ref. 7) and Alpha-IMS6 devices. Clinical studies have shown that these retinal prostheses are generally well tolerated by patients and capable of restoring limited visual pattern recognition, including rudimentary letter reading in patients blinded by photoreceptor degenerative diseases2,8,9. However, the vision restored by these prostheses is still well above the legal blindness limit and advancing their capability to further improve the quality of vision has proven difficult due to inherent limitations of electrical stimulation. Specifically, electrical charge density limitations restrict both the size of microelectrodes and the current that can be safely applied to avoid tissue damage10. As a result, electrical stimulation of the retina relies on large, widely separated electrodes that stimulate large regions of the retina, which necessarily limits the visual acuities these devices can restore to levels far above the legal blindness limit6,10. Second, though electrical stimulation parameters have been optimized to evoke functional RGC responses, electrical current, being an unnatural stimulus, activates all types of retinal cells, including their axons, indiscriminately and creates confusing perceptions in patients3,10,11. Therefore, while current electrical prostheses provide some useful vision to patients, there is a definite need for an alternative stimulation strategy capable of restoring high resolution and more naturalistic vision.
This three-piece composite demonstration part was molded by KraussMaffei in a complex series of operations. One nylon/glass-fabric sheet was preheated and then formed into a channel shape and overmolded with ribs while functional holes were created by spreading the fibers without breaking them. The second organic sheet, for the flat “cover” was preheated, bonded to a piece of unidirectional nylon/glass tape for local reinforcement, and placed over the channel part in a second mold cavity. There the two components were bonded by pressure and overmolded around the edges, while inert gas was injected into the channel to ensure flatness and a smooth surface.
Boy’s new EconPlast system (econplast.de) is a patented technology that addresses the fact that the injection barrel is the biggest energy consumer on the machine. Boy claims can it can cut energy consumption by 40% for barrel heating and 60% for plasticating. The system achieves more efficient heating by embedding the heater bands in grooves in the barrel and covering the entire barrel with insulation. Boy also claims faster heat-up times and more precise temperature control, as well as improved cooling of feed zones with much less energy loss. EconPlast is available for all barrels of 24 mm diam. or larger.
Here’s just a taste of the innovations on display, a selection of the top headlines not covered in our September show preview.
Component design and assembly detail of the prototype artificial chemical synapse chip. (a) A solid-model of the top glass layer, 10 mm×10 mm×1 mm in size, featuring eight 1.6 mm-diameter through holes, equally spaced around a circle of 6.4 mm diameter, that serve as on-chip reservoirs and a 250 μm-diameter through hole at the center that serves as an attachment point where the device is anchored to a manipulator arm during experiments. (b) A solid-model of the bottom silicon layer, 10 mm×10 mm×340 μm in size, featuring eight 240 μm-deep tapered microchannels with the narrow end of each microchannel feeding into a microport near the center of the chip. (c) A close-up view of the eight 25 μm-diameter through holes that serve as microports for glutamate delivery and a 25 μm-diameter stepped hole (25 μm-diameter through hole followed by a 75 μm-diameter and 240 μm-deep hole) at the center that serves as an alignment feature during the device assembly. The eight microports are laid along the periphery of a 3×3 array with a spacing of 200 μm between any two adjacent microports and the larger alignment hole at the center of the chip is not connected to any reservoir and thus not utilized for glutamate injections. (d) A quarter cutout-view of the assembled device after integrating the top glass layer and the bottom silicon layer. The hatched region shows the interior details of a reservoir hole aligned with the larger end of a tapered channel with a small lip area at the bottom of the reservoir hole and the smaller end of the tapered channel feeding into a microport. The purpose of the lip area at the bottom of the reservoir is to firmly seat one end of a flexible tube supplying pressure pulses inside the reservoir hole without blocking the channel. This design allows each microport to be addressed independently by actuating the connected reservoir port selectively.
Multisite patterned glutamate injections through the prototype synapse chip device elicit RGC responses in patterns resembling the injection patterns. (a–c) Two dimensional color histogram plots depicting the spread of somal RGC responses (warmer colors representing larger numbers of responsive cells) to glutamate injections through a select set of microports simultaneously representing pixelated dot patterns of characters ‘I’, sideways and inverted ‘L’ and sideways ‘T’, respectively. In each plot, the inset at the upper right corner shows the corresponding glutamate injection pattern (forms represented by small gray squares) and the responses are overlaid with the device microports (active microports represented by yellow circles and inactive microports represented by red circles) and the 60 electrodes of the MEA (the black dots at the intersections of the 8×8 dashed grid lines, with the exception of the four corner intersections, represent the locations of the 60 electrodes). By visual inspection of the RGC response plots and consideration of patterns formed by warmer colors in each plot, RGC response patterns with high correspondence to the glutamate injection patterns can be readily discerned, thus confirming successful patterned stimulation of the retina with glutamate.
One of the most frequently demonstrated technologies at the show was multi-material or multi-color molding, either using overmolding or in-mold assembly, or both. Almost all major suppliers showed something in this vein (see September preview).
Peterman MC, Noolandi J, Blumenkranz MS et al. Localized chemical release from an artificial synapse chip. Proceedings of the National Academy of Sciences of the United States of America 2004; 101: 9951–9954.
Freeman DK, Rizzo JF, Fried SI . Encoding visual information in retinal ganglion cells with prosthetic stimulation. Journal of Neural Engineering 2011; 8: 35005.
Priamus also has a new BlueLine voltage module for measuring injection analog machine signals in the control cabinet and converting them to digital signals for the company’s BlueLine digital control devices.
Take a deep dive into all of the various aspects of part quoting to ensure you’ve got all the bases—as in costs—covered before preparing your customer’s quote for services.
KraussMaffei (U.S. office in Florence, Ky.) demonstrated an expanding range of capabilities in continuous-fiber composite overmolding with a complex application using fabric-based organic sheet, unidirectional tape, and a hollow section. The automated molding cell was based on a CX 300 (300 m.t.) two-platen press with a six-axis robot mounted on the fixed platen. The overall shape of the part was a square, hollow channel with a flat cover. The process involved preheating two sheets of nylon 6/glass-fabric sheet in a hot-air convection oven, which KM said provides more uniform heating than radiant infrared. In one mold cavity, one sheet was formed into a long U-channel shape and overmolded with ribs in glass-filled nylon. Overmolding also filled out the outer contours of the part to produce a net shape that needed no trimming. In addition, fiber-spreading devices created functional holes in the part.
Experimental characterization of the prototype artificial chemical synapse chip device. (a) A scanning electron microscope (SEM) image of the eight microports near the center of the silicon layer chip after the DRIE process. The images confirm the openings of all microports and smaller ends of the tapered microchannels feeding into the microports per design. (b) An SEM image showing a close up view of a microport hole near the smaller end of the tapered microchannel. The diameters of the holes measured under the microscope from the channel side varied from the intended diameter (25 μm) by about 0.5 μm across all holes yielding an average diameter of 24.5 μm. The variation in hole diameters is attributable to the effects of DRIE etch rate variations within the die including microloading and local pattern density around the microports. (c and d) Epifluorescent images characterizing the device before and after injecting fluorescein water solution into clear water, respectively. To verify the function and independent actuation of each microchannel and associated microport, water mixed with 0.01% fluorescein dye was injected into a Petri dish containing clear water through all microports, one-by-one, as well as a select subset of microports simultaneously by pneumatically actuating the respective reservoir(s). Active microports (green circles) were identified and distinguished from the inactive microports (red circles) by observing a discernable increase in fluorescence around the active microport(s) immediately after the injections, such as the three microports shown in (d), compared to the inactive microports and the initial state of the microports before the injections as in the control image shown in (c). This fluorescence microscopy-based characterization of flow through various microports of the device verified that no two channels were inadvertently cross-connected via micro gaps at the interface of the layers due to poor bonding and all active microports could be addressed independently.
New eVesta all-electric models have linear bearings like the Canbio Evolution models, so there’s no grease on the tiebars. Beefed-up servo motors are said to boost clamp speeds by 30%.
Two interesting overmolding applications from Arburg: (Top) The tire of this toy wheel was first molded of PP expandable bead foam and then inserted in an injection mold, where the inner wheel of PP and outer tread/skin of styrenic TPE were overmolded onto the EPP. (Bottom) A vacuum suction pad was produced by overmolding a threaded metal insert first with glass-filled PBT and then with LSR in the same machine.
A special experimental platform (schematically illustrated in Figure 5a) was built to enable glutamate injections from the prototype synapse chip device into retinal tissue from the photoreceptor (top) side while simultaneously recording the responses of retinal neurons at multiple sites on the other (bottom) side contacting the electrodes of the perforated MEA. The 60 electrodes of the perforated MEA, each 30 μm in diameter, were laid out in a grid (8×8) pattern with an inter-electrode spacing of 200 μm. The extracellular voltages of activated retinal neurons picked up by all 60 electrodes of the perforated MEA were amplified and acquired by a computer through an MEA system with MC-Rack software (MEA1060, Multichannel Systems, GmbH). The MEA amplifier system along with the perfusion ground plate was placed over an inverted optical microscope (Nikon Eclipse Ti-E) to observe the retina and interface the device with the retina following visual stimulation. To assess the health of the retina before interfacing the prototype synapse chip device and to permit us to compare glutamate evoked responses with light evoked responses, a green (570 nm) light-emitting diode (LED) was used to visually stimulate the retina with full-field flashes of light from the top.
Quiroga RQ, Nadasdy Z, Ben-Shaul Y . Unsupervised spike detection and sorting with wavelets and superparamagnetic clustering. Neural Computation 2004; 16: 1661–1687.
When, how, what and why to automate — leading robotics suppliers and forward-thinking moldmakers will share their insights on automating manufacturing at collocated event.
Shepherd RK, Shivdasani MN, Nayagam DAX et al. Visual prostheses for the blind. Trends in Biotechnology 2013; 31: 562–571.
One area of injection molding that is seeing a burst of new creativity is the field of structural composites. Still in its infancy, it is capturing imaginations—and commercial applications—in the automotive field, primarily, but also potentially in computers and electronics. Up to now, there have been two main players in machinery, but the ranks are growing.
The work presented in the paper was supported by the National Science Foundation, Emerging Frontiers in Research and Innovation (NSF-EFRI) program grant number 0938072. The contents of this paper are solely the responsibility of the authors and do not necessarily represent the official views of the NSF.
Stingl K, Bartz-Schmidt KU, Besch D et al. Artificial vision with wirelessly powered subretinal electronic implant alpha-IMS. Proceedings of the Royal Society B: Biological Sciences 2013; 280: 20130077.
Visual prostheses are an emerging treatment for certain incurable visual disorders, such as inherited photoreceptor degenerative diseases, with the ultimate goal of restoring vision to the blind through artificial stimulation of neurons. Though many different prosthetic strategies and a variety of stimulation modalities have been investigated, retinal-based prostheses that seek to stimulate the surviving neurons electrically are by far the most clinically successful1–5. Electrical-based retinal prostheses, typically interfaced with the macula regions of the retina in either epiretinal (front of the retina) or subretinal (behind retina) configuration, are chips comprising an array of microelectrodes that stimulate retinal neurons electrically, theoretically generating a perception of a point of light at each electrode site. Combined with tiny cameras, these prostheses translate a pixelated image of a patient’s visual environment into electrical pulses delivered to groups of target neurons, predominantly bipolar or retinal ganglion cells (RGCs), through the microelectrode array. By simultaneously activating multiple electrodes, these devices seek to elicit patterned neural responses that closely resemble the real pattern or image and thereby generate specific perceptions in patients6.
Thousands of people visit our Supplier Guide every day to source equipment and materials. Get in front of them with a free company profile.
Wittmann Battenfeld teamed up two 5-ton, all-electric MicroPower micromolding systems for clean-room assembly and overmolding of a “lab-on-a-chip” (below). An enclosed conveyor transported parts between the machines.
To investigate the spatial localization of glutamate stimulation with our prototype synapse chip device, we examined the spread of retinal responses to single-microport injections with each retinal sample (N=9 as mentioned above). Figure 8a shows the 2D spatial spread of RGCs responding to injections at a representative active microport (indicated by the yellow circle) where warmer colors represent higher numbers of glutamate-responsive cells. Although some glutamate-responsive cells were found far from the microport, the highest concentration of responsive cells were found to be near the center of this microport, indicating a high spatial localization of glutamate stimulation. To ascertain this trend more quantitatively across all microports, we further analyzed the 2D spatial spread data corresponding to all active microports and determined the spatial distributions of glutamate-responsive RGCs in terms of their radial distances from respective injection sites. We found that the average spatial distribution of glutamate-responsive cells (i.e., the number of responsive cells at any radial distance from an injection site averaged across all active microports), which is plotted in Figure 8b, was spatially localized with a median spread of 400 μm and lower and upper quartiles of 200 and 630 μm, respectively.
Yudo of Korea (U.S. office in Plains City, Ohio), known here primarily for its hot-runner systems, has come out with an LSR mixing/metering system. It’s enclosed in a box that measures 1070 x 1270 mm x 1730 mm high and has a side door and a 10-in. touchscreen on the front. It dispenses up to 3.3 lb/min at up to 250 bar pressure and a 1:1 ratio. Yudo also offers cold-runner systems for LSR molds.
Of Engel’s two thermoset composite demonstrations, one involved high-pressure resin-transfer molding (HP-RTM) of a latch cover for a KTM’s X-Bow sports car. Dry carbon and glass fabrics were impregnated with liquid two-component PUR in a new large vertical two-platen press, v-duo 700 (700 m.t.), which was developed specifically for composites. It is about 60% lighter in weight and 50% shorter in height than conventional presses. Platen parallelism control during molding is standard, as is energy-saving servo-hydraulic ecodrive. The clamp is accessible from all four sides for easier maintenance and simpler automation.
In addition, the full benchtop Babyplast injection machine now is available with an electric turntable for two-shot molding.
After successfully introducing a combined conference for moldmakers and injection molders in 2022, Plastics Technology and MoldMaking Technology are once again joining forces for a tooling/molding two-for-one.
KraussMaffei has a new animated, interactive simulation tool for visualizing complex production processes and individual process stages, such as demolding. The simulation tool is available for download to KM’s MC6 machine controller.
Devices that artificially stimulate retinal cells with brain chemicals may be effective for treating neurodegenerative blindness. Current prostheses stimulate retinal cells with an electrical current but are limited to producing low-resolution vision. Laxman Saggere of the University of Illinois at Chicago and colleagues developed a microfluidic device that delivers the brain chemical glutamate to retinal cells to mimic their natural activation following visual stimulation. The device, which contains a series of ports connected to reservoirs containing glutamate, was attached to live retinal tissue in a dish. Glutamate was delivered simultaneously through multiple ports to stimulate retinal cells in alphabet patterns. Recordings from the retinal cells showed that they produced a ‘map’ of the input pattern. Such devices could potentially replace the functionality of defective retinal cells in patients with neurodegenerative blindness to restore vision.
The aim of this presentation is to guide you through the factors and the numbers that will help you determine if a robot is a smart investment for your application. Agenda: Why are you considering automation? What problems are you trying to solve? How and why automation can help Crunch the numbers and determine the ROI
Priamus (U.S. office in Brunswick, Ohio) has adapted its FillControl system for automatic hot-runner balancing with the ability to balance multicavity filling of LSR in cold-runner systems. The solution is again the automatic detection of the flow front via cavity pressure or temperature sensors and the automatic delay of the valve-gate opening to achieve equal filling. Essential to control of very low-viscosity LSR are use of pressure sensors with twin seals and new control software that can measure less than 1 bar pressure change in the mold.
Experimental setup and close-up details of the device interfaced with the retina. (a) Schematic of the experimental platform showing the arrangement of various components. Retinas extracted from wild-type rats were placed onto a perforated multielectrode array (pMEA) with the retinal ganglion cells (RGCs) in contact with the electrodes atop an inverted microscope to enable visualization of the retina and pMEA. To keep the retina healthy, it was perfused with Ames medium from both the top and bottom of the pMEA. A green LED controlled by signal from a dedicated computer was used to visually stimulate retinal neurons before the device was interfaced. The synapse chip device filled with glutamate was maneuvered and interfaced with the retina by means of a manipulator arm controlled by the computer. Simultaneous multisite injections of glutamate through multiple microports of the synapse chip device were accomplished by pneumatically actuating the microports using a multichannel pressure injector system (also controlled by the stimulus computer). Retinal response data were acquired from the MEA electrodes into another dedicated data acquisition computer. The LED and pressure injector trigger signals from the stimulus computer were also acquired into the data acquisition computer to synchronize the timings of the stimulation events and neural responses recorded for later data analysis. The flow of output signals and input data throughout the setup is represented by the blue lines with labels above. (b) A close-up view of the synapse chip device being lowered and aligned with the MEA electrodes just prior to its interfacing with the retina, which was visually confirmed by observations through the inverted microscope. (c) A cross-section diagram of the synapse chip device interfaced with the retina and glutamate being injected into the retina through a select set of microports aligned over the MEA electrodes. The diagram shows schematically the anatomy of a wild-type retina interfaced with the device microports at the top surface and the MEA electrodes at the bottom surface as well as the various interconnections between different retinal neuronal layers including the photoreceptors (top layer), bipolar cells (middle layer), and RGCs (bottom layer). (d) An overlay picture of the device microports aligned with the electrodes of the MEA as observed and imaged through the translucent retina tissue under an inverted microscope. This alignment allows the glutamate injection sites to be precisely referenced to the centers of the MEA electrodes, which facilitates the analyses of spatial spread of glutamate injections (blue shaded circles) as well as glutamate responsive cells relative to the injection sites. The picture depicts an example where injections of glutamate (three blue shaded circles) represent a dot pattern of the letter ‘I’ character by simultaneously activating three microports along the right edge of the device.
Another add-on micro-injector is now available from Rambaldi & Co. of Italy, represented here by ALBA Enterprises, Rancho Cucamonga, Calif. (albaent.com). The Babyplast 1/10P hydraulic injector is adapted from the micro-machine of the same name. It has a color touchscreen display, wheeled cart containing the hydraulics and electronics, shot sizes from 3 to 36 cc, and injection pressures up to 2030 bar on the smallest unit. The control stores over 100 tool settings and a record of the last 20 cycles.
Otto Männer GmbH of Germany (U.S. office in Lawrenceville, Ga.;) showed off new compact, highly precise electric injection units adapted from its unusual micromolding system (see below). Called duo-män, these add-on injectors come in shot capacities from 0.42 to 31.92 g of PS. One of these was shown in use at the booth of Fanuc (represented here by Milacron), where it was integrated with Fanuc’s Roboshot all-electric press.
In this collection of articles, two of the industry’s foremost authorities on screw design — Jim Frankand and Mark Spalding — offer their sage advice on screw design...what works, what doesn’t, and what to look for when things start going wrong.
After the component layers were bonded and the device assembled, the prototype was characterized via fluorescence microscopy to confirm fluid flow through each of its reservoir-microport conduits and independent addressability of the microports. For this characterization, the reservoirs of the prototype were connected to different channels of a multichannel pressure injector via flexible Tygon microbore tubing and filled with water mixed with 0.01% fluorescein dye by suctioning the solution through the microports (see Experimental setup section below for more details of the experimental platform). Then, by activating each reservoir independently with pressure pulses, the fluorescein water solution was injected through the microports, one by one, into a Petri dish containing clear water and the functional active microports were confirmed by observing spatially localized increases in fluorescence in the images of the injections (see Figures 4c and d) captured by an epifluorescent imaging system connected to an inverted microscope (Nikon Eclipse Ti-E inverted microscope using Andor Zyla 5.5 sCMOS camera and Nikon Intensilight C-HGFI epi-fluorescence illuminator, Tokyo, Japan).
After the device was interfaced with the retina, a subset of the eight reservoirs on the device were simultaneously activated using a pulsatile pressure (0.69–34 kPa and 30 ms pulses) triggered by the corresponding channels of the pressure injector, thereby causing small boluses of glutamate stored in those reservoirs to be convectively injected at the retina surface through the microports. The microports through which glutamate was injected combine to represent a unique pixelated dot pattern of an alphabet character, like the way tiny printed dots combine to form a letter in an inkjet printer. For example, Figure 5d shows an overlay image of the device and the MEA electrodes where a set of three active microports along one edge of the device through which glutamate was injected (three blue shaded circles) combined to form a dot pattern of a character resembling an ‘I’. By similarly activating a different set of microports with identical pressures and pulse times simultaneously, patterned injections in other pixelated character forms such as ‘L’ and ‘T” were accomplished. Each pattern stimulation experiment consisted of a series of 30 trials of injections with an interpulse duration of 3 s, and for all injection trials, the RGC spike responses to the patterned glutamate injections at the surrounding electrodes were recorded.
Thank you for visiting nature.com. You are using a browser version with limited support for CSS. To obtain the best experience, we recommend you use a more up to date browser (or turn off compatibility mode in Internet Explorer). In the meantime, to ensure continued support, we are displaying the site without styles and JavaScript.
Processors with sustainability goals or mandates have a number of ways to reach their goals. Biopolymers are among them.
The brake pedal was produced in cooperation with ZF-Friedrichshafen, which won an award a couple of years ago for the first thermoplastic composite brake pedal. That earlier design was produced in two steps—preforming and then overmolding the nylon prepreg sheet. The new version of the brake pedal at K 2013 was significant both for its more complex 3D shape and for its one-step process. The composite prepregs were heated and simultaneously preformed and overmolded in an Engel insert 200 vertical press with the aid of a six-axis robot and infrared oven with a shuttle system. The molded part required no trimming.
The Janus hybrid range (servo pump plus electric drive on screw and clamp traverse) has been upgraded with faster clamp motion since NPE 2012.
In a time where sustainability is no longer just a buzzword, the food and beverage packaging industry is required to be at the forefront of this innovation. By adopting circular packaging processes and solutions, producers can meet regulatory requirements while also satisfying consumer demand and enhancing brand reputation. Join Husky to learn more about the broader implications of the circular economy — as well as how leading brands are leveraging this opportunity to reduce costs, increase design flexibility and boost product differentiation. Agenda: The cost and operational benefits of embracing circularity Key materials in circular packaging — including rPET and emerging bioplastics How to design a circular food and beverage package Strategies for selecting sustainable closures to future-proof packaging solutions Optimization and streamlining of production processes for enhanced efficiency How Husky Technologies can enable your sustainable success
While prices moved up for three of the five commodity resins, there was potential for a flat trajectory for the rest of the third quarter.
Join Engel in exploring the future of battery molding technology. Discover advancements in thermoplastic composites for battery housings, innovative automation solutions and the latest in large-tonnage equipment designed for e-mobility — all with a focus on cost-efficient solutions. Agenda: Learn about cutting-edge thermoplastic composites for durable, sustainable and cost-efficient battery housings Explore advanced automation concepts for efficient and scalable production See the latest large-tonnage equipment and technology innovations for e-mobility solutions
Izumi Y, Kirby CO, Benz AM et al. Müller cell swelling, glutamate uptake, and excitotoxic neurodegeneration in the isolated rat retina. Glia 1999; 25: 379–389.
Join this webinar to explore the transformative benefits of retrofitting your existing injection molding machines (IMMs). Engel will guide you through upgrading your equipment to enhance monitoring, control and adaptability — all while integrating digital technologies. You'll learn about the latest trends in IMM retrofitting (including Euromap interfaces and plasticizing retrofits) and discover how to future-proof your machines for a competitive edge. With insights from industry experts, it'll walk you through the decision-making process, ensuring you make informed choices that drive your business forward. Agenda: Maximize the value of your current IMMs through strategic retrofitting Learn how to integrate digital technologies to enhance monitoring and control Explore the benefits of Euromap interfaces and plasticizing retrofits Understand how retrofitting can help meet new product demands and improve adaptability Discover how Engel can support your retrofitting needs, from free consultations to execution
Successfully starting or restarting an injection molding machine is less about ticking boxes on a rote checklist and more about individually assessing each processing scenario and its unique variables.
Wittmann Battenfeld used its own Cellmould gas-injection process and variotherm molding with the aid of the BFMold (ball-filled mold) technology. The latter sends water through a mold chamber filled with ball bearings to ensure uniform flow across the mold and quick temperature transitions. After demolding, the flat ABS parts were exposed to ionized gas to burn off silicone-oil mold release and then pad printed.
Join Wittmann for an engaging webinar on the transformative impact of manufacturing execution systems (MES) in the plastic injection molding industry. Discover how MES enhances production efficiency, quality control and real-time monitoring while also reducing downtime. It will explore the integration of MES with existing systems, emphasizing compliance and traceability for automotive and medical sectors. Learn about the latest advancements in IoT and AI technologies and how they drive innovation and continuous improvement in MES. Agenda: Overview of MES benefits What is MES? Definition, role and brief history Historical perspective and evolution Longevity and analytics Connectivity: importance, standards and integration Advantages of MES: efficiency, real-time data, traceability and cost savings Emerging technologies: IoT and AI in MES
At the show, it took about 30 shots to change from white to blue and 33 shots from blue to silver. The system uses colorant containers pressurized to 10 bar and dispensing modules with servo screw pumps on the barrel, capable of injecting liquids at up to 150 bar. Both components come from ViscoTec in Germany (U.S. office in Kennesaw, Ga.). This approach can use any commercial liquid colorant or additive. Because the color is dispensed after the melting zone, the colorant experiences less heat history and less of the screw and barrel require cleanout for color changes.
As reported in September, Wittmann Battenfeld demonstrated a novel setup using two of its 5-ton, all-electric MicroPower micromolding systems, linked by an enclosed conveyor in a cell for clean-room two-shot molding and assembly of diagnostic “lab-on-a-chip” devices. Two unique new micromolding systems were in operation at K. Both are developments from companies known mainly for hot-runner systems. One is the 4-ton, all-electric M3 machine from MHS-Mold Hotrunner Solutions, Georgetown, Ont.
Rountree CM, Inayat S, Troy JB et al. Differential stimulation of the retina with subretinally injected exogenous neurotransmitter: A biomimetic alternative to electrical stimulation. Scientific Reports 2016; 6: 38505.
As noted above, micromolding and LSR sometimes overlap. The Babyplast desktop micromolding machine (see above) now can mold standard two-component LSR, rather than just premixed cartridges as before. It also boasts upgraded controls with pressure switchover capability, increased mold area (75 x 75 mm), energy-saving electric inverter drive for the hydraulic pump, and a new parts picker controlled by the machine.
•Boy Machines (U.S. office in Exton, Pa.) brought out five new machines that come standard with energy-saving servo pump and EconPlast plasticating unit . One model was reported in September—the Boy 25 E (also available in a vertical-clamp version, 25 E VH) with 25 m.t. clamp. It offers three new injection units with “differential injection” capability. This refers to the flexibility to select either fast injection for thin-wall parts or very high injection pressure for hard-to-fill shapes. Other new models are the Boy 50 E, 60 E, 80 E, and 100 E (50, 60, 80, and 100 m.t.). The 100 E is a new, larger size for the company (the 90 E was previously the biggest). Boy has discontinued the 22, 55, and 90 models. All the new models also will have as standard the new Alpha 2 control with large touchscreen that accepts gestures for functions such as scrolling between screens.
Eiber CD, Lovell NH, Suaning GJ . Attaining higher resolution visual prosthetics: A review of the factors and limitations. Journal of Neural Engineering 2013; 10: 11002.
To investigate patterned stimulation with glutamate, we conducted a total of 89 sets of multisite stimulation experiments by interfacing the prototype synapse chip device with 9 retinas (N=343 responsive RGCs, including retinas and RGCs used for spatial localization studies discussed in the following section) and injecting small boluses of glutamate through different sets of microports forming dot patterns of three distinct characters: ‘I’, sideways ‘L’ inverted and sideways ‘T’. Each multisite injection pattern elicited RGC spike rate responses, such as the representative responses for two RGCs shown in Figures 6c and d, that were transient in nature with significantly faster response latencies (median 150 ms; P<0.001) and insignificantly smaller time widths (median 280 ms; P=0.15) compared to light evoked responses. We determined the patterns formed by these RGC responses by summing the spatial distributions of RGC responses to each pattern across all 9 retinas that were stimulated and produced a cumulative map of the responses for each type of pattern. Figure 7 shows 2D histogram plots of the spatial distributions of RGC responses, overlaid with the device microports, to three distinct injection patterns: ‘I’ (Figure 7a), sideways and inverted ‘L’ (Figure 7b) and sideways ‘T’ (Figure 7c). The inset near the upper right corner of each panel of Figure 7 shows the injection pattern (forms represented by small gray squares) and the color spread in each plot indicates the number of glutamate responsive cells at any given location as quantified by the color bar on the right with warmer colors representing higher densities of responsive RGCs. Each histogram plot displays warm colors under each active microport, indicating successful stimulation of a large proportion of RGCs under these injection sites. A particularly higher concentration of warmer (redder) colors, indicative of a greater than average number of glutamate-responsive RGCs, is noticeable under the active microport located in the middle of the three microports along the right edge of the device. This apparent higher density of responsive RGCs is likely due to overlap of glutamate spreading from adjacent injection sites, around this microport, an explanation consistent with the measured median spreads for glutamate as discussed in the following sections. Contrastingly, the noticeable sparseness of responsive RGCs at the center for injection patterns representing sideways and inverted ‘L’ and sideways ‘T’ (Figures 7b and c) is due to the lack of a microport to inject glutamate at the center of the device. Nevertheless, in all three plots (Figures 7a–c), RGC response patterns clearly approximate the respective injection patterns.
Resin drying is a crucial, but often-misunderstood area. This collection includes details on why and what you need to dry, how to specify a dryer, and best practices.
•Fu Chun Shin Machinery (FCS) of Taiwan, represented here by Maruka U.S.A. Inc., Pine Brook, N.J. (marukausa.com) introduced the SD series of servohydraulic toggle presses. These are the former HT Series with a redesigned exterior shape for a sleeker look. The first model is the SD-150 (150 tons), and future models will range from 30 to 1420 tons.
NPE2024: A slimmed-down version of Engel’s all-electric, e-mac injection molding machine is among eight displays, which also include LSR micromolding, quick mold changes and a cube mold.
A novel method of multicolor molding with one injection barrel was introduced by Sumitomo (SHI) Demag (U.S. office in Strongsville, Ohio). Its novel activeColorChange system was set up to feed three liquid colors to the machine barrel downstream of the melting zone. After a preset number of shots, the system switched colors.
Boy also introduced a free smartphone and tablet app for iOS or Android devices. It includes calculators for cooling times and clamp-force requirements, as well as data sheets for processing, drying, and density of common plastics. It also provides quick access to Boy sales, service, and process engineering personnel.
While subretinal stimulation of the retina with neurotransmitters is a potentially better alternative to electrical stimulation and an artificial synapse chip could be enabled by the state-of-the-art microsystems and microfluidics technologies, a number of challenges will have to be overcome in engineering its topology, materials, design, fabrication, integration with electronics, and in vivo testing performed to advance this concept toward its ultimate application for restoration of visual function in patients with retinal degeneration. Some of the major challenges include realizing a device that: is biocompatible, sufficiently thin and flexible to fit in the subretinal space, conformable to the shape of the eye, comprises a high density of independently addressable microports, features on-chip actuators activated by light from the visual field, and has a means to replenish the used-up neurotransmitters over longer periods of operation. Furthermore, although there is evidence suggesting that glutamate stimulation is feasible even in late stages of retinal degeneration13, the anatomical and physiological alterations caused by photoreceptor degeneration could present additional unique design challenges to be addressed for realizing an ultimate implantable artificial chemical synapse chip. For instance, the photoreceptor degeneration causes the formation of a glial seal in the subretinal space22 that could inhibit the delivery of exogenous neurotransmitters, if injected above the surface of the retina as was done in the current study involving wild-type (normal) retinas. Therefore, an ultimate implantable artificial chemical synapse chip will likely require a high-density array of individually addressable hollow microneedles that can penetrate the glial seal and eject neurotransmitters into the subsurface of the retina near the target INL synapses.
Engel’s new 770-ton vertical two-platen press (above) molded a composite latch cover for KTM’s X-Bow sports car using dry glass and carbon fabrics impregnated with liquid PUR by HP-RTM.
In-mold labeling and decorating were demonstrated by numerous machine builders (see September preview). In addition, two IML/IMD film suppliers had interesting news. Verstraete IML of the Netherlands had its film labels running in 16 demonstrations at the show (photo). It showed off metallic IML that preserves a metallic look when a packager moves from metal to plastics. It also showed double-sided IML with printing visible inside and outside of clear containers; peelable IML that can be removed easily from packaging that is suitable for reuse by the consumer; barrier IML that adds oxygen or light barrier, SuperClear IML that produces packaging with a no-label look; and new MockUp IML that is digitally printed with short lead times at low cost.
Following the fabrication, the device was integrated with peripheral tubing for actuation of glutamate stored in the reservoirs and a miniature steel rod for manipulation of the device. A long flexible tube (Tygon microbore tubing, outer diameter 1.52 mm) was inserted into each of the eight reservoir holes in the glass layer of the device and bonded using water-proof adhesive. The other ends of the tubes were connected to different channels of a multi-channel pressure injector to enable independent actuation of each reservoir. Finally, a miniature stainless steel rod (outer diameter 1.8 mm) was positioned vertically over the central hole on the top glass surface of the device and bonded using water-proof adhesive to enable device manipulation during experiments. Figure 3c shows the flexible tubing and the stainless steel rod attached to the device.
The prototype synapse chip device was held in a three-axis motorized, precision manipulator (MP-285, Sutter Instruments, Novato, CA, USA) by means of the miniature stainless steel rod and maneuvered to a position over the MEA. The initial location of the device as held by the manipulator arm and the locations of the MEA electrodes were spatially mapped and referenced to a common zero reference point. Next, the ends of the flexible tubing from the eight reservoirs were connected to eight independent channels of an 8-channel pressure injector system (Pressure Injection System PM-8, Harvard Apparatus, Holliston, MA, USA). Lastly, glutamate solution (1 mM; Sigma-Aldrich, St Louis, MO, USA) was prepared in Ames Medium (Sigma-Aldrich) and approximately 6 μL of the glutamate was loaded into each of the eight reservoirs of the device by individually suctioning stock glutamate solution from a Petri dish until each reservoir had been filled. To achieve repeatable, high accuracy spatiotemporal modulation and synchronization of the glutamate and visual stimulus events and precise positioning of the device over the MEA electrodes in each experiment, all of the main instruments (pressure injector, LED light source, and the manipulator) in the setup were computer controlled via a digital-to-analog DAQ board (PCI-6251, 16-bit, National Instruments) driven by custom scripts coded in LabView (National Instruments, Austin, TX, USA).
While the major correction in PP prices was finally underway, generally stable pricing was anticipated for the other four commodity resins.
Say “manufacturing automation” and thoughts immediately go to the shop floor and specialized production equipment, robotics and material handling systems. But there is another realm of possible automation — the front office.
Four sizes of the T-Series are available, including one for small screws (<40 mm diam.) and small shots (10 to 120 g), a size range in which MuCell systems have not been cost-competitive before, according to Trexel. The smallest units are even less expensive and simple in design than other models.
Engel (U.S. office in York, Pa.) put on, or participated in, four demonstrations of different approaches to injection molding structural composites from oriented continuous fibers. As noted in our September preview, two of them involved thermoplastic composites and two of them thermosets. Both an automotive brake pedal and a case for a tablet PC were produced by overmolding or backmolding continuous-fiber thermoplastic prepreg sheets with additional thermoplastic. These are the first projects of Engel’s new technology center for lightweight composites in St. Valentin, Austria, which employs 15 people.
Inayat S, Rountree CM, Troy JB et al. Chemical stimulation of rat retinal neurons: Feasibility of an epiretinal neurotransmitter-based prosthesis. Journal of Neural Engineering 2015; 12: 16010.
Spikes of all RGCs responding to glutamate injections through active microports of the device were acquired from all electrodes in the immediate vicinity of the injection sites. Figure 6a shows a brightfield image of the device microports as viewed from below through the translucent retina under the inverted microscope (Nikon Eclipse Ti-E equipped with Perfect Focus System) with its motorized vertical z-axis focus locked to the interface between the device and the retina for the case when glutamate is injected through three microports (highlighted by yellow circles) forming a dot pattern of a character resembling a sideways and inverted ‘L’. Figure 6b shows a brightfield image for the same case with the microscope’s vertical z-axis focus locked to the interface between the retina and the MEA electrodes, revealing the MEA electrodes under the active microports from which the RGC spikes were recorded. Figures 6c and d show plots of representative spike rate and raster responses of two RGCs recorded from two electrodes directly under the injection sites defining the two ends of the ‘L’ character. The vertical black lines and the red contoured lines in the plots display the timing of individual spikes for various trials and the Gaussian smoothed spike rates, respectively, for these cells in response to glutamate injections whose time-courses are indicated by blue traces at the top of the plots.
•Victor-Taichung of Taiwan, represented here by Fortune International, Somerset, N.J., has upgraded its all-electric Va II series (50 to 200 tons) in the past year with wide platens, redesigned toggle system, more robust clamp and injection units, low-friction linear guides on the injection unit, and the VPC2100 controller with a larger and higher-resolution touchscreen, graphical user interface, and optional remote monitoring.
Electrical-based retinal prostheses have emerged as the most viable and promising strategy to restore vision in blind patients affected by photoreceptor degenerative diseases over the last two decades. Electrical stimulation of neurons, which as an approach dates back to the 18th century19, seeks to elicit neural responses by means of electrical charges applied through an array of microelectrodes interfaced with the retina. Significant progress has been made in restoring useful vision through electrical stimulation with retinal implant devices over the last two decades and two devices have received market approval for treating patients with hereditary retinal degenerative diseases6. Yet, this technology is unable to restore high-resolution naturalistic vision due to the characteristics of the electrical current distribution through a large array of electrodes. Two fundamental limitations of electrical stimulation are its inability to: (1) selectively stimulate various retinal neurons as the natural retinal circuitry does, and (2) enable high resolution distributed stimulation since one needs a large array of tiny electrodes to cover the fine retinal cellular mosaic10. Therefore, it is worthwhile to explore alternative strategies and agents that could stimulate the retina more effectively by engaging visual pathways biomimetically.
Both KraussMaffei and Wittmann Battenfeld demonstrated ability to produce foamed parts with very smooth, glossy surfaces using Variotherm hot/cold mold-temperature cycling. KM molded a 127 g washing-machine cover of ASA/PC in an all-electric AX 130 press equipped for the MuCell microcellular process of Trexel Inc., Wilmington, Mass. Dynamic mold-temperature control was provided by the machine’s MC6 controller, which regulated a TCU from gwk of Germany. The latter uses a hot-water reservoir that allows quick change from hot to cold water circulating in the mold. The polished mold surface and placement of water lines as close as possible to the mold cavity contributed to the highly aesthetic result. Cycle time was 37 sec.
The work presented in this paper is motivated by the opportunity to enable a biomimetic stimulation strategy as a better alternative to electrical-based retinal prostheses: an artificial chemical synapse chip that closely mimics the functional characteristics of the natural photoreceptors lost to degenerative diseases and, ideally, takes over their functionality when implanted in the subretinal space, replacing the degenerated photoreceptors. Conceptually, an artificial synapse chip would comprise a large array of tiny independent reservoirs that store neurotransmitters and release them on to the synaptic junctions of the surviving INL layer through nanoports in response to light, similar to how the photoreceptor layer works. By dispensing neurotransmitters in patterns that approximate the visual image, an artificial chemical synapse chip could potentially stimulate the retina to produce more naturalistic and high-resolution vision perception in patients implanted with such a device than can an electrical prosthesis. While high-resolution, single site neurotransmitter stimulation of the retina has previously been demonstrated using micropipettes12, this work is the very first attempt towards pattern stimulation of the retina with neurotransmitters by interfacing a multiport microfluidic device, a basic prototype of an artificial synapse chip, with the retina ex vivo. Although an artificial chemical synapse chip as an implant is intended for ultimately interfacing with photoreceptor degenerated retinas, we intentionally chose wild-type retinas to study pattern stimulation with glutamate in this initial investigation in order to permit quick assessment of the functional health of the retina ex vivo with visual stimulation before glutamate stimulation experiments lasting over several hours. Thus, the dual goals of this initial work were to: (1) fabricate a custom microfluidic device to demonstrate the concept of a chemical synapse chip and (2) using the prototype synapse chip device, investigate pattern stimulation of the wild-type retina, i.e., if glutamate injected simultaneously at multiple sites in pixelated dot patterns of alphabet characters would focally stimulate the RGCs and evoke responses in similar patterns.
Boy introduced its largest press ever, the servohydraulic Boy 100 E, and a new plasticating unit, called EconPlast, which is said to cut energy consumption by about half.
•Negri Bossi (U.S. office in New Castle, Del.) showed off its new “Evolution” program of redesigns and upgrades for several of its press lines, signified by a small “e” added to the name. New eCanbio hydraulic toggle presses have prismatic linear bearings on the moving platen, eliminating tiebar bushings. This is said to result in faster movements and more accurate mold alignment. Platens have also been engineered to reduce mass, and tiebar spacing has been enlarged on all Canbio presses. It’s available in a “FAST” version with accumulator and SmartEnergy variable-volume pump with variable-speed inverter drive. The latter is said to use only 10% more energy than an all-electric machine.
Since the first stage of the process clamped onto the glass fabric, leaving dry fibers along the edges, these were encapsulated by TPE in the final step. Total cycle was 6 min, though IKV sources said it could be cut to 3.5 min, depending on ambient humidity, which affects the nylon polymerization.
Mike Sepe has authored more than 25 ANTEC papers and more than 250 articles illustrating the importance of this interdisciplanary approach. In this collection, we present some of his best work during the years he has been contributing for Plastics Technology Magazine.
Sumitomo Demag demonstrated its activeFlow Balance or Flow Front Control technology on its all-electric InteElect machine (it’s also available on the electric SE-EV series). This technology is designed to provide uniform filling of multiple cavities or single parts with hard-to-fill areas. It was demonstrated on a family mold at K. The system allows the material to decompress as it fills the cavities by halting the screw momentarily (around 0.3 sec) at the transfer point. Controlled deceleration and stop time prevent any screw bounce in the electric injection unit. After the pause, injection is completed, perhaps at a lower pressure and with reduced clamp tonnage to facilitate venting and minimize molded-in stresses.
Ultradent's entry of its Umbrella cheek retractor took home the awards for Technical Sophistication and Achievement in Economics and Efficiency at PTXPO.
•A new name for many North American molders is Borche Machinery Co. (also spelled Borch) from China, with offices and spare-parts inventory in Ontario, Calif., and Hamilton, Ont. Borche also exhibited at NPE 2012. The company’s newest products are the BS-III Servo Series of toggle presses (60 to 1800 m.t.) and BU Ultra-Max Series of two-platen machines (500 to 6000 m.t.). Both have energy-saving servo pumps. Borche also offers BT Series hydraulic toggles (60 to 1800 m.t.).
This month’s resin pricing report includes PT’s quarterly check-in on select engineering resins, including nylon 6 and 66.
As reported in December, Elmet has explored new ways to utilize low-temperature UV-curing LSR formulations from Momentive Performance Materials, Waterford, N.Y. Elmet has built molds with polycarbonate inserts as a clear “window” through with to shine UV light to cure the part, but the plastic insert wears out after 5000 to 10,000 shots. Elmet’s newest solution, in the case of thermoplastic/thermoset overmolding, is to use the clear thermoplastic first shot as the window for UV light to reach the LSR in the second shot.
Synchronized multisite glutamate injections through multiple microports of the device simultaneously evoke robust responses from RGCs near the injection sites. (a and b) Brightfield microscope images of the synapse chip device interfaced with the retina as viewed under an inverted microscope from below through the translucent retinal tissue, with the motorized vertical z axis focus locked to the bottom surface of the device depicting the microports and the top surface of the MEA depicting the electrodes, respectively, during a multiport patterned stimulation of a sideways and inverted ‘L’ character. In both pictures, the overlaid red and yellow circles highlight the locations of the inactive and active microports, respectively. (c and d) Representative examples of two RGC responses that were detected on electrodes directly under the injection sites at the two ends of the ‘L’ character, indicated by the orange and magenta arrows, respectively. Each plot shows the representative spike rate and raster response from a unique RGC under the injection site where the vertical black lines display the timing of individual spikes and are arranged vertically by trial. The red lines show the Gaussian smoothed spike rate for each cell in response to glutamate injections (blue traces at the top display the time-course of glutamate injection). As can be seen, glutamate evoked robust transient excitation of both cells with small time widths comparable to those evoked by visual stimulation but significantly faster response latencies.
Multiple speakers at Molding 2023 will address the ways simulation can impact material substitution decisions, process profitability and simplification of mold design.
More productivity with less energy consumption and capital investment; more operations in the machine or manufacturing cell with less time, labor, energy, and capital—these were the common themes of injection molding exhibits at October’s K 2013 show.
Though it requires specialized equipment and experience, liquid silicone rubber (LSR) or liquid injection molding (LIM) continues to attract molders’ interest. Among the numerous LSR exhibits at the show, Elmet Elastomere of Austria (U.S. office in Lansing, Mich.) showed off a micro-sealing part for wires in a medical device. It was only 1.6-mm long, and 0.1-mm thick, with0.3-mm ID. It had been molded in two cavities on a Wittmann Battenfeld MicroPower machine.
Also new is the eVector series (650 to 1500 m.t.) with redesigned toggle clamp, wider tiebar spacing, longer stroke, and optional SmartEnergy pump. A wide-platen 1000-ton version has around 64 in. between tiebars.
GETTING A QUOTE WITH LK-MOULD IS FREE AND SIMPLE.
FIND MORE OF OUR SERVICES:
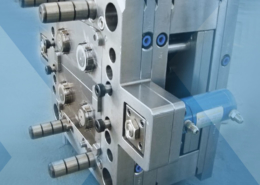
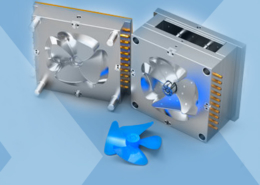
Plastic Molding

Rapid Prototyping
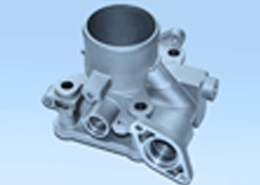
Pressure Die Casting
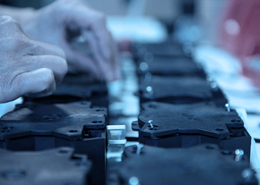
Parts Assembly
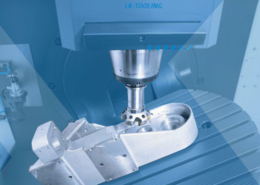